Table of Contents:
- Introduction
- Nylon Chemical and Physical Properties
- Nylon Types and Their Properties
- Nylon Applications and Properties
- Nylon Processing and Properties
- Nylon Testing and Properties
- Conclusion
-
1.Introduction
Nylon is a synthetic polymer that was first introduced by the DuPont Corporation in 1935. Since then, it has become a popular material due to its excellent properties and versatility. Nylon is widely used in various applications, including automotive parts, textiles, consumer goods, and medical equipment. This guide aims to provide a comprehensive overview of nylon properties, including its chemical and physical properties, different types of nylon and their applications, processing techniques, testing methods, and future developments.
The purpose of this guide is to help readers understand the different aspects of nylon properties and its various applications. It is intended for anyone who wants to learn more about nylon, including engineers, designers, manufacturers, and students. By providing a detailed overview of nylon properties, this guide aims to help readers select the appropriate material for a specific application and understand the material’s behavior during processing and use. Additionally, this guide will discuss the future of nylon, including ongoing research and development that aims to improve its properties and reduce its environmental impact.
-
2.Nylon Chemical and Physical Properties
Nylon is a thermoplastic material made from polyamide, which is a synthetic polymer consisting of repeating units of amide groups. The chemical composition of nylon varies depending on the type of nylon, but it typically includes carbon, hydrogen, oxygen, and nitrogen.
The molecular structure of nylon is a long-chain polymer that consists of repeating units of amide groups (-CONH-) linked together by methylene (-CH2-) groups. The number of carbon atoms between the amide groups determines the type of nylon. For example, nylon 6 has six carbon atoms between the amide groups, while nylon 6,6 has six carbon atoms in the amide group of one monomer and six carbon atoms in the amide group of the adjacent monomer.
Nylon’s physical properties include high stiffness, high tensile strength, and low coefficient of friction. Nylon is also known for its excellent strength, durability, and resistance to abrasion and chemicals. Its melting point ranges from 160°C to 270°C, depending on the type of nylon. Additionally, nylon is hydrophilic, which means it has a high affinity for water molecules. The presence of water molecules can affect its properties, including its strength and stiffness. However, nylon can be modified to become more hydrophobic, which makes it less susceptible to moisture absorption.
-
3.Nylon Types and Their Properties
Nylon is a versatile material that comes in different types, each with its unique properties and characteristics. Here’s an overview of the most common types of nylon and their properties:
Nylon 6:
- Chemical formula: (NH(CH2)5CO) n
- Properties: High strength, toughness, and stiffness. Good abrasion resistance and low friction coefficient. Good fatigue resistance and excellent electrical insulation. Moderate heat resistance and low water absorption.
- Applications: Automotive parts, electrical components, industrial applications, and textiles.
.
Nylon 6,6:
- Chemical formula: (NH(CH2)6NHCO(CH2)4CO) n
- Properties: Higher melting point and greater resistance to heat than nylon 6. Higher stiffness, strength, and abrasion resistance than nylon 6. Good resistance to chemicals and solvents. Lower water absorption than nylon 6.
- Applications: Automotive parts, bearings, gears, and industrial applications.
.
Nylon 11:
- Chemical formula: (NH(CH2)10CO) n
- Properties: High resistance to impact, puncture, and wear. Good flexibility and elasticity. Low moisture absorption and good chemical resistance. Good UV resistance and flame retardancy.
- Applications: Fuel lines, air brake tubing, hydraulic hoses, and electrical cables.
.
Nylon 12:
- Chemical formula: (NH(CH2)10CO(CH2)2CO) n
- Properties: Good flexibility and impact resistance. Excellent resistance to chemicals and hydrocarbons. Low water absorption and good dimensional stability. Low coefficient of friction.
- Applications: Flexible tubing, pneumatic hoses, and fuel lines.
.
Comparison of Nylon Types:
Nylon 6 and nylon 6,6 are the most commonly used types of nylon, with nylon 6 being more flexible and nylon 6,6 being more rigid. Nylon 11 and nylon 12 are specialty nylons with unique properties that make them suitable for specific applications. When selecting a nylon type for a particular application, factors such as strength, stiffness, temperature resistance, chemical resistance, and water absorption should be considered.
