Table of Contents:
- Introduction
- Manufacturing Processes of Precision Machined Components
- Materials Used in Precision Machined Components
- Applications of Precision Machined Components
- Factors to Consider When Choosing a Precision Machined Components Manufacturer
- Top Precision Machined Components Manufacturers
- Conclusion
-
1.Introduction
Precision machined components are parts that are manufactured to exact specifications, using advanced machining techniques and high-quality materials. These components are used in a wide variety of industries, including aerospace, medical, automotive, electronics, and many more. Their importance cannot be overstated, as precision machined components are often critical to the functioning and safety of machines, devices, and products.
Precision machined components may be produced using various machining processes, such as CNC machining, turning, milling, grinding, and more. Each process has its own benefits and limitations, and the choice of machining method depends on the specific needs and requirements of the project.
The materials used to produce precision machined components must be carefully selected based on their properties, such as strength, weight, corrosion resistance, and temperature resistance. Metals, plastics, ceramics, and composites are all commonly used materials in precision machining.
-
2.Manufacturing Processes of Precision Machined Components
CNC Machining:
CNC machining is a computer-controlled manufacturing process that creates high-precision parts. The process involves generating a Computer-Aided Design (CAD) of the desired component, then using programmed software to control the movement of a variety of cutting tools, which in turn shape and cut a raw material into its finished form. CNC machines are capable of producing parts with very tight tolerances, with a high level of accuracy and repeatability.
Turning:
Turning is a machining process that involves removing layers of material from a workpiece to create a cylindrical shape. This process is typically accomplished using a lathe, a machine that spins the workpiece while a cutting tool removes material from the exterior. Turning is often used to produce parts such as shafts, bushings, sleeves, and other cylindrical shapes.
Grinding:
Grinding is a machining process that utilizes an abrasive wheel or abrasive material to remove small amounts of material from a workpiece. This process is used to create smooth and precise surfaces on a variety of materials, including metals, plastics, and ceramics. Precision grinding can produce parts that meet extremely tight tolerances and surface finish requirements.
Milling:
Milling is a process that uses a rotating cutting tool to remove material from a workpiece to create a part with a specific shape. Milling is used to create complex parts with intricate features such as contours, holes, and grooves. Milling machines are capable of producing parts with very tight tolerances.
Others:
There are several other machining processes that are often used to create precision machined components, including drilling, honing, and broaching. Drilling is used to create holes in a workpiece, honing is used to produce an ultra-smooth surface finish, and broaching is used to create complex contours or profiles in parts.
In summary, precision machined components can be manufactured using several different machining processes, each with their own strengths and limitations. Selecting the most appropriate machining process for a specific project is crucial to achieve the desired quality and performance of the precision machined component.
-
3.Materials Used in Precision Machined Components
Metals:
Metals are commonly used to produce precision machined components due to their strength, durability, and excellent conductivity of electricity and heat. The most commonly used metals in precision machining are aluminum, brass, copper, stainless steel, and titanium. Metals can be machined at high speeds and can produce high-quality finished products with excellent tolerance levels.
Plastics:
Plastics are often used to produce precision machined components due to their lower density, low cost, and high strength-to-weight ratio. Plastics can be machined easily and can produce high-quality finished products. Some common plastics used in precision machining are acetal, nylon, and polycarbonate.
Ceramics:
Ceramics are used to produce precision machined components when high-temperature or wear-resistant properties are required. Ceramics are very hard and brittle materials that offer excellent resistance to wear, corrosion, and temperature changes. Common ceramics used to produce precision machined components are zirconia, alumina, and silicon nitride.
Composites:
Composites are made up of two or more materials and are commonly used to produce precision machined components with specific properties. The combination of the two or more materials can provide strength, durability, and resistance to wear, heat, and corrosion. Some examples of composites used in precision machining are carbon fiber, fiberglass, and Kevlar.
In summary, precision machined components can be manufactured using a variety of materials, each offering unique properties and characteristics. The selection of the material used depends on the specific requirements of the application, such as cost, strength, wear-resistance, and temperature resistance. Choosing the right material for a specific application is crucial to produce high-quality precision machined components.
