Table of Contents:
- Introduction
- Types of Plastic Finishes
- Applications of Plastic Finishes
- Techniques for Applying Plastic Finishes
- Factors to Consider When Choosing a Plastic Finish
- Advantages and Disadvantages of Plastic Finishes
- Maintenance and Care of Plastic Finishes
- Conclusion
-
1.Introduction
Plastic is one of the most versatile and widely used materials in modern manufacturing, with applications in almost every industry. However, while plastic is durable and easy to mold into various shapes, it often lacks the aesthetic appeal and protection needed for many applications. That’s where plastic finishes come in. In this article, we will explore the definition of plastic finishes, their importance, and their applications in different industries.
Definition of Plastic Finishes:Plastic finishes refer to a range of coatings and treatments that are applied to plastic surfaces to enhance their appearance, durability, and functionality. These finishes can be applied to a wide variety of plastic materials, including polyethylene, polypropylene, polycarbonate, and PVC. They are designed to provide a protective layer that can resist environmental damage, such as UV radiation, moisture, and abrasion, while also improving the aesthetic appeal of the plastic object.
Importance of Plastic Finishes:Plastic finishes are essential in many industries, as they can significantly enhance the functionality and appearance of plastic products. For example, in the automotive industry, plastic finishes are used to create a high-end, glossy appearance for car parts such as dashboards and exterior trims. In the consumer goods industry, plastic finishes can improve the durability and hygiene of products such as toys, kitchen appliances, and furniture. In the medical industry, plastic finishes are used to create hygienic, easy-to-clean surfaces for medical equipment and devices. In the construction industry, plastic finishes are used to create weather-resistant, long-lasting surfaces for building materials such as siding, roofing, and windows.
-
2.Types of Plastic Finishes
There are many types of plastic finishes available in the market today, each with its own unique properties and applications. Some of the most popular types of plastic finishes are:
- Gloss Finishes:Gloss finishes are a popular choice for plastic objects that require a shiny, reflective surface. These finishes are highly durable and can provide excellent resistance to scratches and abrasions. They are often used in the automotive industry for car parts such as grilles, trim, and interior components.
- Matte Finishes:Matte finishes are the opposite of gloss finishes, offering a non-reflective, low-sheen appearance. These finishes are ideal for creating a more subtle, understated look and are often used in consumer goods such as electronics, appliances, and household items.
- Satin Finishes:Satin finishes offer a compromise between gloss and matte finishes, providing a slightly glossy, smooth appearance that is not too reflective. These finishes are often used in furniture, fixtures, and other decorative items.
- Textured Finishes:Textured finishes are designed to provide a tactile, non-slip surface that is easy to grip and manipulate. These finishes can be applied to a wide range of plastic objects, including tool handles, sporting equipment, and medical devices.
- Metallic Finishes:Metallic finishes are a popular choice for creating a high-end, luxurious appearance for plastic objects. These finishes can provide a metallic sheen and are often used in automotive parts, electronic devices, and consumer goods such as jewelry boxes and decorative items.
-
3.Applications of Plastic Finishes
Plastic finishes are widely used in various industries, providing a range of benefits such as improved appearance, durability, and functionality. Here are some of the most common applications of plastic finishes:
- Automotive Industry:The automotive industry is one of the largest users of plastic finishes. Gloss finishes are often used for car parts such as grilles, trim, and interior components, while metallic finishes are popular for creating a high-end, luxurious appearance. Textured finishes are used for non-slip surfaces such as steering wheels and gearshifts, while matte finishes can be used for dashboards and other interior components.
- Electronics Industry:The electronics industry relies heavily on plastic finishes to provide protection against environmental damage, such as moisture, UV radiation, and scratches. Gloss finishes are often used for electronic device housings, while matte finishes are used for screens and displays to reduce glare.
- Consumer Goods Industry:Plastic finishes are widely used in the consumer goods industry to improve the appearance, durability, and hygiene of products such as toys, kitchen appliances, and furniture. Gloss finishes can provide a high-end, luxurious appearance for these products, while matte finishes can create a more understated look. Textured finishes are used for non-slip surfaces on products such as cutlery and cookware.
- Medical Industry:The medical industry requires hygienic, easy-to-clean surfaces for medical equipment and devices. Plastic finishes with antimicrobial properties are often used in this industry to reduce the risk of infection. Textured finishes can also provide a non-slip surface for medical devices and equipment.
- Packaging Industry:The packaging industry uses plastic finishes to protect products during transport and storage. Gloss finishes can provide a high-end, professional appearance for packaging, while matte finishes can create a more natural, understated look. Textured finishes can be used for grip and ease of handling.
