Table of Contents:
- Introduction to Vacuum Casting
- Process of Vacuum Casting
- Applications of Vacuum Casting
- Quality Control and Inspection in Vacuum Casting
- Advancements and Future Trends in Vacuum
- Casting Comparison between Vacuum Casting and Other Prototyping Methods
- Conclusion
-
1.Introduction to Vacuum Casting
Vacuum casting is a manufacturing process that allows the production of small to medium-sized parts in large quantities with high accuracy and detail. It is a cost-effective method used for rapid prototyping and small batch production, in which a silicone mold is filled with liquid polyurethane material, and then the pressure is reduced in a vacuum to eliminate air bubbles and to allow the material to settle uniformly throughout the mold.
Advantages and Limitations of Vacuum Casting:
The benefits of vacuum casting include quick turnaround times, flexibility, and the ability to produce small and medium-sized parts in large quantities. Vacuum casting also produces high-quality finishes with relatively low tooling costs compared to other manufacturing techniques, making it a perfect choice for rapid prototyping and small-scale manufacturing.
However, there are some limitations. One of the major drawbacks is the strength and durability of the final product. Vacuum-cast parts do not achieve the same strength and durability as other mass production methods. Additionally, vacuum casting is restricted to the production of non-ferrous materials, limiting the utility of vacuum casting to less complex designs.
-
2. Process of Vacuum Casting:
Mold Preparation:
The first step in vacuum casting is preparing the master pattern. The pattern is the product that the final mold will be created from. The quality of the master pattern can have a significant impact on the final product quality. Making the pattern requires software to design the piece, followed by 3D printing, CNC milling or other appropriate means of generating the pattern. After confirming that the pattern is correct, it is used to create the silicone mold.
Vacuum Casting Process Steps:
To produce a vacuum-cast product, a specific process is followed:
- The silicone mold is created by pouring silicone onto the master pattern.
- The silicone mold is removed from the master pattern once cured.
- The mold is then placed onto an open casting box and injection gates embedded.
- Liquid polyurethane is then poured into the mold.
- The casting box is sealed in a vacuum chamber.
- The pressure inside the chamber is decreased, and the polyurethane starts to flow over the mold.
- Once the material cures and sets, the mold is removed.
- The final casted part is then cleaned, post-processed, and finished as required.
Types of Materials Used in Vacuum Casting:
Vacuum casting uses a variety of materials to suit different applications, prototypes, and budget constraints. Thermoplastics, resins, and silicones are the most common materials used for vacuum casting. In addition, composites are another material that is slowly gaining popularity in vacuum casting.
-
3. Applications of Vacuum Casting:
Automotive Industry Applications:
Vacuum casting has been widely applied in the automotive industry to produce parts such as gears, housings, air vents, lighting systems, and other components. The process allows auto-makers to create complex and intricate parts while minimizing costs and producing parts in large quantities.
Medical Industry Applications:
Vacuum casting is used in medical applications to create parts such as implants or surgical tools. Vacuum casting offers much higher accuracy and precision than traditional casting methods, making it an ideal method for the medical industry, where precision and reliability are critical.
Consumer Goods Applications:
Vacuum casting is also used in the production of consumer goods. The versatility of materials available for vacuum casting allows manufacturers to produce complex and efficient designs while keeping the production cost-effective. Examples include cosmetic products or decorative items.
-
4. Quality Control and Inspection in Vacuum Casting:
Key Metrics in Vacuum Casting Quality Control:
Quality control and inspection are essential in vacuum casting, and the key metrics that need to be monitored include dimensional accuracy, material hardness, color consistency, and finish quality.
QC Techniques and Approaches:
To check the quality of production using vacuum casting, non-destructive testing, visual inspection, microscopic examination, and mechanical testing methods are used.
Safety and Regulatory Challenges and Considerations:
Vacuum casting presents safety issues, such as exposure to epoxy resins and other chemicals, and workers must follow recommended safety procedures, including wearing protective clothing and following proper safety procedures. OSHA and other local safety regulatory groups impose safety laws to ensure safety compliance.
-
5. Advancements and Future Trends in Vacuum Casting
Advancements in Vacuum Casting Technology:
Advancements in vacuum casting technology include the integration with additive manufacturing and 3D printing technology, which speeds up the process and increases accuracy, enabling the production of larger and more intricate parts. Additionally, advances are being made in silicone-free materials, which are becoming more popular and lead to fewer defects in the final product.
