Introduction
The world of 3D printing has seen remarkable advancements in recent years, with the technology finding applications in diverse industries. One exciting development is the emergence of light-curing 3D printing for manufacturing fully 3D printed slippers. This innovative approach to footwear design and production combines speed, customization, and sustainability to create comfortable and stylish slippers. In this blog post, we will explore the process of light-curing 3D printing, its advantages, and the potential impact on the footwear industry.
Light-Curing 3D Printing: An Overview
Light-curing 3D printing, also known as stereolithography (SLA) or digital light processing (DLP), is an additive manufacturing technique that uses light-sensitive resins to build 3D objects layer by layer. In the context of slipper manufacturing, the process involves selectively curing the resin using ultraviolet (UV) light to create the desired shape of the slipper sole and upper.
Advantages of Light-Curing 3D Printed Slippers
1. Speedy Production
The most striking advantage of light-curing 3D printing for slipper manufacturing is the incredible speed of production. Unlike traditional shoe manufacturing, which involves multiple steps and extended lead times, light-curing 3D printing can fabricate a complete pair of slippers in just one hour. This rapid production process allows for on-demand manufacturing, reducing inventory costs and meeting customer demands more efficiently.
2. Customization and Integrated Design
Light-curing 3D printing enables designers to create fully customized slippers that perfectly fit an individual's foot shape and size. Additionally, the technology allows for integrated design, where the sole and upper are seamlessly combined into a single 3D printed piece. This integration enhances comfort, durability, and aesthetics, offering a sleek and contemporary look.
3. Lightweight and Comfortable
The materials used in light-curing 3D printing for slippers are often lightweight and flexible, providing optimal comfort and support for daily wear. Designers can experiment with different materials to achieve the desired level of cushioning and flexibility, tailoring the slipper to suit various activities and lifestyles.
4. Sustainability
Light-curing 3D printing is inherently more sustainable than traditional manufacturing methods. The additive nature of 3D printing results in minimal waste, as the exact amount of material required is used to create each slipper. Additionally, the ability to produce slippers on-demand reduces overproduction and excess inventory, contributing to a more sustainable and eco-friendly footwear industry.
5. Design Freedom and Innovation
With light-curing 3D printing, designers have unparalleled freedom to experiment with intricate and complex geometries. This opens up possibilities for innovative and artistic designs that were previously challenging to achieve using traditional shoemaking techniques.
The Impact on the Footwear Industry
The introduction of light-curing fully 3D printed slippers has the potential to disrupt the traditional footwear industry. As consumers increasingly seek personalized and sustainable products, the on-demand nature of 3D printing offers a compelling solution. Customized slippers can be designed and produced swiftly, satisfying the preferences of individual consumers while reducing environmental impact.
Additionally, 3D printing allows for more efficient supply chains and localized manufacturing, reducing the need for global shipping and transportation. This localization can create opportunities for local businesses and manufacturers to cater to regional markets, supporting economic growth.
Conclusion
Light-curing fully 3D printed slippers represent a significant advancement in the field of footwear design and production. The combination of speed, customization, sustainability, and design freedom offers a new paradigm for the footwear industry. As 3D printing technology continues to evolve, we can expect further innovations in footwear design and manufacturing, with a focus on personalized, comfortable, and environmentally friendly products. The rise of light-curing 3D printed slippers signals a promising future for the footwear industry, where innovation and sustainability go hand in hand.
Yanko Design has just released its latest 3D printed footwear, with a cool design of all-in-one 3D printed shoes that they claim can be 3D printed in under an hour.
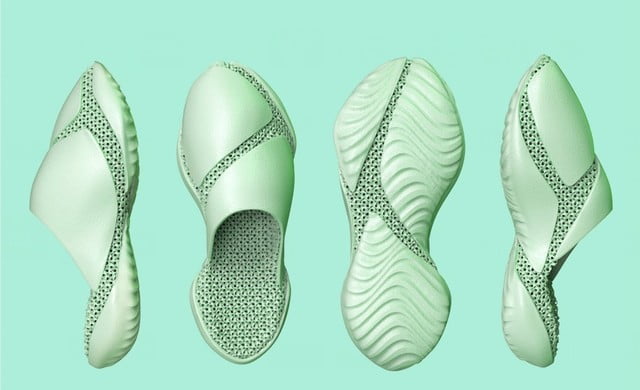
Designed by designer Shun Ping Pek, the shoes are so simple in construction that the entire shoe can be 3D printed in one go. The entire shoe consists of an inner mesh layer and an outer covering designed with several different sections to protect the foot. The shoe is shock absorbent and can be customised according to the wearer's wishes by using data from a pressure map of the foot, softening in one area and hardening in another.
The shoes are manufactured by relying on resin-based light-curing 3D printing technology and the price has not yet been announced. The biggest benefits of additive manufacturing are the affordability, incredible manufacturing speed and the ability to customise to the needs of the customer.
Clothing and footwear designers are enjoying 3D printing these days. Digital manufacturing is a tool that is clearly in the spirit of the art, as middlemen and factories can be cut out completely. Designers can come up with an idea at any time of the day or night, convert it to 3D and then start printing prototypes or actual functional pieces in small batches.