5 Axis CNC Machining Services
Our 5 Axis CNC Machining services allow for bespoke parts with extreme multi-axis complexity to be machined on time and to budget.
5 Axis CNC Machining Parts
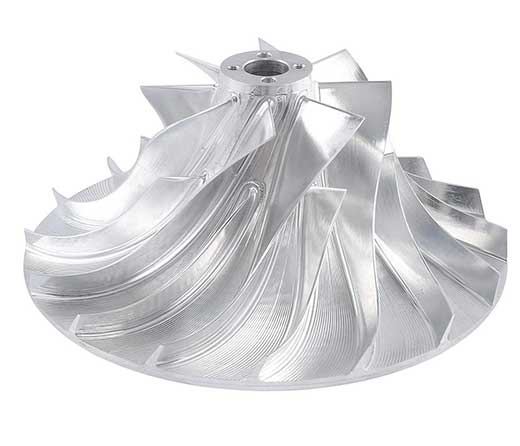
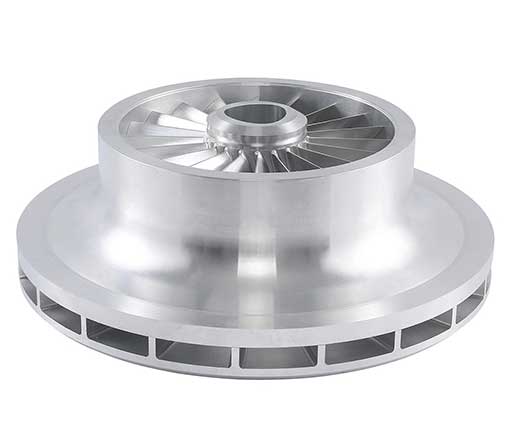
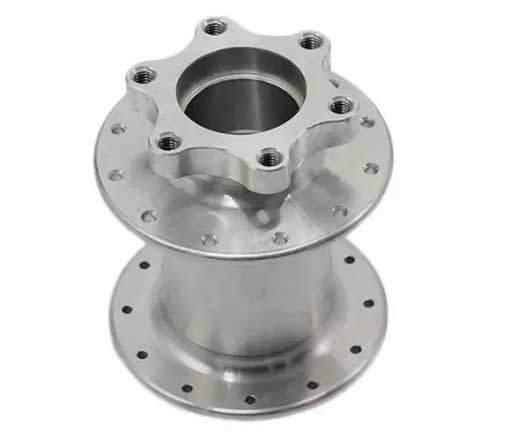
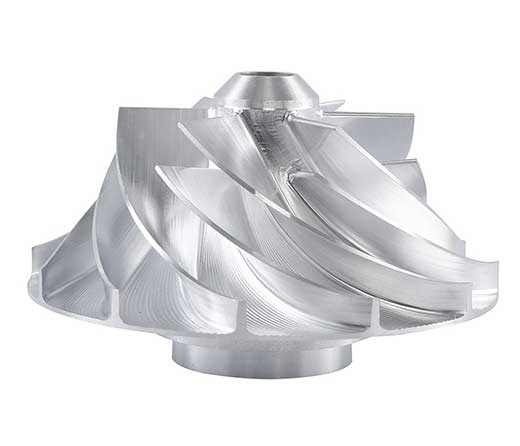
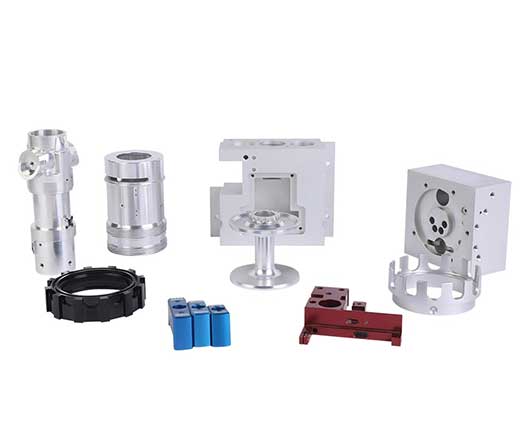
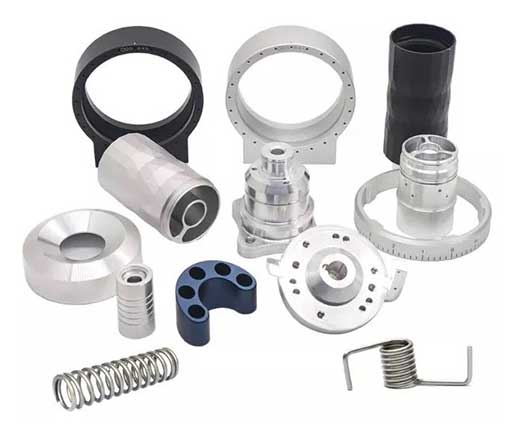
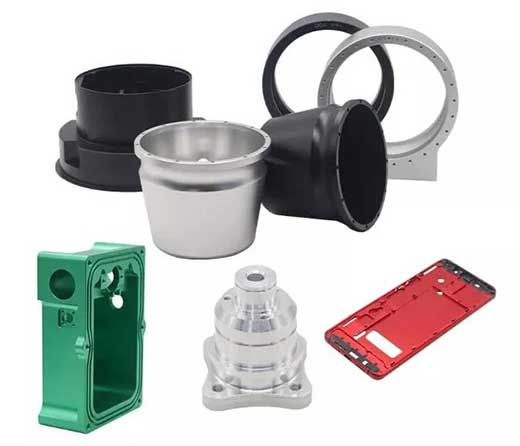
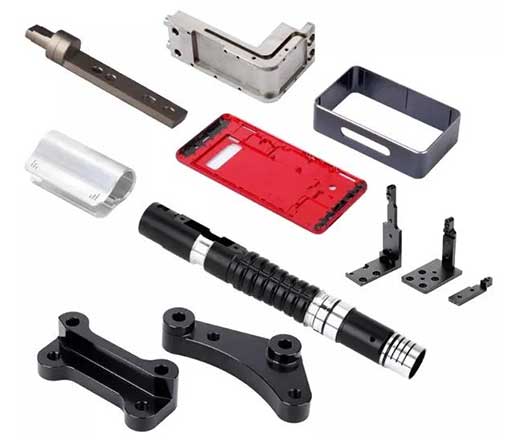
5 Axis CNC Machining Services
5 Axis CNC Machining is a subtractive process that cuts away at a block of material using a high-speed cutting tool that resembles a drill. Typical 3 Axis CNC Machines are constrained to linear X, Y and Z