Table of Contents:
- Introduction
- Materials Used in Metal Die Casting Parts
- Processes Involved in Metal Die Casting
- Applications of Metal Die Casting Parts
- Advancements in Metal Die Casting Technology
- Benefits of Metal Die Casting Parts
- Challenges in Metal Die Casting
- Future of Metal Die Casting Parts
- Conclusion
1.Introduction
Metal die casting is a manufacturing process used to create high-volume, precise, and complex metal parts. The process involves injecting molten metal into a reusable mold, or die, under high pressure. This allows for the creation of intricate parts with tight tolerances, smooth surfaces, and excellent dimensional accuracy. Metal die casting parts are widely used in various industries, including automotive, aerospace, electronics, and consumer goods. In this article, we will explore the materials, processes, applications, benefits, challenges, and future of metal die casting parts.
-
2. Materials Used in Metal Die Casting Parts
The metal die casting process is highly versatile and can be used with a wide variety of metals and alloys. The choice of material depends on the specific application and the required properties of the final part. Some of the most common metals used in metal die casting include:
- Aluminum: Aluminum is a lightweight metal that is highly corrosion-resistant and has excellent thermal and electrical conductivity. It is widely used in automotive and aerospace applications, as well as in consumer electronics and household appliances.
- Zinc: Zinc is a low-cost metal that is easy to cast and has excellent dimensional stability. It is often used in the production of small parts such as gears, hinges, and fasteners.
- Magnesium: Magnesium is a lightweight metal that has excellent strength-to-weight ratio and is highly recyclable. It is often used in the production of automotive and aerospace components, as well as in consumer electronics and medical devices.
- Copper: Copper is a highly conductive metal that has excellent thermal and electrical conductivity. It is often used in electrical and electronic components, as well as in plumbing and HVAC applications.
- Brass: Brass is an alloy of copper and zinc that is highly corrosion-resistant and has excellent machinability. It is often used in the production of decorative and functional parts such as door handles, knobs, and hinges.
The choice of material for metal die casting depends on several factors, including the required mechanical and physical properties of the final part, the production volume, and the cost. Each material has its own set of properties and advantages, making it suitable for specific applications. For example, aluminum is often preferred for automotive and aerospace applications due to its lightweight and corrosion-resistant properties, while brass is often used for decorative and functional parts due to its excellent machinability and corrosion resistance.
-
3. Processes Involved in Metal Die Casting
Metal die casting is a complex process that involves several steps to create high-quality parts. These steps include:
- Mold Design: The first step in the metal die casting process is the design of the mold. The mold is typically made of steel and is designed to create the desired shape of the part. The mold design takes into account factors such as part geometry, material properties, and production volume.
- Mold Preparation: Once the mold design is complete, the mold is prepared for production. This involves applying a release agent to the mold to prevent the part from sticking, and heating the mold to a specific temperature to ensure proper metal flow and solidification.
- Metal Melting: The next step in the process is the melting of the metal. The metal is heated to a specific temperature until it reaches a liquid state.
- Injection: Once the metal is melted, it is injected into the mold at high pressure. The pressure is necessary to fill the mold completely and ensure that the part has a consistent shape and density. The injection stage also helps to remove any air pockets or voids in the part.
- Cooling: After the metal has been injected into the mold, it begins to cool and solidify. The cooling time depends on the material being used, the size and shape of the part, and the complexity of the mold. Cooling is a critical stage in the process as it ensures that the part retains its shape and strength.
- Ejection: Once the metal has cooled and solidified, the mold is opened, and the part is ejected from the mold. Any excess material is trimmed away, and the part is inspected for defects or imperfections.
- Finishing: The final step in the metal die casting process is finishing. This involves removing any surface imperfections such as flash or burrs, and applying any required surface treatments such as painting, plating, or polishing.
In summary, the metal die casting process involves several critical steps that must be carefully controlled to produce high-quality parts. The process requires expertise and experience to ensure that the final product meets all design and performance requirements.
-
4. Applications of Metal Die Casting Parts
The versatility and cost-effectiveness of metal die casting make it a popular choice for a wide range of industries. Some of the most common industries that use metal die casting parts include:
- Automotive: Metal die casting is widely used in the automotive industry for the production of engine components, transmission parts, and other critical components. The process provides high dimensional accuracy and the ability to produce complex geometries, making it ideal for automotive applications.
