Table of Contents:
- Introduction to Plastic Injection Molding Materials
- Types of Plastic Injection Molding Materials
- Factors to Consider When Choosing Plastic Injection Molding Materials
- Commonly Used Plastic Injection Molding Materials
- The Injection Molding Process and Material Selection
- Key Trends and Innovations in Plastic Injection Molding Materials
- Conclusion and Final Thoughts
-
1.Introduction to Plastic Injection Molding Materials
Plastic injection molding is a popular manufacturing process that involves injecting molten plastic into a mold to create a finished product. The process has become increasingly popular thanks to its ability to produce complex parts with high precision quickly, reliably, and cost-effectively. However, the success of the process depends mainly on the selection of the right material for the job.
There are many types of plastic injection molding materials available today, each with unique properties and characteristics that make them suitable for specific applications. The choice of the material must take into account many factors, such as the desired mechanical and thermal properties, moldability, color, and surface finish. This is why it is essential to have a solid understanding of the different types of materials and the role they play in the injection molding process.
This guide aims to provide a comprehensive overview of plastic injection molding materials. We will explore the different types of materials used in injection molding, the factors to consider when choosing a material, and the most common types of plastic injection molding materials used today. By the end of this guide, you should have a good understanding of the role that material selection plays in the plastic injection molding process and how to select the right material for your specific application.
-
2.Types of Plastic Injection Molding Materials
Thermoplastics, thermosetting plastics, and elastomers are the three main types of plastic injection molding materials. Each type has unique characteristics that make them ideal for specific applications.
- 1.Thermoplastics:Thermoplastics are the most commonly used materials in plastic injection molding. They offer several advantages, including high strength, durability, and impact resistance. These materials are also highly moldable, meaning they can be melted and re-formed multiple times without losing their original properties. This makes them ideal for use in applications that require frequent molding or re-molding, such as in the automotive and packaging industries. Examples of thermoplastics include Polyethylene (PE), Polypropylene (PP), Polystyrene (PS), Polyvinyl Chloride (PVC), among others.
- 2.Thermosetting Plastics:Thermosetting plastics are materials that undergo a reaction during the molding process, resulting in a permanent, non-reversible change in the material’s properties. This means that once a thermoset plastic has been molded, it can no longer be melted and re-formed. These materials offer high mechanical strength, excellent insulation properties, and high resistance to heat and chemicals, making them ideal for use in applications such as electrical components, cookware handles, and automotive parts. Examples of thermosetting plastics include epoxy, phenolic, and melamine resins.
- 3.Elastomers:Elastomers are materials with rubber-like properties that can be stretched and deformed but return to their original shape once the force is removed. These materials offer high elasticity, low compression set, and excellent resistance to chemicals, making them ideal for use in applications such as seals, gaskets, and hoses. The most common types of elastomers used in injection molding include silicone, EPDM (ethylene propylene diene monomer), and natural rubber.
-
3.Factors to Consider When Choosing Plastic Injection Molding Materials
When choosing plastic injection molding materials, there are several factors that manufacturers and designers need to consider to ensure that the final product meets the necessary requirements. Below are three critical factors to consider when selecting a plastic injection molding material.
- 1. Material Properties:The properties of the material are perhaps the most important factor to consider when selecting a plastic injection molding material. The material must have the mechanical, thermal, electrical, and chemical properties necessary to meet the functional requirements of the final product. For example, an automotive part requires high strength and durability, while a packaging material may require flexibility, clarity, and a glossy finish. Other critical properties that should be considered include temperature resistance, scratch resistance, UV resistance, and dimensional stability. Additionally, the material must be compatible with the injection molding process to ensure that it can be molded into the desired shape.
- 2. Cost:The cost of the material is another crucial factor to consider when selecting plastic injection molding materials. Different materials have different costs, and the price can vary widely depending on the quantity ordered, the supplier, and other factors. The cost of the material should be weighed against the desired properties of the final product to ensure that the most economical material is used. Additionally, the cost of processing and recycling the material should also be taken into consideration.
- 3. Sustainability:Sustainability is becoming an increasingly important factor in the selection of plastic injection molding materials. The use of sustainable materials and environmentally-friendly manufacturing processes is essential in minimizing the environmental impact of plastic injection molding. When selecting a material, designers and manufacturers should consider the material’s biodegradability, recyclability, and energy consumption during production. By choosing sustainable materials and manufacturing processes, they can reduce waste, minimize their carbon footprint, and contribute to the circular economy.
