Selective Laser Melting (SLM) 3D Printing
Looking for a high-quality Selective Laser Melting (SLM) 3D printing service? Look no further! Our SLM technology provides precise and efficient layer-by-layer printing, creating complex and durable metal components for a wide range of applications. From prototyping to production, our SLM 3D printing service delivers superior quality and exceptional accuracy. Get started today and revolutionize your manufacturing process with the power of SLM 3D printing!
Selective Laser Melting (SLM) 3D Printing Parts
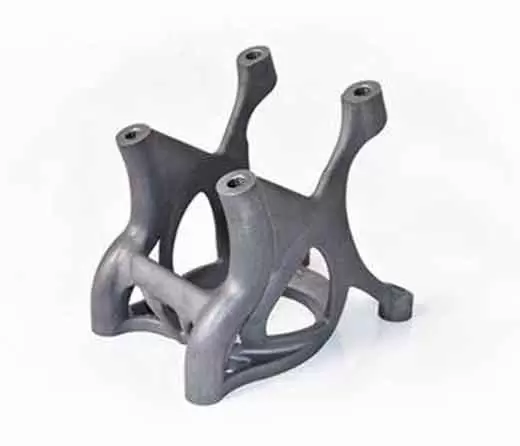
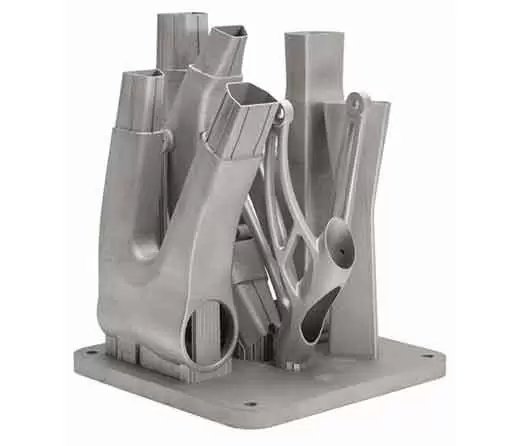
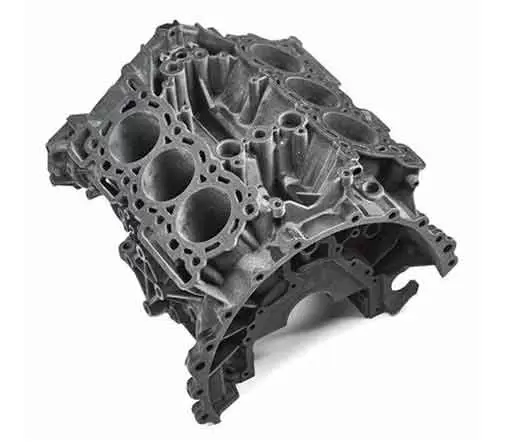
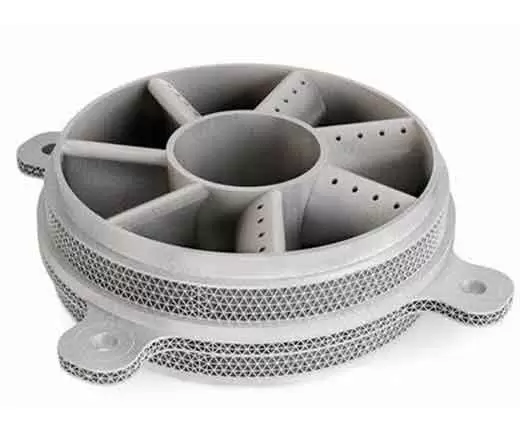
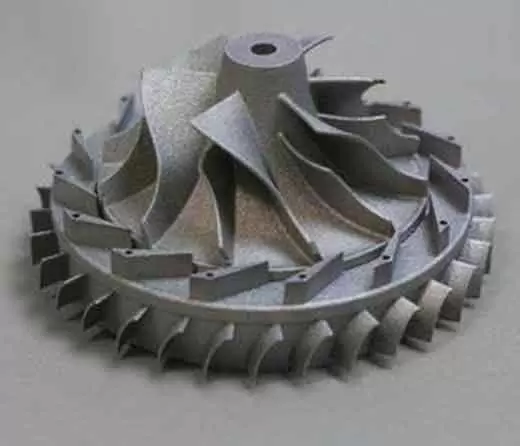
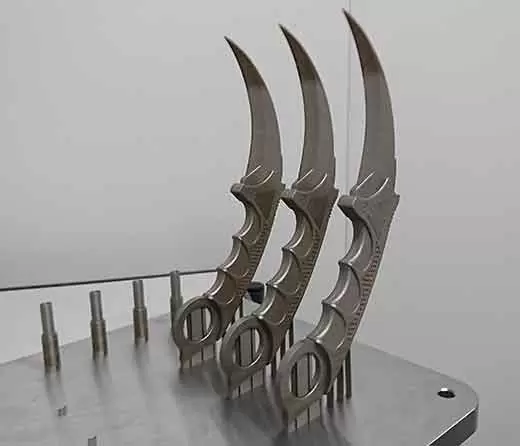
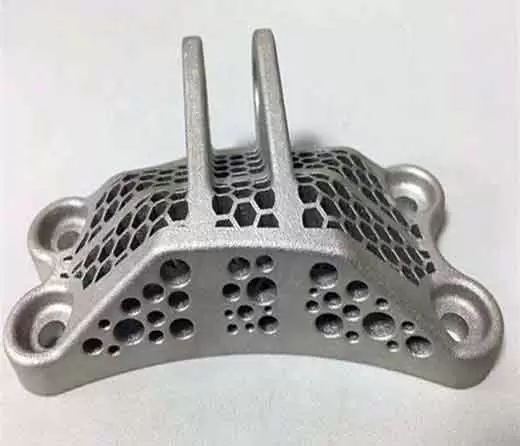
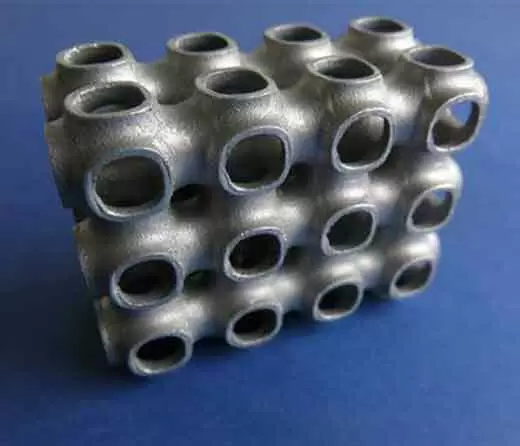
Stereolithography (SLA) 3D Printing Service
Introducing our groundbreaking Selective Laser Melting (SLM) 3D Printing Service, designed to revolutionize the way you manufacture metal components. Our SLM technology is at the forefront of the 3D printing industry, providing unrivaled precision, speed, and efficiency for all your prototyping and production needs.
