Table of Contents:
- Introduction
- CNC Machining Products Overview
- CNC Milling Machines
- CNC Lathes
- CNC Router Machines
- CNC Plasma Cutting Machines
- Applications of CNC Machining Products
- Conclusion
-
1.Introduction
CNC (Computer Numerical Control) machining refers to a manufacturing process that utilizes pre-programmed computer software to control and operate machinery tools. CNC machining eliminates the need for manual intervention and delivers high-precision results for mass production or prototyping. CNC machining has revolutionized the manufacturing industry by offering increased productivity, accuracy, and efficiency. CNC machines offer several key benefits, including increased flexibility, improved repeatability, and reduced setup times, all of which lead to cost savings. Overall, CNC machining products offer precision and efficiency that are unmatched by traditional manual methods of machining.
-
2.CNC Machining Products Overview
CNC machining products encompass a range of machines used for various manufacturing processes. This section provides an overview of the different types of CNC machining products and the materials that are suitable for CNC machining.
Types of CNC machining products:
- CNC Milling Machines: These machines utilize a rotating cutting tool to remove material. Ideal for producing complex parts with high precision using a range of materials including metals, plastics, and composites.
- CNC Lathes: These machines rotate the material while the cutting tool is held stationary. Ideal for producing cylindrical parts, such as shafts, rods, and bearings using a range of materials including metals, plastics, and composites.
- CNC Router Machines: Router machines are ideal for milling, drilling, and cutting wood, plastic, PVC, and other materials. They are commonly used for making signs, furniture, and other decorative items.
- CNC Plasma Cutting Machines: These machines use a plasma torch with high velocity to cut and shape metals. These machines are ideal for cutting thick materials such as thick sheets and tubes.
Material suitability for CNC machining:
CNC machining can be used with a variety of materials, although some materials are better suited than others. Materials suitable for CNC machining include metals (such as aluminum, steel, brass, and titanium), plastics, composites, wood, and ceramics. In general, materials that are hard, tough, and durable are suitable for CNC machining. However, materials that are waxy, brittle, or fibrous may not be suitable for CNC machining. Before CNC machining is performed, the machinist should carefully review the material properties to ensure the tolerance and finish requirements are met.
-
3.CNC Milling Machines
CNC milling machines are one of the most commonly used CNC machining products. In this section, we will cover their overview, working principle, commonly used types, and the benefits of using CNC milling machines.
Overview and working principle:
CNC milling machines are utilized for the milling process, which involves removing material from a workpiece using rotating cutting tools. The workpiece is held in place on a table, while the cutting tool is moved in various directions to remove material. This cutting operation can be performed in 3-axis, 4-axis, or 5-axis mode, depending on the machine’s specification.
Commonly used types of CNC milling machines:
- Vertical Milling Machine: The spindle axis is perpendicular to the table, which allows for easy drilling, cutting, and shaping operations.
- Horizontal Milling Machine: The spindle axis is parallel to the table, which enables cutting with larger surface area.
- Bed Milling Machine: Uses a bed to support the cutting tools in the X, Y, and Z-axis.
- Gantry Milling Machine: Has a bridge-like structure, mainly used for producing large or complex parts.
Advantages of using CNC milling machines:
- Increased Precision: CNC milling machines are capable of achieving high-precision results, making them ideal for complex and intricate parts.
- Improved Efficiency: CNC milling machines allow for faster and more efficient production, reducing the time and labor required for manual machining.
- Flexibility: Due to their programmable nature, CNC milling machines can produce a wide range of parts and shapes without requiring the retooling of the machine.
- Cost Savings: With reduced labor and setup times, CNC milling machines offer cost savings and increased productivity compared to traditional milling methods.
-
4.CNC Lathes
In this section, we will cover an overview of CNC lathes, their working principle, commonly used types, and the benefits of using CNC lathes.
Overview and working principle:
CNC lathes are utilized for turning operations, which involve rotating the workpiece while a cutting tool removes material to achieve the desired shape and size. The cutting tool is moved along the workpiece either horizontally or vertically, creating a cylindrical or conical shape. The lathe can operate in a 2-axis or 3-axis mode, allowing for complex shapes and threads to be produced.
Commonly used types of CNC lathes:
- Horizontal CNC Lathe: The workpiece is held parallel to the ground, while the cutting tool is moved perpendicular to the axis of rotation.
