Table of Contents:
- Introduction to Injection Molding
- The Injection Molding Process
- Types of Injection Molding
- Materials Used in Injection Molding
- Key Parameters in Injection Molding
- Advantages and Disadvantages of Injection Molding
- Applications of Injection Molding
- Future of Injection Molding
- Conclusion
1.Introduction to Injection Molding
Injection molding is a widely used manufacturing process for producing parts in large quantities. It involves injecting molten material into a mold cavity, which then solidifies to form a part. The process is highly versatile and can be used to produce parts with complex shapes and geometries, making it a popular choice for a range of industries. Injection molding is used to produce a wide range of products, from automotive parts and medical devices to consumer goods and packaging. In this guide, we will provide an overview of the injection molding process, the materials used, and the key parameters involved in the process. We will also explore the advantages and disadvantages of injection molding, as well as its applications and future prospects.
-
2.The Injection Molding Process
The injection molding process involves four main components: the injection molding machine, the mold, the material, and the injection molding cycle. Here’s an overview of each component:
A. The Injection Molding Machine:
The injection molding machine is a piece of equipment that melts and injects material into the mold. The machine consists of a hopper, which feeds the raw material into a heated barrel. The material is then heated and mixed until it becomes a molten state. Once the material is melted, it is injected into the mold under high pressure.
B. The Mold:
The mold is a tool that is used to create the shape of the part that is being produced. The mold is made up of two halves, the cavity and the core, which are designed to fit together perfectly. Once the molten material is injected into the mold, it fills the cavity and takes on the shape of the part being produced. The mold is typically made from steel or aluminum and is precision machined to ensure the highest level of accuracy.
C. The Material:
The material used in injection molding can be a variety of materials, including thermoplastics, thermosets, and elastomers. The material is chosen based on the requirements of the part being produced, such as its strength, durability, and flexibility. The material is typically supplied in pellet form and is fed into the hopper of the injection molding machine.
D. The Injection Molding Cycle:
The injection molding cycle consists of several stages, including clamping, injection, cooling, and ejection. In the clamping stage, the mold is closed and held together tightly while the material is injected into the mold. In the injection stage, the molten material is injected into the mold at high pressure. The cooling stage involves allowing the material to cool and solidify in the mold, which can take anywhere from a few seconds to a few minutes. Finally, in the ejection stage, the finished part is ejected from the mold, and the process starts over again.
Overall, the injection molding process is a highly efficient and cost-effective method for producing large quantities of parts with high precision and quality.
-
3.Types of Injection Molding
There are several different types of injection molding processes, each with its own advantages and disadvantages. Here are the most common types of injection molding:
A. Thermoplastic Injection Molding:
Thermoplastic injection molding is the most common type of injection molding process. It involves melting and injecting a thermoplastic material into a mold to produce a part. The thermoplastic material can be heated and cooled multiple times, making it a highly versatile and widely used material in injection molding.
B. Thermoset Injection Molding:
Thermoset injection molding involves injecting a thermosetting material into a mold to produce a part. Thermosetting materials differ from thermoplastics in that they undergo a chemical reaction during the molding process, which causes them to cross-link and harden permanently. This makes thermosetting materials ideal for applications where high strength and durability are required.
C. Liquid Injection Molding:
Liquid injection molding is a specialized form of injection molding that is used to produce parts from liquid silicone rubber (LSR). LSR is a highly flexible and durable material that is used in a range of industries, including medical, automotive, and consumer goods. The liquid injection molding process involves injecting the LSR material into a mold under high pressure, which then cures and solidifies into a part.
-
4.Materials Used in Injection Molding
Injection molding is a versatile manufacturing process that can be used to produce a wide range of parts from different materials. Here are the most common materials used in injection molding:
A. Thermoplastics:
Thermoplastics are the most commonly used materials in injection molding. They are a type of plastic that can be melted and solidified repeatedly, which makes them ideal for injection molding. Thermoplastics can be used to produce a wide range of parts, including automotive components, electronic housings, and consumer products.
B. Thermosets:
Thermosets are another type of plastic used in injection molding. They differ from thermoplastics in that they undergo a chemical reaction during the molding process, which causes them to harden permanently. This makes them ideal for applications that require high strength and durability, such as aerospace components and electrical insulators.