At our state-of-the-art facility, we use advanced SLM equipment to create complex metal parts with incredible accuracy and durability. Using a layer-by-layer printing process, we can produce even the most intricate designs, from prototype to finished product.
Our team of skilled technicians is committed to delivering the highest quality results, ensuring your parts are completed to your exact specifications, on time and on budget. With our SLM 3D Printing Service, you’ll benefit from faster production times, reduced part costs, and increased design flexibility.
Join the growing number of businesses discovering the benefits of SLM 3D printing. Contact us today to learn how we can help you bring your innovative ideas to life with our advanced manufacturing capabilities.
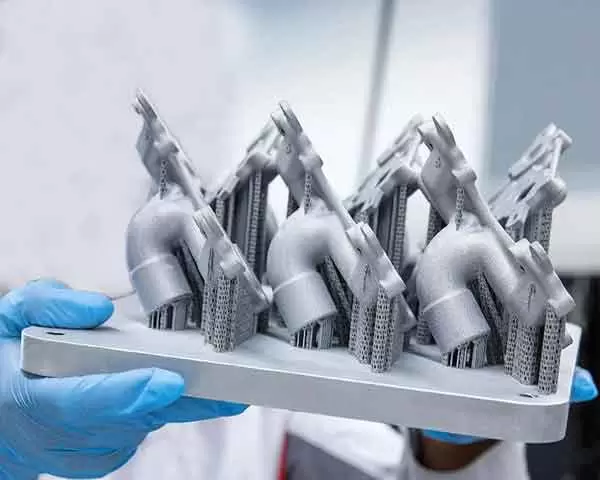
SLM 3D Printing Finishes
A polished finish is perfect for components that require a smooth, glossy surface. Our SLM 3D Printing service can achieve a polished finish through a range of techniques, including tumbling, sandblasting, and buffing.
A matte finish is achieved by sandblasting the component with fine grit. This creates a textured, non-reflective finish that is ideal for parts that require a non-glossy appearance.
Anodizing is an electrochemical process that creates a durable, corrosion-resistant finish on metal parts. This finish can be achieved in a range of colors, making it perfect for parts that need to be aesthetically appealing as well as functional.
