Multi-material additive manufacturing, also known as material jetting, enables the production of complex components with diverse materials and properties. This guide delves into the design and fabrication processes of multi-material additive manufacturing, exploring its potential in various industries. You'll learn about the latest technologies, materials combinations, and manufacturing applications that are revolutionizing product design and production. With this comprehensive guide, you'll gain innovative insights into multi-material additive manufacturing and its impact on modern industry.
I. Introduction to Multi-Material Additive Manufacturing
A. What is Multi-Material Additive Manufacturing?
Multi-Material Additive Manufacturing (MM-AM) represents a significant advancement in 3D printing technology, allowing the simultaneous use of multiple materials in the fabrication process. Unlike traditional additive manufacturing methods that are often limited to a single material, MM-AM opens the door to a new realm of possibilities. This technology enables the creation of complex and functional structures by combining materials with diverse properties, offering unprecedented versatility in design and fabrication.
B. The Evolution of Multi-Material AM Technology
The evolution of Multi-Material Additive Manufacturing technology is a testament to the relentless pursuit of innovation within the 3D printing industry. Early 3D printers were limited to single-material deposition, but as technology advanced, the demand for more versatile and sophisticated capabilities emerged. The development of MM-AM has seen the integration of multiple print heads, advanced material extrusion systems, and intricate software controls, allowing for the precise deposition of various materials in a single printing process.
C. The Role of Materials in Design and Fabrication
Materials play a pivotal role in the design and fabrication process of Multi-Material Additive Manufacturing. The ability to combine materials with different mechanical, thermal, or electrical properties opens up a plethora of applications. From creating products with varying levels of flexibility and strength to embedding electronic components seamlessly, the choice of materials becomes a critical factor in achieving the desired functionality. MM-AM empowers designers and engineers to optimize material selection based on specific requirements, leading to innovative and tailor-made solutions.
In the realm of Multi-Material Additive Manufacturing, the synergy between technology and materials defines the landscape. As we delve deeper into the intricacies of MM-AM, it becomes apparent that this technology is not merely a progression from its single-material counterparts but a paradigm shift that unlocks a new dimension of possibilities in design and fabrication.
Stay tuned for the upcoming sections as we explore the design principles, fabrication techniques, and applications that make Multi-Material Additive Manufacturing a transformative force in the world of advanced manufacturing.
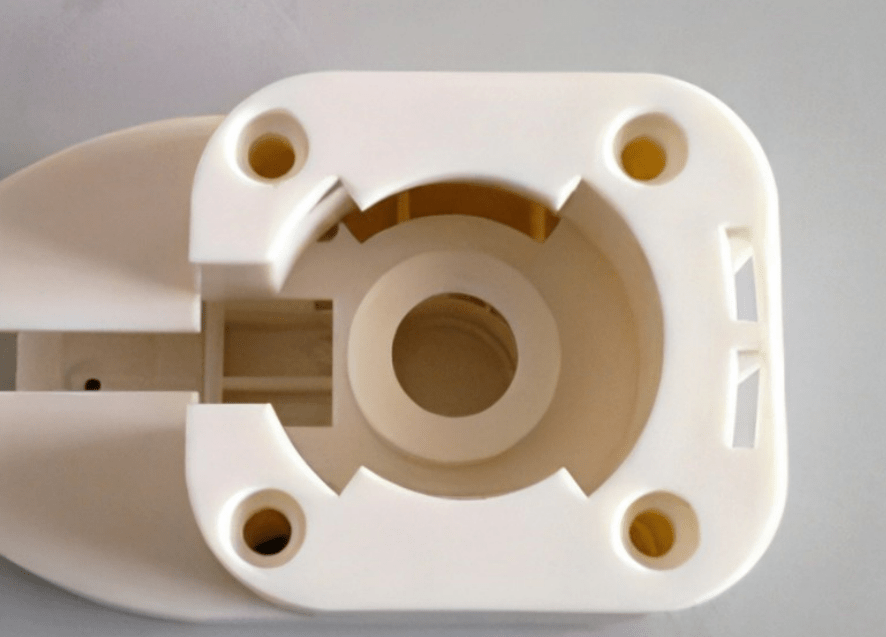
II. Design Considerations for Multi-Material AM
A. Material Properties and Interactions
In the realm of Multi-Material Additive Manufacturing (MM-AM), understanding material properties and their interactions is paramount. Each material utilized in the printing process brings unique characteristics to the final product. Designers must meticulously evaluate factors such as thermal expansion, adhesion, and compatibility to ensure that the chosen materials interact seamlessly during printing and deliver the desired mechanical and aesthetic properties. This intricate understanding of material behavior forms the foundation for successful MM-AM designs.
B. Design for Assembly and Disassembly
One of the distinctive advantages of MM-AM is the ability to create assemblies with integrated components made from different materials. Designing for assembly and disassembly becomes a critical consideration, especially when creating complex structures with multiple parts. Ensuring that components fit together seamlessly and can be disassembled without compromising structural integrity is essential for applications where maintenance, repairs, or upgrades are anticipated. This approach enhances the overall lifecycle and sustainability of MM-AM products.
