Table of Contents:
- Introduction
- Materials used in Custom Plastic Parts
- Custom Plastic Parts Manufacturing Techniques
- Design Considerations for Custom Plastic Parts
- Prototyping and Testing
- Applications of Custom Plastic Parts
- Customization and Manufacturing Process Optimization
- Future of Custom Plastic Parts
- Conclusion
-
1.Introduction
Definition of Custom Plastic Parts:
Custom plastic parts are specifically designed and manufactured plastic components that are unique to a particular product or application. These plastic parts are made-to-order in small or large quantities based on the specifications and requirements of the client.
Importance and Uses:
Custom plastic parts play a critical role in various industries, including automotive, medical, packaging, consumer products, and more. They are used to replace metal or other materials, providing a cost-effective and efficient solution for manufacturing. Custom plastic parts can be tailored to exact specifications, minimizing material waste and reducing overall cost and lead time. These plastic parts can serve various purposes such as structural support, mechanical components, visual display, and more.
Advantages of Custom Plastic Parts:
There are many advantages to using custom plastic parts in manufacturing processes. Some of these advantages include:
- Lightweight and Durable
- Cost-Effective
- Design Flexibility
- Tailored Specifications
- High Production Output
- Corrosion Resistant
- Improved Aesthetics and Finishing
- Low Maintenance
Overall, custom plastic parts provide an excellent alternative to conventional manufacturing methods, providing multiple advantages such as customization, durability, and cost savings.
-
2.Materials used in Custom Plastic Parts
Types of Plastics for Custom Plastic Parts:
There are various types of plastics used for custom plastic parts. Some of the most popular plastic materials used for custom plastic parts include:
- Acrylics
- ABS (Acrylonitrile Butadiene Styrene)
- Polyethylene
- Polypropylene
- Polycarbonate
- PVC (Polyvinyl Chloride)
- Nylon
- PTFE (Polytetrafluoroethylene)
Factors to Consider in Material Selection:
Choosing the right material for custom plastic parts is essential to ensuring that the final product is high-quality and meets the required specifications. The material chosen for custom plastic parts can affect their durability, strength, cost, and overall quality.
Some factors to consider when choosing the right material for custom plastic parts include:
- Strength and Durability
- Chemical Resistance
- Temperature Resistance
- UV and Weathering Resistance
- Dielectric Strength and Insulation Properties
- Regulatory Compliance and Safety Standards
- Cost and Availability
- Color and Surface Finishing
The selection of the most appropriate plastic material for a specific custom part application involves careful evaluation of different factors and considerations. Therefore, it is necessary to have technical expertise and knowledge to make the most effective material selection decision.
-
3.Custom Plastic Parts Manufacturing Techniques
There are several plastic manufacturing techniques used to produce custom plastic parts. The choice of technique is usually based on the part’s size and shape, the production quantity required, and the required quality specifications.
The following are some of the most common custom plastic parts manufacturing techniques:
- Injection Molding:
Injection molding is the most widely used method for producing custom plastic parts. It involves the melting of plastic material pellets into a liquid form, which is then pumped into a mold cavity. Once inside, the material is cooled to solidify to form the desired shape. Injection molding is suitable for producing large volumes of small to medium-sized intricate parts, and it’s highly efficient. - Blow Molding:
Blow molding is a technique that involves extruding a hollow tube of molten plastic material, which is then inflated to the shape of the desired part. This process is commonly used for producing water bottles and other plastic containers with large volumes and limited geometries. - Rotational Molding:
Rotational molding is a unique plastic manufacturing process used for molded parts with complex geometries. A hollow mold is filled with plastic material, heated, and then rotated around two perpendicular axes, ensuring the material bonds with the mold wall, producing the shape. - Thermoforming:
Thermoforming is a plastic manufacturing technique that involves heating plastic sheets until they become pliable, and then they are shaped into the final form using a mold or press. Thermoforming is ideal for producing large, lightweight parts with shallow shapes. - Extrusion:
Extrusion involves melting raw plastic material pellets, passing it through a die, which shapes it into a continuous profile, and then cooled with the desired shape. Extrusion is great for producing long pieces with uniform cross-sections, such as plastic tubing and pipes.
Each of these manufacturing techniques has its advantages and disadvantages, necessitating careful consideration of production requirements, performance specifications, and other key factors when selecting a suitable method.
-
4.Design Considerations for Custom Plastic Parts
Creating custom plastic parts involves a series of design considerations that need careful evaluation to achieve the desired product specification, performance, quality, and cost-effectiveness.
