Table of Contents:
- Introduction
- Rapid Prototyping Techniques Used in Automotive field
- Applications of Rapid Prototyping in Automotive Field
- Advantages of Rapid Prototyping in Automotive Field
- Case Studies in Rapid Prototyping in Automotive Field
- Challenges and Limitations of Rapid Prototyping in Automotive Field
- Future of Rapid Prototyping in Automotive Field
- Conclusion
-
1. Introduction
The automotive industry has always been at the forefront of innovation and technology, constantly pushing the limits in terms of design, manufacturing, and performance. Rapid prototyping is one such innovation that has significantly impacted the automotive industry in recent years. Rapid prototyping is the process of quickly creating physical models, prototypes, or parts using computer-aided design (CAD) software and various manufacturing methods. The use of rapid prototyping has revolutionized the automotive industry, allowing for faster design to market time, cost reduction, improved quality, and increased innovation.
Definition of Rapid Prototyping:
Rapid prototyping is the quick and cost-effective production of physical prototypes, models, or parts using CAD software and various manufacturing methods, such as 3D printing, selective laser sintering (SLS), and computer numerical control (CNC) machining. The process of rapid prototyping enables engineers and designers to create a physical model as an accurate representation of the final product, which can then be tested and validated for design, function, and performance.
Importance of Rapid Prototyping in Automotive Industry:
Rapid prototyping has become increasingly important in the automotive industry due to its ability to accelerate innovation and production processes. The automotive industry is known for its complex designs and intricate manufacturing processes, and rapid prototyping has made it easier for manufacturers to create physical prototypes quickly and accurately, reducing the need for costly and time-consuming manual modeling. Rapid prototyping enables automotive design and engineering teams to produce a physical model for presenting to management, marketing, and stakeholders to assess design issues and make revisions. Moreover, rapid prototyping also enables engineers to test a product’s mechanical and structural properties to verify its design and fit for purpose before mass production. The application of rapid prototyping in the automotive industry can result in reduced production lead times, better product quality, and increased innovation, leading to a competitive edge in the automotive market.
-
2. Rapid Prototyping Techniques Used in the Automotive Field
There are several rapid prototyping techniques used in the automotive industry, each with its own benefits and limitations. The primary methods used in the automotive industry include 3D printing, selective laser sintering (SLS), and computer numerical control (CNC) machining.
- 3D Printing
3D printing, also known as additive manufacturing, is the most commonly used rapid prototyping technique in the automotive industry. 3D printing technology involves layer-by-layer additive manufacturing, where the printer deposits and fuses material layer by layer until the 3D object is complete. It is a versatile technology as it supports the use of various materials, such as thermoplastics, metal, and composites, and is capable of producing complex geometries, intricate designs, and customized parts. 3D printing is ideal for making concept models, detailed designs, and small-scale functional parts. - Selective Laser Sintering
Selective laser sintering is another rapid prototyping technique used in the automotive industry. SLS uses a high-powered laser to fuse powdered materials, such as nylon, metal, or ceramics, to create functional prototypes or final parts. The process is similar to 3D printing as it uses layer-by-layer printing to construct the parts. The primary advantage of SLS is that it can produce parts with complex geometries, which are difficult to achieve using traditional methods. Additionally, the process is fast and cost-effective, making it ideal for tooling and fixture production. - CNC Machining
CNC machining is a subtractive manufacturing process used in the automotive industry for rapid prototyping. CNC machines remove material from a solid block of material to produce a final part. The machines are precise and capable of producing complex geometries, making them ideal for producing small batches of complex parts or functional prototypes. Another significant advantage of CNC machining is that it can use a wide range of materials, including aluminum, plastics, and composites.
In conclusion, the automotive industry has made significant strides in the use of rapid prototyping technology to accelerate innovation and production. The various rapid prototyping techniques used in the automotive industry offer unique advantages in terms of design, function, and material usage. The choice of rapid prototyping technique depends on the specific requirements of the final product, project timeline, and budget constraints.
-
3. Applications of Rapid Prototyping in Automotive Field
Rapid prototyping is a vital tool in the automotive industry, and it offers several applications that have helped to revolutionize the entire design and production process. The primary applications of rapid prototyping in the automotive industry include concept design and visualization, functional testing and validation, tooling and fixture production, and manufacturing and production optimization.