- Aerospace: Metal die casting is also used extensively in the aerospace industry for the production of engine parts, structural components, and other critical parts. The process provides high strength-to-weight ratio and the ability to produce parts with thin walls and intricate features.
- Electronics: Metal die casting is used in the production of a wide range of electronics components, including computer and mobile phone casings, connectors, and heat sinks. The process provides high dimensional accuracy and the ability to produce thin-walled components with complex geometries.
- Medical: Metal die casting is used in the production of medical devices and equipment, including surgical instruments, implants, and diagnostic equipment. The process provides high precision and the ability to produce parts with tight tolerances and complex geometries.
.
Examples of products made using metal die casting include:
- Automotive parts: Examples include engine blocks, transmission cases, and suspension components.
- Aerospace components: Examples include turbine blades, engine housings, and structural components.
- Consumer electronics: Examples include computer and mobile phone casings, camera components, and heat sinks.
- Medical equipment: Examples include surgical instruments, implants, and diagnostic equipment.
In conclusion, metal die casting is a versatile and cost-effective process that is used in a wide range of industries for the production of high-quality parts and components. The choice of material depends on the specific application and the required properties of the final part. The automotive, aerospace, electronics, and medical industries are among the biggest users of metal die casting parts, with examples including engine components, transmission parts, casings, and structural components.
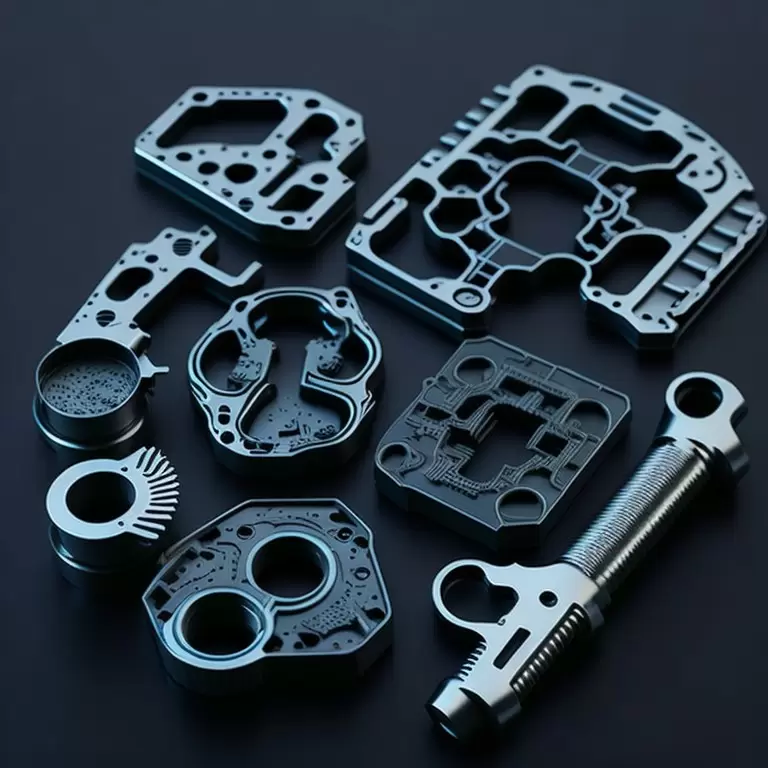
-
5. Advancements in Metal Die Casting Technology
Over the years, metal die casting technology has advanced significantly, resulting in improved efficiency, sustainability, and cost-effectiveness. Some of the new technologies used in metal die casting include:
- Computer-Aided Design (CAD) and Computer-Aided Manufacturing (CAM): These technologies enable designers and engineers to create highly complex 3D models of parts and components, which can then be manufactured using metal die casting. CAD and CAM software also allow for virtual simulations of the casting process, enabling designers to optimize part design for manufacturability and reduce production time and costs.
- High-Pressure Die Casting (HPDC): This is a variant of the traditional die casting process that involves injecting molten metal at very high pressure (up to 30,000 psi) into a die cavity. HPDC results in higher density, better surface finish, and improved mechanical properties in the final part.
- Vacuum-Assisted Die Casting (VADC): This process involves applying a vacuum to the die cavity during the casting process, which helps to remove trapped air and reduce defects in the final part. VADC is particularly useful for producing parts with thin walls and complex geometries.