-
4.Commonly Used Plastic Injection Molding Materials
In plastic injection molding, there are several materials that are commonly used due to their unique properties and characteristics that make them suitable for specific applications. Below are some of the most commonly used plastic injection molding materials:
- Polypropylene (PP):Polypropylene is a thermoplastic polymer that is widely used in injection molding applications. It is a highly versatile material that offers excellent impact resistance, chemical resistance, and mechanical properties such as stiffness and strength. Additionally, it is lightweight and has a low density, which makes it an ideal material for use in packaging, automotive parts, and consumer goods.
- Acrylonitrile Butadiene Styrene (ABS):Acrylonitrile Butadiene Styrene is a thermoplastic polymer that is commonly used in the automotive industry for its excellent mechanical properties, including high impact resistance and tensile strength. It is also highly resistant to chemicals and is an excellent material for use in injection molding applications that require intricate shapes, such as toys, electronics, and furniture.
- Polyethylene Terephthalate (PET):Polyethylene Terephthalate, commonly known as PET, is a clear, durable thermoplastic polymer that is primarily used in the production of plastic bottles and containers. It offers excellent chemical resistance, toughness, and durability, making it an ideal material for packaging applications. Additionally, it is highly recyclable and is often used in the production of sustainable packaging materials.
- Polyvinyl Chloride (PVC):Polyvinyl Chloride is a thermoplastic polymer that is widely used in injection molding applications due to its excellent electrical properties and resistance to chemicals and weathering. It is commonly used in the production of pipes, fittings, and automotive parts.
- Polycarbonate (PC):Polycarbonate is a thermoplastic polymer that is famous for its high impact resistance, optical clarity, and high-temperature resistance. It is commonly used in the production of automotive parts, electronic components, and optical lenses.
- Nylon:Nylon is an excellent choice for injection molding applications requiring high tensile strength, durability, and flexibility. It is commonly used in the production of gears, bearings, and automotive parts.
In conclusion, selecting the right plastic injection molding material is critical to the success of the final product. Polypropylene, Acrylonitrile Butadiene Styrene, Polyethylene Terephthalate, Polyvinyl Chloride, Polycarbonate, and Nylon are all commonly used materials that offer unique properties and characteristics that make them ideal for specific applications. Understanding the properties of these materials and their suitability for specific applications is essential in ensuring that the final product meets all the necessary requirements.
If you need about Plastic Injection Molding Services,You can click on the V1 Prototype website to find it.
-
5.The Injection Molding Process and Material Selection
The plastic injection molding process involves several steps that must be carefully executed to ensure the production of high-quality parts. The selection of the right material for injection molding is critical to the success of the process. The following are the steps involved in the injection molding process and how material selection plays a role in each step:
- Melting:The first step in the injection molding process is melting the plastic. The material is melted in an injection molding machine and placed into a chamber. It is then heated to a temperature where it becomes molten and can be molded into the desired shape. The melting point of the material must be sufficient to ensure complete melting without damaging the material.
- Injection:Once the plastic is melted, it is injected into the mold. The mold must be designed appropriately to ensure that the material flows evenly and fills the mold completely. Material selection plays a critical role in this step, as the rheological properties of the material must be optimized to ensure even flow and filling.
- Cooling:After the plastic is injected into the mold, it is cooled to a temperature where it solidifies and can be removed from the mold. The cooling rate is essential in determining the material properties of the final product. Materials with high thermal conductivity are ideal for injection molding, as they can be cooled quickly and evenly.
- Ejection:Once the plastic has cooled, it is ejected from the mold, and the process is repeated. The ejecting system should be designed to ensure that the part is not damaged during the ejection process. The material’s mechanical properties, such as strength and toughness, play a critical role in determining the design of the ejecting system.
In conclusion, material selection is a critical factor in the plastic injection molding process. The material must be carefully selected to ensure that it can be molded evenly, fill the mold completely, and cool quickly without damaging the material. By choosing the right material and optimizing the process parameters, manufacturers can produce high-quality parts that meet all the necessary requirements.
