This guide provides an overview of the applications and materials used in Selective Laser Sintering (SLS) technology. It covers the principles of SLS, its various industrial and medical applications, and the materials that are suitable for this additive manufacturing process. The guide also includes information on the advantages and limitations of SLS, along with future trends and developments in the field.
I. Introduction to Selective Laser Sintering (SLS)
A. Principles of SLS
Selective Laser Sintering (SLS) stands at the forefront of additive manufacturing, utilizing a laser to sinter powdered materials into three-dimensional structures. Unlike traditional manufacturing methods, SLS does not require support structures during the build process, making it highly efficient and versatile.
The process begins with a bed of powdered material, commonly nylon or other polymers, which is selectively fused layer by layer using a high-powered laser. The laser sinters the powdered material, creating a solid cross-section of the desired object. This layer-by-layer approach allows for the production of intricate and complex geometries with remarkable precision.
B. Evolution of SLS Technology
Since its inception, SLS technology has evolved significantly. Originally developed for rapid prototyping, it has expanded its capabilities to become a vital tool in various industries. Advancements in laser technology, powder materials, and software have contributed to the widespread adoption of SLS for both prototyping and end-use part production.
II. Applications of SLS
A. Industrial Applications
Complex Part Manufacturing
SLS has revolutionized complex part manufacturing by offering a unique advantage in producing intricate geometries that would be challenging with traditional methods. Industries such as aerospace and automotive benefit from SLS technology, enabling the creation of lightweight and high-strength components that meet the stringent demands of modern engineering.
Rapid Prototyping
In the realm of product development, SLS plays a pivotal role in rapid prototyping. Designers and engineers can quickly iterate and test their ideas, accelerating the product development cycle. The ability to create functional prototypes with complex geometries ensures that the prototypes closely resemble the final product, facilitating more accurate testing and validation.
Direct Digital Manufacturing
SLS has transcended its initial role as a prototyping tool to become a key player in direct digital manufacturing. The technology allows for the production of end-use parts directly from digital files, eliminating the need for molds or tooling. This shift towards on-demand manufacturing contributes to reduced lead times and increased flexibility in production processes.
B. Medical Applications
Customized Implants and Prosthetics
SLS has found a significant niche in the medical field, particularly in the production of customized implants and prosthetics. The technology's ability to work with a variety of biocompatible materials, such as medical-grade nylon, enables the creation of patient-specific implants that match individual anatomies. This customization enhances the overall effectiveness and comfort of medical implants.
Tissue Engineering and Regenerative Medicine
In the realm of tissue engineering, SLS plays a crucial role in fabricating scaffolds for cell growth. The precision of the SLS process allows for the creation of intricate structures that support tissue regeneration. This application holds immense promise for regenerative medicine, offering solutions for repairing and replacing damaged tissues and organs.
Drug Delivery Systems
SLS technology has also been employed in the creation of personalized drug delivery systems. By leveraging its precision and the ability to work with various materials, SLS enables the production of controlled-release drug formulations. This customization allows for tailoring drug delivery systems to meet specific patient needs, optimizing treatment outcomes.
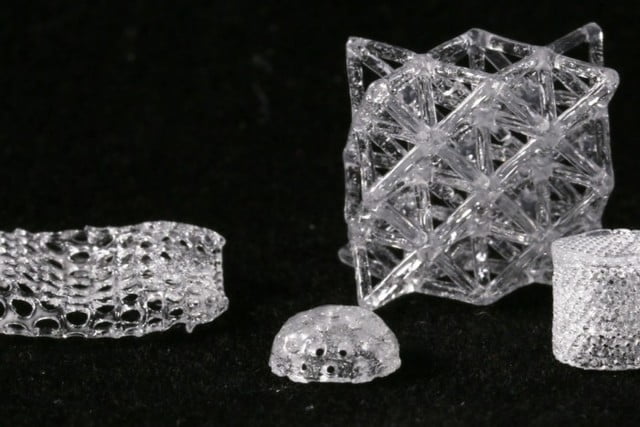
III. Materials for SLS
A. Polymers
ABS
Acrylonitrile Butadiene Styrene (ABS) is a thermoplastic polymer commonly used in SLS. Known for its durability and impact resistance, ABS is suitable for a wide range of applications, including prototyping and functional end-use parts.
Nylon
Nylon, a popular choice for SLS, offers excellent strength and flexibility. Its ability to produce parts with high precision and durability makes it suitable for various industrial applications, from automotive components to consumer goods.
Polyetherimide (PEI)
Polyetherimide (PEI) is a high-performance thermoplastic with exceptional thermal and chemical resistance. SLS using PEI is well-suited for applications where parts need to withstand harsh environmental conditions, making it a preferred choice in aerospace and medical industries.
B. Metals
Steel
SLS has extended its reach beyond polymers to include metals like steel. Steel SLS provides a cost-effective solution for producing metal parts with complex geometries, making it valuable in industries where strength and durability are paramount.