- Thixomolding: This is a relatively new technology that involves using semi-solid metal (in a “mushy” state) rather than liquid metal for the casting process. Thixomolding results in parts with improved mechanical properties, better surface finish, and reduced porosity.
.
Improved efficiency and sustainability in the metal die casting process has been achieved through:
- Recycling: The metal die casting process generates a significant amount of scrap material, which can be recycled and used in subsequent casting operations. Recycling not only reduces waste but also reduces the environmental impact of the process.
- Energy efficiency: The use of energy-efficient furnaces, casting machines, and other equipment has helped to reduce the energy consumption of the metal die casting process. This has not only reduced production costs but also lowered the environmental impact of the process.
- Waste reduction: New technologies and process improvements have helped to reduce the amount of waste generated during the metal die casting process. This has not only reduced production costs but also lowered the environmental impact of the process.
In conclusion, advancements in metal die casting technology have led to improved efficiency, sustainability, and cost-effectiveness in the process. Computer-Aided Design (CAD) and Computer-Aided Manufacturing (CAM), High-Pressure Die Casting (HPDC), Vacuum-Assisted Die Casting (VADC), and Thixomolding are some of the new technologies used in metal die casting. The use of energy-efficient equipment, recycling, and waste reduction efforts have helped to reduce the environmental impact of the process.
-
6. Benefits of Metal Die Casting Parts
Metal die casting parts offer numerous benefits that make them an attractive option for a wide range of industries. Some of the key benefits include:
- Strength and Durability: Metal die casting parts are known for their strength and durability. The process involves injecting molten metal into a die under high pressure, resulting in parts with excellent mechanical properties. Parts made using metal die casting are able to withstand high loads, resist wear and tear, and have a long service life.
- Cost-Effectiveness: Metal die casting is a cost-effective manufacturing process that allows for the production of high-quality parts at a low cost. The process is highly automated, which reduces labor costs and improves production efficiency. Additionally, the high precision and repeatability of the process reduce the need for secondary operations, further reducing costs.
- Design Flexibility and Precision: Metal die casting allows for the production of complex shapes and geometries with high precision. This makes it possible to create intricate parts that would be difficult or impossible to produce using other manufacturing processes. The process also offers high repeatability, ensuring that each part is produced to the same exacting standards.
- Surface Finish: Metal die casting parts have a smooth surface finish that requires little to no post-processing. This means that the parts are ready for use as soon as they are produced, reducing the need for additional finishing operations.
- Wide Range of Materials: Metal die casting can be used with a wide range of materials, including aluminum, zinc, magnesium, and brass. This allows manufacturers to choose the best material for their specific application, based on factors such as strength, weight, and corrosion resistance.
In conclusion, metal die casting parts offer numerous benefits that make them an attractive option for a wide range of industries. The strength and durability of the parts, cost-effectiveness of the process, design flexibility and precision in manufacturing, and the wide range of materials available all contribute to the popularity of metal die casting.
-
7. Challenges in Metal Die Casting
While metal die casting offers numerous benefits, there are also some challenges associated with the process. Some of the key challenges include:
- Complexity of the Die Casting Process: Metal die casting is a complex process that requires a high degree of skill and expertise. The process involves a number of steps, including the preparation of the die, the melting and injection of the metal, and the extraction and cooling of the finished part. Each step in the process must be carefully controlled to ensure that the final part meets the required specifications.
- Quality Control Challenges in Production: Ensuring consistent quality in metal die casting production can be a challenge. Variations in material composition, die design, and process parameters can all affect the final product. As a result, it is important to have a robust quality control system in place to monitor the process and identify any issues that may arise.
- Environmental Concerns and Sustainability: Metal die casting is an energy-intensive process that can have a significant environmental impact. The melting of metals requires large amounts of energy, which contributes to greenhouse gas emissions and other environmental issues. Additionally, the disposal of waste materials from the process can be a challenge. To address these concerns, manufacturers are exploring ways to reduce energy consumption, minimize waste, and improve the sustainability of the process.
In conclusion, metal die casting is a complex process that presents several challenges, including quality control, environmental concerns, and sustainability. However, with the right expertise and quality control systems in place, these challenges can be overcome, allowing manufacturers to produce high-quality, cost-effective parts with a wide range of applications.
