Table of Contents:
- Introduction
- ABS Material Properties
- Injection Molding Process
- Types of ABS Injection Molding Techniques
- Applications of ABS Injection Molding
- Advantages of ABS Injection Molding
- Challenges and Solutions
- Future Trends
- Conclusion
-
1.Introduction
ABS injection molding is a manufacturing process that involves the injection of Acrylonitrile Butadiene Styrene (ABS) thermoplastic material into a mold cavity. The melted material is then cooled and solidified to produce a final product.
ABS injection molding has been around since the 1940s when it was first developed by the chemical company, BASF. Since then, the technology has continued to evolve, and it is now widely used in various industries due to its versatility, durability, and ease of processing. In this article, we will explore the basics of ABS injection molding, including its material properties, injection molding process, techniques, applications, advantages, challenges, and future trends.
-
2.ABS Material Properties
Acrylonitrile Butadiene Styrene (ABS) is a thermoplastic polymer that is composed of three monomers: acrylonitrile, butadiene, and styrene. The chemical composition of ABS can vary depending on the specific application and manufacturer.
Physical properties:
- Density: 1.05 g/cm3
- Tensile strength: 40-50 MPa
- Flexural strength: 70-80 MPa
- Heat deflection temperature: 90-100 °C
- Notch impact strength: 7-12 kJ/m2
- Glass transition temperature: 100-110 °C
Advantages:
- High impact resistance
- Good dimensional stability
- Excellent surface finish
- Wide range of color options
- Easy to process and mold
- Good chemical resistance
Disadvantages:
- Low heat resistance
- Low resistance to UV light and weathering
- Susceptible to warping and shrinkage
- Poor solvent resistance
The unique combination of ABS material properties makes it ideal for a variety of applications, including automotive parts, electronic enclosures, toys, and household appliances.
-
3.Injection Molding Process
Injection molding is a manufacturing process that involves the production of parts by injecting molten material into a mold cavity. Here are the key aspects of the injection molding process for ABS:
Mold design:
- Designing the mold involves creating a cavity that matches the final product shape.
- Mold design also includes determining the gate location, runner size, and cooling system.
- The mold is typically made of steel and can be custom-designed for specific applications.
Equipment and machinery:
- Injection molding machines consist of a hopper that feeds the ABS material into a heated barrel.
- The material is then melted and injected into the mold cavity under high pressure.
- The machine includes a clamping unit that applies pressure to the mold to ensure proper filling and cooling.
Steps of the process:
- Material preparation: The ABS material is loaded into the hopper and fed into the heated barrel, where it is melted.
- Injection: The molten material is injected into the mold cavity under high pressure, filling the cavity and forming the part.
- Cooling: The mold is cooled to solidify the material and ensure the part retains its shape.
- Ejection: Once the part is cooled, it is ejected from the mold cavity.
- Finishing: The part may undergo additional processing, such as trimming, drilling, or painting.
The injection molding process can be used to produce high volumes of parts with consistent quality and accuracy, making it an efficient and cost-effective manufacturing method for ABS parts.
-
4.Types of ABS Injection Molding Techniques
There are various types of injection molding techniques used for ABS, including:
- Injection molding - This is the most common technique, where the molten ABS material is injected into a mold cavity to form a solid part.
- Structural foam molding - In this technique, a chemical blowing agent is added to the molten ABS material to create a foam core. This process results in a part that is lighter in weight but has higher strength-to-weight ratio.
- Gas-assisted molding - This technique involves injecting nitrogen gas into the molten ABS material to hollow out the part and create a thin-walled structure.
-
5.Applications of ABS Injection Molding
ABS injection molding is used in a wide range of applications, including:
- Automotive industry - ABS is commonly used in automotive interiors and exteriors, such as instrument panels, bumpers, and trim parts.
- Electronic and electrical industry - ABS is used in the manufacturing of electronic and electrical components, such as computer housing, keyboards, and printers.
- Consumer goods - ABS is used in the production of toys, luggage, and kitchen appliances, among others.
- Medical devices - ABS is used in the manufacturing of medical devices such as incubators, surgical instruments, and laboratory equipment due to its biocompatibility and sterilization capabilities.
The versatility of ABS injection molding makes it suitable for a broad range of industries and applications, from consumer products to industrial components.
-
6.Advantages of ABS Injection Molding
ABS injection molding offers several advantages over other manufacturing processes, including:
- High-quality production - Injection molding allows for the production of high-quality and consistent parts, with little variation between individual parts. This results in parts that meet or exceed specifications and have excellent surface finishes.
- Low waste production - The injection molding process produces very little waste material, as any excess material can be reused in future production runs. This makes it a highly efficient and sustainable manufacturing process.