Our SLM 3D Printing service can also produce parts with a painted finish. This is achieved by applying a coat of paint to the component, either by hand or using an automated process. With a range of paint options available, we can match your desired color or finish.
A brushed finish is created through a process of creating fine, directional lines on the surface of the component using abrasive grinding or sanding. This finish gives the part an industrial, brushed metal appearance that is ideal for a range of mechanical components.
A textured finish is achieved through a range of techniques, including bead blasting, sandblasting, and etching. This creates a unique, non-uniform finish that can be customized to your exact specifications.
At our state-of-the-art facility, we can apply a range of finishes to your SLM 3D Printed components to match your desired look and functionality. Contact us today to learn more about our finishing options and how we can help bring your designs to life.
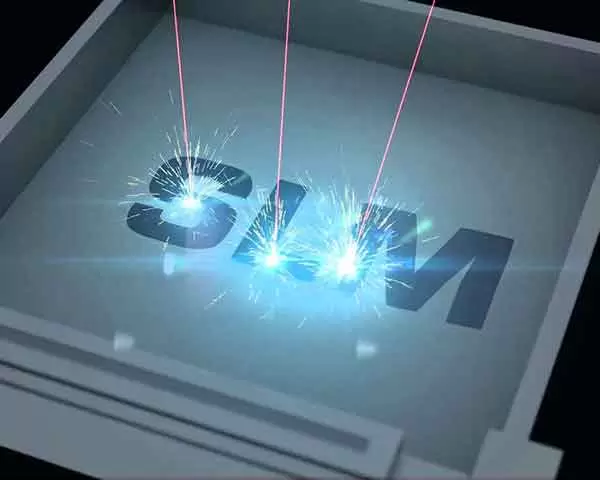
Why Choose SLM 3D Printing?
There are many reasons why Selective Laser Melting (SLM) 3D Printing is quickly becoming the preferred method for manufacturing high-quality metal components. With its advanced technology and precise layer-by-layer printing process, SLM offers a range of benefits that are hard to ignore.
First and foremost, SLM 3D Printing is incredibly efficient, reducing production times and lowering costs. This is because SLM can produce complex designs with multiple parts in one print run, eliminating the need for assembly and reducing potential errors.
Another major advantage of SLM 3D Printing is its flexibility in design. This opens up a range of new possibilities for product innovation and design.In addition, SLM 3D Printing is incredibly accurate, ensuring that each part is produced to precise specifications.
Beyond these benefits, SLM 3D Printing is also highly versatile, capable of producing parts in a range of metals and alloys, from titanium to stainless steel to cobalt chrome. This makes this technology ideal for a range of industries, from aerospace to medical devices to automotive and beyond. Experience the benefits of SLM 3D Printing for yourself and contact us today to get started.
SLM 3D Printing Production FAQs
SLM 3D printing is a metal additive manufacturing technology that uses a laser to melt and fuse layers of metal powder into complex shapes and parts.
SLM 3D printing is an advanced manufacturing technology that uses a laser beam to melt metal or other materials layer by layer to create complex three-dimensional structures. Here are some materials that can be used for SLM 3D printing:
1. Metal alloy: This is the most common material type for SLM 3D printing. Including titanium alloys, nickel-based superalloys, aluminum alloys, stainless steel, etc. These metal alloys have excellent strength and durability and are suitable for manufacturing aerospace components, medical implants, automotive parts, and more.
2. High-performance plastics: SLM 3D printing can also use high-performance plastics, such as nylon, polycarbonate, polyester, etc. These plastics have good wear, heat and impact resistance and are suitable for manufacturing tools, molds and consumer products.
3. Ceramic materials: Ceramic materials, such as alumina, zirconia, etc., can also be used for SLM 3D printing. These materials have excellent heat resistance, corrosion resistance and insulation properties and are suitable for manufacturing electronic devices and biomedical equipment.
4. Composite materials: Composite materials are composed of two or more materials and usually have better properties than a single material. For example, carbon fiber reinforced plastic (CFRP) is a common composite material used to make lightweight parts for airplanes and cars.
5. Metal powder and metal wire: In addition to directly using metal alloys for printing, metal powder and metal wire can also be used as printing materials. These materials are melted and stacked layer by layer during the printing process to form the final three-dimensional structure.
In general, SLM 3D printing can use various types of materials, including metal alloys, high-performance plastics, ceramic materials, composite materials, and metal powders and wires. This enables SLM 3D printing to be used in a variety of different industries and applications.
