Table of Contents:
- Introduction
- Properties of Aluminum Injection Molds
- Advantages of Aluminum Injection Molds
- Applications of Aluminum Injection Molds
- Design Considerations for Aluminum Injection Molds
- Maintenance and Repair of Aluminum Injection Molds
- Conclusion
-
1.Introduction
Injection molding is a widely used manufacturing process in which melted plastic or metal is injected into a mold to form a desired shape. Aluminum injection molding, also known as aluminum die casting, refers to the process of injecting aluminum alloys into molds to make complex and precise-shaped components.
The history of aluminum injection molding dates back to the 1830s, when the first metal casting machine was developed in China. From there, the process has continued to evolve, and aluminum injection molds are now widely used in various industries, including automotive, aerospace, consumer products, medical, and electronics.
This article provides an overview of the properties, advantages, applications, design considerations, and maintenance of aluminum injection molds.
-
2.Properties of Aluminum Injection Molds
Aluminum injection molds have several properties that make them suitable for various manufacturing applications. Some of the essential properties of aluminum injection molds include:
- High Thermal Conductivity: Aluminum injection molds possess excellent thermal conductivity, allowing for high heat exchange rates between the mold and the melted metal being injected. As a result, the manufacturing process becomes more efficient and requires less cooling time.
- High Strength-to-Weight Ratio: Aluminum injection molds are lightweight yet highly durable, so they can withstand high force and pressure. The high strength-to-weight ratio of aluminum results in the production of high-quality components.
- Excellent Corrosion Resistance: Aluminum injection molds have a high resistance to corrosion and rust, making them ideal for use in wet and humid conditions.
- High Durability and Longevity: Aluminum injection molds can generally withstand high stress and temperature variations without cracking or warping, this feature contributes to the molds’ long lifespan, offering a significant cost-benefit over time.
- Good Surface Finish: Aluminum injection molds have smooth finishes, which result in high-quality finished products produced with higher accuracy and reliability.
Overall, the properties of aluminum injection molds make them highly desirable for numerous manufacturing industries, primarily due to their high strength, durability, corrosion resistance, and good surface finish.
-
3.Advantages of Aluminum Injection Molds
Aluminum injection molds offer several advantages over other mold materials, such as plastic or steel. Some of the key advantages of aluminum injection molds are:
- Reduced Cycle Time: Aluminum injection molds have excellent thermal conductivity, allowing for faster cooling times during the manufacturing process. As a result, there is a reduced cycle time, meaning that the production process is faster, and production costs are lower.
- Cost-Effective: Aluminum injection molds are generally less expensive compared to other mold materials, reducing the overall production cost.
- Reduced Weight and Improved Efficiency: Aluminum injection molds have a higher strength-to-weight ratio than other mold materials. This feature makes them lightweight, and the process of manufacturing with lightweight molds can reduce energy consumption while operating the machinery.
- Improved Productivity: Aluminum injection molds can produce high volumes of parts with consistent quality and accuracy, resulting in improved production efficiency.
- Customization and Complexity: Aluminum injection molds can accurately replicate complex and intricate features, giving designers the freedom to create unique and customized components. Complex geometries are achievable through utilization of Aluminum injection molds, yielding products with precise tolerance and a uniform quality.
Overall, Aluminum injection molds have several advantages, characterized by their cost-effectiveness, reduce production time, produce high-quality finished products, and enabling the creation of intricate designs. The unique advantages make aluminum injection molds a popular choice in several industries.
-
4.Applications of Aluminum Injection Molds
The adaptability of aluminum injection molds across various manufacturing industries has made them popular for different applications. Below are examples of industries where aluminum injection molds are commonly used:
- Automotive Industry: Aluminum injection molds are widely used in the automotive industry to create lightweight and robust components, such as engine blocks, powertrains, suspensions, and transmission cases.
- Aerospace Industry: The aerospace industry also benefits from aluminum injection molds, which are used to produce precision components for airplanes and spacecraft, such as engine parts, turbines, and structural frames.
- Consumer Products Industry: Aluminum injection molds can be used to manufacture high-quality consumer goods, including mobile phones, computers, and home appliances.
- Medical Industry: Aluminum injection molds are popular in the medical field due to the production of precision and accurate components. Medical devices such as x-ray equipment, diagnostic devices and prosthetic limbs are made with assistance from aluminum die casting.
- Electronics Industry: Aluminum injection molds are widely used in electronic parts manufacturing to produce high-precision and complex components required in electronic devices such as computers, tablets, and smartphones.
Aluminum injection molds have a diverse range of applications and are capable of producing quality parts and components used in everyday life.
If you need about Injection Mold Services,You can click on the V1 Prototype website to find it.
-
5.Design Considerations for Aluminum Injection Molds
The design of an aluminum injection mold depends on various factors, some of which are highlighted below:
- Component Size and Geometry: The size and geometry of the desired component dictate the size, shape, and design of the mold. Complex geometries and intricate features may require a more complex mold design.
- Production Volume: The production volume affects the mold design, with high volume productions favoring simpler and more durable molds, while lower volume productions favor complex parts with intricate designs.
- Material Selection: The choice of material used for the mold has an impact on the mold design, with some materials better suited for specific applications based on required product accuracy, compounding speed, mold durability and thermal conductivity.
- Manufacturing Process: The type of aluminum injection molding process employed influences the mold design.
.
It is important to consider these factors in the design of an aluminum injection mold to achieve optimal performance. Meanwhile, some design guidelines also enhance optimal performance; listed below:
- Taper Design: To ensure easy removal of the product from the mold cavity, the mold should incorporate tapered or draft angles ranging from 0.5 to 2 degrees.