- Product Design:
The product design phase involves creating a detailed design drawing of the custom plastic part, outlining specifications such as shape, size, material color, surface texture, finishing, and other critical parameters. The product design phase ensures that the desired product is of top quality, meets specific functionality requirements, and is aesthetically pleasing. - Mold Design:
During the mold design phase, the team creates the specific mold for the custom plastic part’s production. Custom plastic parts manufacturing techniques such as injection molding require the creation of the mold, which is precise and tailored to the product design specifications. The mold design process takes into account the material, product geometry, expected production rates, and costs to ensure efficient and high-quality design. - Tooling Design:
Tooling refers to the tools and equipment used to create and maintain the mold during the manufacturing process. Tooling design takes into account the molded parts’ size and shape, material viscosity, and any specific part release mechanisms needed. The creation of quality tooling design helps produce perfect plastic parts with precise features and the required aesthetic appearance, ensuring the molding process runs efficiently and accurately.
In summary, the design phase plays a pivotal role in custom plastic parts manufacturing, and it is key to producing parts in the exact design and performance specifications required for specific end-use applications. Product design, mold design, and tooling design phases work collectively to ensure that custom plastic parts are low cost, high quality, and delivered on time.
-
5.Prototyping and Testing
Prototyping and testing are crucial phases in the custom plastic parts manufacturing process, and they play an essential role in ensuring that the final product meets the desired quality specifications.
1.Reasons Why Prototyping is Important:
Prototyping is important as it helps identify potential design, manufacturing, and production issues before starting large-scale production. Prototyping can help to reduce costs, avoid potential problems, and allow for design modifications or adjustments. Prototyping also allows customers to validate their designs and ensure the parts will meet all the required specifications.
2.Types of Prototyping:
There are various types of prototyping available in custom parts manufacturing processes, including:
- 3D Printing
- CNC Machining
- Manual Prototyping
- Bridge Tooling
- Soft Tooling
3.Quality Testing and Control:
Quality testing is fundamental in ensuring that the custom plastic parts meet the required specifications and standards. There are several quality control tests for custom plastic parts, including:
- Dimensional Analysis: Ensuring parts are of the correct size, shape, and geometries.
- Material Testing: Testing materials before the product materials to know the properties of the final product.
- Thermal Testing: to ensure parts can handle desired temperature range, thermal testing is conducted.
- Aesthetics and Visual Testing: This test is conducted to insure plastic parts’ appearance meets the required finishing and color requirement.
- Performance Testing: This test is done to ensure that custom plastic parts can perform the function they were designed for without failure.
Overall, the prototyping and testing phases are critical in custom plastic parts manufacturing, allowing for the identification and resolution of design and production issues at an early stage, ensuring that the final product is of high quality and meets the required specifications.
-
6.Applications of Custom Plastic Parts
Custom plastic parts are widely used in various industries, and their versatility makes them a popular choice for many applications. The following are some of the most noteworthy applications of custom plastic parts:
- Automotive Industry:
Custom plastic parts are used extensively in the automotive industry due to their durability, low cost, and excellent finishing. Some examples of custom plastic parts used in the automotive industry include bumpers, interior trims, and fuel tanks. - Consumer Products:
Many consumer products use custom plastic parts to achieve the desired aesthetic appeal, functionality, and durability. These products include electronics, household appliances, toys, sporting goods, and more. - Medical Industry:
Plastic parts used in the medical industry must meet stringent regulatory standards and be biocompatible. Custom plastic parts are used in medical equipment, prostheses, surgical instruments, and more. - Packaging:
Custom plastic parts are used extensively in the packaging industry to create lightweight, durable, and attractively finished packaging materials. Plastic packaging is used in various applications such as food and medical packaging, consumer goods, and many more.
The extensive applications of custom plastic parts underline the versatility and cost-effectiveness of plastic parts’ technology for various consumer and industrial uses from medical and automotive to consumer goods and packaging.
-
7.Customization and Manufacturing Process Optimization
Customization and manufacturing process optimization are critical components in achieving cost-effective and efficient custom plastic parts production.
- Customized Order Processing:
Customized order processing involves the customization and tailoring of production specifications to a specific client’s requirements. This includes product design customization to unique features, fitting specific production runs, and shipment requirements. With custom order processing, clients can have specific input in the final design and manufacturing process, ensuring that the product delivered meets their requirements accurately. - Batch Production vs. Mass Production:
The choice of batch or mass production depends on the production quantity required, the speed of production, and the cost-effectiveness of each method. Batch production is appropriate for small to medium production runs, such as custom plastic medical components or automotive parts. Mass production is a suitable option for a large-scale production of customized plastic parts that require consistency and speed, such as consumer products like plastic bottles and containers. - Reducing Lead Time and Cost:
Reducing lead time and cost is crucial in custom plastic parts manufacturing processes. This can be achieved through the use of the latest technology, optimization of manufacturing processes, and inventory management systems to ensure raw materials and parts are delivered just-in-time. By reducing lead time and cost, clients can receive their orders quickly and at a lower cost.
