Selective Laser Sintering (SLS) 3D Printing
SLS Parts In As Soon As 2 Days; Complex Geometries with High Performance Materials; Cost-Effective for Short-Run Production & Prototyping.
SLS 3D Printing Parts
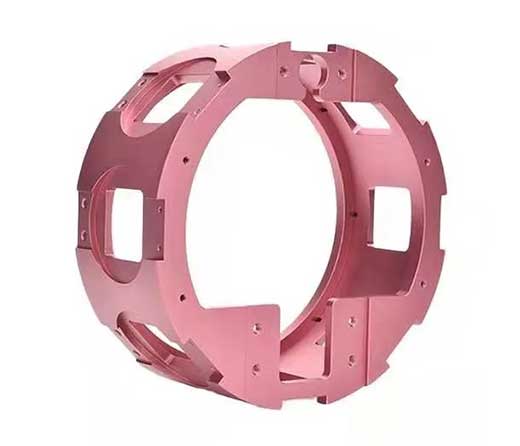

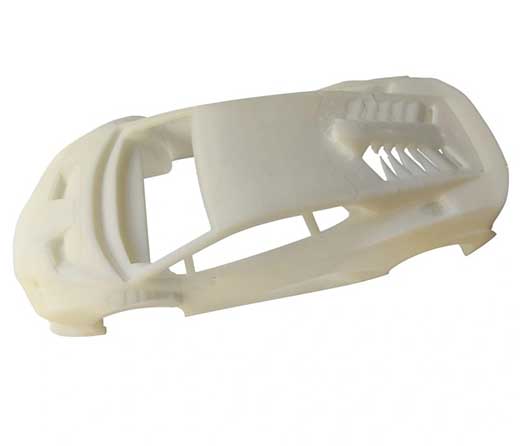
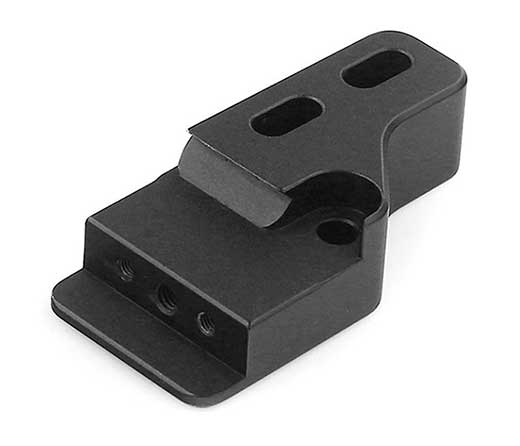
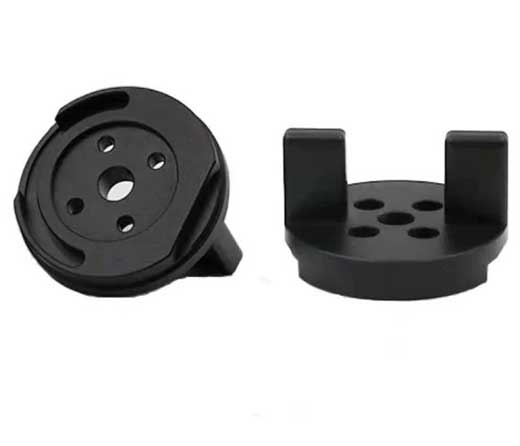
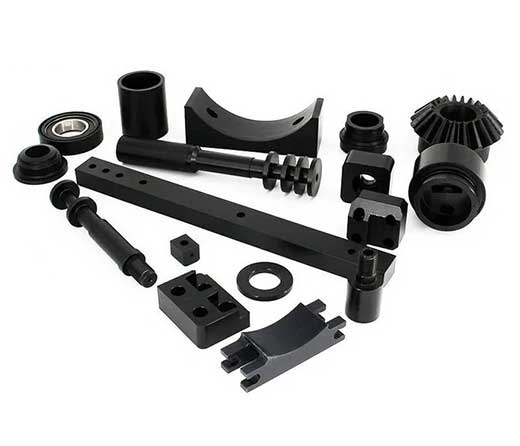
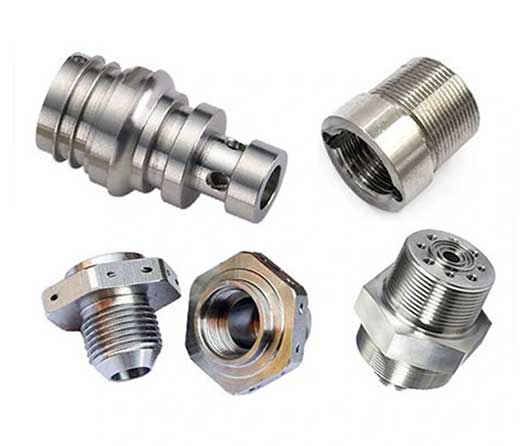
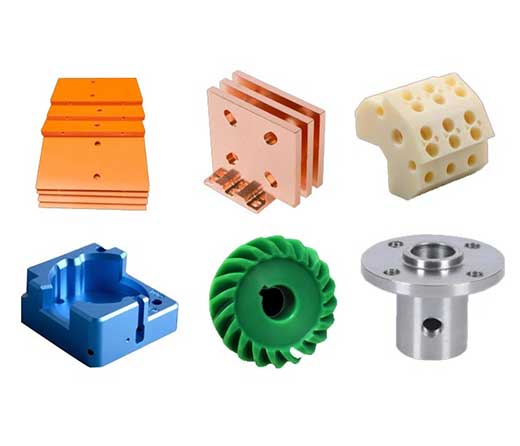
Selective Laser Sintering (SLS) 3D Printing services
Selective Laser Sintering (SLS) is a commonly used powder-based additive technology to create models, prototypes and end-use parts in durable, engineering-grade thermoplastics. Consider SLS technology for applications that involve high-complexity and organic geometries, as well as parts requiring durability. SLS nests in the z direction which allows for short-run production and efficient builds. This technology is also capable of producing parts with finer details than most other additive processes that use high-strength plastics. The composition is one of the more isotropic available from additive manufacturing.
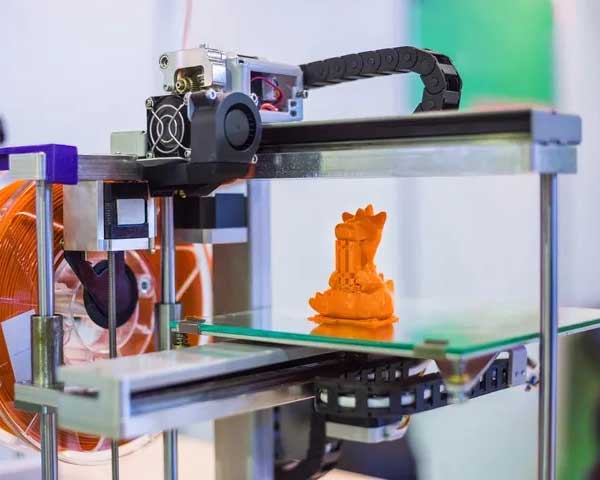
Applications of SLS 3D Printing
Designers and engineers across numerous industries have used SLS printing in their product development process. While SLS can be used for prototyping, it is also used for functional parts, testing and production parts.