- Gate Design: The mold must have sufficient gating to allow for metal flow and removal of unwanted gases during casting, to ensure a quality part.
- Surface Finish: The mold surface must have an appropriate surface finish to ensure a quality casting, with guidelines ranging from sub-micron surface finish to mirror finish for specific applications.
- Cooling System Design: The location and amount of cooling system channels should be optimized to ensure faster heat transfer, improving cooling time of the mould and adequate part quality, such as porosity and mechanical strength.
Overall, the considerations mentioned, and guidelines provided promote optimal performance and production of high-quality products in aluminum injection molding.
-
6.Maintenance and Repair of Aluminum Injection Molds
Maintenance and repair of aluminum injection molds is crucial for optimal performance and longevity. Best practices for maintenance and care of aluminum injection molds include:
- Regular Cleaning: The mold must be kept clean, and the surface free of foreign materials that can affect the quality of the finished products.
- Lubrication: The mold needs to be lubricated with high-temperature lubricants to reduce friction and wear that may arise from prolonged use.
- Inspection: Regular visual examinations of the mold are essential to identify signs of wear, cracks, or other defects.
- Storage: Molds that are not in use should be stored in a dry, cool, and controlled environment to prevent rust, dust, and scratches.
.
Common repairs and techniques for aluminum injection molds may include the following:
- Welding: Welding is an effective technique to repair aluminum injection molds that have cracked or become damaged. Repairs may include patching and reinforcing damaged areas to restore the mold’s structural integrity.
- Polishing: Polishing helps to remove any surface imperfections, scratches or pits that may occur over time on the mold surfaces. This repair method is essential in molds that produce high-quality finishes and require precision tolerances.
- Refurbishing: Refurbishment entails repairing or replacing elements of the mold that have sustained excessive wear, and damage, to restore the mold to its original shape, size, and accuracy.
- Heat Treating: Heat-treating allows the restoration of the metal’s mechanical properties, where structural changes due to heat, impact, and natural aging can be reversed, inducing the mold restoration to improve its performance.
Overall, proper maintenance and repair of aluminum injection molds ensure optimal performance, produce high-quality finished parts, promote safety, and provide a return on investment in mold life.
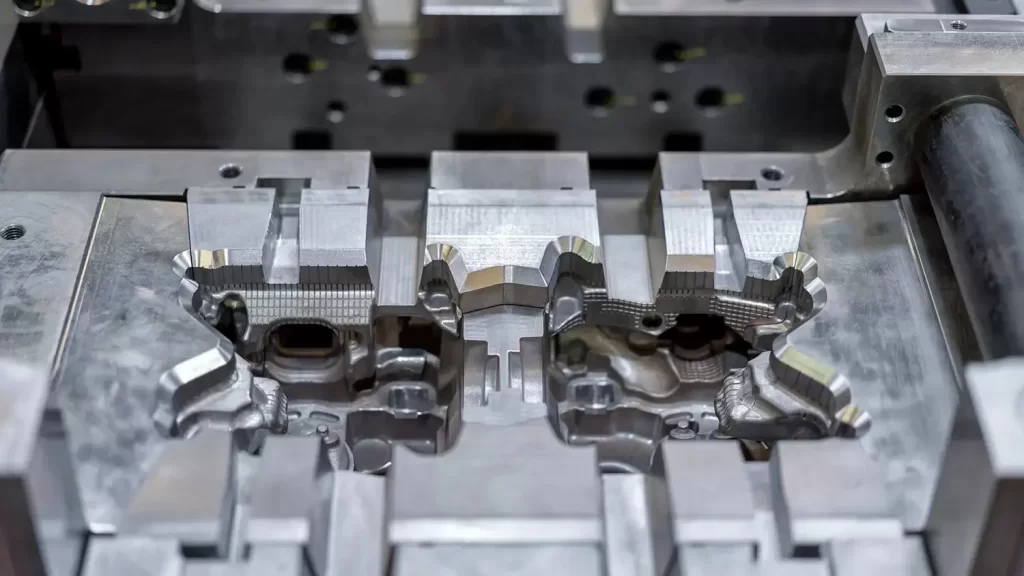
-
7.Conclusion
Aluminum injection molding has become a widely used manufacturing process in various industries due to its properties, advantages, and applications. Some key points highlighted in this article include:
- Aluminum injection molds have excellent thermal conductivity, high strength-to-weight ratio, corrosion resistance, durability, and good surface finish.
- The advantages of aluminum injection molds include reduced cycle time, cost-effectiveness, reduced weight, improved efficiency, improved productivity, and customization.
- Aluminum injection molds are used in the automotive, aerospace, consumer products, medical, and electronics industries.
- Design considerations for aluminum injection molds include component size and geometry, production volume, material selection, and manufacturing process.
- Maintenance and repair of aluminum injection molds involve regular cleaning, inspection, lubrication, and storage. Repair techniques include welding, polishing, refurbishing, and heat treating.
Future outlook and innovations in aluminum injection molding include the application of additive manufacturing, such as 3D printing, the development of hybrid materials by incorporating various materials in aluminum die casting, and the use of artificial intelligence to optimize mold design and manufacturing processes.
In conclusion, aluminum injection molds offer several benefits and versatility for manufacturers, enabling them to produce high-quality and precise components. Proper maintenance, repair, and innovation within the aluminum injection molding industry, suggests that the use of aluminum molds will continue to grow in popularity across a variety of industries.