-
4.Nylon Applications and Properties
Nylon’s excellent properties make it a popular material in various industries. Here’s an overview of some of the most common applications of nylon and its properties:
Automotive Industry:
Nylon is used in various automotive parts, including fuel lines, brake hoses, engine covers, airbags, and gears. Nylon’s high strength, stiffness, and heat resistance make it suitable for applications that require durability, dimensional stability, and low friction.
Textile Industry:
Nylon is widely used in the textile industry due to its high strength, abrasion resistance, and low water absorption. Nylon is used to produce fabrics for various applications, including clothing, upholstery, carpets, and outdoor equipment.
Consumer Goods Industry:
Nylon is used in various consumer goods, including toys, kitchenware, luggage, and electronic casings. Nylon’s toughness, resistance to impact, and low coefficient of friction make it suitable for applications that require durability and smoothness.
Medical Industry:
Nylon is used in medical devices, such as catheters, surgical sutures, and implants, due to its biocompatibility, strength, and flexibility. Nylon’s low water absorption and good chemical resistance make it suitable for applications that require resistance to body fluids and chemicals.
Comparison of Nylon Applications and Properties:
The application of nylon varies depending on the type of nylon and its specific properties. Nylon 6 is commonly used in textile applications due to its flexibility and high water absorption, while nylon 6,6 is commonly used in automotive and industrial applications due to its stiffness and high temperature resistance. Nylon 11 and nylon 12 are commonly used in applications that require flexibility and impact resistance, such as fuel lines and flexible tubing. When selecting a nylon type for a particular application, factors such as strength, stiffness, temperature resistance, chemical resistance, and water absorption should be considered.
-
5.Nylon Processing and Properties
Nylon is a versatile material that can be processed using various methods. Here’s an overview of the most common nylon processing methods and the properties of nylon after processing:
Extrusion:
Extrusion is a common method used to produce nylon tubes, rods, and sheets. The process involves heating the nylon pellets and pushing them through a die to create the desired shape. Extruded nylon has good mechanical properties, including high strength and stiffness, good impact resistance, and good chemical resistance.
Injection Molding:
Injection molding is a widely used method for producing nylon parts, including automotive components, electrical connectors, and consumer goods. The process involves melting the nylon pellets and injecting them into a mold under high pressure. Nylon parts produced by injection molding have good mechanical properties, including high strength, stiffness, and impact resistance. They also have good dimensional stability and can be produced in large quantities.
Blow Molding:
Blow molding is a method used to produce hollow nylon parts, including fuel tanks and air intake ducts. The process involves melting the nylon pellets and inflating them into a mold using compressed air. Blow-molded nylon parts have good mechanical properties, including high strength and stiffness, and can be produced in complex shapes.
Properties of Nylon After Processing:
Nylon properties can be affected by processing methods. For instance, extruded nylon has a high degree of orientation, which results in high stiffness and low impact resistance. On the other hand, injection-molded nylon has a lower degree of orientation, resulting in lower stiffness and higher impact resistance. Blow-molded nylon parts have a lower degree of orientation than extruded or injection-molded parts, resulting in lower stiffness but higher impact resistance. After processing, nylon parts may also exhibit properties such as warpage, shrinkage, and stress cracking, which should be considered during the design process.
-
6.Nylon Testing and Properties
Testing nylon properties is essential to ensure that the material meets the required specifications for a specific application. Here’s an overview of some common tests used to evaluate nylon properties:
Tensile Strength Testing:
Tensile strength testing measures the maximum load that a nylon sample can bear before it breaks under tension. This test is commonly used to evaluate the strength and elasticity of nylon. Nylon has high tensile strength and elongation at break, making it suitable for applications that require high strength and flexibility.
Impact Strength Testing:
Impact strength testing measures the ability of a nylon sample to resist fracture when subjected to a sudden impact. This test is commonly used to evaluate the toughness of nylon. Nylon has good impact resistance due to its high ductility and energy-absorbing capability.
