we delve into the world of design modeling and 3D printing, exploring innovative techniques that push the boundaries of creativity and innovation. From conceptualizing ideas to creating detailed models, we'll explore how these technologies can transform the way we approach design and manufacturing. Join us as we explore the potential of design modeling and 3D printing in driving innovation and creativity in various industries.
I. Introduction
A. Overview of Design Modeling and 3D Printing
In the realm of design and manufacturing, the integration of design modeling and 3D printing has revolutionized the way products are conceived and brought to life. Design modeling serves as the blueprint for innovation, allowing designers to create and refine digital models. 3D printing then brings those models into tangible existence through additive manufacturing. This synergy has transformed how products are developed, from concept to production. This section provides a comprehensive overview of these two crucial components, highlighting their individual significance through the design and prototyping processes. It also emphasizes the transformative synergy they create when combined through integrated digital workflows.
B. Importance of Innovation and Creativity in Design and Manufacturing
Innovation and creativity are the lifeblood of progress, especially in design and manufacturing. New ideas that challenge conventions lead to novel designs and production methods. The design process itself is a creative endeavor, requiring imagination to conceive new solutions. Manufacturing also benefits from innovative thinking to improve efficiency and quality. This segment explores in more depth how creativity plays a key role at each stage, from initial concepts to optimized manufacturing techniques. It delves into examples that demonstrate how pushing boundaries leads to groundbreaking products. Understanding this intrinsic link sets the stage for exploring how design modeling and 3D printing amplify innovation.
C. Objectives of the Guide
As we embark on this guide, our primary objectives are to provide a comprehensive overview of these interconnected fields. We aim to demystify the techniques involved, from sketching and CAD to various 3D printing processes. Showcasing real-world applications and examples reveals their potential for innovation and problem-solving. The guide also offers practical insights for effective implementation. By the end, readers should have an in-depth understanding of tools, workflows, future applications and considerations for responsible development. This will empower continuous advancement.
II. Design Modeling Techniques
A. Sketching and CAD Software for Design Modeling
The journey begins with foundational skills. Sketching on paper or digitally remains a primary outlet for creativity in design. It allows for rapid ideation outside the constraints of CAD systems. This section explores effective sketching techniques such as using different line weights to convey different levels of detail, shading to add realism, and rough dimensioning. Examples include sketches of common objects like chairs or tools at various levels of refinement. Computer-Aided Design (CAD) software then builds upon initial concepts. 2D CAD packages like AutoCAD aid in technical drawing creation while 3D CAD software such as SolidWorks and Fusion 360 translate rough sketches into precise parametric or solid models. Understanding when to use sketching versus CAD is important - sketching fosters early creativity while CAD enables engineering-level definition.
B. Parametric Modeling and Computer-Aided Design (CAD)
Taking modeling further, parametric design and advanced CAD techniques are covered in more depth. Parametric modeling uses design intent and parameters to create dynamically scalable models. Changes update dependent features automatically through the use of equations and constraints. This allows for easy design iteration and optimization. Popular CAD software like SolidWorks and Fusion 360 utilize this approach through their history-based modeling tools. Their capabilities for complex surface modeling using lofts and sweeps as well as assembly modeling using part configurations and joints are examined in detail using specific examples. Realizing designs digitally through parametric modeling streamlines downstream tasks such as engineering change management.
C. Prototyping and Validation
Prototyping bridges the virtual-physical gap and is discussed in more detail here. Examples show how rapid prototyping using inexpensive methods like 3D printing facilitates iterative validation and refinement of designs. Specific case studies demonstrate how prototypes catch issues like improper ergonomics, durability concerns or poor aesthetics early in the design process. The process of testing initial prototypes, analyzing user feedback, and improving the design concept is explored in a step-by-step manner. The benefits of rapid iteration using prototyping for maturing a design concept prior to manufacturing are emphasized.