axes. However, 5 Axis CNC Machining introduces two additional axes; rotation on the X and Y axes (known as A & B axes). The new axes allow the cutting tool to access more areas of the workpieces at a variety of angles.
5 Axis CNC Machining has opened the possibility for parts to be ‘Done in One’, reducing setup and reorientation costs. With intelligent programming, data paths are trialled and tool paths are perfected in advance of production, achieving efficiency and accuracy.
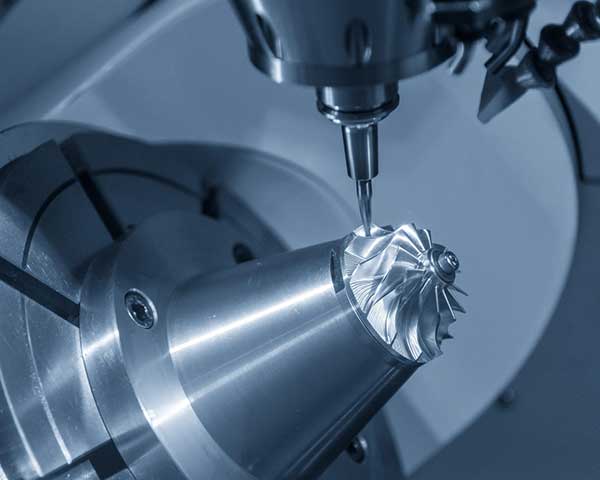
Materials for 5 Axis CNC Machining
Advanced CNC machinery within a bank of trusted partners enables us to produce exactly what you need, when you need it. CAM (Computer Aided Manufacturing) has opened the doors to endless possibilities.