Selective laser melting (SLM) 3D printing technology is an advanced manufacturing technology that can be used with a variety of metal powders, including stainless steel, titanium, aluminum, cobalt-chromium alloys, and other types of metals. The flexibility of this technology allows it to be adapted to a variety of different printing needs.
First of all, for aerospace parts with high strength requirements, SLM 3D printing technology can be achieved by selecting appropriate metal powders. For example, for aerospace parts that need to withstand high temperatures and pressures, high-strength metal powders such as titanium or cobalt-chromium alloys can be printed. These metal powders, when melted, form solid prints with the strength and durability required to meet the stringent requirements of the aerospace industry.
Secondly, for medical devices with high corrosion resistance requirements, SLM 3D printing technology can also be achieved by selecting appropriate metal powders. For example, for medical devices that need to be in contact with the human body, you can choose to use stainless steel or other metal powders with better corrosion resistance for printing. After melting, these metal powders can form smooth and non-porous printed parts with good corrosion resistance, ensuring that medical devices will not be affected by corrosion during use.
In addition, SLM 3D printing technology can also optimize printing effects by adjusting printing parameters, further improving the performance of printed parts. For example, the laser power can be adjusted to control the melting degree and solidification speed of the printed parts to achieve better printing results. At the same time, the layer thickness and surface quality of printed parts can also be controlled by adjusting the scanning speed to meet the needs of different applications.
In short, selective laser melting (SLM) 3D printing technology has broad application prospects. Whether it is aerospace parts with high strength requirements or medical devices with high corrosion resistance requirements, high-quality prints can be achieved by selecting appropriate metal powders and adjusting printing parameters. The flexibility and customizability of this technology make it an important innovation in manufacturing, providing more possibilities for various industries.
Selective laser melting (SLM) 3D printing technology has many significant advantages over traditional manufacturing methods. First, it provides greater design freedom. In the traditional manufacturing process, designers often need to design products based on existing manufacturing technology and equipment limitations, which greatly limits the innovation and flexibility of design. However, the emergence of SLM 3D printing technology has broken this limitation, and designers can use their innovative thinking more freely to design more complex and sophisticated products.
Secondly, SLM 3D printing technology can greatly shorten the time of prototyping and production. Traditional manufacturing methods often require multiple steps to complete the manufacturing of a product, which is not only time-consuming but also can lead to errors at each step, causing delays in the entire manufacturing process. In contrast, SLM 3D printing technology can directly transform the designed model into a physical object in one operation, greatly improving production efficiency.
Finally, SLM 3D printing technology can also reduce material waste. In the traditional manufacturing process, a large amount of waste is often generated due to the need for cutting and processing. However, SLM 3D printing technology manufactures products by stacking materials layer by layer, producing almost no waste, thus greatly reducing material waste.
In general, SLM 3D printing technology is gradually changing the traditional manufacturing industry with its unique advantages and opening up a new path for the development of manufacturing industry.
Selective laser melting (SLM) 3D printing technology has been widely used in many industries, including but not limited to aerospace, automobile manufacturing, medical health, and defense and security.
First of all, the aerospace industry is an important application field of SLM 3D printing technology. In this field, 3D printing technology is used to manufacture complex aerospace parts, such as engine parts, aircraft structural parts, etc. The precision and quality of these parts are critical to the performance and safety of the aircraft. By using SLM 3D printing technology, manufacturers can produce high-quality parts in a short time, greatly improving production efficiency.
Secondly, the automotive industry is also a major user of SLM 3D printing technology. In this field, 3D printing technology is used to manufacture automotive parts, such as engine components, braking systems, etc. The manufacturing of these parts requires high precision and quality, and SLM 3D printing technology can meet these needs. In addition, by using 3D printing technology, automobile manufacturers can also achieve rapid prototyping, thereby greatly shortening the product development cycle.
In the medical and health field, SLM 3D printing technology also plays an important role. In this field, 3D printing technology is used to manufacture various medical equipment and human organ models. For example, doctors can use 3D printing technology to create models of patients' hearts for surgical simulation and training. In addition, by using 3D printing technology, doctors can also create customized prostheses and teeth to meet the individual needs of patients.
Finally, the field of national defense and security is also an important application field of SLM 3D printing technology. In this field, 3D printing technology is used to manufacture various military equipment and weapons. For example, the military can use 3D printing technology to create lightweight body armor and helmets to improve soldiers' survivability. In addition, by using 3D printing technology, the military can also achieve rapid prototyping, thereby greatly increasing the speed of equipment update.
