Table of Contents:
- Introduction
- The Injection Moulding Process
- Factors Affecting Injection Moulding
- Types of Plastics Used in Injection Moulding
- Applications of Injection Moulding
- Troubleshooting and Maintenance
- Advancements in Injection Moulding Technology
- Conclusion
-
1.Introduction
Injection moulding is a widely used manufacturing process that involves shaping plastic parts by injecting molten plastic material into a mould. The process is commonly used to make products ranging from toys, electronic devices, automotive parts, and medical equipment, among others.
Understanding how injection moulding works is of great importance because it enables manufacturers to design parts that are efficient, precise, cost-effective, and of high quality. By mastering the principles and the different stages involved in injection moulding, manufacturers can leverage the full potential of this technology, improve their products, and reduce production costs.
Injection moulding relies on several critical factors, such as temperature, pressure, cooling time, and material selection, which if not appropriately managed, can lead to defects, inefficiencies, or even part failure. Thus, an in-depth understanding of this process is critical to achieving optimal production results.
This article will delve into the details of injection moulding, taking a closer look at the process, the injection moulding machine, material selection, and the various parameters that affect the process. By the end of the article, you will understand how injection moulding works, the potential benefits, and how to optimize the process for successful production.
-
2.The Injection Moulding Process
The injection moulding process involves several stages that are critical to achieving high-quality plastic parts. Here are the key steps involved in injection moulding:
- Material Selection - The first step in injection moulding is choosing the appropriate plastic material for the specific application. The material chosen will depend on the part’s requirements, such as strength, durability, flexibility and heat resistance.
- Pre-processing - The plastic material is then fed into a hopper and heated using a series of heater bands to its melting point. The molten material is then transferred to the injection machine.
- Injection - Once the material has melted and is at the optimal temperature, it is injected into the mould through the nozzle of the injection machine. The mould is typically clamped together with two halves, cavity and core side.
- Cooling - After the molten plastic is injected into the mould, it cools and solidifies in the cavity. The cooling time is crucial to ensure that the plastic has enough time to solidify and attain a consistent state.
- Ejection - Once the plastic has fully solidified, the mould is opened, and the final product is ejected from the mould cavity using ejection pins.
- Trimming - The final product is then trimmed to remove any excess material, and any necessary finishing work, such as painting or texturing, is done.
The role of the mould in the injection moulding process is to give the plastic material its desired shape. The mould is made from different materials, such as steel or aluminum, and typically designed to be reused several times. The injection machine’s role is to melt the plastic material and inject it into the mould cavity under high pressure.
The injection machine comprises several components, including the hopper, heater bands, barrel, screw, nozzle, and injection mould. The barrel houses the screw, which rotates, pushing the material towards the nozzle, where the plastic is injected into the mould cavity.
In conclusion, understanding the injection moulding process’s various steps and the different components in the injection machine is critical to achieving high-quality plastic parts. By optimizing the process and adhering to the best practices, manufacturers can ensure production efficiency and product quality consistency.
-
3.Factors Affecting Injection Moulding
Several factors influence the injection moulding process, including:
- Temperature - Temperature is an essential factor that affects the injection moulding process. The plastic material must be heated to its melting point, and the mould must be at the optimal temperature to achieve high-quality plastic parts. The temperature also influences the flow of the molten plastic material as it fills the mould cavity. Each plastic material has its ideal temperature range, and monitoring the temperature levels during the process is crucial to creating consistent parts.
- Pressure - Pressure is another critical factor that affects injection moulding. The injection machine injects the molten plastic material into the mould cavity under high pressure. The pressure ensures that the plastic material flows into the mould and fills the cavity completely. If the pressure is too low, the plastic material may not fill the mould cavity correctly, leading to voids, warping or short shots.
- Cooling time - Cooling time is the period required for the plastic material to solidify and attain a consistent state before the mould is opened. The cooling time depends on the plastic material’s thickness, complexity, and other factors affecting the material’s thermal properties. Short cooling times may result in under-filled parts, while long cooling times may lead to warping, shrinkage, or sink marks.
- Material selection - Material selection is critical to the injection moulding process’s success and plays a significant role in the product’s strength, durability, and other properties. Different materials are available for injection moulding, such as thermoplastics, thermosets, and elastomers. The material properties, such as the melting point, viscosity, and warpage, must be considered to achieve the target part quality.
Other factors that may affect injection moulding include the design of the mould, humidity, and other environmental factors. It is essential to monitor these factors and adjust the process parameters to achieve optimal results.
Understanding the critical factors that affect injection moulding is crucial to producing high-quality parts consistently. By optimizing the temperature, pressure, cooling time and material selection, manufacturers can improve efficiency, reduce waste and produce high-quality products.
-
4.Types of Plastics Used in Injection Moulding
There are several types of plastics used in injection moulding, each with specific properties and benefits. Here are some of the most common types of plastics used in injection moulding:
- Polyethylene (PE) - Polyethylene is a lightweight and flexible plastic that is commonly used in injection moulding. It is known for its excellent chemical resistance, toughness, and low-cost production. PE is used to create a wide range of products, such as milk bottles, automotive parts, and toys.