Al6061
Al6063
Al6082
Al7075 (Aerospace Grade)
Al5086 (Marine Grade)
Al5754 (H22)
1045 (EN8 / C45)
EN24
EN19
303
304
306
316
Duplex 2205
Titanium Ti-6Al-4V (TC4)
Titanium TA2
Brass C510, C544
Brass CZ121, CZ112 / CW712R
Alloy Steel 4340
Copper C101, C172
Copper C14500 / CW118C
Nickel Inconel 625, 718
ABS
PP
POM-M
POM-C
HDPE
PEEK
PPS
PPSU
5 Axis CNC Machining Processing capacity
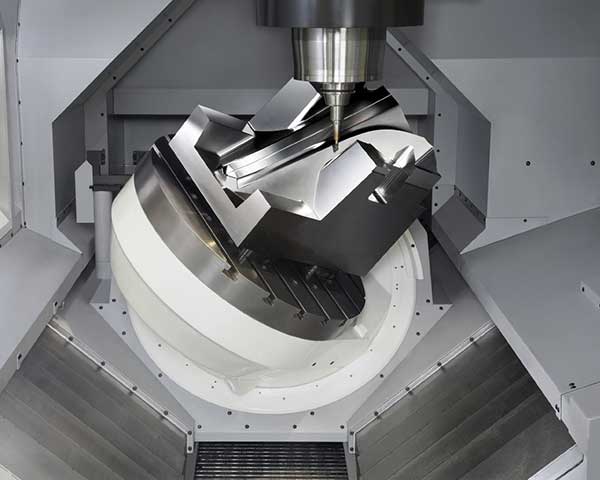
Why choose V1 5 Axis CNC Machined Parts?
Combined with our rapid response rate and excellent customer service, our clients value our experience and approach for their precision manufacturing needs. With dependable 5 Axis machining services, V1 can help you carry your project forward, with the capability for a vast amount of bespoke manufacturing projects and machining needs.
V1 is ISO 9001 certified. This certification recognises our attention towards delivering high-quality parts and we continually strive to improve our services to make your experience as straightforward as possible.
5 Axis CNC Parts are often bespoke, intricate and complex parts. With over 9 years of experience in delivering project-critical, precision machined parts for a wide range of industries, you can trust V1 to deliver.
5 Axis CNC Machining Manufacturing FAQs
5-axis CNC machining is a machining method that uses 5 coordinate axes to control the movement of the tool, allowing the tool to move in more directions to achieve more complex shapes and curves.
Five-axis CNC machining is a very advanced manufacturing technology that works with a variety of different types of materials. These materials include, but are not limited to, metals, plastics, and composite materials. The flexibility and precision of this machining method make it widely used in many different industrial fields. Whether for parts that require high precision and complex shapes, or for parts that require mass production, five-axis CNC machining provides an excellent solution. In addition, due to its ability to handle multiple types of materials, five-axis CNC machining also provides manufacturers with greater design freedom, allowing them to create more unique and innovative products.
Five-axis CNC machining technology can achieve more complex and curvaceous shapes with greater accuracy and efficiency. This technology can complete the processing of multiple surfaces in one clamping, thereby reducing the time of tool changing and positioning, thereby improving production efficiency.
Five-axis CNC machining technology is an advanced manufacturing process that uses five programmable axes to achieve precise control of the workpiece. Compared with traditional three-axis machining, five-axis machining has higher flexibility and adaptability, and can handle more complex geometric shapes and curves. This makes it widely used in aviation, automobile, mold manufacturing and other fields.
One of the advantages of five-axis CNC machining technology is the ability to process polyhedrons in one go. Traditional three-axis machining requires multiple clamping and positioning, while five-axis machining can complete the processing of multiple surfaces in one clamping, greatly shortening the production cycle. This not only improves production efficiency, but also reduces production costs.
In addition, five-axis CNC machining technology can also reduce the time of tool replacement and positioning. In traditional three-axis machining, when different surfaces need to be processed, tools need to be frequently changed and repositioned. Five-axis machining can integrate the processing paths of multiple surfaces through pre-programming, reducing the number of tool changes and positioning, thereby improving production efficiency.
In addition, the precision of five-axis CNC machining technology is also higher. Thanks to the use of advanced control systems and precision measuring equipment, five-axis machining can achieve micron-level precision control to ensure the quality and consistency of workpieces. This is particularly important for parts with high precision requirements, such as engine parts in the aerospace field.
To sum up, five-axis CNC machining technology has become an indispensable and important tool in modern manufacturing with its more complex shape and curve processing capabilities, higher accuracy and efficiency, and less tool replacement and positioning time. . Its application not only improves production efficiency, but also brings more innovation and development opportunities to the manufacturing industry.
Five-axis CNC machining technology is an advanced manufacturing process that can produce a variety of different types of products. These products include, but are not limited to, automotive parts, aerospace parts, tools and molds, medical equipment, and more. The emergence of this technology has greatly improved production efficiency and product quality, allowing manufacturers to meet market demand more flexibly.