Titanium
Titanium, renowned for its lightweight and high strength, is a notable metal used in SLS. This material finds applications in aerospace, medical, and automotive sectors, where the combination of strength and reduced weight is critical.
Cobalt Chrome
Cobalt Chrome alloys, known for their biocompatibility and resistance to corrosion, are used in SLS for medical implants and aerospace components. The ability to produce intricate parts with this metal alloy adds to the versatility of SLS technology.
C. Ceramics
Glass
Glass ceramics, employed in SLS, offer a unique blend of transparency and strength. This material finds applications in industries where optical clarity and mechanical robustness are essential, such as in creating lenses or specialized components.
Zirconia
Zirconia, a ceramic material with high strength and biocompatibility, is utilized in SLS for dental applications and medical implants. Its ability to withstand extreme conditions makes it suitable for precision components.
Alumina
Alumina, known for its high thermal and electrical insulation properties, is used in SLS for applications where these characteristics are crucial. Its application spans from electronics to specialized components in industrial settings.
IV. Advantages and Limitations of SLS
A. Advantages
Highly Versatile Process
SLS stands out for its versatility, accommodating a wide range of materials and producing parts with intricate geometries. The process allows for the creation of complex and functional prototypes or end-use parts with minimal design constraints.
Ability to Produce Complex Parts
The layer-by-layer approach of SLS facilitates the production of highly intricate parts that would be challenging or impossible with traditional manufacturing methods. This capability is particularly advantageous in industries where complex geometries are essential.
Customizable Outputs
SLS offers a high degree of customization, allowing manufacturers to tailor parts according to specific requirements. This customization extends to material selection, enabling the creation of parts with varied mechanical properties to meet diverse application needs.
B. Limitations
Material Costs
While SLS provides a wide range of material options, some specialized materials can be expensive. This can impact the overall cost of production, especially for large or complex projects that require unique materials.
Post-Processing Requirements
SLS parts often require post-processing to achieve desired surface finishes or meet specific tolerances. This additional step in the manufacturing process may add time and cost, influencing the overall efficiency of the SLS technology.
Limited Application for Some Materials
While SLS accommodates various materials, the technology might not be equally suitable for every material. Some materials may have limitations in terms of mechanical properties, thermal resistance, or other factors, restricting their applicability in certain industries or applications.
V. Future Trends and Developments in SLS
A. Innovations in Materials and Processes
Advanced Polymers
The future of Selective Laser Sintering (SLS) holds exciting prospects for the development of advanced polymers. Researchers and engineers are actively exploring novel polymer blends with enhanced properties, such as increased strength, flexibility, and thermal resistance. These innovations aim to expand the range of applications for SLS, making it an even more versatile solution for various industries.
Metal Matrix Composites
As the demand for metal parts with superior mechanical properties grows, the SLS landscape is expected to witness the introduction of metal matrix composites. These composites, combining metals with reinforcing elements, promise to offer enhanced strength and lightweight characteristics. The integration of such materials into SLS processes could open new avenues for applications in aerospace, automotive, and other high-performance industries.
Sustainable Materials
With a global focus on sustainability, the future of SLS includes a shift towards the use of eco-friendly and recyclable materials. Researchers are exploring sustainable alternatives for both polymer and metal SLS applications. This development aligns with the broader movement towards environmentally conscious manufacturing practices, addressing concerns about material waste and ecological impact.
B. Enhanced Applications in Industry and Medicine
Industry 4.0 Integration
The fourth industrial revolution, often referred to as Industry 4.0, emphasizes the integration of digital technologies into manufacturing processes. In the context of SLS, this entails further advancements in software, connectivity, and automation. Real-time monitoring, predictive maintenance, and data-driven optimization are expected to become integral parts of SLS systems, enhancing efficiency and reducing production costs.
Biocompatible Materials for Medical Applications
The medical field will witness a surge in the use of biocompatible materials in SLS. Ongoing research aims to develop materials that not only meet the stringent requirements for medical devices but also encourage seamless integration with the human body. SLS is poised to play a vital role in producing customized, patient-specific implants and medical devices, contributing to advancements in personalized medicine.
Pharmaceutical Applications
In the pharmaceutical industry, SLS is anticipated to find new applications in the development of drug delivery systems. The precision of SLS technology allows for the fabrication of intricate structures, enabling the controlled release of pharmaceutical compounds. This could lead to the creation of more efficient and patient-specific drug delivery solutions.
Conclusion
The future of Selective Laser Sintering (SLS) holds tremendous promise, driven by ongoing innovations in materials and processes. As advanced polymers, metal matrix composites, and sustainable materials become integral to SLS, the technology will continue to evolve and diversify its applications. The integration of Industry 4.0 principles will further enhance efficiency, while the medical and pharmaceutical sectors will benefit from tailor-made solutions for patient-specific needs. The trajectory of SLS points towards a future where additive manufacturing plays an increasingly pivotal role in reshaping industries and advancing technological frontiers.