-
4.Applications of Precision Machined Components
Aerospace:
The aerospace industry requires high-precision machined components to manufacture aircraft and spacecraft components such as engines, landing gear, flight controls, and other critical systems. These precision components are essential to ensure the safe and reliable operation of aircraft and spacecraft.
Medical:
Precision machined components are used in the medical industry for a variety of applications, such as producing implants, surgical instruments, and diagnostic equipment. The medical industry requires highly precise and reliable components to ensure patient safety and device efficacy.
Automotive:
The automotive industry relies heavily on precision machined components for manufacturing various automotive parts, such as engines, transmissions, and chassis components. High-quality precision components improve vehicle performance and reliability, ensuring that vehicles meet industry standards for efficiency and safety.
Electronics:
Precision machined components are widely used in the electronics industry, from manufacturing computer parts, smartphones, and other consumer electronics to creating large-scale electronic systems such as satellites and radar systems. The demand for high-quality and high-precision components has increased significantly in recent years, as the global demand for technology and communication systems increases.
Others:
Precision machined components are used in a wide array of other industries, including the defense sector, oil and gas, and industrial equipment manufacturing. These industries require precision components to ensure reliable and efficient operation of their systems.
In summary, precision machined components are vital to many industries and applications, requiring high levels of precision, durability, and reliance. Industries like aerospace, medical, automotive, electronics, defense, and many others depend on precision machined components to produce reliable and efficient products.
-
5.Factors to Consider When Choosing a Precision Machined Components Manufacturer
Quality Control:
When selecting a precision machined components manufacturer, it’s essential to ensure they have a robust quality control process in place, including in-process inspections, final inspections and testing, and documentation. The manufacturer should have a system of identifying and correcting defects quickly.
Certifications and Standards:
Certification and compliance with industry standards are crucial when selecting a precision machined components manufacturer. An excellent manufacturer would comply with various quality management systems (QMS) like ISO9001 and AS9100, which demonstrate that they are following a rigorous quality program.
Experience in Industry:
The experience of the manufacturer in the industry and in producing precision machined components is also an essential factor to consider. Having experience means they have a vast knowledge of the different materials, machines, techniques, and best practices which helps to ensure the quality of the components.
Technical Capabilities:
The technical capabilities of the manufacturer, including the type of equipment they use and their expertise in different machining processes is another element to consider. A good manufacturer should have the latest equipment and expertise in various types of machining processes to produce high-quality components efficiently.
Customer Service:
The level of customer service provided by the manufacturer is also an essential factor when choosing. A good manufacturer will maintain open communication with their customers, treat them with respect, and ensure their needs are well taken care of.
In summary, selecting the right precision machined components manufacturer can be critical to ensuring the success of a project. Factors to consider include quality control, certifications and standards, experience in the industry, technical capabilities, and customer service. Understanding these factors can help in choosing the best manufacturer that can meet the project needs and requirements.
-
6.Top Precision Machined Components Manufacturers
There are many excellent precision machined components manufacturers worldwide that offer high-quality components to a range of industries. Here is a brief overview of some of the top manufacturers.
- ABBOTT WORKHOLDING:
Abbott Workholding is a California-based manufacturer specializing in workholding and fixturing solutions for precision machining. Their product offerings include precision chucks, custom fixtures, and automation systems. Strengths: technically capable, cost-effective solutions. Weaknesses: narrow product range. - ARMSTRONG RM CORPORATION:
Armstrong RM Corporation is a Washington-based manufacturer that produces precision machined components for aerospace, defense, and medical industries. Their product offerings include gears, shafts, and other custom components. Strengths: technical capabilities, quality control. Weaknesses: limited industry presence. - APEX MICROTECHNOLOGY:
Apex Microtechnology is a Texas-based manufacturer specializing in power analog components, including amplifiers and voltage converters. Their components are used in high-performance applications, such as medical devices, aerospace, and defense systems. Strengths: technical expertise, high-performance solutions. Weaknesses: narrow product range. - BRAUN MANUFACTURING CO.:
Braun Manufacturing Co. is a Pennsylvania-based manufacturer that provides custom metal fabrication and machining solutions to various industries, including aerospace, defense, and medical. Their product offerings include precision machined components and assemblies, weldments, and custom metal fabrication. Strengths: diverse capabilities, experience in various industries. Weaknesses: limited specializations. - FERGUSON PRODUCTION, INC.:
Ferguson Production, Inc. is a Wisconsin-based manufacturer specializing in precision machined components for industries such as aerospace, medical, and defense. Their product offerings include parts and assemblies, high-performance machining, and prototyping solutions. Strengths: technical capabilities, customer-centric approach. Weaknesses: limited production capacity.