C. Material Zoning and Customization
Material zoning and customization are key design considerations that leverage the versatility of MM-AM. Designers can strategically assign different materials to specific regions of a product, tailoring properties to meet specific functional requirements. For example, a product may have rigid and flexible zones, or areas with varying thermal conductivity. This level of customization allows for the creation of highly specialized and optimized components, pushing the boundaries of what is achievable with traditional manufacturing methods.
D. Simulation and Modeling Tools for Design
The complexity of Multi-Material Additive Manufacturing necessitates advanced simulation and modeling tools to ensure the feasibility and predictability of designs. These tools simulate the interaction between materials, predict structural behavior, and optimize designs for performance. Engineers and designers can utilize simulations to identify potential challenges, such as stress concentrations or material incompatibility, allowing for iterative refinement before the physical printing process begins. This iterative design approach significantly reduces the risk of errors and enhances the overall efficiency of MM-AM projects.
As designers navigate the unique challenges and opportunities presented by Multi-Material Additive Manufacturing, these considerations become crucial elements in creating successful and innovative products. The synergy between design principles and the capabilities of MM-AM technology defines the future of advanced manufacturing, where customization and functionality converge in unprecedented ways. In the subsequent sections, we'll delve into the practical aspects of fabrication and explore real-world applications that showcase the transformative potential of Multi-Material Additive Manufacturing.
III. Fabrication Processes of Multi-Material AM
A. Material Jetting Technologies
Material jetting is a cutting-edge Multi-Material Additive Manufacturing (MM-AM) process that involves jetting droplets of liquid photopolymer onto a build platform. Each droplet is selectively cured by ultraviolet (UV) light, layer by layer, forming the desired 3D object. This technology allows for the simultaneous use of multiple materials, providing exceptional resolution and enabling the creation of complex, multi-material prototypes and end-use parts. Material jetting is particularly suitable for applications where high precision and fine details are crucial.
B. Binder Jetting
Binder jetting is a versatile MM-AM process that utilizes a powder bed and selectively deposits a liquid binding agent to solidify specific areas. Multiple materials can be used in the powder bed, offering the flexibility to create multi-material structures. After the printing process, the part undergoes post-processing, often involving sintering to achieve the desired mechanical properties. Binder jetting is known for its speed and cost-effectiveness, making it an attractive option for producing complex and large-scale multi-material components.
C. Powder Bed Fusion
Powder bed fusion in the context of MM-AM involves selectively fusing powdered materials layer by layer using a heat source, such as a laser or electron beam. This technique enables the creation of multi-material objects by introducing different powders into the build chamber. The heat source selectively melts the powders, resulting in a solidified structure. Powder bed fusion is renowned for its precision and ability to produce intricate, high-resolution multi-material parts, making it a preferred choice for applications demanding exceptional detail.
D. Vat Photopolymerization
Vat photopolymerization, commonly associated with stereolithography (SLA), is adapted for multi-material applications in MM-AM. This process uses a vat of liquid photopolymer resin that is selectively cured layer by layer using UV light. By incorporating multiple materials into the resin, Vat Photopolymerization can produce objects with varying properties in a single print. This technique is ideal for creating detailed, high-resolution multi-material prototypes and components, particularly in industries such as jewelry and dental.
E. Directed Energy Deposition
Directed Energy Deposition (DED) is a multi-material AM process that involves depositing material layer by layer, typically in the form of metal powder or wire, and melting it with a focused energy source, such as a laser or electron beam. DED is known for its ability to create large and complex structures with varying material compositions. This process is highly adaptable, making it suitable for applications in aerospace, where multi-material components with specific properties are often required.
F. Material Extrusion
Material extrusion, commonly associated with Fused Filament Fabrication (FFF), has been adapted for multi-material applications in MM-AM. This process involves extruding thermoplastic filaments layer by layer to build up a 3D object. By incorporating multiple extruders with different materials, Material Extrusion can create multi-material structures with diverse properties. This approach is cost-effective and suitable for applications where a combination of rigid and flexible materials is required.
G. Multi-Material AM Challenges and Considerations
Despite the transformative capabilities of Multi-Material Additive Manufacturing, challenges exist. Achieving optimal adhesion between different materials, managing material transitions during printing, and addressing the compatibility of dissimilar materials are ongoing considerations. Additionally, post-processing steps may be required to refine the final product, adding complexity to the overall fabrication process. As MM-AM technologies evolve, addressing these challenges will be essential to unlock the full potential of multi-material fabrication.
IV. Applications of Multi-Material AM
A. Aerospace and Aviation
Multi-Material Additive Manufacturing (MM-AM) has significantly impacted the aerospace and aviation industries by enabling the creation of lightweight, high-performance components. In aircraft design, where weight is critical, MM-AM allows for the integration of materials with different properties, optimizing structural integrity and reducing overall weight. Applications range from intricate engine components to complex internal structures, enhancing fuel efficiency and performance.