SLS 3D printing has been used for consumer goods in the medical, footwear and beauty industries.
SLS has been used by motorsports companies to innovate vehicle design to increase performance.
Airline companies are incorporating lightweight SLS 3D parts on their aircraft including air vent grills and other cabin components.
Jigs, Fixtures & Other Tooling
Snap Fits & Living Hinges
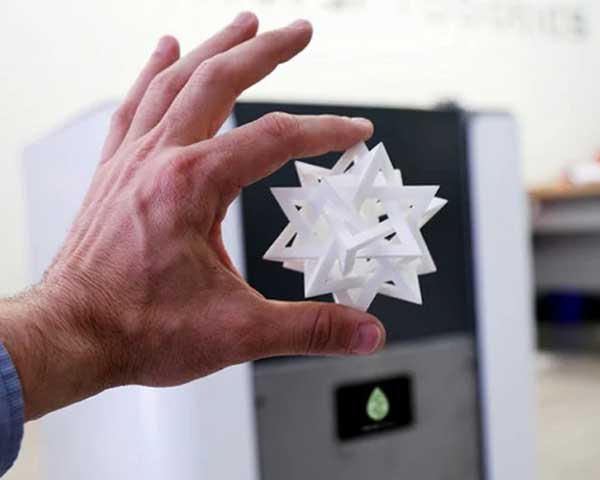
How does SLS Technology Work?
SLS uses a blade to spread a thin layer of powder over the build volume. A laser sinters the cross-section of the part to fuse the powder together. The z stage then drops one layer and the process begins again until the build is finished. Parts are then excavated from the build powder-cake so excess powder can be removed. The unused powder in the build envelope acts as the support structures which eliminates the need to remove support structures after the build process.
SLS 3D Printing Manufacturing FAQs
SLS (Selective Laser Sintering) is an additive manufacturing technique that uses laser beams to fuse powdered materials together to create three-dimensional objects.
Selective laser sintering (SLS) 3D printing technology is widely used in automobiles, aerospace, medical, industrial design and other fields. The main advantage of this technology is the ability to manufacture parts with complex shapes, high precision and superior performance.