- Vertical CNC Lathe: The workpiece is held perpendicular to the ground, while the cutting tool is moved parallel to the axis of rotation.
- Swiss CNC Lathe: Used for producing small, precise, and complex parts, capable of producing parts with high precision and accuracy due to a unique guide bushing method.
Advantages of using CNC lathes:
- Precision: CNC lathes offer higher precision than traditional lathes, which lead to better surface finishes and tighter tolerances.
- Automation: CNC lathes are automated, requiring minimal manual intervention.
- Complex Shapes: CNC lathes can produce complex geometries, including threads, tapers, and chamfers, with high repeatability.
- Fast Setup: CNC lathes require a quick setup time, allowing for faster production compared to traditional lathes.
- Cost-Effective: CNC lathes offer cost savings by reducing labor costs and increasing production efficiency and throughput.
-
5.CNC Router Machines
CNC router machines are commonly used for cutting and shaping wood, plastics, and other soft materials. In this section, we will cover the overview, working principle, commonly used types, and advantages of using CNC router machines.
Overview and working principle:
CNC router machines use rotating cutting tools to cut and shape materials. The machine moves the cutting tool in the X, Y, and Z directions, enabling the production of complex, high-precision shapes and curves. The material to be cut is placed on a table, and the cutting tool moves along the material to achieve the desired outcome. CNC router machines can operate in a 3-axis, 4-axis, or 5-axis mode, depending on their specification.
Commonly used types of CNC router machines:
- Desktop CNC Routers: Small table-top machines, usually used for crafting and hobby purposes.
- Industrial CNC Routers: Large machines used for production in industrial settings, capable of processing large sheets of material.
- Gantry CNC Routers: Oversized CNC routers designed for producing large or heavy products.
Advantages of using CNC router machines:
- High Precision: CNC routers offer high-precision results, producing complex shapes and curves with ease.
- Versatile: CNC routers are versatile machines that can cut a wide range of materials, including woods, plastics, and composites.
- Efficiency: With their automated cutting processes, CNC routers are faster and more efficient than traditional routing methods.
- Repeatability: CNC routers produce precise and repeatable cuts, reducing material wastage and ensuring consistent results every time.
- Cost Savings: CNC routers can save businesses money by reducing the time, labor, and error rates associated with manual routing methods.
-
6.CNC Plasma Cutting Machines
In this section, we will cover the overview, working principle, commonly used types, and advantages of using CNC plasma cutting machines.
Overview and working principle:
CNC plasma cutting machines use high-velocity hot plasma to cut and shape metals. The machine moves the plasma torch in the X, Y, and Z directions, depending on the cutting requirements. The material is held in place on a table, and the plasma torch moves along the material surface, producing a high-precision cut. The plasma arc is generated by ionizing gas molecules, which is then used to melt and blow away the metal to form the desired shape.
Commonly used types of CNC plasma cutting machines:
- Benchtop CNC Plasma Cutters: These machines are small and most commonly used for small hobby projects.
- Portable CNC Plasma Cutters: These machines are designed for easy transportation and small-scale production.
- Industrial CNC Plasma Cutters: Large machines designed for heavy-duty industrial use.
Advantages of using CNC plasma cutting machines:
- High Speed: CNC plasma cutting machines can cut through metal at high speeds, increasing overall productivity.
- Precision: CNC plasma cutting machines offer high precision cutting results, with consistently high quality and repeatability.
- Versatility: CNC plasma cutting machines can cut a wide range of materials, including steel, aluminum, and brass.
- Minimal Material Wastage: CNC plasma cutting machines produce minimal waste, costing less in materials and reducing environmental waste levels.
- Cost Effective: CNC plasma cutting machines have a lower cost than laser cutters, making them an affordable solution for metal cutting and fabrication needs.
-
7.Applications of CNC Machining Products
CNC machining products are used in a wide range of industrial and commercial applications, including:
- Aerospace and Aviation industry: For producing aircraft parts and components.
- Automotive Industry: For manufacturing automotive parts and components.
- Medical Industry: For producing surgical instruments, implants, and prosthetics.
- Electronics Industry: For producing printed circuit boards and electrical components.
- Architectural Industry: For producing customized metal structures for the construction of buildings.
- Consumer Products industry: For producing high-quality consumer products such as jewelry, watches, and eyeglasses.
- Furniture Industry: For producing custom furniture and fixtures.
Click on the V1 Prototype website to gain more information.