The maximum build size of SLM 3D printing machines will vary, but can typically vary from a few centimeters to several meters. This technology allows users to choose the appropriate print size based on their needs and the size of their project. For example, for small models or prototype designs, only a few centimeters of print size may be required. However, for large structures or complex parts, print sizes of several meters may be required. This flexibility makes SLM 3D printing widely used in a variety of industries and applications, including aerospace, automotive manufacturing, healthcare, and more.
Selective laser melting (SLM) 3D printing technology offers a high level of accuracy. Specifically, its accuracy is typically in the range of +/- 0.1 mm to +/- 0.2 mm, which varies depending on the material used and the type of machine. This high-precision feature makes SLM 3D printing technology widely used in many fields, such as aerospace, medical health, automobile manufacturing, etc.
In the aerospace field, SLM 3D printing technology is widely used to manufacture complex parts and structural parts. Since the aerospace industry requires very high precision for parts, traditional manufacturing methods often cannot meet the demand. SLM 3D printing technology can achieve micron-level accuracy and can produce very fine parts, thereby improving the performance and reliability of aircraft and spacecraft.
In the medical and health field, SLM 3D printing technology also plays an important role. By using biodegradable materials, SLM 3D printing technology can create personalized medical devices and implants. These devices and implants can be customized to a patient's specific condition, improving the success rate of surgery and patient recovery. In addition, SLM 3D printing technology can also be used to create bionic organs and tissues, providing new possibilities for medical research and clinical treatment.
In the field of automobile manufacturing, SLM 3D printing technology also has broad application prospects. The traditional automobile manufacturing process requires a large number of molds and tools, while SLM 3D printing technology can achieve rapid prototyping and small batch production, reducing manufacturing costs and time. In addition, SLM 3D printing technology can also produce lightweight automobile parts and improve the fuel efficiency and performance of automobiles.
In addition to the above fields, SLM 3D printing technology has also been applied in other industries. For example, in the energy field, SLM 3D printing technology can produce efficient solar panels and wind turbine blades; in the art and design field, SLM 3D printing technology can realize the design and production of complex shapes; in the construction field, SLM 3D printing Technology can be used to create architectural models and components, etc.
In short, the high-precision characteristics of selective laser melting (SLM) 3D printing technology have made it widely used in various fields. With the continuous development and innovation of technology, SLM 3D printing technology is expected to continue to promote the development and progress of various industries in the future.
Yes, Selective Laser Melting (SLM) 3D printing technology is capable of producing functional parts with similar mechanical properties to traditionally manufactured parts. This advanced manufacturing technology uses high-energy laser beams to melt metal powder layer by layer to build complex three-dimensional structures. By precisely controlling the scanning path and power of the laser beam, SLM 3D printing can achieve precise control of the internal structure of the part, resulting in mechanical properties comparable to traditional manufacturing methods.
SLM 3D printing technology offers many advantages over traditional manufacturing methods. First, it can achieve rapid prototyping and small batch production, greatly shortening the product development cycle. Secondly, due to its layer-by-layer manufacturing characteristics, SLM 3D printing can produce very complex geometries, while traditional manufacturing methods are often limited by process limitations. In addition, SLM 3D printing can also maximize material utilization and reduce waste and costs.
In terms of functionality, SLM 3D printing technology can produce parts with high strength, high hardness and wear resistance. These parts can be used in various applications such as aerospace, automotive manufacturing, medical devices, etc. For example, in the aerospace field, SLM 3D printing technology can produce lightweight and high-strength engine parts to improve aircraft performance and fuel efficiency. In the field of automobile manufacturing, SLM 3D printing technology can produce complex-shaped engine parts and body structural parts, improving the safety and fuel economy of automobiles.
In short, the emergence of SLM 3D printing technology has brought revolutionary changes to the manufacturing industry. Not only can it produce functional parts with similar mechanical properties to traditionally manufactured parts, it also offers advantages such as rapid prototyping, manufacturing of complex geometries and maximizing material utilization. With the continuous development of technology and the expansion of applications, SLM 3D printing technology will play an increasingly important role in various fields.
Selective laser melting (SLM) 3D printing can achieve a variety of surface finishes from smooth to rough through post-processing techniques such as sandblasting or polishing. These post-processing technologies play a vital role in the 3D printing process, and they can significantly improve the surface quality and appearance of the printed parts.
First, sandblasting is a common post-processing method that removes excess material and imperfections from the surface of a print by spraying fine abrasive particles at high speeds. This technology can effectively improve the surface roughness of the printed part without damaging its structure. The surface of the printed parts after sandblasting presents an effect similar to frosted glass, which is both beautiful and has certain anti-slip properties.