First of all, in the automotive industry, SLS 3D printing technology can be used to manufacture various complex automotive parts, such as engine parts, brake system parts, etc. The shapes of these parts are often very complex and often difficult to achieve with traditional manufacturing methods. SLS 3D printing technology can easily print these complex shapes, greatly improving production efficiency and product quality.
Secondly, in the aerospace field, SLS 3D printing technology also has important applications. For example, it can be used to manufacture key components such as aircraft engine parts and fuel nozzles. The performance requirements of these components are very high and require high precision and strength. SLS 3D printing technology can meet these strict performance requirements and ensure the safe operation of aircraft.
In the medical field, SLS 3D printing technology is also widely used. It can be used to manufacture various medical devices, such as prostheses, teeth, artificial joints, etc. These devices require close contact with the human body, so the requirements for precision and performance are very high. SLS 3D printing technology can accurately print these devices to meet the needs of the medical industry.
In addition, in the field of industrial design, SLS 3D printing technology is also widely used. Designers can use this technology to create a variety of product prototypes with complex shapes and superior performance. This not only improves design efficiency but also reduces production costs.
Selective Laser Sintering (SLS) 3D printing technology is an advanced manufacturing process that is capable of producing parts with complex shapes, high precision and performance. The main advantage of this technology is its rapid manufacturing capabilities, which can greatly shorten the product development cycle. In addition, SLS 3D printing technology also has the advantages of material saving and waste reduction.
First, SLS 3D printing technology is capable of producing parts with complex shapes. This is because the technology uses a special laser to melt plastic powder layer by layer to create the desired three-dimensional structure. This allows designers to be more creative in the design process without having to worry about the limitations of traditional manufacturing processes.
Secondly, SLS 3D printing technology enables high-precision and high-performance parts production. Because the technology can precisely control the degree of melting of each layer of plastic powder, it ensures the quality of the final product. In addition, part performance can be further improved by optimizing printing parameters.
Furthermore, SLS 3D printing technology has the advantage of rapid manufacturing. Traditional manufacturing processes often require a lot of time and resources to produce parts, while SLS 3D printing technology can produce parts in a shorter time. This can not only greatly shorten the product development cycle, but also improve production efficiency.
In addition, SLS 3D printing technology also has the advantages of material saving and waste reduction. Because the technology melts plastic powder layer by layer to create parts, only the amount of material actually needed is used, reducing material waste. At the same time, since less waste is generated during the production process, it also helps reduce environmental pollution.
The materials used in selective laser sintering (SLS) 3D printing technology mainly include polyamide (PA), polyimide (PEI), nylon, carbon fiber, glass fiber, etc. These materials have excellent performance and broad application prospects in the 3D printing process.
First of all, polyamide (PA) is a high-performance engineering plastic with good wear resistance, chemical resistance and dimensional stability. In SLS 3D printing, PA can be used to manufacture high-strength, wear-resistant parts, such as gears, bearings, etc. In addition, PA also has good melt fluidity, which allows it to solidify quickly during the SLS printing process and improves printing efficiency.
Secondly, polyimide (PEI) is a high-performance thermoplastic polymer with excellent heat resistance, electrical insulation and mechanical strength. In SLS 3D printing, PEI can be used to manufacture parts used in high-temperature environments, such as electronic connectors, circuit boards, etc. At the same time, PEI also has good chemical resistance, allowing it to maintain good performance in harsh environments.
Nylon is a common engineering plastic with good toughness, wear resistance and weather resistance. In SLS 3D printing, nylon can be used to manufacture various structural parts, such as automobile parts, home appliance casings, etc. In addition, nylon also has good melt fluidity, which allows it to solidify quickly during the SLS printing process and improves printing efficiency.
Carbon fiber is a lightweight, high-strength material with excellent tensile strength and stiffness. In SLS 3D printing, carbon fiber can be used to manufacture lightweight, high-performance parts, such as parts in the aerospace field, sports equipment, etc. At the same time, carbon fiber also has good corrosion resistance and wear resistance, allowing it to maintain good performance in harsh environments.
Glass fiber is a commonly used reinforcing material with good mechanical properties and heat resistance. In SLS 3D printing, glass fiber can be combined with resins such as nylon and polyester to create composite parts with excellent properties. In addition, glass fiber also has good molding properties, allowing it to quickly solidify during the SLS printing process and improve printing efficiency.
The printing accuracy of SLS 3D printing technology can reach 0.1 mm, which mainly depends on the printer and materials used. This high-precision printing capability makes SLS technology widely used in many fields, such as manufacturing complex parts, prototyping and medical applications.
