This guide delves into the world of 3D printing, exploring its potential and revolutionary impact on various industries. You'll learn about the technology's capabilities, limitations, and future trends, as well as discover innovative applications in fields such as healthcare, manufacturing, and design. With this comprehensive guide, you'll unlock the full potential of 3D printing and use it to create groundbreaking solutions.
I. Introduction to 3D Printing
A. What is 3D Printing?
3D printing, also known as additive manufacturing, is a groundbreaking technology that transforms digital designs into physical objects by layering materials. This additive process allows for the creation of intricate and complex structures, offering unprecedented flexibility in manufacturing.
B. Evolution of 3D Printing Technology
The journey of 3D printing began in the 1980s with the invention of stereolithography (SLA). Since then, the technology has evolved significantly, introducing various techniques like Fused Deposition Modeling (FDM), Selective Laser Sintering (SLS), and more. These advancements have democratized manufacturing, enabling rapid prototyping, customization, and even end-use production.
C. Principles of 3D Printing
At its core, 3D printing relies on layer-by-layer construction from digital models. The process involves three key steps: digital design, slicing the model into layers, and the physical layering of materials. This revolutionary approach allows for precise and intricate creations that would be impractical or impossible with traditional manufacturing methods.
II. Capabilities and Limitations of 3D Printing
A. Types of 3D Printing Processes
Fused Deposition Modeling (FDM)
FDM is widely used for its simplicity and versatility, making it accessible to hobbyists and professionals alike. It involves extruding thermoplastic filaments layer by layer, creating robust and functional prints.
Stereolithography (SLA)
SLA employs a laser to solidify liquid resin, resulting in highly detailed and accurate prints. This technology excels in producing intricate designs with smooth surfaces.
Selective Laser Sintering (SLS)
SLS uses a laser to fuse powdered materials, offering the capability to print with a variety of materials, including plastics and metals. It is renowned for creating strong and durable objects.
B. Materials for 3D Printing
A wide array of materials can be used in 3D printing, ranging from polymers like PLA and ABS to metals such as titanium and aluminum. The material selection influences the properties of the final print, catering to different applications and industries.
C. Applications of 3D Printing
Rapid Prototyping
3D printing is a go-to solution for rapid prototyping, allowing designers to quickly iterate and test their ideas before moving into full-scale production.
Customization in Healthcare
In the healthcare sector, 3D printing enables the production of customized implants, prosthetics, and even patient-specific anatomical models for surgical planning.
Aerospace and Automotive Components
The aerospace and automotive industries leverage 3D printing to create lightweight yet robust components, reducing overall weight and improving fuel efficiency.
Complex Architectural Designs
Architects and designers utilize 3D printing to bring complex architectural designs to life, exploring shapes and structures previously considered unattainable.
D. Challenges and Limitations of 3D Printing
Speed and Scalability
While 3D printing offers unparalleled design freedom, the speed of the process remains a challenge, particularly for large-scale production. Scaling up for mass manufacturing can be time-consuming.
Material Limitations
Certain materials used in 3D printing may lack the properties required for specific applications, limiting the technology's scope in industries with stringent material requirements.
Post-Processing Requirements
Many 3D prints require post-processing to achieve a polished finish, adding extra steps and time to the overall production process.
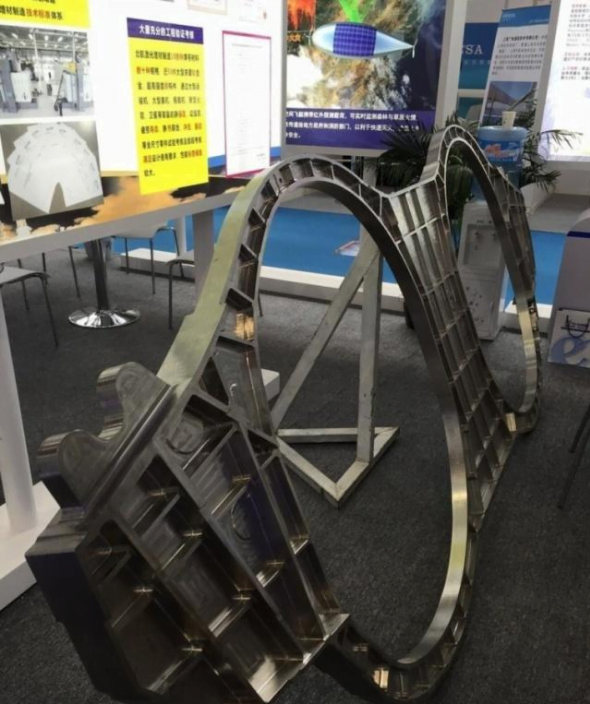
III. Innovative Applications of 3D Printing
A. Healthcare Applications
Patient-Specific Implants
3D printing has revolutionized healthcare by enabling the production of patient-specific implants, ensuring a perfect fit and enhancing patient outcomes.
