3D printing technology has brought tremendous advancements in the manufacturing industry. It has revolutionized the way we create products, from rapid prototyping to mass production. One of the most exciting advancements in 3D printing technology is the ability to print metal objects. This article provides a set of diagrams to help you understand metal 3D printing technology, including the technique used for metal printing and the technologies involved.
With the rapid development of 3D printing technology in recent years, it is rapidly changing the way we traditionally produce and live. As a typical representative of the emerging manufacturing technology, metal 3D printing technology, which was earlier applied in the aerospace field, has shifted more to the industrial, automotive, medical, mould and die, education and jewellery markets. How much do you know about the technology Today I would like to explain the mainstream metal 3D printing technology.
There are now five mainstream metal 3D printing technologies: laser-selective sintering (SLS), nanoparticle jet metal forming (NPJ), laser-selective melting (SLM), laser near net forming (LENS) and electron beam selective melting (EBSM) technologies.
Selective Laser Sintering (SLS)
The entire SLS process unit consists of a powder cylinder and a forming cylinder. The powder cylinder piston rises and a powder laying carriage spreads a uniform layer of powder over the forming cylinder, while a computer controls the 2D scanning trajectory of the laser beam to selectively sinter the solid powder material to form a layer of the part based on a slice model of the prototype. After a layer is completed, the working piston drops one layer thickness and the powder laying system lays down a new layer, controlling the laser beam to scan and sinter the new layer again. This cycle is repeated, layer by layer, until the three-dimensional part is formed.
The laser-selective sintering process:
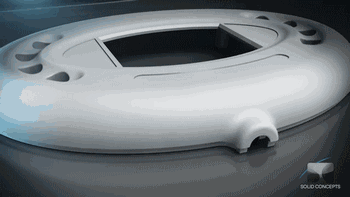
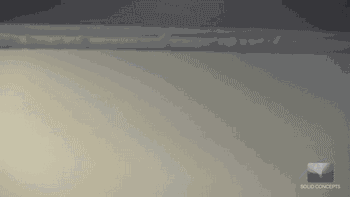
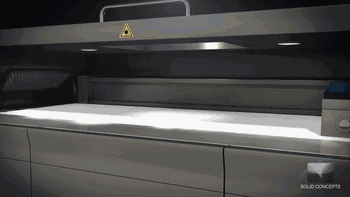
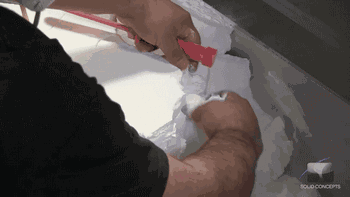
Nanoparticle Jet Metalforming (NPJ)
While it is well known that ordinary metal 3D printing technology uses laser melting or laser sintering of metal powder particles, Nanoparticle Jet Jetting (NPJ) technology uses a liquid form rather than a powder form. The metal is encased in a tube in liquid form and inserted into a 3D printer, where it is shaped by a jet of 'iron' containing metal nanoparticles during the 3D printing of the metal. The benefit is that by printing the metal in iron water, the whole model is more rounded and can be used as a tool with a normal inkjet print head. When the print is complete, the build chamber is heated to evaporate the excess liquid, leaving only the metal part behind.
Nanoparticle jet metal forming process:
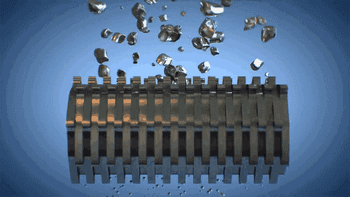
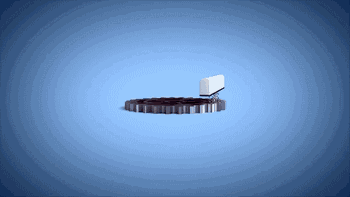

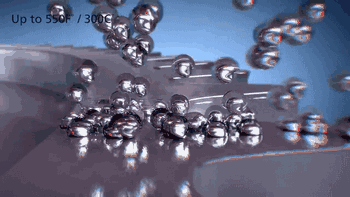
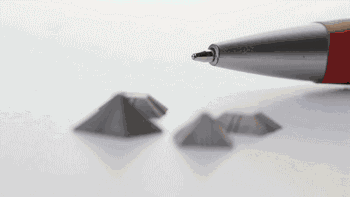
Laser Selective Melting (SLM)
The basic principle of laser selective melting technology is to first design a 3D solid model of the part on a computer using 3D modelling software such as Pro/e, UG, CATIA, etc., and then slice and layer the 3D model through slicing software to obtain the contour data of each section, and generate filled scan paths from the contour data. The machine will follow these fill scan lines and control the laser beam to selectively melt the layers of metal powder material, gradually stacking them into a 3D metal part. Before the laser beam starts scanning, the powder laying device first pushes the metal powder onto the substrate of the forming cylinder, the laser beam then follows the filling scan line of the current layer, selectively melting the powder on the substrate and processing the current layer, then the forming cylinder drops a layer thickness distance, the powder cylinder rises a certain thickness distance, the powder laying device then spreads the metal powder on the current layer that has been processed, the device transfers the next layer of contour data for processing. So layer by layer until the entire part is processed.