First, SLS 3D printing technology can be used to manufacture complex parts. Due to its high-precision printing capabilities, SLS technology can accurately replicate the designer's intent, resulting in parts with complex geometries and details. This has important implications for industries that require a high degree of precision and complexity, such as aerospace, automotive manufacturing, and medical devices.
Secondly, SLS 3D printing technology also has wide applications in prototyping. By using SLS technology, designers can quickly create physical models of products for testing and verification. Compared with traditional prototyping methods, SLS technology is faster and lower cost, while maintaining high printing accuracy. This makes SLS technology an indispensable tool in the product development process.
In addition, SLS 3D printing technology also plays an important role in the medical field. Due to its high-precision printing capabilities, SLS technology can create medical devices and implants that conform to human anatomy. These devices and implants can be used for surgical simulation, customized treatment plans, and personalized patient care. By using SLS technology, doctors can better understand a patient's condition and develop a more effective treatment plan.
In short, the high-precision printing capability of SLS 3D printing technology makes it have broad application prospects in manufacturing complex parts, prototyping and medical fields. With the continuous development and improvement of technology, I believe that SLS technology will play an important role in more fields and bring more innovation and convenience to all walks of life.
Selective Laser Sintering (SLS) 3D printing technology is an advanced manufacturing process whose layer thickness can vary depending on the printer and materials used. Generally speaking, the layer thickness of SLS 3D printing technology can range from 0.05 mm to 0.5 mm.
The core principle of this technology is to stack powders of specific materials layer by layer using a laser beam, which is then heated and solidified to form the final three-dimensional object. During this process, each layer of material is precisely controlled and positioned to ensure the quality and precision of the final product.
The choice of layer thickness is very important for the SLS 3D printing process. Thinner layer thicknesses provide higher resolution and finer detail for applications requiring high precision and complex geometries. For example, in the medical field, using thinner layer thicknesses can produce more accurate models of artificial bones or teeth.
However, thinner layer thicknesses may also result in increased printing time, as more layers are required to complete the build of the entire object. In addition, thinner layer thicknesses can also increase material waste, since each layer requires additional material to fill.
Conversely, thicker layer thickness can speed up printing and reduce material waste, but may reduce the resolution and detail of the printed object. Therefore, when choosing layer thickness, there are trade-offs based on specific application needs and printer performance.
In summary, the layer thickness of SLS 3D printing technology can vary from 0.05 mm to 0.5 mm, the specific choice depends on the characteristics of the printer and material as well as the required printing accuracy and speed. This flexibility makes SLS 3D printing technology widely applicable in various fields.
The manufacturing speed of SLS 3D printing technology depends on the printer used, the materials used, and the size and complexity of the part. Typically, this technology can produce dozens of parts per hour.
SLS 3D printing technology is a rapid prototyping technology based on the principle of Selective Laser Sintering. It builds three-dimensional objects by stacking layers of powder of a specific material and using a high-energy laser beam to sinter the powder layer by layer. Due to its unique working principle, SLS 3D printing technology has significant advantages in manufacturing speed.
First of all, printer performance is one of the key factors affecting manufacturing speed. High-performance SLS 3D printers are usually equipped with more advanced laser systems and control systems, enabling higher scanning speeds and more precise laser control. These advanced devices can complete the sintering process of each printed layer faster, thereby increasing overall manufacturing speed.
Secondly, the materials used also affect the manufacturing speed. Different SLS 3D printing materials have different melting points and sintering characteristics, so their manufacturing speeds will also vary. Some high-performance materials, such as nylon, polycarbonate, etc., have higher melting points and faster sintering speeds, which can complete the printing process faster.
In addition, the size and complexity of the part are also important factors that affect the speed of manufacturing. Larger parts require more time to complete the entire printing process, while complex geometries may require more printing layers. Therefore, manufacturing can be relatively slow for large and complex parts.
Overall, the manufacturing speed of SLS 3D printing technology can reach the level of dozens of parts per hour. However, the exact manufacturing speed will be affected by a variety of factors, including printer performance, material selection, and the size and complexity of the part. Therefore, when choosing SLS 3D printing technology, these factors need to be considered comprehensively to obtain the best manufacturing efficiency and cost-effectiveness.
Selective Laser Sintering (SLS) 3D printing technology requires a series of post-processing steps after completing the printing process to ensure the quality and performance of the final product. These post-processing methods include powder removal, baking, polishing and painting.
First, powder removal is an important step because during the printing process, uncured plastic powder will adhere to the surface of the printed part. By using a brush, vacuum cleaner or other tools, this excess powder can be effectively removed, leaving the print surface smoother and cleaner.
Next, baking is a critical step to ensure the print is fully cured. During the SLS 3D printing process, plastic powders are melted and solidified together by exposure to laser light. However, the heat of the laser alone may not fully cure the entire print. Therefore, the print is placed in an oven at high temperatures to ensure that it is cured to the ideal degree both inside and out.