Moisture Absorption Testing:
Moisture absorption testing measures the amount of water that a nylon sample absorbs when exposed to a humid environment. Nylon has a high affinity for water, and its properties can be affected by moisture. Moisture absorption can cause dimensional changes, reduced mechanical properties, and reduced chemical resistance.
Chemical Resistance Testing:
Chemical resistance testing evaluates the resistance of nylon to various chemicals. Nylon has good chemical resistance to many solvents, oils, and acids. However, nylon may be degraded by some chemicals, such as strong acids, strong bases, and some organic solvents.
Comparison of Nylon Testing and Properties:
The testing and properties of nylon vary depending on the type of nylon and the specific application. For instance, Nylon 6 has higher moisture absorption than Nylon 6,6, making it unsuitable for some applications that require low water absorption. Nylon 6,6 has higher stiffness and temperature resistance than Nylon 6, making it suitable for high-temperature applications. When selecting a nylon type for a specific application, factors such as tensile strength, impact strength, moisture absorption, chemical resistance, and temperature resistance should be considered.
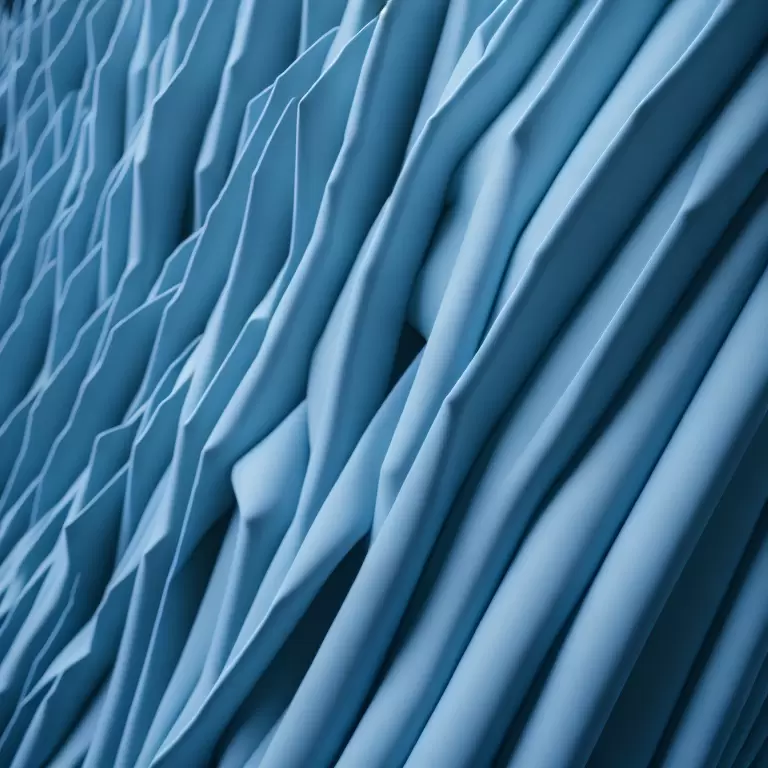
-
7.Conclusion
Nylon is a versatile material that has found numerous applications in various industries, including automotive, textile, consumer goods, and medical industries. Its excellent properties, such as high strength, stiffness, and chemical resistance, make it suitable for a wide range of applications.
In this guide, we have covered the chemical and physical properties of nylon, the different types of nylon and their properties, nylon applications, processing and properties, testing and properties, and a comparison of nylon properties. We have seen that the properties of nylon vary depending on the type of nylon, the processing method, and the specific application.
Looking to the future, nylon will continue to be a valuable material for various industries. With ongoing research and development, we can expect to see new types of nylon with improved properties and increased applications. For instance, Nylon 6,10 is a new type of nylon that offers improved strength and stiffness compared to traditional nylons, making it suitable for use in high-performance applications.
In conclusion, nylon is a material with a bright future, and its versatility, durability, and excellent properties make it a preferred choice for many applications. By understanding the properties and characteristics of nylon, we can make informed decisions when selecting a nylon type for a specific application.