- Construction Industry:The construction industry relies on plastic finishes to provide weather-resistant, long-lasting surfaces for building materials such as siding, roofing, and windows. Gloss finishes can provide a shiny, reflective appearance for these materials, while matte finishes can create a more subtle, natural look.
-
4.Techniques for Applying Plastic Finishes
There are several techniques used for applying plastic finishes to objects. The choice of technique depends on the type of plastic finish, the size and shape of the object, and the desired outcome. Here are some of the most common techniques used for applying plastic finishes:
- Spray Painting:Spray painting is a popular technique for applying plastic finishes, especially for smaller objects or those with complex shapes. A spray gun is used to apply a fine mist of paint onto the surface of the object, creating a smooth and even finish. Spray painting is ideal for gloss, matte, and metallic finishes.
- Dip Coating:Dip coating is a technique where an object is dipped into a liquid coating material, such as paint or varnish, and then allowed to dry. This method is often used for coating small or intricate objects, such as screws or nuts. Dip coating is ideal for creating even, consistent finishes on small objects.
- Electrostatic Coating:Electrostatic coating involves the use of a charged spray gun that applies a charged mist of paint onto a grounded object. The charged paint particles are attracted to the grounded object, creating an even and uniform coating. Electrostatic coating is ideal for gloss, matte, and metallic finishes.
- Powder Coating:Powder coating is a process where a dry powder is applied to an object and then heated to melt and form a hard, durable finish. Powder coating is often used for outdoor furniture, car parts, and appliances, as it provides excellent resistance to weathering and corrosion.
- Roll Coating:Roll coating is a technique where an object is passed through a series of rollers that apply a coating material to the surface. This method is often used for large, flat objects, such as sheets of plastic or metal. Roll coating is ideal for creating even, consistent finishes on large surfaces.
-
5.Factors to Consider When Choosing a Plastic Finish
When choosing a plastic finish, there are several factors that should be taken into consideration to ensure that the chosen finish meets the desired aesthetic and performance requirements. Here are some of the most important factors to consider when choosing a plastic finish:
- Surface Type and Condition:The surface type and condition of the object being finished are important factors to consider. The type of plastic finish used will depend on whether the surface is smooth, textured, or porous. The condition of the surface will also affect the choice of finish, as damaged or uneven surfaces may require additional preparation before the finish can be applied.
- Environmental Conditions:The environment in which the object will be used is an important factor to consider when choosing a plastic finish. If the object will be exposed to harsh weather conditions or chemicals, a durable finish such as powder coating may be necessary. On the other hand, if the object will be used in a clean room environment, a finish that is resistant to dirt and dust may be more appropriate.
- Desired Aesthetic:The desired aesthetic is another important factor to consider when choosing a plastic finish. Glossy finishes are ideal for creating a shiny, reflective surface, while matte finishes are ideal for creating a subdued, non-reflective surface. Textured finishes can be used to add depth and interest to a surface, while metallic finishes can be used to create a metallic sheen.
- Performance Requirements:The performance requirements of the object being finished should also be taken into consideration. If the object will be subjected to high levels of wear and tear, a durable finish such as powder coating may be necessary. If the object will be used in a high-temperature environment, a finish that is heat-resistant may be more appropriate.
-
6.Advantages and Disadvantages of Plastic Finishes
Plastic finishes offer many advantages over other types of finishes, but they also have some disadvantages. Here are some of the most common advantages and disadvantages of plastic finishes:
Advantages:
- Versatility:Plastic finishes can be used on a wide range of surfaces, including metal, wood, and plastic. They can be applied in a variety of textures, colors, and finishes, making them a versatile choice for many applications.
- Durability:Plastic finishes are often more durable than other types of finishes, such as paint or varnish. They can withstand exposure to harsh weather conditions, chemicals, and abrasion, making them ideal for use in industrial and outdoor applications.
- Resistance to Corrosion:Many plastic finishes offer excellent resistance to corrosion, making them ideal for use in applications where the object will be exposed to water or other corrosive substances.
- Ease of Application:Plastic finishes are often easy to apply and require minimal preparation. Many finishes can be applied using simple techniques such as spray painting or dip coating, making them a cost-effective option for many applications.
Disadvantages:
- Limited Adhesion:Plastic finishes may not adhere well to certain surfaces, particularly those that are very smooth or non-porous. This can lead to poor adhesion and a less durable finish.
- Limited Heat Resistance:Many plastic finishes are not suitable for use in high-temperature environments. They may melt or deform when exposed to heat, reducing their durability and effectiveness.
- Environmental Concerns:Some plastic finishes contain harmful chemicals, such as volatile organic compounds (VOCs), which can be released into the environment during application or use. This can contribute to air pollution and may be harmful to human health.
