Table of Contents:
- Introduction to Plastic Mold Design
- Types of Plastic Molds
- Factors to Consider in Plastic Mold Design
- Plastic Mold Design Process
- Mold Maintenance and Repair
- Conclusion
-
1.Introduction to Plastic Mold Design
Plastic mold design is a critical process in the manufacturing of plastic parts and products. A mold is a tool consisting of a cavity into which molten plastic is injected, and then solidified to create a final product. Mold design is the process of creating the mold that will be used to manufacture the plastic part or product.
Definition of plastic mold design:
Plastic mold design is the process of designing and creating a mold that is used to produce plastic parts or products. The mold must be carefully designed to ensure that the final product meets the desired specifications.
Benefits of plastic mold design:
- Consistency: Plastic mold design ensures consistent production of high-quality plastic parts or products, meeting the required specifications and tolerances.
- Cost-effective: Plastic mold design is cost-effective in the long run, as it eliminates the need for manual labor and increases production speed and efficiency.
- Versatility: Plastic mold design allows for the creation of complex shapes and intricate designs, with sizes varying from small to large.
- Durability: Mold design ensures that molds are made with durable materials and are designed with high precision, making them long-lasting.
- Customization: Plastic mold design allows for customization of the design, making it possible to create unique and specialized products that meet specific customer needs.
-
2.Types of Plastic Molds
- Injection Mold:
Injection molds are the most common type of plastic molds used in manufacturing. This mold type consists of two plates that are clamped together, with the molten plastic injected into the cavity under high pressure. Once the plastic solidifies, the two plates are separated, and the finished product is ejected. - Blow Mold:
Blow molds are used to create hollow plastic products like bottles, jars, and containers. This type of mold has a cavity that is shaped like the desired product, and compressed air is blown into the cavity to create the final product shape. - Extrusion Mold:
Extrusion molds are used to create products with a continuous cross-section, such as tubing, pipes, and sheets. In this type of mold, the molten plastic is extruded through a die, which shapes the plastic into the desired product shape. - Compression Mold:
Compression molds are used to create solid plastic products like plates, discs, and other flat or round shapes. This type of mold consists of two plates that are heated and pressed together, forcing the molten plastic to take the shape of the cavity. Once the plastic cools and hardens, the mold is opened, and the finished product is ejected.
Overall, each type of plastic mold has its specific purpose and advantages, and choosing the right type of mold depends on the product and the production requirements.
If you need about Plastic Molding Services,You can click on the V1 Prototype website to find it.
-
3.Factors to Consider in Plastic Mold Design
- Material Selection:The material used for the mold must be carefully chosen based on the plastic material to be molded and the required production standards. Material selection criteria include factors such as durability, machinability, resistance to heat and chemical corrosion, and cost.
- Part Design:The design of the plastic part or product to be produced is crucial in mold design. The mold must be designed to accommodate the part’s features, which includes factors such as shape, size, and complexity, to ensure that the final product is accurate and precise.
- Wall Thickness:The thickness of the part’s walls is a critical factor in mold design, as it determines the flow of the plastic material and the cooling process. The mold must be designed in such a way as to achieve the desired wall thickness, ensuring that it’s uniform and consistent throughout the part.
- Draft Angle:A draft angle refers to the angle of the walls of the mold. It determines how easily the part can be ejected from the mold once it’s been formed. A properly designed draft angle is essential to ensuring the part can be released from the mold without damaging or distorting the part.
- Gate Design:The gate is the point where the molten plastic enters the mold cavity. The gate’s design and placement are essential in ensuring that the plastic flows evenly and that the final product is free of defects. Factors to consider include the gate’s size, shape, and location, as well as the type of gating system to be used.
- Ejection System:The ejection system is the mechanism that releases the final product from the mold after it has been formed. Factors to consider here include the ejection system’s location, shape, and speed, ensuring that it does not damage the product or cause any production defects.
Overall, these factors must be carefully considered during plastic mold design, as they affect not only the final product’s quality and accuracy but also the production efficiency and cost-effectiveness.
-
4.Plastic Mold Design Process
- Design Concept:The first step in plastic mold design is to create a design concept, which involves defining the product’s specifications and requirements. This step includes factors such as the part’s purpose, size, shape, and material.
- 3D Modeling:Once the design concept has been established, the next step is to create a 3D model of the product using computer-aided design (CAD) software. This step allows the designer to visualize the part in 3D, identify potential defects or design flaws, and make adjustments as needed to optimize the part’s performance.
- Mold Flow Analysis:Mold flow analysis is a critical step in mold design, which involves creating a simulation of the molten plastic’s flow through the mold cavity. This analysis helps the designer identify potential defects, such as air pockets or warping, and optimize the mold’s design to prevent such issues.
- Mold Assembly Design:With the 3D model and mold flow analysis in place, the mold assembly design can begin. This step involves creating the mold’s detailed design, including the cavities, cores, ejector pins, and other components. This step requires precision and attention to detail to ensure that the mold works efficiently and effectively.
- Mold Tooling Manufacture:The final step in the plastic mold design process is mold tooling manufacture. This step involves using computer-guided machining tools to create the mold tooling based on the detailed mold design. The mold must be manufactured to the highest standards of accuracy and quality to ensure the final product meets the desired specifications.
Overall, the plastic mold design process is complex, and each step requires careful attention to detail, precision, and expertise. A well-designed mold is essential to producing high-quality plastic parts and products while minimizing production costs and defects.