In summary, there are many top precision machined components manufacturers that offer high-quality components to various industries. Each manufacturer has its strengths and weaknesses, so choosing the best one depends on the project needs and requirements.
Click on the V1 Prototype website to gain more information.
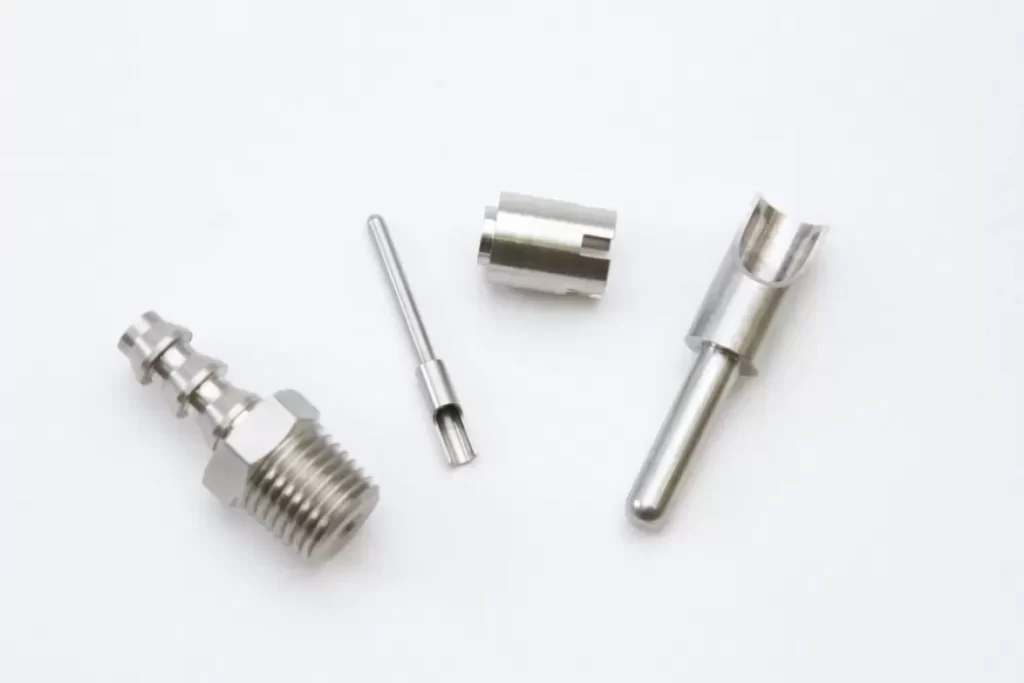
-
7.Conclusion
Recap of Key Points:
Precision machined components are essential parts of modern manufacturing and are used in a wide range of industries, including aerospace, medical, automotive, electronics, and others. CNC machining, turning, grinding, milling, and other machining processes can be used to produce precision components. Materials commonly used in precision machining include metals, plastics, ceramics, and composites. When selecting a precision machined components manufacturer, factors to consider include quality control, certifications, experience in the industry, technical capabilities, and customer service.
The Future of Precision Machined Components Manufacturing:
The future of precision machined components manufacturing is highly promising due to the increasing demand for high-quality and high-precision components. The use of automation and advanced technology, such as artificial intelligence and additive manufacturing, is expected to revolutionize the precision machining industry in the coming years. These technologies will mean faster production times, increased precision, and more efficient processes, which will ultimately lead to lower costs and higher-quality components. In summary, precision machining is a constantly evolving industry that plays a crucial role in modern manufacturing, and the future looks bright for precision machined components manufacturing.