C. Elastomers:
Elastomers are a type of polymer that can stretch and return to their original shape. They are commonly used in injection molding to produce parts that require high flexibility, such as seals, gaskets, and medical devices. Elastomers can be either thermoplastic or thermoset.
-
5.Key Parameters in Injection Molding
The quality and consistency of the injection molding process are dependent on several key parameters that must be carefully controlled to ensure the production of high-quality parts. Here are some of the most important parameters in injection molding:
A. Temperature:
Temperature is a critical parameter in injection molding because it affects the material properties and the flow characteristics of the molten plastic. The temperature of the material, mold, and injection molding machine must be carefully controlled to ensure that the material melts uniformly, flows smoothly, and solidifies correctly.
B. Pressure:
Pressure is another critical parameter in injection molding. It affects the filling of the mold and the packing of the material. The injection pressure must be high enough to ensure that the mold cavity is completely filled with the material, but not so high that it causes damage to the mold or the machine.
C. Injection Speed:
Injection speed is the rate at which the material is injected into the mold. It affects the filling of the mold and the cooling time of the part. The injection speed must be carefully controlled to ensure that the material flows smoothly and that the mold is completely filled without causing any defects in the part.
D. Cooling Time:
Cooling time is the amount of time required for the material to cool and solidify inside the mold. It affects the dimensional accuracy and surface finish of the part. The cooling time must be long enough to ensure that the part is fully solidified but not so long that it causes production delays or increased cycle times.
-
6.Advantages and Disadvantages of Injection Molding
Injection molding is a widely used manufacturing process that offers several advantages and disadvantages. Here are some of the key advantages and disadvantages of injection molding:
A. Advantages:
- High Efficiency: Injection molding is a highly efficient manufacturing process that can produce large quantities of parts quickly and consistently.
- Design Flexibility: Injection molding can produce complex parts with intricate shapes and details that are difficult or impossible to achieve with other manufacturing processes.
- Material Versatility: Injection molding can be used to produce parts from a wide range of materials, including thermoplastics, thermosets, and elastomers.
- Minimal Waste: Injection molding produces very little waste material, making it a cost-effective and environmentally friendly manufacturing process.
- Consistent Quality: Injection molding produces parts with consistent quality and dimensional accuracy, making it ideal for applications where precision is critical.
B. Disadvantages:
- High Startup Costs: Injection molding requires significant upfront investment in equipment and tooling, making it less suitable for low-volume production runs or custom projects.
- Long Lead Times: The design and production of molds for injection molding can take several weeks or even months, which can cause delays in the production process.
- Part Design Limitations: Injection molding imposes certain design limitations due to the need to remove the part from the mold, which can limit the complexity of the part’s shape and features.
- Part Size Limitations: Injection molding is best suited for producing small to medium-sized parts, making it less suitable for large-scale manufacturing.
- Material Selection Limitations: While injection molding can produce parts from a wide range of materials, the selection of materials is limited compared to other manufacturing processes like CNC machining or 3D printing.
-
7.Applications of Injection Molding
Injection molding is a widely used manufacturing process that finds applications in various industries. Here are some of the key industries that use injection molding and their applications:
A. Automotive Industry:
Injection molding is extensively used in the automotive industry for producing various parts such as interior and exterior trims, dashboards, bumpers, and engine components. Injection molding is preferred in the automotive industry because of its high production rate, consistency, and cost-effectiveness.
B. Medical Industry:
Injection molding is widely used in the medical industry for producing parts such as syringes, IV tubes, surgical instruments, and medical devices. Injection molding is preferred in the medical industry because of its ability to produce high-quality, precision parts that meet strict regulatory requirements.
C. Consumer Goods Industry:
Injection molding is used extensively in the consumer goods industry for producing a wide range of products such as toys, electronics, packaging, and household items. Injection molding is preferred in the consumer goods industry because of its ability to produce parts with complex shapes, high consistency, and low cost.
Other industries that use injection molding include the aerospace industry for producing lightweight components and the construction industry for producing pipes, fittings, and other components.