- Cost-effective - Injection molding is a highly automated and repeatable process, which makes it a cost-effective manufacturing method for high-volume production runs. It also offers lower per-unit costs compared to other manufacturing processes like machining or casting.
The combination of these advantages makes ABS injection molding an attractive option for manufacturers who need to produce large quantities of high-quality parts in a cost-effective and efficient manner.
-
7.Challenges and Solutions
While ABS injection molding offers many benefits, there are also some challenges that manufacturers may encounter. Here are some of the key challenges and their potential solutions:
- Warpage and shrinkage - ABS material is prone to warpage and shrinkage during the cooling process, which can affect the final part dimensions and surface finish. Solutions to this problem include optimizing the cooling process, adjusting the mold design, and using additives to reduce shrinkage.
- Mold design and maintenance - Mold design and maintenance are critical factors that can affect the quality and consistency of the final product. To address these challenges, manufacturers should ensure that their molds are properly designed, built, and maintained to prevent defects and prolong the mold’s lifespan.
- Recycling and sustainability - While ABS is a highly versatile and widely used material, it can also be difficult to recycle. To address this challenge, manufacturers can explore sustainable production methods, such as using recycled materials in the injection molding process, reducing waste, and designing products that are easy to disassemble and recycle at end-of-life.
By addressing these challenges, manufacturers can optimize their ABS injection molding processes to produce high-quality parts with minimal waste and environmental impact.
-
8.Future Trends
As technology advances, there are several emerging trends in ABS injection molding that manufacturers should keep an eye on, including:
- 3D printing and ABS injection molding - 3D printing is an additive manufacturing technology that offers several advantages over traditional injection molding, such as greater design flexibility and faster prototyping. However, 3D printing is still limited in terms of material selection and production volume. One emerging trend is the integration of 3D printing with ABS injection molding, where 3D printing is used to create molds for injection molding, allowing for greater design flexibility and faster time-to-market.
- Emerging applications - ABS injection molding is already used in a wide range of applications, but there are still emerging areas where it can be applied. One example is in the production of lightweight and high-strength parts for the aerospace industry. Another emerging application is in the production of bio-based and biodegradable ABS materials, which offer a sustainable alternative to traditional petroleum-based ABS.
As these and other emerging trends continue to develop, ABS injection molding is likely to remain a critical manufacturing process for a wide range of industries and applications. Manufacturers who stay up-to-date with these trends and adapt their processes accordingly will be well-positioned to succeed in the years ahead.
Click on the V1 Prototype website to gain more information.
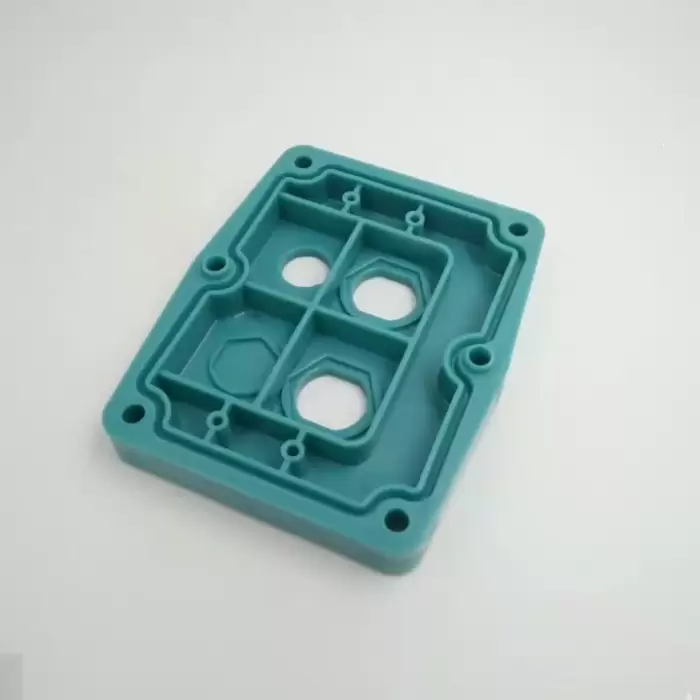
-
9.Conclusion
ABS injection molding is a widely used manufacturing process that offers many benefits, including high-quality production, low waste production, and cost-effectiveness. By optimizing their injection molding processes and addressing key challenges, manufacturers can produce high-quality parts with minimal waste and environmental impact.
Looking to the future, emerging trends such as the integration of 3D printing and the production of bio-based and biodegradable ABS materials offer exciting prospects for the continued growth and development of ABS injection molding. By staying up-to-date with these trends and adapting their processes accordingly, manufacturers can continue to leverage the many advantages of ABS injection molding and meet the evolving needs of their customers and the market.
In conclusion, ABS injection molding is a critical manufacturing process with a bright future ahead, and manufacturers who embrace its potential and overcome its challenges will be well-positioned to thrive in the years to come.