-
6.Key Trends and Innovations in Plastic Injection Molding Materials
The plastic injection molding industry is constantly evolving, driven by the need for improved materials that offer better performance, sustainability, and cost-effectiveness. Below are some of the key trends and innovations in plastic injection molding materials:
- Sustainable Materials:Sustainability is becoming an increasingly critical factor in plastic injection molding materials. Manufacturers are looking for alternative sources of raw materials that have a lower environmental impact than traditional petrochemical-based plastics. Sustainable materials such as bioplastics, recycled resins, and plant-based materials are gaining prominence, driven by the growing demand for eco-friendly products and packaging.
- High-Performance Materials:As technology advances and new applications emerge, demand is rising for plastic injection molding materials that offer greater mechanical strength, chemical resistance, and thermal stability. Materials such as high-performance thermoplastics, thermosetting plastics, and composites are being developed to meet these demands.
- Additive Manufacturing:Additive manufacturing, often referred to as 3D printing, is challenging the traditional injection molding process. Manufacturers are exploring the use of 3D printing in plastic injection molding to create prototypes and produce small batches of parts quickly and cost-effectively. Materials that are compatible with 3D printing, such as thermoplastic filaments, resins, and powders, are being developed to support this trend.
- Smart Materials:Smart materials that can sense, respond to, and adapt to their environment are gaining popularity in plastic injection molding. These materials incorporate sensors or other technologies that allow them to change shape, color, or other properties in response to external stimuli. These materials are being developed for a range of applications, including consumer goods, packaging, and automotive.
- Advanced Processing Techniques:Advanced processing techniques such as micro injection molding, multi-component injection molding, and insert molding are becoming more prevalent in plastic injection molding. These techniques allow manufacturers to produce parts with greater complexity and precision, opening up new opportunities for innovation and design.
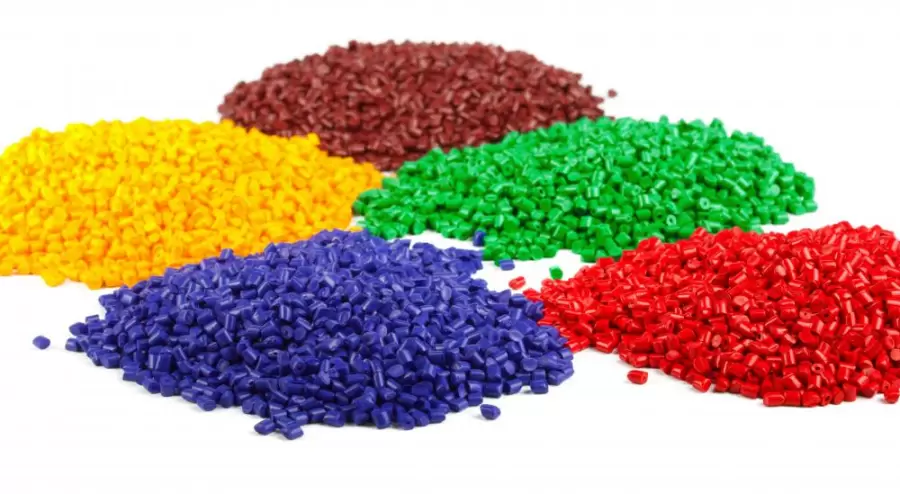
-
7.Conclusion and Final Thoughts
In conclusion, plastic injection molding is a critical technology that has transformed the manufacturing industry worldwide. The ability to mold plastic into complex shapes inexpensively and rapidly has been a game-changer for many industries, from automotive and consumer goods to healthcare and aerospace. As we’ve discussed, selecting the right material for injection molding is critical to the process’s success.
With the adoption of new materials that offer improved strength, sustainability, and responsiveness, alongside advanced processing techniques like micro-injection molding and multi-component injection molding, the possibilities for innovation and design are endless. However, safety and environmental concerns around plastic waste continue to grow, and it remains essential for manufacturers to focus on sustainability by incorporating eco-friendly materials and practices into their operations.
As technology advances and customer demands change, manufacturers must continue to stay ahead of the curve by adopting new materials, technologies, and processes. By doing so, they can produce products that are not only of high quality but also meet the needs of today’s environmentally-conscious consumers. With the proper material selection and processing techniques, plastic injection molding will remain an essential technology that continues to advance and transform manufacturing for years to come.