Polishing is another important post-processing step that improves the surface quality and gloss of your prints. By using a polishing tool or machine, you can remove rough parts of the surface of your print, making it smoother and more refined. This is especially important for prints that need to have a good look and feel.
Finally, painting is an essential post-processing step in many applications. By applying a protective coating to the surface of your print, you can increase its durability and water resistance while also improving its appearance. Painting can be carried out using a variety of coatings and spraying techniques to suit the needs of different applications.
In short, the post-processing methods of SLS 3D printing technology include powder removal, baking, polishing and painting. These steps not only improve the quality and performance of your prints, but also meet the needs of different applications.
SLS 3D printing technology can improve the surface quality of the parts through post-processing after printing is completed. Post-processing includes a variety of methods, such as heat treatment, spraying, electroplating, etc., which can further increase the density and strength of the part while reducing the porosity in the part.
First, heat treatment is a common post-processing method that changes the physical properties of parts through the process of heating and cooling. For SLS 3D printed parts, heat treatment can increase their density and strength, making them stronger and more durable. For example, by heating a part to a certain temperature and holding it there for a period of time, the materials inside the part can be rearranged, thereby increasing its density. In addition, heat treatment can eliminate stress in the part and improve its resistance to deformation.
Secondly, spraying is a common post-processing method that can improve the surface quality of parts. SLS 3D printed parts usually have rough surfaces, and spraying can form a protective film on the surface of the part to make it smoother and more uniform. Spray coating can also provide additional functions such as corrosion protection, wear resistance, etc., thus increasing the service life of parts.
In addition, electroplating is also a common post-processing method that can increase the corrosion resistance and conductivity of parts. A layer of metal plating can be formed by immersing the part in a solution containing metal ions and depositing the metal ions on the surface of the part under the action of an electric current. This metal coating not only improves the corrosion resistance of the part, but also provides good electrical conductivity.
To sum up, post-processing of SLS 3D printing technology can significantly improve the surface quality of parts, increase their density and strength, and reduce porosity in parts. These post-processing methods can be selected and combined according to specific needs to meet the performance requirements of parts in different fields.
Selective Laser Sintering (SLS) 3D printing technology is an advanced manufacturing process that is capable of producing parts of various sizes. The flexibility of this technology allows it to be adapted to a variety of different needs, whether it is small precision parts or large complex structures.
First of all, we need to understand that the maximum size of SLS 3D printing technology is not fixed, but depends on the printer and materials used. Different printers have different print spaces, which means the part sizes they can handle will vary. For example, some high-end SLS printers may have a larger print volume and therefore can produce larger sized parts.
Secondly, the 3D printing material used will also affect the size of the final part. Different materials have different physical properties, such as strength, hardness and heat resistance, which may limit the size of a part. In addition, the material's flow and solidification speed may also affect the size of the part.
In general, the maximum size of SLS 3D printing technology is determined by the printing space of the printer and the 3D printing material used. So if you need to produce parts of a specific size, you need to choose the right printer and materials.
There is a certain relationship between the printing accuracy and layer thickness of SLS 3D printing technology. Generally speaking, the thinner the layer thickness, the higher the printing accuracy. This is because during the SLS 3D printing process, the printer builds the object by stacking material layer by layer. The material thickness of each layer determines the accuracy and surface quality of the printed object.
When the layer thickness is thinner, the printer can more precisely control the deposition location and shape of each layer. This means it can better replicate the details and geometry of a design, increasing the accuracy of printed objects. In addition, thinner layer thickness can also reduce stress and deformation during the printing process, further improving the stability and quality of printed objects.
However, it is important to note that layer thickness that is too thin may result in slower printing speeds because the printer needs more time to deposit material layer by layer. In addition, too thin a layer thickness can lead to material waste, as the printer may deposit too much material on each layer. Therefore, there is a trade-off between print accuracy and print speed when choosing layer thickness.
In short, there is a close relationship between the printing accuracy and layer thickness of SLS 3D printing technology. Thinner layer thickness can improve printing accuracy and surface quality, but may increase printing time and risk of material waste. Therefore, when selecting layer thickness, a comprehensive consideration needs to be based on specific application requirements and printer performance.
Common question in SLS 3D Printing Production
The materials used in SLS 3D printing technology have high strength and rigidity, which can reach a level comparable to or even higher than traditional manufacturing.
Selective laser sintering (SLS) 3D printing technology is an advanced manufacturing process that has significant advantages in many aspects. First, this technology can effectively save materials and energy. By precisely controlling the printing process, SLS 3D printing can reduce material waste, thereby lowering production costs. In addition, due to its efficient use of energy, this technology also produces relatively low carbon emissions during production.