Secondly, polishing is a more delicate post-processing technique that uses a soft polishing cloth and abrasive particles to repeatedly rub the surface of the print to remove tiny bumps and imperfections. The surface of the polished print is as smooth as a mirror, with good gloss and tactile feel. In addition, polishing can improve the scratch resistance of the print and extend its service life.
In addition to sandblasting and polishing, there are several other post-processing techniques that can be used to improve the surface quality of SLM 3D prints. For example, electrochemical polishing can achieve a uniform polishing effect by applying voltage in an electrolyte solution to cause charged abrasive particles to flow on the surface of the printed part. Another method is anodizing, which forms an aluminum oxide film on the surface of the print, thereby improving its corrosion and wear resistance.
In summary, by using different post-processing techniques, SLM 3D printing can achieve various surface finishes from smooth to rough. These technologies not only improve the appearance quality of your prints, but also improve their performance and longevity. Therefore, when choosing SLM 3D printing, post-processing technology should be reasonably selected and applied based on actual needs and application scenarios.
Selective laser melting (SLM) 3D printing technology has significant advantages over traditional manufacturing methods. First, it can significantly reduce material waste. In the traditional manufacturing process, a large amount of waste and residual materials are often generated, which not only increases production costs, but also puts certain pressure on the environment. However, SLM 3D printing technology maximizes the use of raw materials and reduces the generation of waste through precise lamination and melting processes.
Secondly, SLM 3D printing technology can also reduce energy consumption. Traditional manufacturing methods often require large amounts of energy to drive machinery and heat processes. SLM 3D printing technology achieves a more energy-efficient production process by using efficient lasers to melt metal powder. This efficient use of energy not only reduces production costs, but also helps reduce negative environmental impacts.
To sum up, SLM 3D printing technology has obvious advantages in reducing material waste and energy consumption compared with traditional manufacturing methods. Its eco-friendly properties make it a more sustainable and preferable option. As people's awareness of environmental protection continues to increase, SLM 3D printing technology is expected to be more widely used in the future, bringing greater change and development to the manufacturing industry.
Common question in SLM 3D Printing Additive Manufacturing
Yes, SLM 3D printing can be used for mass production, particularly for complex or low-volume parts.
In the selective laser melting (SLM) 3D printing process, some specialized software tools are usually used. These software tools include computer-aided design (CAD) software, simulation software, and slicing software.
First, computer-aided design (CAD) software is an integral part of the SLM 3D printing process. It helps designers create and edit 3D models to prepare them for the subsequent printing process. Through CAD software, designers can easily rotate, scale and translate models to meet different design needs. In addition, CAD software can be seamlessly integrated with other software tools, such as simulation software and slicing software, to automate the entire printing process.
Secondly, simulation software also plays an important role in SLM 3D printing. Simulation software can simulate various physical phenomena during the printing process, such as the formation of molten pools, melting and solidification of metal, etc. By accurately simulating these phenomena, simulation software can help designers optimize printing parameters to improve print quality and efficiency. In addition, simulation software can also predict problems that may occur during the printing process, such as stress concentration, deformation and defects, etc., thereby helping designers adjust the design plan in a timely manner.
Finally, slicing software is another key tool in the SLM 3D printing process. Slicing software can cut the 3D model into a series of thin slices and generate corresponding control instructions for the printing process of each layer. These control instructions include laser power, scanning speed and scanning path, etc., which determine the melting and solidification behavior of the metal during the printing process. The slicing software can also adjust slicing parameters according to actual printing conditions to achieve the best printing effect.
In short, software tools such as CAD software, simulation software, and slicing software play a vital role in the SLM 3D printing process. They not only help designers create and optimize 3D models, but also automate and intelligentize the printing process, thereby improving printing quality and efficiency.
To ensure personal safety when performing certain activities or jobs, we need to take some precautions. First of all, it is very important to wear protective glasses and protective clothing. These gears can effectively protect our eyes and body from possible injuries. For example, if we conduct chemical experiments in a laboratory, protective glasses can prevent chemicals from splashing into the eyes and causing damage; and protective clothing can prevent chemicals from coming into contact with the skin and avoid skin burns or other injuries.
Secondly, ensuring good ventilation is also an important safety measure. In some working environments, harmful gases or vapors may be produced. Without good ventilation, these harmful substances may cause harm to the human body. Therefore, we need to ensure that the work area has adequate ventilation facilities to discharge harmful gases in a timely manner.
Finally, we need to follow the manufacturer's instructions. Whether using mechanical equipment or chemicals, manufacturers provide detailed instructions and safety tips. We need to read and understand these instructions carefully to ensure that we use the product correctly and avoid accidents.