The Impact of Sustainability on Vacuum Casting:
Sustainability has become a central driver of innovation in vacuum casting. Manufacturers are investing in more environmentally friendly materials, focusing on reducing waste in the manufacturing process and increasing recycling rates. Eco-friendly resins made from renewable sources provide a way for manufacturers to reduce their carbon footprint while maintaining high-quality products. Sustainability measures help reduce the costs of disposal, processing and contribute to a cleaner environment.
The Prospect of Industry 4.0 in Vacuum Casting:
The integration of Industry 4.0 in vacuum casting has the potential to revolutionize the manufacturing process. The industrial internet of things, big data analytics, and artificial intelligence are being used to optimize the vacuum casting process through real-time monitoring, diagnostic tools, predictive maintenance, and data-driven decision-making. Additionally, digital twins are being used to create digital simulations of products, which enables manufacturers to identify defects early and improve the accuracy of molds.
-
6. Comparison between Vacuum Casting and Other Prototyping Methods
Comparison with Injection Molding:
Vacuum casting is often preferred over injection molding for small-batch production because of its cost-effectiveness, speed, and flexibility. While injection molding is highly effective for large-scale production and can produce stronger and more resilient parts, it is also more expensive, requires high setup and tooling costs, is limited to only a few materials, and has a longer lead time.
Comparison with 3D Printing:
While vacuum casting and 3D printing are both additive manufacturing processes, they have different applications. 3D printing is ideal for prototyping because it is highly flexible, cost-effective, and allows the production of complex geometries. However, 3D printed parts have limitations in terms of strength and durability, and the production cost of 3D printing can be higher than that of vacuum casting. Vacuum casting can produce parts with higher accuracy and quality while also maintaining strength.
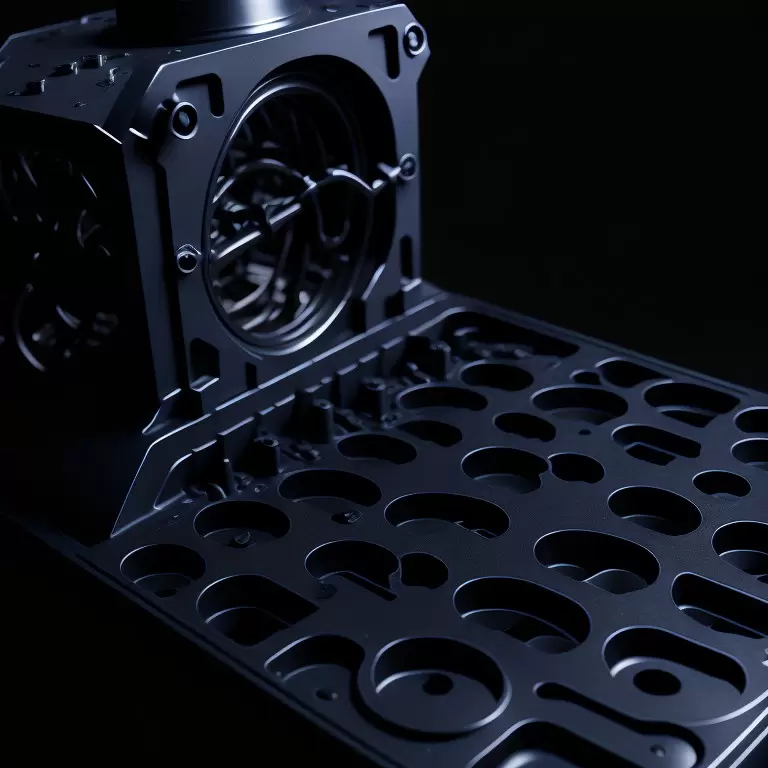
-
7. Conclusion
Vacuum casting is an important method for rapid prototyping and small-scale production across many industries. The process is cost-effective, flexible, and produces high-quality parts with excellent surface finish and dimensional accuracy. Manufacturers can take advantage of new technologies such as Industry 4.0 to optimize the vacuum casting process, reduce waste, and improve production efficiency. Sustainability is another area of growth for vacuum casting as eco-friendly materials become more popular among consumers. Lastly, it is important to consider the limitations and trade-offs when comparing vacuum casting with other prototyping methods to choose the most appropriate one for specific manufacturing needs.