Secondly, SLS 3D printing technology helps reduce waste generation. Traditional manufacturing methods often produce large amounts of waste and by-products, while 3D printing avoids this by printing the entire part in one go. Not only does this reduce the cost of waste disposal, it also reduces the impact on the environment.
Finally, SLS 3D printing technology is highly environmentally friendly. Since its production process does not require the use of harmful chemicals, this technology has less impact on the environment and human health. In addition, due to its ability to accurately print complex geometries, SLS 3D printing technology can also be used to produce lighter and more durable products, further reducing energy consumption and waste generation.
The cost of SLS 3D printing technology is indeed higher than that of traditional manufacturing technology. However, in some application areas, this technology can effectively save time and cost.
First, SLS 3D printing technology has significant advantages in prototyping. The traditional manufacturing process usually requires multiple steps, including design, mold making, injection molding, etc. These steps are not only time-consuming, but also costly. Using SLS 3D printing technology, designers can directly import design files into the printer to quickly produce accurate prototypes. As a result, companies can design and verify products faster, saving a lot of time and costs.
Secondly, SLS 3D printing technology also has advantages in small batch production. For traditional manufacturing technology, small batch production often requires a large amount of manpower and material resources, and the cost is high. SLS 3D printing technology can realize on-demand production, that is, customized production according to customer needs, avoiding inventory backlog and waste. In this way, companies can flexibly adjust production plans according to market demand and reduce production costs.
In addition, SLS 3D printing technology can also realize the manufacturing of complex structures. Traditional manufacturing technology is often limited by the production and processing capabilities of molds and cannot produce complex geometric shapes. SLS 3D printing technology can easily produce complex structural parts by stacking layer by layer. In this way, companies can design more innovative products and improve product competitiveness.
In summary, although the cost of SLS 3D printing technology is relatively high, in some specific application fields, it can bring time savings and cost reductions. With the continuous development and maturity of technology, I believe that SLS 3D printing technology will be widely used in more fields and bring more economic benefits to enterprises.
Compared with the two 3D printing technologies of FDM and SLA, SLS (selective laser sintering) 3D printing technology has higher precision, better surface quality and wider application fields. However, this also means that its cost is relatively high.
First, SLS 3D printing technology excels in terms of accuracy. Because it works by building objects by sintering powder material layer by layer with a laser beam, very fine prints can be achieved. In contrast, FDM and SLA technologies may have some problems with loose bonding between layers during the printing process, resulting in higher surface roughness of the final product. SLS technology can better control the focus and scanning speed of the laser beam, thereby achieving higher printing accuracy.
Secondly, SLS 3D printing technology also has advantages in surface quality. Because the materials used are usually powdered nylon or metal powder, these materials will form a uniform particle structure during the laser sintering process, resulting in a smoother surface of the final product. In contrast, FDM and SLA technologies may produce some bubbles or flow traces of molten material during the printing process, affecting the appearance quality of the product.
In addition, SLS 3D printing technology also has a wider range of applications. Because it can print objects with complex geometric shapes and internal structures, it has broad application prospects in aerospace, automobile manufacturing, medical equipment and other fields. In contrast, FDM and SLA technologies have relatively few applications in these fields.
However, despite the many advantages of SLS 3D printing technology, its relatively high cost is also a problem that cannot be ignored. Because it requires the use of special powder materials and laser equipment, as well as subsequent processing and post-processing work, its cost is usually much higher than traditional FDM and SLA technologies. This is also one of the important factors limiting the popularity of SLS technology.
The printing speed of SLS 3D printing technology is affected by the size and complexity of the part. Specifically, larger and more complex parts take longer to manufacture. This is because during the SLS 3D printing process, the printer needs to stack materials layer by layer to build the part. For large parts, the printer requires more time to complete each layer, so the overall manufacturing time increases accordingly.
In addition, the design of complex parts usually involves more details and curves, which increases the difficulty for the printer to handle during the printing process. Printers need more time to accurately print these complex geometries to ensure the quality and accuracy of the final part.
In addition, SLS 3D printing technology uses a method called Selective Laser Sintering. In this process, a laser beam is used to heat powder material to a molten state, which is then solidified layer by layer to form the part. Because the process occurs layer by layer, large and complex parts require more laser beam scanning and material handling steps, increasing manufacturing time.
Selective Laser Sintering (SLS) 3D printing technology is an advanced manufacturing process that can print multiple parts at the same time, thereby significantly improving production efficiency. This technology creates complex three-dimensional structures by melting and solidifying specific materials, such as plastic or metal powder, layer by layer using high-powered laser beams.