The cost of selective laser melting (SLM) 3D printing varies based on a number of factors, including the size and complexity of the part, the materials used, and the cost of the machine and software. First of all, the size and complexity of the parts are one of the important factors that affect the cost. If the part is larger or has complex geometry, the time and technical requirements required to print increase, leading to higher costs. Conversely, small and simple parts typically require less time and resources to print and therefore cost less.
Secondly, the materials used also have an impact on the cost. SLM 3D printing can use various metal materials, such as titanium alloy, stainless steel, aluminum alloy, etc. Different materials also have different prices, so choosing different materials will have a direct impact on costs. Additionally, some specialty materials may require special handling and post-processing steps, which can also increase costs.
Finally, the cost of machines and software is also one of the factors affecting the cost of SLM 3D printing. SLM 3D printers are more expensive and vary depending on their performance and features. In addition, using high-quality 3D modeling software and design tools also requires a certain fee. These costs may include purchasing software licenses, training and usage fees, etc.
To summarize, the cost of SLM 3D printing is affected by a variety of factors, including the size and complexity of the part, the materials used, and the cost of the machine and software. When carrying out SLM 3D printing, these factors need to be comprehensively considered and reasonable cost control based on specific needs.
SLM 3D printing lead times can vary depending on the size and complexity of the part, but are typically faster than traditional manufacturing processes.
SLM 3D printing is an advanced manufacturing technology that uses laser beams to melt and solidify metal powder layer by layer to create complex three-dimensional objects. SLM 3D printing offers many advantages over traditional manufacturing methods, one of which is shorter lead times.
First, SLM 3D printing does not require molds or models to make parts. In contrast, traditional manufacturing methods often require making molds or models, which increases production cycle time and cost. SLM 3D printing can generate parts directly from computer-aided design (CAD) files, greatly reducing time and resource consumption in the manufacturing process.
Secondly, SLM 3D printing can process multiple parts simultaneously. Traditional manufacturing methods typically build parts one by one, meaning each part requires separate preparation and machining processes. SLM 3D printing can process multiple parts at the same time, greatly improving production efficiency and delivery speed.
In addition, SLM 3D printing can also be customized and personalized production according to needs. Traditional manufacturing methods usually require large-scale production of parts with the same specifications, which may not be suitable for some special needs or small batch production. SLM 3D printing can be customized according to customer requirements. Whether it is size, shape or material selection, it can be flexibly adjusted to meet the needs of different customers.
However, it should be noted that the delivery time of SLM 3D printing is still affected by some factors. For example, the size and complexity of the part can affect the time and process of printing. Larger parts may take longer to print, while complex geometries may require more support structures and post-processing steps. Therefore, these factors need to be taken into consideration and a reasonable assessment made when determining delivery time.
Overall, SLM 3D printing, as an advanced manufacturing technology, has shorter lead times. It increases production efficiency and flexibility with the ability to generate parts directly from CAD files, process multiple parts simultaneously, and customize production. However, delivery time is still affected by the size and complexity of the part, so reasonable evaluation and planning are required in practical applications.
Selective laser melting (SLM) 3D printing is a reliable manufacturing process that has been proven in practice for many years and is widely used in various industries. This advanced manufacturing technology builds three-dimensional objects with a high degree of accuracy and customizability by using high-energy laser beams to melt metal powder layer by layer.
First of all, SLM 3D printing technology plays an important role in the aerospace field. Due to its ability to produce complex geometries and lightweight structures, it is widely used to manufacture aerospace engine parts, spacecraft structures and components, etc. This technology not only improves production efficiency, but also reduces weight and cost, giving the aerospace industry a huge competitive advantage.
Secondly, SLM 3D printing is also widely used in the medical field. It provides doctors and surgical teams with better surgical planning and training tools due to its ability to create high-precision medical devices and mannequins. In addition, SLM 3D printing can also manufacture personalized prosthetics and orthotics to provide patients with more comfortable and effective treatment options.
In addition, SLM 3D printing also plays an important role in the field of automobile manufacturing. It provides automakers with higher production efficiency and quality control capabilities due to its ability to produce complex and strong automotive parts such as engine mounts, braking systems and body structures. In addition, SLM 3D printing can also achieve rapid prototyping and design iteration, speeding up the automotive development cycle.
Finally, SLM 3D printing also shows great potential in the energy field. It provides new solutions for the development of renewable energy due to its ability to create high-efficiency solar panels and wind turbine blades. In addition, SLM 3D printing can also produce efficient fuel cells and energy storage devices, promoting innovation and development in the energy field.