First, five-axis CNC machining technology plays an important role in the automobile manufacturing industry. Through this technology, manufacturers can produce extremely precise automotive parts, such as engine parts, braking systems, suspension systems, etc. The accuracy of these parts directly affects the performance and safety of the car, so it is crucial for car manufacturers to adopt five-axis CNC machining technology.
Secondly, five-axis CNC machining technology is also widely used in the aerospace field. Aerospace parts often have complex shapes and high-precision requirements, and five-axis CNC machining technology can meet these needs. Through this technology, manufacturers can produce aerospace engine parts, spacecraft structural parts, avionics and other key components, providing strong support for the development of the aerospace industry.
In addition, five-axis CNC machining technology also has important applications in the field of tool and mold manufacturing. Tools and molds are the foundation of manufacturing, and their quality and precision are directly related to product quality and production efficiency. Through five-axis CNC machining technology, manufacturers can produce high-precision tools and molds, improve product manufacturing efficiency and quality, and reduce production costs.
Finally, five-axis CNC machining technology is also widely used in the medical field. The accuracy and reliability of medical equipment are critical to patient health. Through this technology, manufacturers can produce high-precision medical equipment, such as surgical instruments, imaging equipment, etc., providing strong support for the development of the medical industry.
To sum up, five-axis CNC machining technology is a very powerful manufacturing process that can produce a variety of different types of products, including automotive parts, aerospace parts, tools and molds, medical equipment, and more. The application of this technology not only improves production efficiency and product quality, but also provides strong support for the development of all walks of life.
Five-axis CNC machining technology can achieve very high machining accuracy, usually reaching an accuracy of 0.001 mm. This advanced processing method has broad application prospects in the manufacturing industry because it can provide very precise processing results to meet the manufacturing needs of various complex parts.
The core of five-axis CNC machining technology is the use of five programmable axes to control the movement of the machine tool. The five axes include three linear axes and two rotary axes, which can coordinate movements simultaneously to achieve complex geometries and surface machining. Compared with traditional three-axis CNC machining, five-axis CNC machining has higher flexibility and precision.
With five-axis CNC machining, very fine machining operations can be achieved. Normally, its processing accuracy can reach the level of 0.001 mm, which means that the size and shape of parts can be precisely controlled to the micron level. This is very important for many application fields with high precision requirements, such as aerospace, medical equipment and precision instruments.
Five-axis CNC machining technology has a wide range of applications. It can be used to process a variety of materials, including metals, plastics, ceramics, and more. Whether it is simple plane processing or complex curved surface processing, five-axis CNC machining is capable of it. In addition, it can also be used for drilling, milling, turning and other processing techniques to meet the needs of different industries.
However, it is not easy to achieve such high machining accuracy. Five-axis CNC machining requires the use of advanced control systems and high-performance machine tools. At the same time, operators also need to have rich experience and skills to ensure the stability and accuracy of the processing process. Therefore, five-axis CNC machining technology needs to fully consider costs and benefits during implementation to fully realize its potential.
In short, five-axis CNC machining technology is a very advanced machining method that can achieve very high machining accuracy. It has broad application prospects and can play an important role in various industries. With the continuous development and maturity of technology, it is believed that five-axis CNC machining technology will be more widely used and promoted in the future.
Five-axis CNC machining can typically use up to 200 tools simultaneously, including different types of milling cutters, drills, thread cutters, turning tools, etc. This advanced processing technology enables multiple processes to be completed in one operation, greatly improving production efficiency and product quality.
First of all, the five-axis CNC machining system is highly flexible and adaptable, and can select appropriate tools according to different processing needs. Whether it is plane milling, curved surface machining or complex three-dimensional engraving, it can be achieved by adjusting the type and parameters of the tool. This variety of tool selection enables five-axis CNC machining to cope with various complex machining tasks and meet the needs of different industries.
Secondly, the five-axis CNC machining system has high precision and stability. Through precise control algorithms and advanced servo control systems, micron-level machining accuracy and stable cutting processes can be achieved. This is particularly important for the processing of some precision parts, such as complex parts in the aerospace field, medical equipment, etc. The high stability and high precision of five-axis CNC machining ensure the quality of the product and reduce subsequent trimming and debugging work.
In addition, five-axis CNC machining also has the characteristics of high efficiency and automation. Through optimized tool path planning and efficient cutting parameter settings, machining time and energy consumption can be minimized. At the same time, the five-axis CNC machining system can also be seamlessly integrated with automated equipment and production lines to achieve unmanned or semi-unmanned production. This not only improves production efficiency, but also reduces labor costs and labor intensity.