III. 3D Printing Basics
A. Understanding 3D Printing Technology
This section comprehensively explains 3D printing technology, which transforms digital designs into physical objects. The layer-by-layer additive manufacturing process is described in detail. Methods like material extrusion, photopolymerization and powder bed fusion are introduced. Key advantages like design freedom, mass customization capabilities and on-demand manufacturing are explored. Understanding the core layering approach demystifies 3D printing.
B. FDM (Fused Deposition Modeling) and SLA (Stereolithography) Printing
Two prominent techniques - Fused Deposition Modeling (FDM) and Stereolithography (SLA) - are examined closely. FDM deposits and bonds plastic filament through a movable extruder. SLA uses ultraviolet lasers to cure liquid photopolymer resin. Their detailed processes, capabilities, common materials and ideal applications are discussed. Real-world examples showcase effective usage of each method.
C. Supported Materials and Processes
Material selection impacts the final 3D printed part or prototype. Commonly used thermoplastics, photopolymers, metals, ceramics and composites are introduced. Characteristics like strength, temperature resistance and surface finish are evaluated to determine suitability. Post-processing techniques like support removal, infiltration and heat treatment are also examined to optimize properties and functionality.
IV. Innovation and Creativity in Design Modeling and 3D Printing
A. Case Studies of Innovative Designs and Products
Turning theory into practice, compelling real-world examples are presented. From consumer products to medical devices, case studies showcase the limitless potential of integrated digital design and additive manufacturing. In-depth analyses reveal how non-traditional designs address specific needs through creative applications. Successful outcomes inspire further innovation.
B. Collaborative Projects and Teamwork
Innovation thrives on collaboration. Examples demonstrate how interdisciplinary teams across industries, academia and startups achieve more through cooperation. Anecdotes illustrate how combining varied skills and perspectives leads to new applications. Strategies for effective team-based innovation are also provided. Readers learn that partnership amplifies creativity.
C. Challenges and Overcoming Obstacles
While innovation faces hurdles, understanding and overcoming challenges is key. Technical, resource and conceptual roadblocks are examined alongside solutions. Time management, intellectual property protection and production scaling issues are also addressed. Realistic strategies empower readers to navigate obstacles. Continuous learning ensures challenges evolve into opportunities.
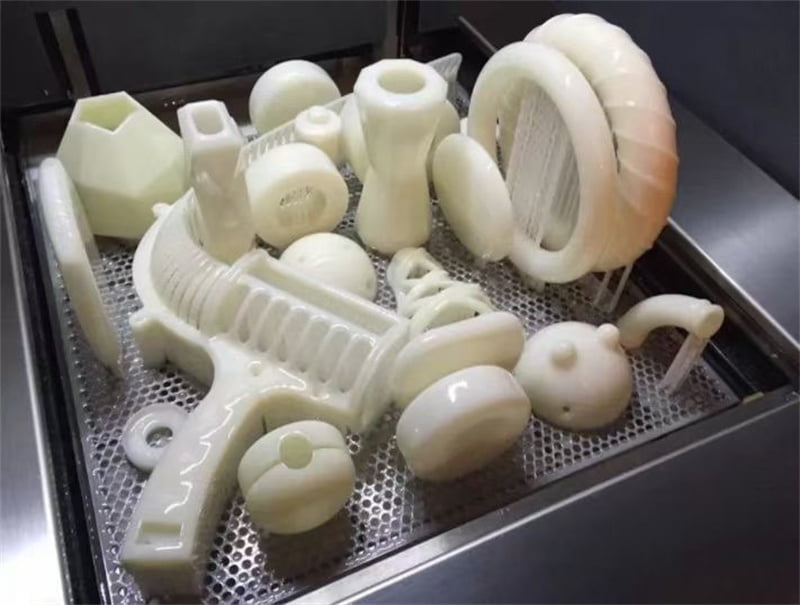
V. Applications of Design Modeling and 3D Printing
A. Product Development and Manufacturing
From initial concepts to mass production, integrated digital workflows streamline processes. Case studies demonstrate reduced costs, lead times and inventories in more detail. For example, an automotive manufacturer case study shows 25% lower production costs through iterative prototyping guided refinements before tooling. On-demand manufacturing supports mass customization and personalization through modular product architectures and on-site 3D printing. Readers gain insights into quantified benefits applicable across industries seeking increased efficiency and manufacturing flexibility.