Bioprinting
Researchers are exploring bioprinting to create living tissues and organs, opening new possibilities in regenerative medicine and organ transplantation.
B. Manufacturing and Production
Rapid Tooling
3D printing facilitates the rapid production of tooling for manufacturing processes, reducing lead times and costs associated with traditional tooling methods.
On-Demand Production
The ability to print on demand allows for more flexible and efficient manufacturing processes, minimizing waste and storage needs.
C. Architecture and Design
Prototyping Architectural Models
Architects use 3D printing to create detailed and accurate architectural models, providing a tangible representation of their designs.
Custom Furniture and Decor
Designers and artists leverage 3D printing to craft unique furniture and decorative pieces that push the boundaries of traditional design.
D. Consumer Products and Gifts
Customized Consumer Goods
Consumers can now personalize everyday items such as phone cases, jewelry, and home decor, thanks to 3D printing.
Personalized Gifts
The technology enables the creation of one-of-a-kind gifts, fostering a culture of unique and thoughtful present-giving.
E. Education and Research
Hands-On Learning
Educational institutions use 3D printing to enhance hands-on learning experiences, allowing students to materialize their ideas and concepts.
Research Prototyping
In research, 3D printing aids in the rapid prototyping of experimental setups, accelerating the pace of scientific discovery.
IV. Future Trends in 3D Printing
A. Advancements in Materials and Technologies
Smart Materials
The development of smart materials, capable of responding to external stimuli, opens new possibilities for dynamic and adaptive 3D-printed structures.
4D Printing
The evolution into 4D printing involves the integration of time as a variable, allowing printed objects to transform or self-assemble over time.
B. Increased Adoption Across Industries
Mainstream Adoption
As technology matures, 3D printing is expected to witness increased adoption across diverse industries, becoming a standard part of manufacturing processes.
Integration in Supply Chains
The integration of 3D printing into traditional supply chains is anticipated, offering more flexibility and responsiveness to market demands.
C. Impact on Global Markets and Economy
Decentralized Production
3D printing's potential to decentralize production may impact global supply chains, redistributing manufacturing capabilities and influencing global economic structures.
Job Evolution
While some traditional manufacturing jobs may be impacted, the rise of 3D printing is likely to create new opportunities in design, materials development, and technology maintenance.
D. Role of 3D Printing in Sustainable Development
Reduced Waste
The ability to print on demand and customize products contributes to a reduction in waste, aligning with sustainable manufacturing practices.
Localized Production
3D printing's potential for localized production can minimize the environmental impact associated with global shipping and transportation.
V. Conclusion
A. Summary of Key Learnings
In summary, 3D printing has transformed from a niche technology into a powerful tool with wide-ranging applications across industries. From healthcare to consumer products, its impact on manufacturing, design, and innovation is undeniable. While challenges exist, ongoing advancements and innovations in materials and technologies promise a future where 3D printing becomes an integral part of global production and sustainable development.
B. Resources for Further Exploration
To delve deeper into the world of 3D printing, explore online resources, attend conferences, and engage with communities. Platforms like industry forums, educational websites, and manufacturer documentation provide valuable insights, troubleshooting tips, and continuous learning opportunities. Embracing a curious and proactive approach ensures you stay abreast of the latest developments in this dynamic field, empowering you to unleash the full potential of 3D printing technology.