To sum up, five-axis CNC machining, as an advanced manufacturing technology, has many advantages. It can use up to 200 tools at the same time, including different types of milling cutters, drill bits, thread cutters, turning tools, etc., meeting the processing needs of different industries. Its high precision, high stability, high efficiency and automation characteristics make five-axis CNC machining an important tool in modern manufacturing, making an important contribution to improving production efficiency and product quality.
The speed of five-axis CNC machining mainly depends on the hardness and complexity of the material being processed. This type of processing can usually be performed in the range of 5,000 to 30,000 revolutions per minute. This means that if the material has a higher hardness or has a complex shape, the processing speed may be relatively low; conversely, if the material has a low hardness or the shape is simple, the processing speed may be relatively high. The flexibility of this processing method allows it to adapt to various processing needs, thus playing an important role in various industrial productions.
The time for five-axis CNC machining depends on many factors, including but not limited to the size, shape, complexity and material of the product. First, the size of the product is an important consideration. If the product is very large, the time required for processing increases accordingly. This is because large products require more time and steps to complete the processing process.
Secondly, the shape of the product will also affect the processing time. Some complex shapes may require more delicate machining and more operating steps, which will increase processing time. In contrast, simple shapes may require fewer operating steps and therefore result in relatively shorter processing times.
In addition, product complexity is also an important factor affecting processing time. Complex products usually have more details and features, which require higher precision and more operating steps to complete the processing. Therefore, products with higher complexity often require longer processing times.
Finally, the materials used in the product will also have an impact on processing time. Different materials have different hardness, toughness and processing characteristics. Some materials may require special tooling and techniques to machine, which can increase processing time. Some softer or easier-to-process materials may be able to be processed faster.
To sum up, the time of five-axis CNC machining is a complex issue, which is affected by many factors. Typically, five-axis CNC machining takes hours to days to complete. However, the specific processing time needs to be determined based on the specific characteristics and requirements of the product.
The cost of 5-axis CNC machining is a complex and multifaceted issue that is influenced by a variety of factors. These factors include the size, shape, and complexity of the product being machined, as well as the material from which it is made. Additionally, the machining time required to complete the task and the tool usage involved in the process also play a significant role in determining the overall cost.
One of the key considerations when assessing the cost of 5-axis CNC machining is the size of the product. Larger products require more time and resources to machine, which can increase the overall cost. Similarly, products with intricate shapes or complex geometries may require additional tooling and programming, further adding to the expense.
Another important factor to consider is the material from which the product is made. Different materials have different machinability characteristics, which can impact the efficiency and effectiveness of the machining process. For example, some materials may be more difficult to cut or machine than others, requiring specialized tools and techniques that can increase costs.
In addition to these factors, the machining time required to complete the task is also a significant contributor to the overall cost. Longer machining times can result in higher labor costs and increased wear and tear on equipment, both of which can add to the overall expense.
Finally, tool usage is another crucial factor that must be considered when assessing the cost of 5-axis CNC machining. The type and quality of tools used during the machining process can significantly impact the efficiency and accuracy of the process, as well as its overall cost. High-quality tools may be more expensive but can also result in better outcomes and reduced downtime, ultimately saving money in the long run.
In conclusion, the cost of 5-axis CNC machining is a complex issue that is influenced by a wide range of factors. By carefully considering each of these factors, including product size, shape, complexity, material, machining time, and tool usage, manufacturers can make informed decisions about their machining processes and optimize their operations for maximum efficiency and cost savings.
To ensure the operator's safety when operating a five-axis CNC machine tool, some protective equipment such as safety glasses, gloves, and protective clothing must be provided. The purpose of these protective equipment is to protect the operator from possible injuries, such as flying metal fragments or hot cutting fluids. Safety glasses can prevent metal fragments from entering the eyes and causing serious eye injuries. Gloves protect hands from cutting fluid corrosion and heat. Protective clothing can provide full body protection and prevent cutting fluid from splashing on the skin and causing chemical burns. Therefore, when using five-axis CNC machine tools, strict compliance with safety regulations and correct wearing of protective equipment are important measures to ensure operator safety.
Five-axis CNC machining is a highly complex manufacturing process that relies on the support of computer-aided design/computer-aided manufacturing (CAD/CAM) software. The main function of this software is to convert the 3D model into executable machine code so that the CNC machine tool can accurately perform the predetermined processing tasks.