- Cost:Plastic finishes can be more expensive than other types of finishes, particularly if specialized equipment is required for application. This can make them less cost-effective for some applications.
-
7.Maintenance and Care of Plastic Finishes
Plastic finishes, like any other type of finish, require proper maintenance and care to maintain their appearance and functionality. Here are some tips for maintaining and caring for plastic finishes:
Cleaning Techniques:
- Use a soft cloth:When cleaning plastic finishes, use a soft, lint-free cloth to avoid scratching the surface. Avoid using abrasive cleaners or steel wool, which can damage the finish.
- Use mild soap:Use a mild soap solution and warm water to clean the finish. Avoid using harsh chemicals or solvents, which can damage the finish.
- Rinse thoroughly:After cleaning the finish, rinse it thoroughly with clean water to remove any soap residue.
Protective Measures:
- Avoid Exposure to UV light:Plastic finishes can fade or become brittle when exposed to UV light. To protect the finish, avoid exposing it to direct sunlight or UV light sources.
- Use Protective Coatings:To protect the finish from scratches and abrasion, apply a protective coating, such as a clear coat or wax.
- Avoid High Temperatures:Plastic finishes can melt or deform when exposed to high temperatures. Avoid placing hot objects on the finish or exposing it to high-temperature environments.
- Store Properly:When storing objects with plastic finishes, store them in a cool, dry place to prevent damage from moisture or humidity.
By following these maintenance and care tips, manufacturers can help ensure that plastic finishes remain functional and aesthetically pleasing for their intended lifespan.
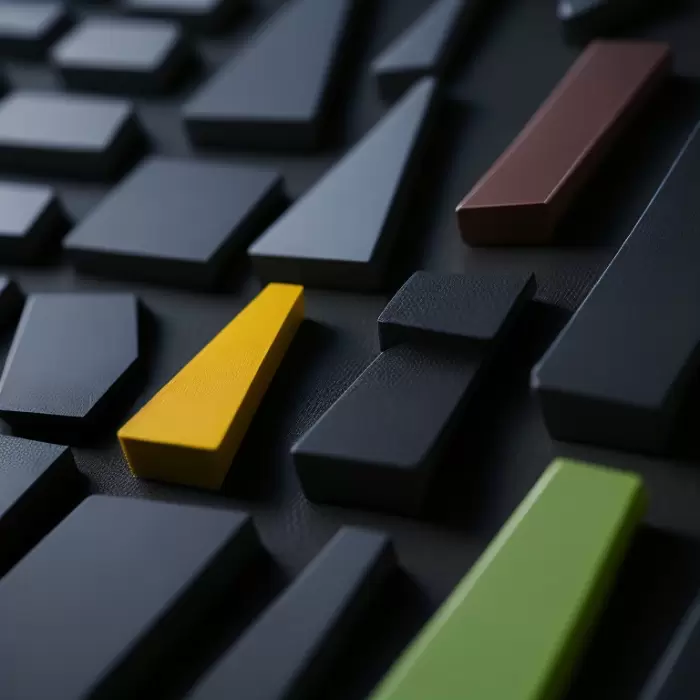
-
8.Conclusion
Plastic finishes are an important and versatile type of finish used in a wide range of industries and applications. They offer many advantages, including versatility, durability, resistance to corrosion, and ease of application. However, they also have some disadvantages, such as limited adhesion, limited heat resistance, environmental concerns, and cost.
To maintain plastic finishes, proper maintenance and care are required. This includes using gentle cleaning techniques and protective measures such as avoiding exposure to UV light, using protective coatings, avoiding high temperatures, and storing properly.
Summary of Key Points:
- Plastic finishes are a versatile type of finish used in many industries and applications.
- They offer many advantages, including versatility, durability, and resistance to corrosion.
- Proper maintenance and care are required to maintain plastic finishes, including using gentle cleaning techniques and protective measures.
- Some disadvantages of plastic finishes include limited adhesion, limited heat resistance, environmental concerns, and cost.
Future Trends in Plastic Finishes:
As technology advances, there are several trends emerging in the world of plastic finishes. These include the use of sustainable and eco-friendly materials, the development of new textures and finishes, and the integration of functional properties such as UV protection and antimicrobial properties.
In addition, there is an increasing demand for custom finishes that allow manufacturers to create unique and personalized products. This trend is being driven by advancements in digital printing and other technologies that allow for greater customization and flexibility.
Overall, the future of plastic finishes looks bright, with continued innovation and advancements that will enable manufacturers to create even more durable, functional, and aesthetically pleasing finishes.