- Polypropylene (PP) - Polypropylene is a versatile plastic commonly used in injection moulding. It has a low melting point and is known for its flexibility, durability, and resistance to moisture. PP is used to make a wide range of products, including food containers, medical devices, and toys.
- Acrylonitrile Butadiene Styrene (ABS) - ABS is a thermoplastic widely used in injection moulding. It is known for its high impact resistance, toughness, and rigidity. ABS is frequently used to create products such as automotive parts, toys, electronic devices, and household appliances.
- Polycarbonate (PC) - Polycarbonate is a strong and durable plastic commonly used in injection moulding. It is known for its high resistance to impact, temperature, and ultraviolet (UV) rays. PC is used to make products ranging from medical devices to smartphone cases.
- Polyurethane (PU) - Polyurethane is a thermoset plastic used in injection moulding, known for its excellent elasticity, durability, and resistance to abrasion, chemicals, and moisture. PU is commonly used in the automotive industry to create products like car bumpers and seats and in the footwear industry for shoe soles.
- Polystyrene (PS) - Polystyrene is a commonly used plastic in injection moulding, known for its low cost and versatility. It is a rigid, transparent, and lightweight plastic that is used in different products, including packaging materials and consumer goods.
In conclusion, the type of plastic used in injection moulding will depend on several factors. Factors like the final product’s requirements, the material characteristics needed, and the manufacturing process involved. By selecting the right plastic material, manufacturers can achieve the desired product properties while also reducing production costs.
-
5.Applications of Injection Moulding
Injection moulding is one of the most widely used manufacturing processes globally, and the products made through this process are ubiquitous in everyday life. Some of the common products made through injection moulding include:
- Automotive parts - From steering wheels to bumpers, automotive companies rely heavily on injection moulding to create automotive parts due to the process’s speed, precision and cost-effectiveness.
- Medical devices - Injection moulding is commonly used in the production of medical devices like syringes, inhalers and tubing. It allows for the creation of high-quality, sterile and consistent medical products.
- Consumer goods - A variety of consumer goods, like toys, household appliances, and packaging materials, are made through injection moulding due to the process’s high volume capability and cost-effectiveness.
- Electronics - Injection moulding is used to create various electronic components, such as mobile phone cases, computer keyboards, and game controllers.
.
Benefits of using injection moulding for manufacturing include:
- Low cost - Injection moulding is a cost-effective way of mass-producing plastic parts, enabling manufacturers to produce products that are affordable to customers.
- High speed - The injection moulding process is faster compared to other manufacturing processes, increasing the production rate and reducing the time it takes to bring a product to market.
- High precision - Injection moulding ensures high precision and consistency, which reduces the need for post-production processing.
- Customization - Injection moulding allows for the creation of complex geometric designs and the use of different colors and textures, enabling manufacturers to customize products for specific applications.
In conclusion, the versatility of injection moulding makes it possible to manufacture products for different sectors, ranging from the automotive industry to the medical industry. The high speed, precision, and cost-effectiveness of the process make it a popular choice for manufacturers globally, propelling innovation in the manufacturing industry.
-
6.Troubleshooting and Maintenance
Despite being a reliable manufacturing process, injection moulding systems can encounter issues that may affect the production process, leading to product quality issues and downtime. Some common issues encountered during injection moulding include:
- Flashing - This occurs when excess material seeps out of the mould cavity, resulting in a thin layer of plastic around the part’s edge.
- Warping - Warping occurs when the part’s surface skin cools and contracts faster than the core, resulting in permanent deformation.
- Cracking - Cracks may appear on the surface or inside the part as a result of excessive pressure, cooling time or warping.
- Burn marks - Burn marks occur when the material overheats or burns due to excessive temperature, high injection speed or long residence time.
.
To troubleshoot and maintain injection moulding systems, here are some strategies:
- Regular maintenance - Regular maintenance of the machine, such as cleaning, lubricating, and replacing worn-out parts, can prevent machine failure and downtime, extend the machine’s lifespan, and maintain production quality.
- Monitor variables - Regular monitoring of the injection moulding process variables, such as temperature, pressure, cooling time and fill time, can help identify and correct issues early on.
- Use high-quality materials - Using high-quality materials and controlling material moisture can prevent issues like warping, cracking and burning.
- Adjust process parameters - Calibrating the machine’s process parameters, such as injection speed, pressure and temperature, can optimize the process and ensure product quality consistency.
- Train operators - Properly training and equipping operators to troubleshoot common issues and maintain the machine reduces the risk of machine failure and ensures that production runs smoothly.
In conclusion, injection moulding troubleshooting and maintenance require careful attention to detail and regular monitoring of the machine’s components and process variables. By following the best practices and employing the strategies mentioned above, manufacturers can minimize machine downtime, ensure consistent product quality and maximize production efficiency.
-
7.Advancements in Injection Moulding Technology
Injection moulding technology has been evolving over the years, leading to the development of innovative technologies that improve the efficiency and capabilities of the manufacturing process. Here is an introduction to some of the innovative injection moulding technologies:
- 3D Printing Injection Moulding - This technology uses 3D printing to produce an injection mould to create plastic parts quickly and cost-effectively. The process allows for design iteration and modifications before creating the final injection mould.