B. Automotive
The automotive industry has embraced MM-AM for its ability to create intricate and customized components. From producing lightweight yet strong chassis components to designing personalized interior features, MM-AM is revolutionizing automotive manufacturing. The versatility of multi-material printing allows for the incorporation of materials with varying mechanical properties, contributing to enhanced safety and performance.
C. Healthcare and Biotechnology
In healthcare and biotechnology, MM-AM is transforming the way medical devices and prosthetics are manufactured. Customized implants with varying material properties can be created to match the specific needs of individual patients. This personalized approach enhances the fit and functionality of implants, leading to improved patient outcomes. Additionally, multi-material printing is being explored in bioprinting for creating complex tissues and organs.
D. Consumer Products and Personalized manufacturing
Consumer products and personalized manufacturing benefit from MM-AM's capability to combine materials seamlessly. From personalized gadgets to custom-designed consumer goods, the ability to incorporate multiple materials enhances product functionality and aesthetics. Industries are leveraging MM-AM to offer unique, tailor-made products that cater to the individual preferences of consumers.
E. Architecture and Design
Architects and designers are leveraging MM-AM to push the boundaries of creativity in architecture and design. The ability to integrate multiple materials in a single print allows for the creation of structures with diverse properties. This includes customized building components, furniture, and interior design elements that showcase a level of intricacy and innovation not achievable through traditional manufacturing methods.
F. Education and Research
In the realm of education and research, MM-AM serves as a valuable tool for exploring new materials and design possibilities. Students and researchers can utilize multi-material printing to experiment with combinations that mimic real-world applications. This hands-on approach accelerates learning and fosters innovation in various fields, from materials science to engineering.
G. Sustainability and Circular Economy
MM-AM contributes to sustainability by allowing for efficient use of materials and reducing waste. The ability to create structures with varying densities and properties minimizes material usage, aligning with the principles of sustainable design. Additionally, the potential for recycling and reusing materials in multi-material prints supports the concept of a circular economy, where resources are utilized responsibly.
H. Defense and Security Applications
The defense and security sector benefits from MM-AM in the production of intricate and customized components for military applications. The ability to integrate multiple materials in a single print enables the creation of complex structures with enhanced functionalities. From lightweight and durable equipment to custom-designed components for defense systems, MM-AM is advancing capabilities in this critical sector.
In the final section, we'll reflect on the impact of Multi-Material Additive Manufacturing, summarizing key insights and providing resources for further exploration into this groundbreaking technology.
V. Case Studies of Multi-Material AM in Action
A. Breakthrough Innovations in the Aerospace Industry
In the aerospace industry, Multi-Material Additive Manufacturing (MM-AM) has led to breakthrough innovations. Companies like Airbus have utilized MM-AM to produce intricate components with a combination of lightweight and high-strength materials. For instance, the integration of composite materials with metal alloys in aircraft components has significantly reduced weight without compromising structural integrity. This breakthrough not only enhances fuel efficiency but also contributes to advancements in aerospace engineering.
B. Revolutionary Designs in the Automotive Industry
The automotive industry has witnessed revolutionary designs with the adoption of Multi-Material Additive Manufacturing. Companies such as Porsche and BMW have incorporated MM-AM to create complex and lightweight components. For example, the production of customized car interiors with a blend of rigid and flexible materials allows for enhanced comfort and aesthetics. These innovative designs showcase the potential of MM-AM to redefine the possibilities of automotive engineering.
C. Personalized Products and Customized Solutions in Consumer Markets
Consumer markets have experienced a wave of personalized products and customized solutions with the integration of Multi-Material Additive Manufacturing. Companies like Nike leverage MM-AM to create personalized footwear that combines various materials for optimal performance and comfort. This customization trend extends beyond fashion to consumer electronics, home goods, and beyond, demonstrating how MM-AM is reshaping the consumer experience.
D. Disruptive Applications in Healthcare and Biotechnology
Multi-Material Additive Manufacturing has introduced disruptive applications in healthcare and biotechnology. Medical companies, such as Medtronic, have embraced MM-AM to create patient-specific implants with a combination of biocompatible materials. This level of customization ensures a perfect fit and functionality, improving the quality of life for patients. Bioprinting is another area where MM-AM is making strides, enabling the fabrication of complex tissues and organs for transplantation.
E. The Role of Multi-Material AM in Sustainable Development and the Circular Economy
The sustainable impact of Multi-Material Additive Manufacturing is exemplified by companies like General Electric (GE). In the aerospace sector, GE utilizes MM-AM to produce components with optimized geometries, reducing material waste and fuel consumption. The ability to create intricate designs with lightweight structures aligns with sustainable development goals. Furthermore, the potential for recycling and reusing materials in multi-material prints supports the circular economy, promoting responsible resource utilization.
In conclusion, the case studies outlined above showcase the transformative impact of Multi-Material Additive Manufacturing across diverse industries. From breakthrough innovations in aerospace to revolutionary designs in automotive, and from personalized consumer products to disruptive applications in healthcare, MM-AM is at the forefront of driving innovation and pushing the boundaries of what is achievable in modern manufacturing. As we continue to explore and harness the potential of MM-AM, it is clear that this technology will play a central role in shaping the future of advanced manufacturing.