In this process, you first need to use CAD software to create or modify a three-dimensional model. This model can be the geometry of a part or the structure of an assembly. This model is then imported into CAM software for further processing and optimization.
In CAM software, engineers can set various parameters according to actual processing needs, such as tool type, path, speed, etc. These parameters will be converted into a language that the machine can understand, that is, machine code. Finally, this machine code is sent to the CNC machine tool, which automatically performs the machining tasks.
Therefore, it can be said that without the support of CAD/CAM software, five-axis CNC machining cannot be carried out. This is because this software can not only help engineers create and optimize models, but also convert the models into a language that machines can understand, thus greatly improving the efficiency and accuracy of processing.
CNC machining machines, which are widely used in various industries forCNC machining machines, which are widely used in various industries for their precision and efficiency, demand a consistent schedule of maintenance and upkeep. This involves a series of essential tasks that must be carried out regularly to ensure the longevity and optimal performance of the machine.
Firstly, cleaning is an integral part of CNC machining machine maintenance. Over time, dust, debris, and other contaminants can accumulate on the machine's components, leading to reduced efficiency and potential damage. Therefore, it is crucial to clean the machine thoroughly, paying close attention to all areas where dirt and grime may have accumulated. This includes the worktable, tool holders, spindle, and other moving parts.
In addition to cleaning, lubrication plays a vital role in maintaining CNC machining machines. Proper lubrication helps reduce friction between moving parts, thereby minimizing wear and tear and extending the lifespan of the machine. It is essential to use high-quality lubricants specifically designed for CNC machining machines and to apply them according to the manufacturer's recommendations.
Another crucial aspect of CNC machining machine maintenance is the replacement of worn or damaged parts. As with any mechanical device, certain components will eventually wear out or become damaged due to regular use. Regular inspections should be conducted to identify any parts that require replacement, such as worn bearings, broken belts, or damaged motor brushes. Timely replacement of these parts ensures that the machine continues to operate efficiently and effectively.
Furthermore, regular calibration and inspection of the CNC machining machine are essential to maintain its accuracy and performance. Calibration involves adjusting the machine's settings to ensure that it produces precise and accurate results. This process should be performed at regular intervals, depending on the machine's usage and the level of precision required for the work being performed.
Inspection, on the other hand, involves visually examining the machine's components for signs of wear, damage, or other issues that may affect its performance. This includes checking the alignment of the machine's axis, ensuring that all moving parts are functioning correctly, and verifying that all electrical connections are secure. Regular inspections help identify potential problems before they escalate into more significant issues, allowing for prompt corrective action.
In conclusion, CNC machining machines require regular maintenance and upkeep to ensure their longevity, accuracy, and optimal performance. This includes cleaning, lubrication, replacement of worn or damaged parts, regular calibration, and thorough inspections. By adhering to these maintenance practices, operators can extend the lifespan of their CNC machining machines and ensure that they continue to deliver precise and efficient results in their respective industries.
Common question in 5 Axis CNC Machining Production
5-axis CNC machining can perform various surface treatments, such as grinding, polishing, spraying, anodizing, etc.
Five-axis CNC machining technology is an advanced manufacturing process that is capable of performing a variety of post-processing operations. These subsequent processing operations include, but are not limited to, laser cutting, water cutting, wire cutting, and electrical discharge machining.
First, let’s learn about laser cutting. Laser cutting is a process that uses high-energy laser beams to cut materials. By focusing the laser beam on the workpiece, laser cutting can accurately cut a variety of materials such as metal, plastic and wood. This cutting method has the characteristics of high precision, high efficiency and non-contact, so it has been widely used in the manufacturing industry.
Secondly, water cutting is a process that uses high-pressure water flow to cut materials. Waterjet cutting is suitable for cutting a variety of materials, including metal, glass, ceramics and plastics. Since there is no thermal deformation and mechanical stress during water cutting, it maintains material integrity and accuracy. In addition, waterjet cutting can also achieve complex geometric shapes and curved cutting, so it is widely used in art design, aerospace, automobile manufacturing and other fields.
Third, wire cutting is a process that uses electric spark discharge to cut materials. Wire cutting is suitable for cutting various conductive materials, such as metals and alloys. Wire cutting has the advantages of high precision, high efficiency and flexibility, and can realize the processing of complex-shaped parts. In addition, wire cutting can also process tiny holes, so it has important applications in the mold manufacturing and electronics industries.