-
5.Mold Maintenance and Repair
- Importance of mold maintenance:Mold maintenance is a critical aspect of ensuring maximum lifespan, optimal performance, and cost-effectiveness of the mold. Through regular maintenance, it’s possible to identify and address minor issues before they escalate into major problems. Maintenance also helps to prevent defects in the final product, ensures efficient and consistent production, and minimizes downtime and repair costs.
- Common mold problems and repair solutions:Here are some of the most common problems that can occur in plastic molds and the repair solutions:
- Wear and Tear: Over time, the mold can experience wear and tear, leading to cracks, corrosion, and other issues. Regular maintenance can help identify and repair these issues before they become more severe. In severe cases, it may be necessary to replace some or all of the mold components.
- Parting Line Flash: Parting line flash refers to an extra layer of plastic that forms along the mold’s parting line. To fix this, the mold must be disassembled and cleaned properly, and any excess material removed.
- Warping: Warping occurs when the plastic part or product warps out of its desired shape during the cooling process. The solution to this problem involves identifying the cause of the warping, such as uneven cooling, and making adjustments to the mold design or process.
- Ejector Pin Marks: Ejector pin marks occur when the ejector pins on the mold leave visible marks on the plastic part. To solve this problem, the mold design may need to be adjusted to avoid these marks or to adjust the ejection system’s timing or configuration.
- Melt Line Defects: Melt line defects refer to marks or blemishes on the plastic part’s outermost layer. This issue may be caused by mold temperature, pressure, or other factors. Addressing the root cause of this problem can help avoid similar defects in the future.
Overall, by identifying and addressing these common mold problems through proactive maintenance and repair, it’s possible to ensure optimal performance and lifespan of the mold, reduce production costs, and produce high-quality plastic parts and products.
-
6.Conclusion
Plastic mold design is a critical process in the production of plastic parts and products, requiring a high level of expertise and attention to detail. The design process involves several critical steps, including design concept, 3D modeling, mold flow analysis, mold assembly design, and mold tooling manufacture.
Maintenance and repair are crucial in ensuring the mold’s optimal performance and lifespan, as regular maintenance can help identify and address minor issues before they escalate into bigger problems that can affect the final product’s quality and performance. A well-designed and properly maintained mold is essential for achieving efficient and consistent production, reducing costs, and minimizing defects.
Potential future developments in plastic mold design:
Some potential future developments in plastic mold design include the use of advanced materials, such as high-strength alloys and ceramics, that are more durable and resistant to wear and corrosion. Additionally, advances in computer simulation and AI technology may improve the mold’s design and optimization, increasing production efficiency and accuracy.
In conclusion, plastic mold design is an essential process in the production of plastic parts and products. By considering the various factors involved in mold design, undertaking proper maintenance and repair regimes, and keeping abreast of future technological developments, it’s possible to produce high-quality plastic products and stay ahead of the pack in this competitive industry.
References and Additional Resources:
- Injection Molding Design Guide, Proto Labs
- Mold Design Handbook, Hanser Publications
- Plastic Mold Design Fundamentals, R.G.W. Pye
- Moldflow Analysis Tutorial, Autodesk
- Injection Molding Troubleshooter, Jay W. Cadwell
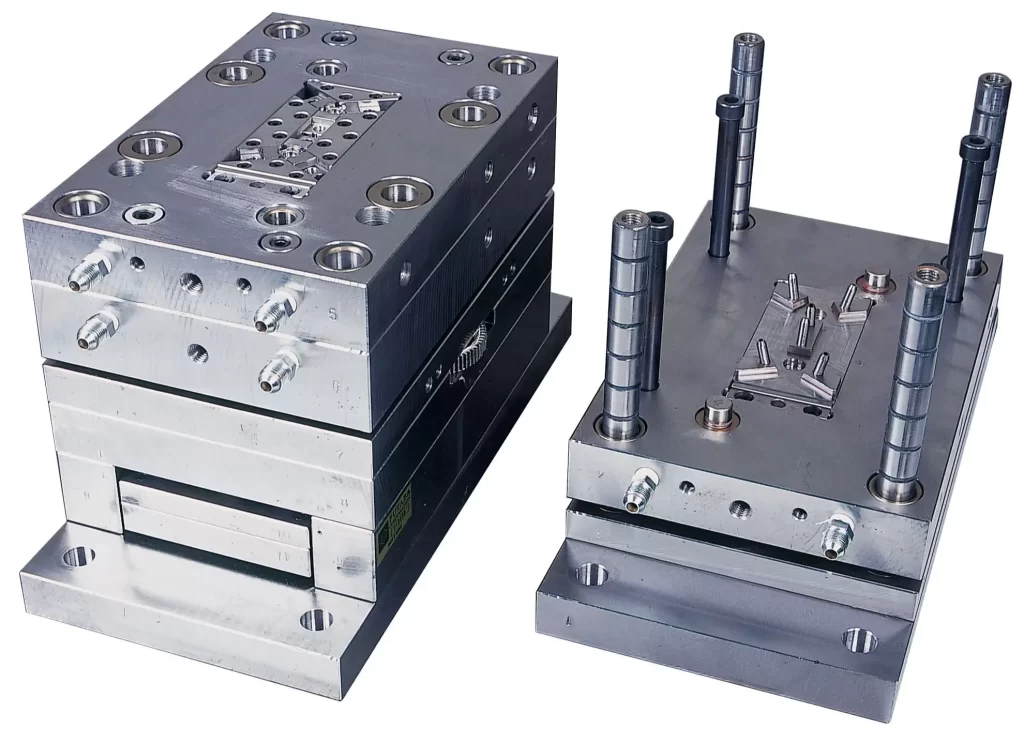