- Concept Design and Visualization:
Concept design and visualization are critical applications that leverage rapid prototyping technology in the automotive industry. Rapid prototyping allows design teams to create physical prototypes or models quickly, enabling them to see the product’s overall design and evaluate it for any issues or improvements. The ability to create early-stage physical models and prototypes for automotive design, which are often complex and high-resolution structures, helps align disparate stakeholders and marketing teams with the same vision. - Functional Testing and Validation:
Rapid prototyping in the automotive industry enables engineers to test the prototypes’ functionality and validate the design. This application can reduce the product development cycle time, costs, and errors. Engineers can test the assemblies, parts, and components even before tooling, to optimize the designs or reduce the number of trials. Rapid prototyping also enables the engineers to scrutinize the prototypes’ mechanical properties, structural integrity, weight distribution, and aerodynamics, ensuring they meet the targets. - Tooling and Fixture Production:
Rapid prototyping methods like 3D printing, SLS, and CNC machining have improved tooling and fixture production in the automotive industry. Tooling and fixture production is one of the most critical functions of a production line, as it allows manufacturers to ensure that the assembly is correct and the parts are precise. Rapid prototyping can reduce the tooling and fixture production time and costs as it can quickly produce jigs/fixtures for use in Lean Manufacturing. - Manufacturing and Production Optimization:
Rapid prototyping is a game-changer in manufacturing and production optimization in the automotive industry. It enables manufacturers to produce small production runs and test design changes before implementing them on a large scale. Rapid prototyping can also help optimize manufacturing processes for quality control, cost accuracy, and time-to-market reduction.
In conclusion, rapid prototyping applications in the automotive industry have significantly impacted the industry’s design and production process. The applications discussed above are just a few of the possibilities made possible by rapid prototyping technologies. Many more possibilities are likely to emerge as technology continues to evolve, making the production of safer, lighter, and more sustainable vehicles a reality.
-
4. Advantages of Rapid Prototyping in Automotive Field
Rapid prototyping has become a valuable asset in the automotive industry, offering numerous advantages throughout the design and production process. Some of the benefits of rapid prototyping in the automotive industry include time and cost savings, improved quality and accuracy, and enhanced collaboration and communication within teams.
- Time and Cost Savings:
Rapid prototyping in the automotive industry can significantly reduce the lead time and cost involved in the product development process. Design to market time is a critical factor in the automotive industry, and rapid prototyping can help take out the guesswork and shorten the product development cycle. Rapid prototyping technologies allow manufacturers to test and validate their products quickly compared to traditional manufacturing methods. By reducing the production lead times and tooling costs, manufacturers can reduce waste and optimize inventory management systems. - Improved Quality and Accuracy:
Another significant advantage of rapid prototyping in the automotive industry is that it can improve product quality and accuracy. Rapid prototyping technologies allow engineers to make design iterations that can be tested, validated, and incorporated before final assembly. The ability to see physical prototypes and visualize design iterations in real-time offers unprecedented access to intuitive feedback and leads to higher accuracy in the parts and systems developed. - Enhanced Collaboration and Communication within Teams:
Rapid prototyping can improve collaboration and communication within automotive design and engineering teams. Rapid prototyping technologies allow teams to share designs and models quickly and easily, enabling participation among internal and external stakeholders. Rapid prototyping bridges gaps that may exist between departmental silos, and by enabling early buy-ins from visual prototypes and functional models, increases stakeholder alignment and helps promote project consensus.
Rapid prototyping technology use is widespread in the automotive industry for the reasons outlined above. The technology has significantly reduced product development lead times, allowing for more innovation and exploration of new materials, new concepts, and designs. Additionally, the ability to quickly produce prototype parts has also led to the development of newer manufacturing processes that reduce waste and operational overhead while maintaining product integrity.
In conclusion, the automotive industry’s rapid prototyping technology has brought about huge advancements in product development, quality, and time-to-market. Rapid prototyping enables manufacturers to achieve higher product quality, reduce costs and lead times, and improve collaboration across departments. The advantages of rapid prototyping in the automotive industry are expected to continue, with emerging technological innovations enhancing the industry further in the future.
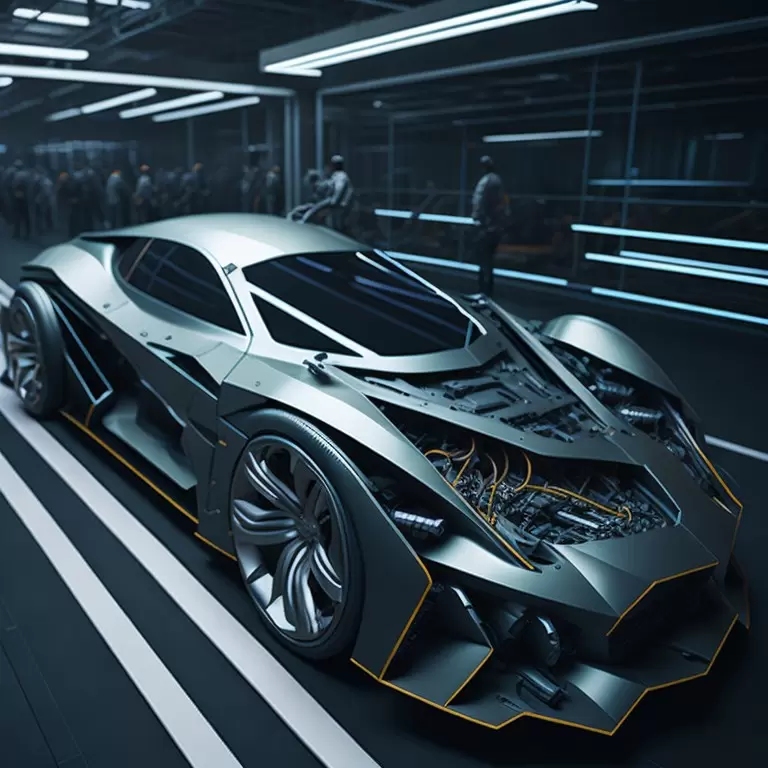
-
5. Case Studies in Rapid Prototyping in Automotive Field
There are numerous examples of rapid prototyping success stories in the automotive industry, but we will focus on three companies: Tesla, BMW, and Ford.