Finally, EDM is a process that uses electrical spark discharges to process materials. EDM is suitable for processing a variety of conductive materials, such as metals and alloys. EDM has the advantages of high precision, high efficiency and flexibility, and can process parts with complex shapes. In addition, EDM can also perform surface strengthening and material removal operations, so it has a wide range of applications in the mold manufacturing and aerospace fields.
To summarize, five-axis CNC machining technology is capable of performing a variety of post-processing operations, including laser cutting, waterjet cutting, wire cutting, and electrical discharge machining. These subsequent processing operations play an important role in the manufacturing industry, providing more choices and possibilities for product manufacturing.
Five-axis CNC machining technology is an advanced manufacturing process that can handle products of various sizes. Whether it is a small component or a large workpiece, this technology can easily handle it. Its flexibility and precision make it widely used in manufacturing. Whether for small batch production or large-scale production, five-axis CNC machining can provide efficient and precise solutions. Therefore, no matter what size product you need to process, five-axis CNC machining can provide you with satisfactory services.
In the process of five-axis CNC machining, the process can be divided into the following steps in detail: First, we need to create a product design model. This stage involves an in-depth understanding and precise grasp of the product's shape, size and functional requirements to ensure that the designed product can meet the needs of actual applications.
Next, we need to use computer-aided design/computer-aided manufacturing (CAD/CAM) software to write the machining program. This step is the core of the entire processing process, which determines how the machine can perform precise processing according to the parameters and paths we set.
After writing the machining program, we need to set the parameters of the machine tool. This includes selecting the right tool, determining cutting speed and feed rate, etc. to ensure the smooth progress of the machining process.
Then we need to load the tools and materials. This step requires us to select appropriate tools and materials according to the requirements of the processing program and install them on the machine tool.
Next, we can start processing. At this stage, the machine tool will automatically perform precise cutting according to the programs and parameters we set.
After completing the preliminary processing, we also need to treat the surface of the product. This may include steps such as sanding, polishing, painting, etc. to improve the product's appearance quality and durability.
Finally, we need to perform follow-up processing, such as checking product quality, packaging products, etc., to ensure product integrity and meet customer needs.
In modern manufacturing, the machining accuracy of five-axis CNC machine tools is an important consideration. The machining accuracy of such machine tools is affected by many factors, including but not limited to tool quality, machine tool stability, machining speed, and tool path planning.
First of all, tool quality is one of the important factors affecting the machining accuracy of five-axis CNC machine tools. High-quality tools ensure stability and accuracy during processing, thereby improving product quality and consistency. Conversely, low-quality tools may lead to an increase in machining errors, which in turn affects the quality of the final product.
Secondly, the stability of the machine tool is also a key factor affecting the machining accuracy. A stable machine tool ensures high-precision machining capabilities over long periods of operation. An unstable machine tool may cause vibration and errors during the machining process, thereby reducing machining accuracy.
In addition, processing speed is also one of the factors affecting the processing accuracy of five-axis CNC machine tools. Appropriate processing speed can improve production efficiency, but too fast a processing speed may cause the machine tool to be unable to remain stable, thus affecting processing accuracy. Therefore, choosing the appropriate processing speed is crucial to ensure processing accuracy.
Finally, tool path planning is also an important factor affecting the machining accuracy of five-axis CNC machine tools. Reasonable tool path planning can reduce unnecessary movements and errors during processing, thereby improving processing accuracy. On the contrary, unreasonable tool path planning may lead to an increase in machining errors, thereby affecting the quality of the final product.
To sum up, the machining accuracy of five-axis CNC machine tools is affected by many factors such as tool quality, machine tool stability, machining speed, and tool path planning. In order to improve processing accuracy, manufacturers need to comprehensively consider these factors and take corresponding measures to optimize the processing process.
The service life of tools is affected by many factors for five-axis CNC machining. These factors include, but are not limited to, tool material, tool quality, frequency of use of the tool, and how well the tool is maintained.
First of all, tool material is one of the important factors affecting the service life of the tool. Different tool materials have different properties such as hardness, wear resistance and corrosion resistance, so choosing a tool material suitable for a specific machining task can effectively extend the service life of the tool. For example, for high-speed cutting, choosing tool materials with high hardness and wear resistance can reduce the rate of tool wear, thereby extending its service life.
Secondly, the quality of the tool is also one of the key factors that determine the service life of the tool. High-quality tools usually have better manufacturing processes and stricter quality control standards, so they are better able to maintain their performance and stability during use. In contrast, low-quality tools may have manufacturing defects or inconsistent performance that can easily lead to early failure or damage.