SLS 3D printing technology offers many advantages over traditional manufacturing methods. First, it can produce a large number of parts in a short time, which is very beneficial for mass production. Second, because each part is precisely printed from a computer-aided design (CAD) model, a high degree of consistency and accuracy is ensured for each part. In addition, SLS 3D printing technology is highly flexible and can easily adapt to parts of various shapes and sizes.
In practical applications, SLS 3D printing technology has been widely used in various fields, such as aerospace, automobile manufacturing, medical care, education, etc. For example, in the aerospace field, engineers can use SLS 3D printing technology to quickly manufacture complex aerospace parts, such as engine components, fuel nozzles, etc. Not only are these components highly precise and strong, they are also lightweight, helping to reduce the overall weight of the aircraft, thereby improving fuel efficiency.
In short, SLS 3D printing technology, as an advanced manufacturing process, provides an effective way to improve production efficiency by printing multiple parts at the same time. With the continuous development and improvement of technology, we have reason to believe that SLS 3D printing technology will play an increasingly important role in the future manufacturing industry.
The materials used in SLS 3D printing technology have good high temperature resistance and can withstand applications in high temperature environments. The materials used in this technology are usually special plastics called thermoplastic resins, which have excellent resistance to heat and chemicals.
First of all, the materials used in SLS 3D printing technology can maintain stable performance in high-temperature environments. This means that even at high temperatures, these materials maintain their shape and size stability without deforming or melting. This makes SLS 3D printing technology very reliable when manufacturing parts and components used in high-temperature environments.
Secondly, the materials used in SLS 3D printing technology have good heat resistance. This means they can be used in high temperature environments for extended periods of time without performance degradation or damage. This is important for parts and assemblies that require long-term use in high-temperature environments, as they need to have sufficient heat resistance to ensure their reliability and durability.
In addition, the materials used in SLS 3D printing technology also have excellent chemical resistance. This means they are resistant to a wide range of chemicals, including acids, bases and solvents. This makes SLS 3D printing technology very advantageous when manufacturing parts and components that need to be used in chemically corrosive environments.
In general, the materials used in SLS 3D printing technology have good temperature resistance and can withstand applications in high-temperature environments. This makes it very reliable and suitable when manufacturing parts and components that need to be used in high temperature environments. Whether it is aerospace, automotive manufacturing or medical fields, SLS 3D printing technology can provide these industries with high-quality, high-performance parts and components.
The materials of SLS 3D printing technology can be customized in color according to customer needs and can be produced according to customer needs. This customized production method allows customers to choose the color of the material according to their own preferences and needs, thereby obtaining a more personalized product. Whether for individual users or corporate customers, this customized service can provide a better user experience and meet their needs.
Through SLS 3D printing technology, customers can choose from a variety of different colors to make their products. Whether it's bright colors or pastel tones, it can be achieved by adjusting the color of the material. This customization option allows customers to more freely express their thoughts and creativity during the design process, resulting in unique products.
In addition, SLS 3D printing technology is also highly flexible and can manufacture materials according to customers' specific needs. Whether it is for small batch production or high-volume production, it can be achieved by adjusting printing parameters and material formulas. This customized production method can not only meet the individual needs of customers, but also improve production efficiency and reduce costs.
In short, the material customization service of SLS 3D printing technology provides customers with more choices and flexibility. Customers can customize the product according to their needs, both in terms of color and material manufacturing. This customized production method can not only meet the individual needs of customers, but also improve production efficiency and reduce costs, providing customers with better experience and services.
Selective laser sintering (SLS) 3D printing technology is an advanced manufacturing process that can accurately print complex three-dimensional shapes and internal structures. The main advantages of this technology are its flexibility and precision, making it ideal for manufacturing a wide range of complex parts.
First of all, SLS 3D printing technology can print a variety of complex three-dimensional shapes. Whether it is simple geometric shapes such as cubes, cylinders and cones, or more complex shapes such as spirals, waves, etc., they can all be easily realized with this technology. This gives designers unlimited room for innovation, allowing them to design more unique and personalized products.
Secondly, SLS 3D printing technology can also print out internal structures. This means that not only the external shape of an object can be printed, but also the cavities and channels inside the object. This is very useful for manufacturing parts that require internal structures, such as pipes, gears, honeycomb structures, etc. These internal structures can improve the performance of the part, such as increasing strength, reducing weight, improving thermal conductivity, etc.
In addition, SLS 3D printing technology also features high precision. Because this technology uses lasers to melt plastic powder layer by layer, the shape and thickness of each layer can be precisely controlled, ensuring a highly precise final product. This is very important for parts that require high precision, such as aerospace components, medical equipment, etc.
Overall, SLS 3D printing technology is a powerful manufacturing tool that can print complex three-dimensional shapes and internal structures, providing unlimited design possibilities while ensuring product accuracy and performance.