- Tesla:
Tesla is a pioneer in the use of rapid prototyping in the automotive industry, using 3D printing and other techniques to produce prototypes in-house. The company leverages rapid prototyping to accelerate product innovation, reduce costs, and improve the quality of their cars. Tesla uses complex CAD software to enable geometric design optimization and renders stunning visualizations for easy stakeholder alignment. Additionally, Tesla uses rapid prototyping to manufacture fixtures and production equipment, reducing costs and speeding up production. - BMW:
BMW is another automotive company that has adopted rapid prototyping technology to enhance its product development process. Using 3D printing and other techniques, BMW engineers can quickly prototype designs, evaluate concepts, and test parts, shortening the design-to-market process. BMW leverages the technology to offer individualized solutions to customer needs by creating customized and scalable designs quickly. Additionally, the company has used rapid prototyping to develop lightweight components that help reduce fuel consumption and carbon emissions. - Ford:
Ford Motor Company has also leveraged rapid prototyping technology to optimize the production process and reduce development costs. The company uses 3D printing and CNC machining to create prototypes and parts, enabling them to explore new material capabilities, validate new design concepts, and achieve increased production precision. Ford uses rapid prototyping tools to empower Design-For-Manufacturing methodologies, offering reduced risks and higher efficiency during new product releases.
In conclusion, these case studies demonstrate the many advantages and applications of rapid prototyping in the automotive industry, from conceptual design to functional testing, and production optimization. The widespread adoption of this technology has played a vital role in cost reduction, product innovation, and improved product quality across the industry. By using rapid prototyping technologies, automotive companies have achieved invaluable time-to-market reduction, generated testable research, and optimized production processes to ensure sustained success in a highly competitive business field.
-
6. Challenges and Limitations of Rapid Prototyping in Automotive Field
While there are many advantages to using rapid prototyping in the automotive field, there are also several challenges and limitations that manufacturers encounter. Here are some of the primary limitations faced by rapid prototyping in the automotive industry:
- Technical Limitations:
Rapid prototyping has technical limitations as it is not capable of producing industrial-level quality components. Where traditional manufacturing methods can produce high-volume parts at lower costs, rapid prototyping remains relatively costly for high-volume production. Additionally, the strength of the final product is also limited, as materials used in rapid prototyping have specific strength limitations. - Material Selection and Compatibility:
Material selection and compatibility are other significant limitations of rapid prototyping. With each rapid prototyping technology, there are constraints regarding the types of materials that can be used. Also, as material development moves at a slower pace compared to rapid prototyping technology, designers and engineers are limited to a fixed set of materials. Additionally, compatibility must be taken into account, as some materials may not work in all rapid prototyping methods, leading to potential issues in material optimization and product integrity. - Intellectual Property Concerns:
Rapid prototyping technology can make it easier for competitors to produce “copycat” designs of innovative car components, especially when files are shared across platforms. There is a need for more effective protective measures to safeguard intellectual property rights throughout the design and production cycle.
In conclusion, the rapid prototyping technology presents limitations and challenges to its widespread use in the automotive industry. More progress is needed in the development of advanced materials or material reinforcements to overcome the current technical limitations of rapid prototyping. Additionally, there is a growing need for protective measures, such as file protection, throughout the design and production cycle to safeguard intellectual property rights. As automotive companies move towards the development of Industry 4.0 manufacturing, rapid prototyping will continue to play a pivotal role in product innovation and production optimization.