The laser zone melting process:
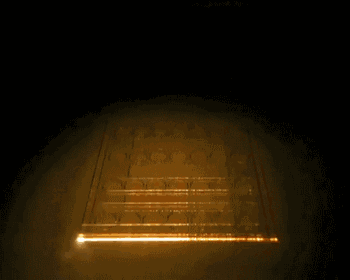
Laser Near Net Shaping (LENS)
Laser Near Net Structuring (LENS) technology uses the principle of simultaneous operation of laser and powder conveying. The computer slices the 3D CAD model of the part in layers and obtains the 2D planar profile data of the part, which in turn is transformed into the movement path of the CNC table. LENS enables the manufacture of metal parts without moulds, resulting in significant cost savings.
The laser near net forming process:
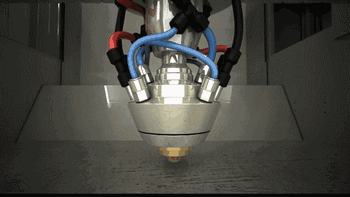
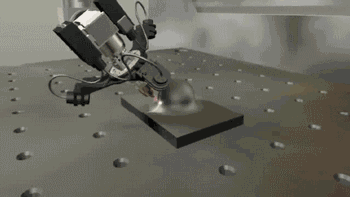
What do you understand by 3D printing technique?
Overview
3D printing, also known as additive manufacturing, is a technique of creating three-dimensional objects from a digital file. The 3D printer builds the object layer by layer, based on the instructions given by the design software. Traditional manufacturing methods, such as machining or injection molding, are subtractive processes that involve removing material from a larger piece. In contrast, 3D printing is an additive process that can create complex geometries that would otherwise be either impossible or too expensive to create using traditional manufacturing methods. 3D printing is used across multiple industries, from healthcare to aerospace, and continues to evolve and improve.
Which 3D printing technique is used for metal printing?
Overview
There are several 3D printing techniques used for metal printing. However, the most common method of metal 3D printing is a technique known as powder bed fusion. This technique involves melting metal powder layer by layer, using a laser or electron beam, to create a solid metal object.
Powder Bed Fusion Metal Printing Process
The powder bed fusion metal printing process involves several steps:
- The 3D model of the object is created using computer-aided design (CAD) software.
- The model is then sliced into layers using specialized software that generates instructions for the printer.
- The printer reads the instructions and applies a thin layer of metal powder to the build plate.
- A laser or electron beam is then directed at the powder bed to melt the metal particles and fuse them together.
- The build platform moves down, and the process is repeated until the final object is complete.
- When the printing process is complete, the metal object is removed from the build chamber and cleaned to remove any remaining powder.
What technologies are used in 3D printing?
Fused Deposition Modeling (FDM)
Fused deposition modeling (FDM) is one of the most common 3D printing technologies used today. It works by depositing melted material layer by layer to create a 3D object. FDM uses thermoplastics such as ABS or PLA, which are melted and extruded through a nozzle to create the object. FDM is a versatile and cost-effective method of 3D printing that can be used to create a wide range of objects, including prototypes, tools, and final parts.
Stereolithography (SLA)
Stereolithography (SLA) is a popular 3D printing technology used to create detailed, high-precision objects. SLA uses a vat of liquid photopolymer resin that solidifies when exposed to ultraviolet light. The printer uses a laser or light to draw the pattern of each layer, solidifying the resin to create the final object.
Selective Laser Sintering (SLS)
Selective laser sintering (SLS) is a 3D printing technology used to create parts with complex geometries or those with internal channels. SLS works by using a laser to selectively fuse powdered materials, such as nylon or metal, into a solid object. The unsintered powder acts as a support structure, allowing for the creation of complex geometries that would be impossible to achieve using traditional manufacturing methods.
Electron Beam Melting (EBM)
Electron beam melting (EBM) is a 3D printing technology used for creating metal objects. EBM works by melting metal powder using an electron beam. It is similar to powder bed fusion but uses an electron beam instead of a laser to melt the metal particles. EBM can create objects with high precision and accuracy, making it suitable for creating medical implants, aerospace components, and other high-performance applications.
Binder Jetting (BJ)
Binder jetting (BJ) is a 3D printing technology used to create metal, ceramic, and composite parts. BJ works by layering powdered materials and using a binder to fuse them together. BJ printers use a print head to apply the binder to the powder, creating a solid object. BJ is a relatively low-cost 3D printing technology, making it an accessible option for small businesses or hobbyists.
Directed Energy Deposition (DED)
Directed energy deposition (DED) is a 3D printing technology used for creating solid objects by injecting a stream of molten material into a predefined location. DED is suitable for creating large, complex objects such as turbine blades, rocket engine components, and other aerospace applications. DED can be done using different feedstock materials and deposition methods such as powder or wire. The final product resulting from DED has excellent mechanical properties, making it suitable for high-performance applications.
Conclusion
Metal 3D printing technology has opened up new possibilities for manufacturing industries, allowing for the creation of complex designs and geometries that would have been impossible or too expensive to create using traditional manufacturing methods. Powder bed fusion is the most common technique used for metal printing, but there are several other 3D printing technologies used for creating metal, ceramic, and composite parts. Fused deposition modeling, stereolithography, selective laser sintering, electron beam melting, binder jetting, and directed energy deposition are some of the most popular 3D printing technologies used today. As 3D printing technology continues to evolve and improve, it will undoubtedly lead to new innovations and applications in various industries.