- Two-shot Injection Moulding - This technology is a more advanced injection moulding technique that combines two injection units, allowing for the injection of two different materials or colors in one machine cycle. This technology reduces production cycle times, reduces waste and improves product aesthetics.
- Micro-injection Moulding - This technology allows for the production of micro-scale plastic parts through a highly precise and controlled injection process. It is commonly used in medical, optical and electronic industries.
- In-mould labelling - This innovative technology allows for the integration of the labelling process into the injection moulding process, creating high-quality and durable product labels in a single manufacturing step.
.
These innovative technologies are impacting the manufacturing industry in several ways:
- Increased efficiency - Innovative technologies like two-shot injection moulding and 3D printing injection moulding are speeding up the production process, reducing cycle times, and cutting production costs.
- Greater design flexibility - These advancements allow for more design flexibility and customization possibilities, making it possible to create complex and multi-functional parts with superior quality.
- Improved product quality - In-mould labelling technology improves product aesthetic appeal, durability and reduces the need for secondary labelling processes.
- Reduced waste and environmental impact - Advanced manufacturing technologies like micro-injection moulding technology enable manufacturers to produce smaller and precise plastic parts, reducing the material waste.
In conclusion, innovative injection moulding technologies are revolutionizing the manufacturing industry, creating new possibilities and driving efficiency, speed, and product quality improvement. Manufacturers who embrace these advancements benefit from increased efficiency, cost savings, and improved product quality, positioning themselves as leaders in their industries.
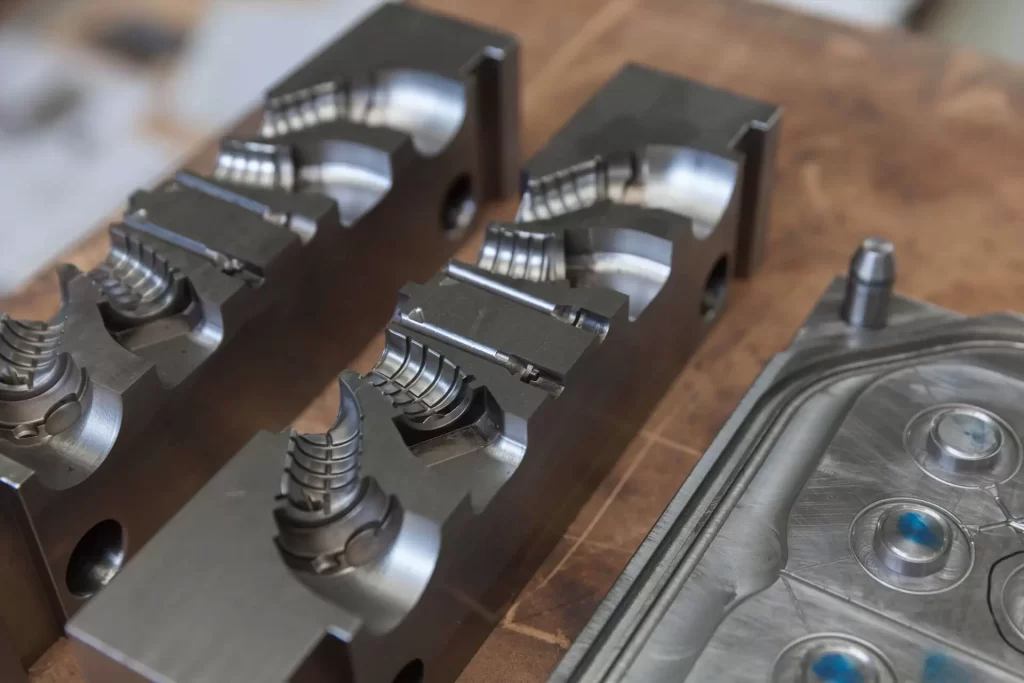
-
8.Conclusion
In conclusion, injection moulding is an essential manufacturing process that has revolutionized the production of plastic parts, resulting in a wide range of applications across several industries. Here’s a recap of the main ideas discussed in this book:
- Injection moulding requires careful consideration of various factors like temperature, pressure, cooling time, and material selection for optimal results.
- Injection moulding is used to make a wide variety of products, from automotive parts to medical devices and consumer goods, due to its cost-effectiveness, high speed, and precision.
- Troubleshooting and maintaining injection moulding systems require regular maintenance and monitoring of process variables to ensure consistent product quality and prevent machine downtime.
- The injection moulding industry is evolving, with innovative technologies like 3D printing injection moulding, micro-injection moulding, in-mould labelling, and two-shot injection moulding creating new possibilities and improving efficiency, design flexibility, and product quality.
Looking to the future, the injection moulding industry is set to continue growing. With the development of new technologies and more advanced materials, the industry will likely see improved production efficiency, reduced environmental impact, and further customization possibilities.
Overall, the injection moulding industry’s future looks promising, as it continues to evolve and innovate, meeting the increasing demand for plastic parts of different shapes, sizes and functionalities across various industries worldwide.