-
8. Future of Metal Die Casting Parts
Metal die casting is a mature technology that has been used in various industries for many years. However, there is still a lot of potential for growth and development in this field. Some of the key trends and future directions for metal die casting include:
- Technological Advancements in Die Casting: There are a number of technological advancements that are driving innovation in the die casting industry. These include new materials, such as high-performance alloys and composites, as well as advanced simulation and modeling tools that can help optimize the casting process. Additionally, there are new process technologies, such as high-pressure die casting and squeeze casting, that are being developed to improve efficiency and quality.
- Sustainability and Environmental Considerations: As the environmental impact of manufacturing processes becomes an increasingly important consideration, there is a growing focus on sustainability in the die casting industry. This includes efforts to reduce energy consumption and waste, as well as to explore alternative materials and production methods that have a lower environmental impact.
- Potential New Applications for Metal Die Casting: While metal die casting is already used in a wide range of applications, there is still potential for growth in new areas. For example, there is increasing interest in using die casting for lightweight structural components in automotive and aerospace applications, as well as for medical implants and devices.
In conclusion, the future of metal die casting looks promising, with ongoing technological advancements and a growing focus on sustainability and new applications. As these trends continue to evolve, we can expect to see continued growth and innovation in this important field.
If you need about Metal Die Casting Services,You can click on the V1 Prototype website to find it:Provide Aluminum And Zinc Metal Alloys Die Casting Processing In Many Industries, Product Structure Optimization Design, Mold Optimization Design, Product Surface Technology, Etc.
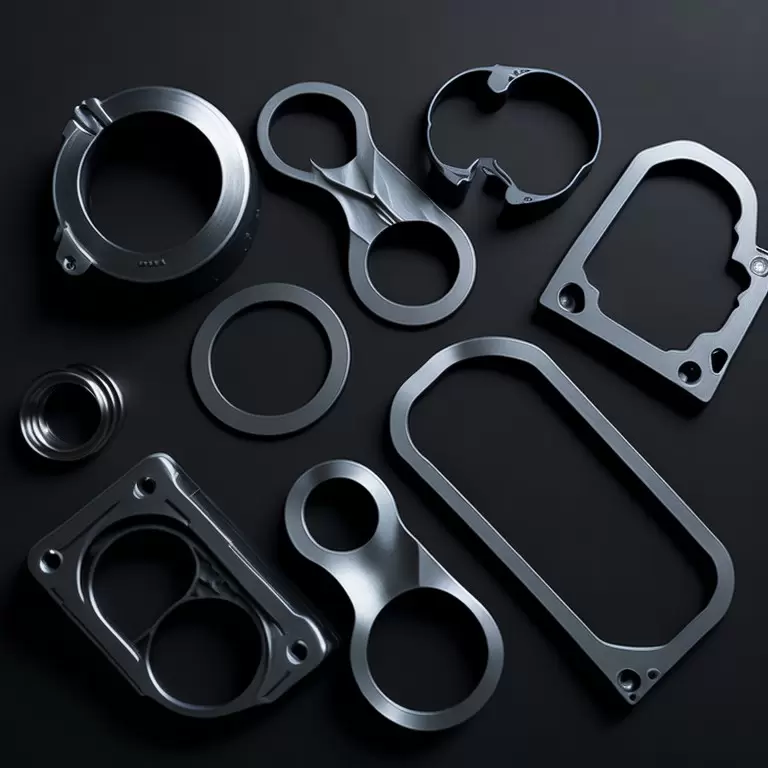
-
9. Conclusion
Metal die casting parts have played a significant role in many industries for decades, offering a range of benefits including strength, durability, cost-effectiveness, design flexibility, and precision manufacturing. The die casting process has evolved over time, with advancements in technology leading to improved efficiency, sustainability, and the ability to use new materials and processes.
Looking ahead, the future of metal die casting looks bright, with ongoing innovations and a growing focus on sustainability and new applications. As the industry continues to evolve, we can expect to see continued growth and innovation in this important field, with the potential for new materials, processes, and applications to emerge.
In conclusion, metal die casting remains an important manufacturing process, offering a wide range of benefits and applications. As technology and sustainability continue to drive innovation in the industry, we can look forward to continued growth and development in the years to come.