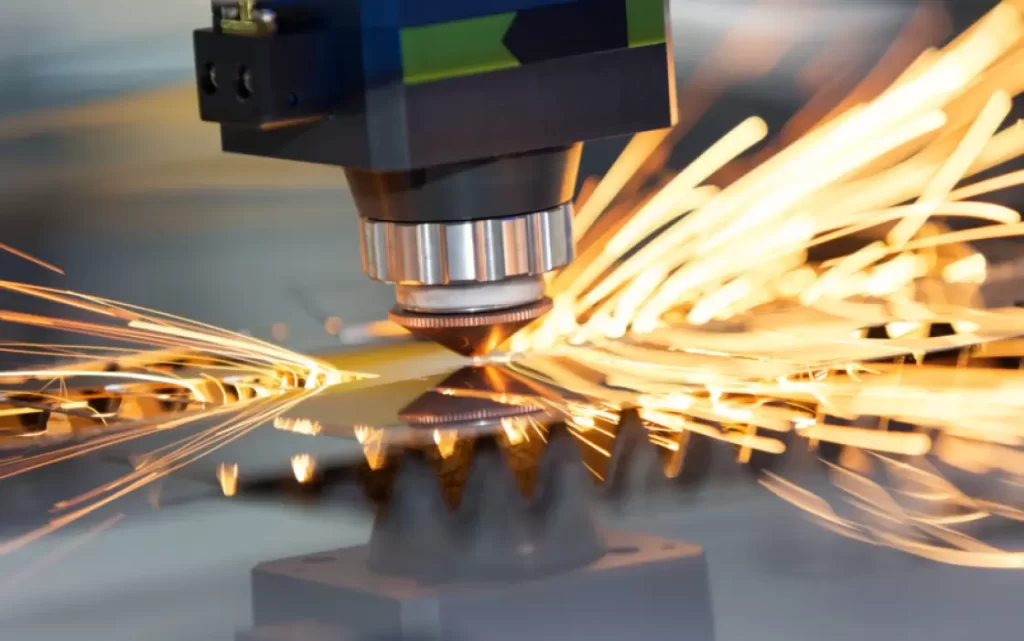
-
8.Conclusion
CNC machining products are an integral part of the manufacturing industry, offering precision, efficiency, and cost savings. The benefits of CNC machining products include increased productivity, versatility, precision, and cost savings. With their programmable nature, CNC machines offer a wide range of applications in various industries, from aerospace and automotive to medical and electronics. As technology continues to advance, CNC machining products will become more sophisticated, offering even more benefits to the manufacturing industry.
CNC machining products are the result of advanced technology that uses computer-controlled machines to produce precise and efficient parts and components. CNC stands for computer numerical control, which means that the machine follows a set of instructions encoded in a numerical code. CNC machining products can be made from various materials, such as metal, plastic, wood, or composite, and can have complex shapes and features that are difficult or impossible to achieve with manual methods. CNC machining products have many advantages, such as:
- High accuracy and consistency: CNC machines can produce parts with tight tolerances and minimal errors, ensuring that every product meets the specifications and quality standards.
- High productivity and efficiency: CNC machines can operate continuously and automatically, reducing the need for human intervention and supervision. CNC machines can also perform multiple tasks simultaneously, such as drilling, milling, turning, and cutting, saving time and resources.
- High flexibility and versatility: CNC machines can be programmed to create different products with different designs and dimensions, allowing for customization and innovation. CNC machines can also adapt to changing demands and requirements, such as new materials or specifications.
CNC machining products are widely used in various industries, such as aerospace, automotive, medical, military, and construction. CNC machining products can range from small components, such as screws and bolts, to large parts, such as engine blocks and turbine blades. CNC machining products can also be integrated with other technologies, such as 3D printing, robotics, or artificial intelligence, to create smart and innovative solutions.
If you are looking for CNC machining products that offer precision and efficiency at your fingertips, you have come to the right place. We are a leading provider of CNC machining products that can meet your needs and expectations. We have a team of experienced and skilled engineers who can design and manufacture CNC machining products according to your specifications. We have a fleet of state-of-the-art CNC machines that can handle any project size and complexity. We have a strict quality control system that ensures that every product is tested and inspected before delivery. We have a fast turnaround time and competitive prices that make us your best choice for CNC machining products.
Contact us today to get a quote or to learn more about our CNC machining products. We are ready to serve you with excellence and professionalism.