In conclusion, customization and manufacturing process optimization are critical components in custom plastic parts manufacturing. Customization allows precise production specifications to meet specific product standards, while manufacturing process optimization enhances cost-effectiveness and reduces lead time, ensuring clients receive quality products produced with maximum efficiency.
-
8.Future of Custom Plastic Parts
The future of custom plastic parts will be influenced by emerging trends and the need for sustainable and eco-friendly solutions that provide product durability, quality, and design flexibility while minimizing production costs and environmental impact.
- Emerging Trends and Technologies:
Emerging trends and technologies such as additive manufacturing (3D printing), artificial intelligence (AI), and the Internet of Things (IoT) are changing the custom plastic parts industry. For instance, 3D printing has the potential to revolutionize the design and prototyping of custom plastic parts, while AI and IoT can optimize production processes, reduce material waste, and ensure optimal quality while reducing energy consumption. - Sustainability and Eco-Friendly Solutions:
The push for sustainable and eco-friendly solutions will continue to shape the future of custom plastic parts. This includes the development of biodegradable and recycled plastic materials, and the adoption of circular business models, which aim to minimize waste and maximize resource utilization.
In Conclusion, the future of custom plastic parts will be shaped by emerging trends and technologies that improve production efficiency and minimize environmental impact. Additionally, efforts to promote sustainability and eco-friendly solutions are likely to lead to the development of new materials and manufacturing processes designed to meet evolving demands and challenges. Custom plastic parts will remain a valuable solution in several industries for the manufacture of light, inexpensive, and robust components.
Click on the V1 Prototype website to gain more Custom Plastic Parts information.
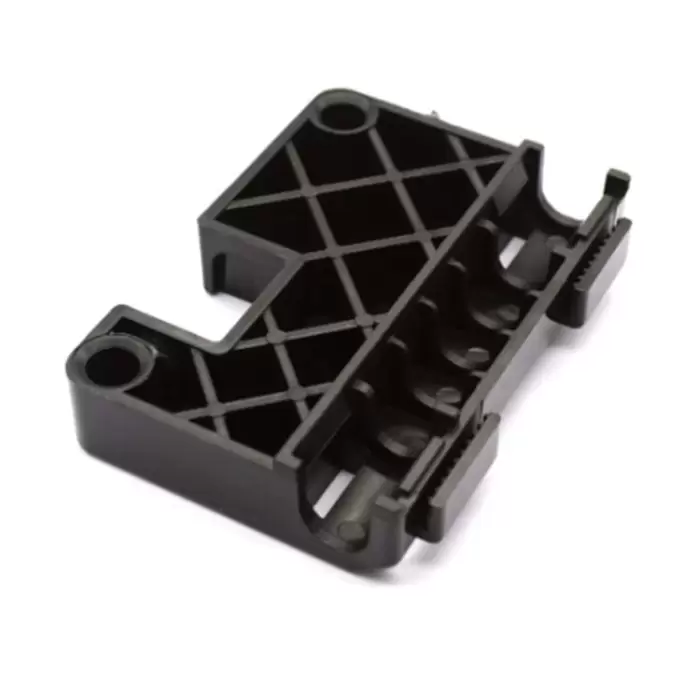
-
9.Conclusion
Throughout this discussion of custom plastic parts, we have identified several key points. Custom plastic parts are widely used in various industries, and their versatility makes them a popular choice for many applications, including the automotive industry, consumer products, packaging, and the medical industry. These custom plastic parts manufacturing techniques include injection molding, blow molding, rotational molding, thermoforming, and extrusion, which are chosen based on the part’s size and shape and the required production quantity.
The design phase plays a pivotal role in custom plastic parts manufacturing and is key to producing parts that meet the exact design and performance specifications required for specific end-use applications. Product design, mold design, and tooling design phases work collectively to ensure that custom plastic parts are low cost, high quality, and produced on time.
Prototyping and testing are crucial phases in the custom plastic parts manufacturing processes, and they play an essential role in ensuring that the final product meets the desired quality specifications. Customization, emerging trends and technologies, and the push for sustainable and eco-friendly solutions influence the future of custom plastic parts.
In conclusion, it is apparent that custom plastic parts play an essential role in various industries, and they will continue to do so in the future. The importance of custom plastic parts’ production process optimization, sustainability, and eco-friendly solutions ensures that it remains a valuable solution to many industries.