-
8.Future of Injection Molding
The future of injection molding looks bright, with advancements in technology and materials driving innovation and growth in the industry. Here are some of the key trends and developments that are shaping the future of injection molding:
- Automation and Industry 4.0:
The integration of automation and Industry 4.0 technologies such as Artificial Intelligence (AI), Internet of Things (IoT), and Big Data analytics are transforming the injection molding industry. Automation and Industry 4.0 technologies are enabling manufacturers to improve production efficiency, reduce costs, and enhance product quality. - Sustainable Materials:
As environmental concerns continue to mount, the use of sustainable materials in injection molding is becoming increasingly important. Manufacturers are exploring alternative materials such as bioplastics, which are biodegradable and compostable, to reduce the environmental impact of injection molding. - Advanced Materials:
The development of advanced materials such as high-performance polymers, nanocomposites, and metal-filled plastics is expanding the range of applications for injection molding. These materials offer enhanced properties such as improved strength, stiffness, and thermal resistance, making them ideal for demanding applications in industries such as aerospace and defense. - Additive Manufacturing:
The integration of additive manufacturing technologies such as 3D printing with injection molding is enabling manufacturers to produce parts with complex geometries and features that were previously difficult or impossible to produce. This hybrid approach is unlocking new possibilities for product design and customization.
Click on the V1 Prototype website to gain more Injection Molding information.
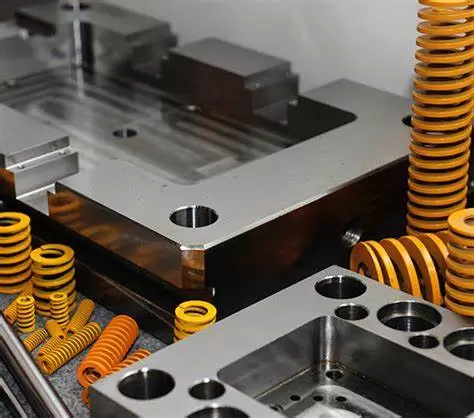
-
9.Conclusion
Injection molding is a widely used manufacturing process that has been around for many years, yet it continues to evolve and innovate. The process involves injecting molten material into a mold to produce a wide range of parts and components used in various industries, including automotive, medical, and consumer goods.
Key parameters such as temperature, pressure, injection speed, and cooling time play a critical role in the injection molding process. Manufacturers must carefully control these parameters to produce high-quality parts that meet their customers’ requirements.
The future of injection molding looks bright, with advancements in technology and materials driving innovation and growth in the industry. Automation, Industry 4.0, sustainable and advanced materials, and additive manufacturing are some of the key trends and developments that are shaping the future of injection molding.
In conclusion, injection molding is a versatile and cost-effective manufacturing process that plays a critical role in many industries. As the industry continues to evolve, manufacturers who embrace new technologies and materials will be well-positioned to meet the changing needs of their customers and drive innovation in the field.
Injection molding is a manufacturing process that involves injecting molten material into a mold cavity to produce a desired shape. The material can be plastic, metal, ceramic, or rubber, depending on the application and the product requirements. Injection molding is widely used for mass production of complex parts, such as toys, medical devices, automotive components, and consumer electronics.
The injection molding process consists of four main stages: clamping, injection, cooling, and ejection. In the clamping stage, the mold halves are closed and secured by a hydraulic or mechanical force. The mold cavity defines the shape and size of the product. In the injection stage, the molten material is fed into the mold cavity through a nozzle attached to a heated barrel. The material is pressurized and filled into the mold cavity at a high speed. In the cooling stage, the material solidifies and takes the shape of the mold cavity. The cooling time depends on the material properties, the mold design, and the product thickness. In the ejection stage, the mold halves are opened and the product is ejected from the mold cavity by a mechanism such as a pin or a plate.
The injection molding process requires careful selection and preparation of the material and the mold. The material should have suitable flowability, thermal stability, and mechanical strength for the intended application. The material should also be compatible with the mold material and the injection molding machine. The mold should have a smooth surface finish, adequate venting, and proper cooling channels to ensure quality and efficiency of the process. The mold should also be designed to minimize defects such as warping, shrinkage, flash, and sink marks.
Injection molding is a versatile and cost-effective process that can produce high-quality products with complex shapes and features. However, it also has some limitations and challenges, such as high initial investment, long lead time for mold development, limited design flexibility, and environmental impact of waste material. Therefore, injection molding should be carefully planned and optimized to achieve the best results.