3D printing technology has revolutionized the manufacturing industry, enabling manufacturers to create complex parts and structures with ease. This technology has opened up new possibilities, allowing individuals to create anything they want, from simple objects to complex designs that were once impossible to produce.
3D printing technology has been in development for more than 30 years and although it is not widespread, it is slowly making its way into human life and can be found in more and more fields. 3D printing technology has many advantages such as saving time, increasing efficiency and reducing costs, and will certainly be used in a wide range of fields in the future. Nowadays, 3D printing technology has been used in aerospace technology, medical field, electronics industry, automotive industry and so on.
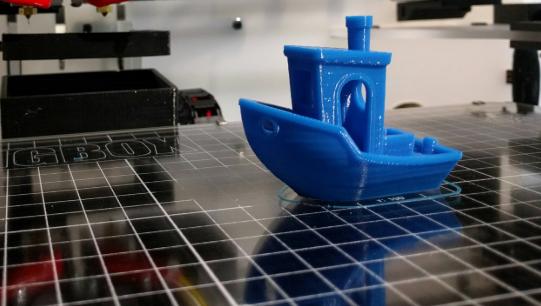
Within the aerospace sector, 3D printing technology is used to make parts for flying machines, facilitating weight reduction in aircraft; 3D printed parts in civil aviation aircraft can reduce the structural mass of the aircraft, the service life of the aircraft is extended and manufacturing costs are saved.
In the medical field, a research team has already developed and produced a low-cost method of making a three-dimensional model of the liver that can see the internal structure of blood vessels and other parts. 3D printed skulls, 3D printed spines, 3D printed hearts, 3D printed palms… 3D printing technology is slowly penetrating into the medical field and will certainly play a vital role in the future.
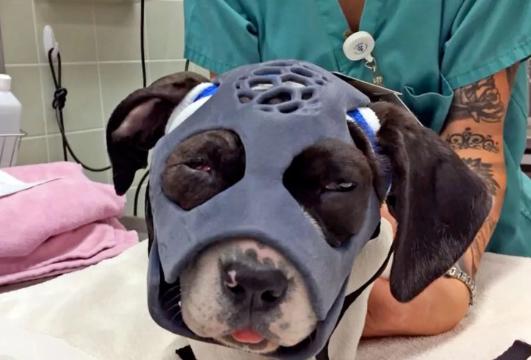
The world's first 3D printed car was designed and manufactured by Rock Auto in the USA when it opened a new chapter in the automotive industry. It took just 44 hours to print a car and complete the composition using 3D printing technology. The body is manufactured from black plastic and wrapped in layers of carbon fibre, adding strength to the car, a more spontaneous look, environmentally friendly materials and cost savings.
The 3D printing process is divided into three parts: 3D design, slicing and processing, and finished printing. The design process for 3D printing is to first model the car through computer modelling software and then "partition" the completed 3D model into layer-by-layer sections, i.e. slices, which guide the printer to print layer-by-layer. The printer reads the cross-sections from the file, prints them out layer by layer using liquid, powder or sheet materials, and then bonds the layers together in various ways to create a solid. This technology is unique in that it can be used to create objects of any shape. Whereas traditional manufacturing techniques such as injection moulding can produce large quantities of polymer products at a low cost, 3D printing can produce relatively small quantities of products faster, more flexibly and at a lower cost. A single desktop-sized 3D printer can meet the needs of a designer or concept development team to produce a model. Some technologies can print with multiple materials at the same time. Some technologies also use supports in the printing process, for example, when printing objects that have an upside-down shape, something easily removable (such as a soluble material) is used as a support.
What is the need of 3D printing technology?
The need for 3D printing technology is vast, from prototyping to final production. Traditional manufacturing processes such as injection molding or CNC machining require time, manpower, and tooling, leading to significant costs. However, 3D printing eliminates the need for tooling, allowing manufacturers to reduce costs and quickly produce parts. Additionally, 3D printing technology allows for customization and the creation of complex geometries, giving designers and engineers more freedom to create products tailored to specific needs.
What is the goal of 3D printing?
The goal of 3D printing is to create a manufacturing process that is faster, more efficient, and cost-effective. The technology allows for the production of complex geometries and shapes that traditional manufacturing methods are unable to produce. Additionally, 3D printing enables the creation of customizable parts while eliminating the need for tooling, allowing for quicker, cost-effective production. The end goal is to provide manufacturers with a tool to create products that are customized, efficient, and cost-effective while eliminating the design or production limitations that come with traditional manufacturing methods.
How do you 3D print anything you want?
3D printing technology has made it possible to create anything you want, from simple objects to complex designs. The process can be broken down into several steps:
Step 1: Design the Part
The first step in 3D printing is designing a 3D model of the object you want to create. The model is usually created using 3D design software, allowing for the creation of complex geometries or structures. The software outputs the file format required for 3D printing, such as .stl or .obj.
Step 2: Prepare the 3D Printer
The second step in 3D printing is to prepare the 3D printer. Typically, the printer is loaded with the filament or resin used for printing, and the print bed is leveled to ensure the printer can create a smooth, even layer.
Step 3: Slice the Model
The third step is slicing the 3D model into layers using slicing software. The software takes the 3D model and slices it into thin, virtual layers, creating a roadmap for the printer to follow.
Step 4: Print the Object
The fourth step is printing the 3D model. The printer reads the sliced file and begins printing the object layer by layer. This process repeats until the printer completes building the object.
Step 5: Remove and Finish the Object
The fifth and final step is removing and finishing the object. After the object is printed, it is removed from the 3D printer and any support structures that were used during printing are removed. A final inspection is carried out, and the object can be finished using techniques such as sanding, painting, or polishing to ensure it meets the desired final specifications.
Conclusion
The possibilities of 3D printing technology are endless and have opened up new opportunities for individuals and businesses alike. By eliminating the design and production limitations of traditional manufacturing methods, 3D printing offers unmatched flexibility, speed, and control, allowing for the production of customized, complex designs with ease. As technology continues to advance, the potential of 3D printing will become increasingly profound, disrupting the traditional manufacturing industry and creating new opportunities for product creation, customization, and innovation.