In addition, the frequency of use of the tool will also directly affect its service life. Tools that are used frequently will gradually lose their original performance and accuracy due to factors such as friction, wear, thermal expansion and contraction. Therefore, reasonably planning the time and frequency of tool use and avoiding overuse or continuous use of the same tool for a long time can effectively extend the service life of the tool.
Finally, the maintenance of tools is also an important part of ensuring their service life. Regular cleaning, lubrication and inspection of tools, timely discovery and repair of potential problems can effectively reduce the failure rate and damage of tools and extend their service life. At the same time, proper storage and care of tools can also prevent damage or corrosion caused by environmental factors.
To sum up, the service life of tools is a complex issue for five-axis CNC machining and is affected by many factors. By selecting appropriate tool materials, ensuring tool quality, reasonably planning the frequency of use, and doing maintenance work, the service life of the tool can be maximized and the processing efficiency and quality can be improved.
Five-axis CNC machining technology is an advanced manufacturing process that can handle various complex surface shapes. This technology has a wide range of applications, including but not limited to spherical surfaces, conical surfaces, freeform surfaces, and compound curved surfaces.
First, let’s take a look at five-axis CNC machining technology. This is a precision machining method achieved through computer numerical control (CNC), which uses five independent axes to operate. These five axes can move simultaneously to achieve precise machining of complex curved surfaces.
In five-axis CNC machining, we can process various types of surfaces. The first is the spherical surface, which is a special type of surface that is shaped like a sphere. Through five-axis CNC machining technology, we can accurately machine the curvature and smoothness of the spherical surface to meet specific design requirements.
Secondly, five-axis CNC machining can also handle tapered surfaces. A tapered surface is a curved surface that has a taper, the shape of which gradually becomes thinner or thicker from bottom to top. Through five-axis CNC machining technology, we can precisely control the taper and size of the tapered surface to achieve the desired geometry.
In addition, five-axis CNC machining can also handle free-form surfaces. A free-form surface refers to a surface that does not have a clearly defined geometric shape, and its shape can be any curve or polyline. Through five-axis CNC machining technology, we can freely shape the shape of the free-form surface according to design requirements to achieve unique design effects.
Finally, five-axis CNC machining can also handle compound curved surfaces. A compound curve surface refers to a surface composed of multiple curves. These curves can be straight lines, arcs, elliptical arcs, etc. Through five-axis CNC machining technology, we can combine these curves to form complex surface shapes to meet specific design needs.
To sum up, five-axis CNC machining technology is a powerful tool that can handle various complex surface shapes, including spherical surfaces, tapered surfaces, free-form surfaces and compound curved surfaces. Through precise control and flexible operation, we can achieve efficient processing of complex curved surfaces, bringing great convenience and innovation to the manufacturing industry.
Processing at too fast a rate may cause the tool to wear out more quickly. This rapid wear not only affects the service life of the tool, but also has a negative impact on the quality of the machining. Because when a tool wears too fast, its accuracy and stability may decrease, thus affecting the quality of the processed products.
On the other hand, if the processing speed is too slow, then the processing efficiency will be affected. Because in the production process, time is money. If the processing speed is too slow, it will take longer to complete the same work, which will undoubtedly increase production costs and reduce production efficiency. At the same time, too slow processing speed may also cause waiting in other links in the production process, further affecting the efficiency of the entire production process.
Therefore, we need to find a suitable processing speed that can not only ensure processing quality, but also improve processing efficiency. This requires us to reasonably adjust the processing speed according to specific processing needs and equipment performance in actual operations to achieve the best production results.
Five-axis CNC machining is a high-precision machining method that requires specific environmental conditions to ensure the quality and accuracy of processing. First of all, the environment must be kept dry, because humidity will affect the movement and processing accuracy of the machine tool. Secondly, the temperature must be stable, because changes in temperature will cause thermal expansion and contraction of the machine tool, thus affecting the machining accuracy. In addition, there must be no vibration in the environment, because vibration will affect the stability and processing accuracy of the machine tool. At the same time, there should be no dust in the environment, because dust will enter the inside of the machine tool and affect the operation and processing quality of the machine tool. Finally, there must be no electromagnetic interference in the environment, because electromagnetic interference will affect the electronic system of the machine tool and lead to processing errors. Therefore, in order to ensure the quality and accuracy of five-axis CNC machining, we need to provide a dry, temperature-stable, vibration-free, dust-free, and electromagnetic interference-free environment.