Stainless steel sheet metal is a highly versatile material that is widely used in various industries, including construction, manufacturing, and engineering. Its unique properties make it ideal for applications that require high corrosion resistance, strength, and durability. In this article, we will discuss the properties, uses, and fabrication techniques of stainless steel sheet metal.
- Properties of Stainless Steel Sheet Metal
- Uses of Stainless Steel Sheet Metal
- Fabrication Techniques for Stainless Steel Sheet Metal
- Advantages and Disadvantages of Stainless Steel Sheet Metal
- Conclusion
Properties of Stainless Steel Sheet Metal
Stainless steel is a type of steel that contains at least 10.5% chromium, which provides excellent corrosion resistance. Stainless steel sheet metal is a thin, flat piece of stainless steel that is available in various thicknesses, sizes, and grades. The following are some of the properties of stainless steel sheet metal:
• Corrosion Resistance: Stainless steel is highly resistant to corrosion, making it ideal for applications that require long-term durability in harsh environments.
• Strength and Durability: Stainless steel is a strong and durable material that can withstand high stress and pressure.
• Heat Resistance: Stainless steel is highly resistant to heat and can withstand high temperatures without deformation.
• Easy to Clean: Stainless steel is easy to clean and maintain, making it ideal for applications that require high levels of hygiene.
Uses of Stainless Steel Sheet Metal
Stainless steel sheet metal is used in various applications, including:
• Kitchen and Restaurant Equipment: Stainless steel sheet metal is commonly used in kitchen and restaurant equipment, including countertops, sinks, and appliances, due to its durability and ease of cleaning.
• Medical Equipment: Stainless steel sheet metal is used in various medical applications, including surgical instruments, implants, and medical devices, due to its biocompatibility and corrosion resistance.
• Aerospace Industry: Stainless steel sheet metal is used in various aerospace applications, including aircraft components, due to its strength, durability, and resistance to high temperatures and corrosion.
• Automotive Industry: Stainless steel sheet metal is used in various automotive applications, including exhaust systems, due to its resistance to corrosion and high temperatures.
• Construction Industry: Stainless steel sheet metal is used in various construction applications, including roofing, façades, and structural components, due to its durability and corrosion resistance.
Fabrication Techniques for Stainless Steel Sheet Metal
Stainless steel sheet metal can be fabricated using various techniques, including:
• Cutting: Stainless steel sheet metal can be cut using various methods, including shearing, laser cutting, and plasma cutting.
• Bending: Stainless steel sheet metal can be bent into different configurations using various techniques, including press braking, roll bending, and stretch bending.
• Forming: Stainless steel sheet metal can be formed into different shapes and configurations using various techniques, including hydroforming, spinning, and stamping.
• Joining: Stainless steel sheet metal can be joined using various methods, including welding, soldering, and brazing.
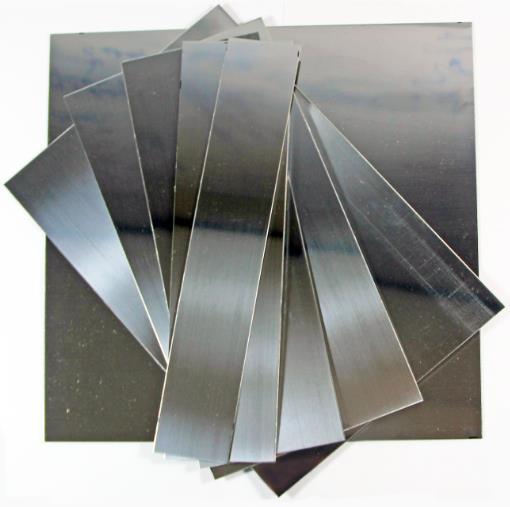
Advantages and Disadvantages of Stainless Steel Sheet Metal
Stainless steel sheet metal offers several advantages and disadvantages, including:
Advantages:
• Corrosion resistance
• Strength and durability
• Heat resistance
• Easy to clean and maintain
• Recyclable
Disadvantages:
• More expensive than other materials
• Requires special tools and techniques for fabrication
• Can be prone to discoloration and staining over time
Conclusion
Stainless steel sheet metal is a highly versatile material that is widely used in various industries due to its unique properties, including corrosion resistance, strength, and durability. It can be fabricated using various techniques, including cutting, bending, forming, and joining . Stainless steel sheet metal is commonly used in applications such as kitchen and restaurant equipment, medical equipment, aerospace components, automotive exhaust systems, and construction components. While stainless steel sheet metal offers several advantages, such as being highly resistant to corrosion and easy to clean, it does have some disadvantages, such as being more expensive than other materials and requiring special tools and techniques for fabrication.