-
7.Future of Rapid Prototyping in Automotive Field
Rapid prototyping is an ever-evolving technology, and the automotive industry’s future is teeming with possibilities. Here are some of the areas where we can expect rapid prototyping to make an increasingly significant impact in the future:
- Emerging Technologies:
With the rise of Industry 4.0, rapid prototyping technology in the automotive industry is set to take significant leaps forward. Emerging disruptive technologies such as 3D printing, Integrated Computational Materials Engineering (ICME), and Artificial Intelligence (AI), will continue to play a pivotal role in product development, supply chain optimization, and production cycles. - Integration with Industry 4.0:
The integration of Industry 4.0 into the automotive industry is set to revolutionize how products are designed, developed and produced. Rapid prototyping technologies will enhance digitalization in manufacturing through Computer-Aided Design (CAD) and Integrated Computational Materials Engineering (ICME) to optimize structures for material composition, formability, and design alternatives. Rapid prototyping will play a pivotal role in Industry 4.0 by enabling faster customization, real-time analytics, and optimizing manufacturing flow within a smart factory environment. - Impact on Supply Chain and Manufacturing Processes:
Rapid prototyping is also set to transform the automotive industry’s supply chain and manufacturing processes, reducing production timeframes and costs. The continued use of rapid prototyping technology allows designers to bring products like cars to the market faster and with less inherent risks. Rapid prototyping enables design and prototyping iterations that are validated, inspected and validated again, resulting in higher precision, quality, and accelerated time-to-market. Additionally, predictive maintenance, digital twins, and integrated quality control mechanisms enhance machine efficiency and optimize complex production processes.
In conclusion, the future of rapid prototyping in the automotive industry is bright, with exciting and transformative possibilities set to take shape. Rapid prototyping technologies will continue to play a pivotal role in product development, supply chain optimization, and product assembly for the automotive industry. As Industry 4.0 advances, rapid prototyping technologies will see even greater integration, enhancing supply chain efficiencies and changing manufacturing processes. The rapid prototyping market will continue to expand, with automotive companies and manufacturers looking to produce faster, more efficient, and customizable supply chains to enhance customer satisfaction and profitability.
If you want more about Rapid Prototyping In Automotive Field information ,You can click on the V1 Prototype website to find it.
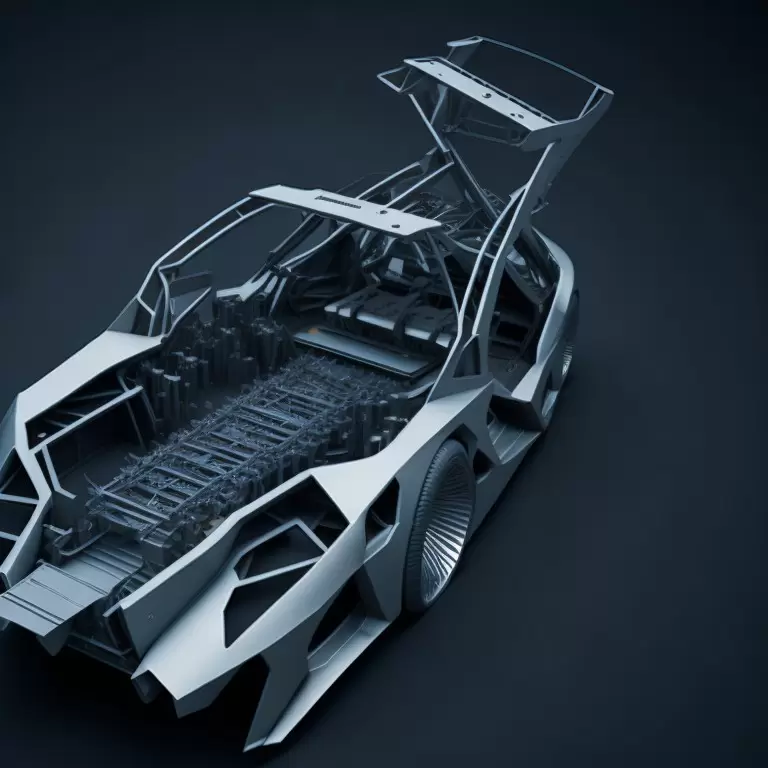
-
8. Conclusion
In conclusion, rapid prototyping technology has become a crucial tool in driving innovation and production in the automotive industry. Rapid prototyping technologies have enabled faster iterations, brought new materials into production, optimized designs, and ultimately accelerated time-to-market.
Rapid prototyping plays a significant role in the automotive industry, from early concept development and visualization to rapid production and end-user customization. By leveraging emerging technologies and Industry 4.0 advances, automotive companies and manufacturers are looking towards a future where rapid prototyping plays a pivotal role in product development and manufacturing supply chains.
While there are challenges and limitations to rapid prototyping, the technology’s benefits are enormous, resulting in streamlined product development, reduced costs, improved quality, and the optimization of manufacturing processes.
In summary, the continued advancements in rapid prototyping technologies will continue to impact the automotive industry, transforming how products are developed and produced, and ultimately improving the industry’s competitiveness. The future of rapid prototyping looks bright as the automotive industry embraces technology’s transformative potential to redefine mobility.