In short, SLM 3D printing, as a reliable manufacturing process, has been widely used in multiple industries. Its high precision, customizability and flexibility make it an important tool in the manufacturing industry, bringing huge development opportunities to all walks of life. With the continuous advancement of technology and the expansion of applications, SLM 3D printing will continue to play an important role in various fields and promote innovation and progress in the manufacturing industry.
Yes, Selective Laser Melting (SLM) 3D printing technology can create hollow parts by using infill patterns or internal support structures. This technology uses a high-energy laser beam to melt metal powder layer by layer to create the desired three-dimensional shape. When manufacturing hollow parts, this can be achieved by controlling the filling pattern or adding internal support structures.
Fill mode refers to filling metal powder into designated areas to create a transition between solid and hollow parts. By adjusting the fill pattern, you can control the shape, size, and wall thickness of the hollow portion. For example, you can use grid fill mode to create hollow parts with complex geometries, or continuous fill mode to make hollow parts with uniform wall thickness.
Internal support structures refer to temporary support structures added during the 3D printing process to maintain the shape and stability of hollow parts. These support structures are typically made from dissolvable materials, such as water-soluble polymers or degradable materials. After printing is complete, the support structure can be dissolved or removed to create the desired hollow part.
By using infill patterns or internal support structures, SLM 3D printing technology enables the manufacture of highly complex hollow parts. This technology has the advantages of high precision, high quality and high efficiency, and is suitable for various application fields, such as aerospace, automobile manufacturing and medical devices.
Although selective laser melting (SLM) 3D printing technology has shown great potential in many fields, it also has some limitations. First, there are limits to the size of parts that this technology can produce. Because SLM 3D printing creates parts by stacking metal powder layer by layer, the large parts it produces may be limited by the size and stability of the equipment.
Secondly, the material selection for SLM 3D printing is also relatively limited. Currently, most SLM 3D printers mainly use metal materials such as titanium alloy, cobalt-chromium alloy, and stainless steel for printing. Although these materials have a wide range of applications in aerospace, medical and other fields, for parts that require the use of other types of materials, such as plastics or ceramics, SLM 3D printing may not be able to meet the demand.
Finally, for some parts, complex post-processing is required after SLM 3D printing. This is because during the printing process, the metal powder can form irregular shapes or leave voids inside the part. In order to ensure the quality and performance of the parts, printed parts often need to be heat treated, grinded, or other forms of post-processing. Not only does this increase production costs, it may also affect the final performance of the part.
Yes, selective laser melting (SLM) 3D printing technology is indeed capable of manufacturing parts with complex geometries. These parts may be difficult or impossible to produce using traditional manufacturing methods. By using SLM 3D printing technology, we can precisely control the shape and size of parts, allowing for highly complex and detailed designs. This technology can not only improve production efficiency, but also reduce production costs, bringing revolutionary changes to the manufacturing industry.
Selective laser melting (SLM) 3D printing technology offers higher precision, better material properties and greater design freedom than other 3D printing technologies, such as fused deposition modeling (FDM) or stereolithography (SLA) Spend.
First, SLM 3D printing technology enables higher precision during the manufacturing process. SLM can achieve micron-level precision by using a laser beam to melt metal powder layer by layer to build objects. In comparison, traditional 3D printing technologies such as FDM and SLA can often only achieve millimeter-level accuracy. This high precision makes SLM 3D printing technology advantageous in manufacturing complex geometries and details, making it suitable for applications that require a high degree of accuracy, such as aerospace, medical devices, and mold manufacturing.
Secondly, SLM 3D printing technology can provide better material properties. Since SLM uses metal powder as raw material, the printed objects have high strength, hardness and wear resistance. This makes SLM 3D printing technology advantageous in manufacturing high-performance parts and tools, such as aerospace engine parts, automotive molds, and medical implants. In comparison, traditional 3D printing technologies such as FDM and SLA can usually only use plastic materials, which have relatively low strength and wear resistance.
Finally, SLM 3D printing technology provides greater design freedom. Because SLM can precisely control the melting process of the laser beam, complex geometric shapes and structural designs can be achieved. This gives designers greater flexibility to create unique products and prototypes without the limitations of traditional manufacturing processes. In contrast, traditional 3D printing technologies such as FDM and SLA often require the use of support structures to maintain object stability, which limits design flexibility.
To sum up, SLM 3D printing technology has higher precision, better material performance and greater design freedom than other 3D printing technologies. These advantages make SLM 3D printing technology promising in many fields, especially in the manufacturing of parts that require high precision and high performance.