B. Customization and Personalization
3D printing and modeling unlock far-reaching personalization possibilities, as discussed in more depth. Specific examples include orthotics customized to patient scans, reducing wait times. Prosthetic case studies show on-demand devices fitted for accurate mobility. Hearing aid manufacturers discuss streamlined mass-customization improving care access. Readers understand through compelling use cases how customization enhances user experiences, clinical outcomes, and access to assistive technologies.
C. Education and Training
These technologies revolutionize learning as discussed in richer detail. Project examples demonstrate hands-on prototyping cultivating creative problem-solving skills. Medical and STEM programs have adopted 3D printed anatomical models and equipment to advance education. Engineering curriculum at various universities has incorporated CAD/CAM into core classes. Makerspaces on school campuses are discussed as collaborative work areas fostering cross-disciplinary innovation. Overall readers gain deeper insights into enriched educational practices cultivating skills through design modeling and 3D printing.
VI. Future Trends and Opportunities in Design Modeling and 3D Printing
A. Emerging Technologies and Innovations
Cutting-edge advancements continually expand applications. Generative design automates concepting. AI augments modeling workflows. Multi-material 3D printing enables sophisticated compositions. 4D printing produces shapes that transform over time. Augmented and virtual reality immerse users in digital environments. Readers glimpse the exciting possibilities ahead.
B. Potential Impact on Design and Manufacturing
Trends are poised to reshape industries through streamlined operations, on-demand customization at scale and sustainable practices. Readers analyze impacts across sectors to recognize opportunities. By understanding technology trajectories, individuals and businesses can pioneer the future through informed implementation.
C. Ethical and Environmental Considerations
Responsible development requires addressing implications proactively. Intellectual property policies protect innovation. Regulations ensure safety and environmental stewardship. Design philosophies prioritize recyclability and eco-friendly materials. Overall readers gain awareness to guide technology towards maximizing human and planetary well-being.
VII. Practical Tips and Best Practices
A. Tools and Software for Design Modeling and 3D Printing
A comprehensive toolkit is outlined to empower effective usage. Industry-leading CAD, CAM, 3D scanning and post-processing software packages are introduced. Readers acquire knowledge for tool selection matching needs and budgets. Resources are also provided for ongoing learning.
B. Time Management and Project Planning
Readers learn techniques for planning projects, setting achievable milestones, prioritizing tasks, documenting workflows, conducting reviews and resolving issues. Examples illustrate how efficiency stems from organization and communication. Teams are guided to success through practical strategies.
C. Troubleshooting Common Issues and Errors
Anticipating challenges is key to overcoming them. Potential software, hardware, design and production glitches are presented alongside remedies. Readers gain diagnostic skills through comprehensive problem-solving guidance. Continuous improvement stems from lessons learned.
VIII. Conclusion
A. Recap of Key Findings and Takeaways
This guide aimed to provide a well-rounded perspective on design modeling, 3D printing, and their transformative synergy. Readers are reminded of fundamentals, applications, considerations, trends and best practices covered. They leave with appreciation for creativity and innovation through these integrated digital technologies.
B. Encouragement for Continued Learning and Innovation
The journey has only begun - technologies will continue advancing. Readers are encouraged to expand knowledge, explore new avenues and contribute their own innovations. Industry partnerships and academic research will strengthen the field through cooperation. With dedication to learning, problem-solving and responsible development, design modeling and 3D printing can progress towards benefiting all of humanity.