The printing effect of SLS 3D printing technology is closely related to the accuracy of the CAD model. The higher the accuracy of the model, the better the printing effect will be. This is because SLS 3D printing technology builds objects by stacking materials layer by layer, while CAD models are three-dimensional models created through computer-aided design software. Therefore, if the accuracy of the CAD model is not high enough, errors will occur during the printing process, resulting in unsatisfactory final printing results.
In order to obtain better printing results, you first need to ensure that the accuracy of the CAD model is high enough. This can be achieved through the use of professional CAD software and precise measurement tools. During the design process, problems such as distortion, overlap, or missing geometric figures should be avoided as much as possible to ensure the accuracy of the model.
Secondly, you also need to pay attention to the size and proportion of the CAD model. If the size or proportions of the model are incorrect, problems can occur during the printing process. For example, if the size of the model is too large or too small, it may cause the print to fail or the printed object not to be as expected. Therefore, when designing a CAD model, the appropriate size and proportion should be determined based on actual needs and printer limitations.
In addition, attention needs to be paid to the surface quality and topology of the CAD model. If the surface quality of the model is not good, such as having too many depressions, ridges, or edges, problems may occur during the printing process. Likewise, if the topology of the model is unreasonable, such as if there are too many support structures or intersections, problems may occur during the printing process. Therefore, when designing a CAD model, you should try to keep the surface flat and the topology reasonable.
Finally, you also need to pay attention to the file format and printer requirements of the CAD model. Different 3D printers may have different requirements for file formats, so when exporting CAD models you should choose a file format suitable for the printer. At the same time, you should also understand the printer's capabilities and limitations so that you can make appropriate adjustments when designing your CAD model.
In summary, to obtain better SLS 3D printing results, it is necessary to ensure that the accuracy of the CAD model is high enough, the size and proportion are appropriate, the surface quality is good, the topology is reasonable, and the file format meets the requirements of the printer. Only by making preparations in these aspects can we ensure that the final printing effect meets expectations.
SLS 3D printing technology is a manufacturing method that uses laser beams to melt and solidify specific materials layer by layer. During the printing process, heat is needed to ensure that the materials are fully melted and bonded together.
First, the printer lays a thin layer of powder material on the workbench. The laser beam then scans the entire powder layer along a pre-set path. When the laser beam hits the surface of the powder, it rapidly absorbs heat, causing the powder material to begin to melt.
As the laser beam moves, the molten material forms a thin pool on the surface. The material in this molten pool gradually cools and solidifies, forming a solid structure. At the same time, the printer will continue to move downward to prepare for the melting and solidification of the next layer of powder material.
Temperature control is very important during the entire printing process. If the temperature is too high, the powder material may melt excessively, causing deformation or defects in the print. Conversely, if the temperature is too low, the powder material may not melt sufficiently, causing the print to be insufficiently strong or unable to bond together.
In order to ensure the stability of the printing process and the quality of the printed parts, SLS 3D printers are usually equipped with advanced temperature control systems. This system can adjust the power and scanning speed of the laser beam in real time based on the geometry and material properties of the printed part to maintain optimal melting and solidification results.
In general, the printing process of SLS 3D printing technology requires heating to ensure that the materials can fully melt and bond together. Through precise temperature control and laser beam scanning, high-quality, high-precision print manufacturing can be achieved.
The file printing formats of SLS 3D printing technology include common STL and OBJ formats, and can also be customized according to needs. The flexibility of this technology allows users to choose the appropriate print format based on their specific needs. Whether using STL or OBJ format, the accuracy and efficiency of the printing process can be ensured.
STL (Stereolithography) is a commonly used 3D printing file format that represents the geometry of an object in the form of a triangular mesh. STL files can contain multiple triangle patches, each patch consisting of a series of points and the edges connecting these points. The advantage of this format is that it is simple and easy to understand and easy to import into various 3D modeling software for editing and modification.
OBJ (Object) is another common 3D printing file format, which is also a geometric representation method based on vertices and faces. Unlike STL, OBJ files can contain more information, such as normal vectors, texture coordinates, etc. This allows OBJ files to better preserve the details and surface properties of the original model.
In addition to the common STL and OBJ formats, SLS 3D printing technology also supports file formats customized according to user needs. This means that users can create print file formats that suit their needs, based on their specific requirements. This ability to customize provides users with greater flexibility and freedom to better meet their printing needs.
In short, the file printing formats of SLS 3D printing technology include common STL and OBJ formats, and also support customization according to needs. No matter which format is used, the printing process is accurate and efficient. This flexibility allows users to choose the appropriate printing format according to their specific needs, thereby obtaining better printing results.