Table of Contents:
- Introduction
- Types of Injection Molding Lifters
- Design Considerations for Injection Molding Lifters
- Injection Molding Lifter Operation
- Applications of Injection Molding Lifters
- Conclusion
-
1.Introduction
Injection molding lifters are mechanical components that are used to lift or move specific features of a molded part during the ejection process. They are an essential part of the injection molding process, allowing manufacturers to create complex parts with undercuts, threads, and other intricate features.
Lifters are critical in injection molding because they help prevent damage to the molded part during the ejection process. Without lifters, certain features of a molded part would be unable to be ejected from the mold, resulting in damaged parts and costly production delays. By using lifters, manufacturers can ensure that the ejection process is smooth and efficient, while also achieving the desired level of precision and accuracy in the molded part.
In summary, injection molding lifters are an integral part of the injection molding process, providing the necessary mechanical movement and control to create complex parts with precision and accuracy. They play a crucial role in ensuring the quality of the final product, reducing production costs, and increasing manufacturing efficiency.
-
2.Types of Injection Molding Lifters
There are four main types of injection molding lifters: fixed core lifters, angle pin lifters, side action lifters, and stripper plate lifters. Each type of lifter is designed for specific applications and features unique advantages.
- Fixed Core Lifters:Fixed core lifters are the simplest type of lifter and are typically used when a feature of a molded part needs to be moved in a straight line. They consist of a core pin that is fixed in place and a lifter that moves along the length of the pin. The lifter is typically shaped like a wedge or ramp and is used to lift a specific feature of the molded part during the ejection process.
- Angle Pin Lifters:Angle pin lifters are used when a feature of a molded part needs to be moved at an angle. They consist of a core pin that is fixed in place and an angled lifter that moves along the length of the pin. The angled lifter is used to lift a specific feature of the molded part at an angle, allowing it to be ejected from the mold without damage.
- Side Action Lifters:Side action lifters are used to create undercuts in the molded part. They consist of a set of plates or cams that move horizontally or vertically to create the undercut feature. Side action lifters are commonly used in the production of gears, threads, and other parts that require undercuts.
- Stripper Plate Lifters:Stripper plate lifters are used to strip the part from the mold. They consist of a set of plates or pins that move perpendicular to the mold opening to push the part off the mold. Stripper plate lifters are typically used in the production of parts with large flat surfaces or with deep draw features.
In summary, each type of injection molding lifter has its unique advantages and is used for specific applications. The selection of the appropriate type of lifter depends on the design of the part and the specific ejection requirements. By understanding the differences between each type of lifter, manufacturers can optimize their injection molding process and produce high-quality parts at a lower cost.
-
3.Design Considerations for Injection Molding Lifters
When designing an injection molding lifter, there are several key considerations to keep in mind. These considerations include lifter design guidelines, material selection for lifters, and lifter placement and size.
- Lifter Design Guidelines:When designing a lifter, it is essential to follow specific design guidelines to ensure that the lifter functions correctly. Some key design guidelines to consider include ensuring that the lifter is properly aligned with the molded feature, making sure that the lifter has enough clearance to move freely, and designing the lifter to withstand the forces exerted during the ejection process.
- Material Selection for Lifters:The material used for the lifter is another critical consideration. The lifter material should be strong enough to withstand the forces exerted during the ejection process, but it should also be able to resist wear and tear from repeated use. Common materials used for lifters include hardened steel, aluminum, and high-strength plastics.
- Lifter Placement and Size:The placement and size of the lifter are also essential considerations. The lifter must be placed in the correct location to ensure that the molded feature is properly ejected from the mold. The size of the lifter must also be carefully selected to ensure that it has enough strength to lift the feature without damaging the part.
In summary, the design of injection molding lifters requires careful consideration of various factors. Manufacturers must follow specific design guidelines, select the appropriate material for the lifter, and carefully consider the placement and size of the lifter. By doing so, they can ensure that the injection molding process is optimized for maximum efficiency and that high-quality parts are produced at a lower cost.
-
4.Injection Molding Lifter Operation
The operation of injection molding lifters involves several steps, including lifter activation, addressing common issues and troubleshooting, and maintenance and care.
- Lifter Activation:Lifters are typically activated during the ejection process of the injection molding cycle. Once the molded part has cooled and solidified, the mold opens, and the lifter is engaged to lift or move a specific feature of the part. The lifter is designed to provide the necessary mechanical movement and control to ensure that the molded part is properly ejected without damage.
- Common Issues and Troubleshooting:Despite their importance, lifters can encounter several common issues during operation, including binding, sticking, and wear and tear. To troubleshoot these issues, manufacturers can examine the lifter for signs of damage, adjust the position or size of the lifter, or replace the lifter altogether. It is also essential to regularly inspect and maintain the lifter to prevent issues from occurring in the first place.
- Maintenance and Care of Lifters:Proper maintenance and care of injection molding lifters are crucial to ensure their longevity and effectiveness. This includes regularly inspecting the lifter for wear and tear, cleaning the lifter to prevent debris buildup, and lubricating the lifter to reduce friction and wear. By properly maintaining and caring for the lifters, manufacturers can reduce downtime and ensure that their injection molding process runs smoothly.
In summary, the operation of injection molding lifters involves lifter activation during the ejection process, addressing common issues and troubleshooting, and maintenance and care. By understanding these aspects of lifter operation, manufacturers can optimize their injection molding process and produce high-quality parts at a lower cost.
-
5.Applications of Injection Molding Lifters
Injection molding lifters are an essential component of the injection molding process and are used in a wide range of applications. Here are some examples of products that require lifters and the benefits of lifters in injection molding.
- Examples of Products that Require Lifters:Lifters are commonly used in the production of products that have undercuts or other complex features that require special ejection techniques. Examples of products that require lifters include automotive parts, medical devices, consumer products, and electronic components.
- Benefits of Lifters in Injection Molding:Lifters offer several key benefits in the injection molding process. These benefits include the ability to produce parts with complex features that would otherwise be impossible to mold, reducing the need for secondary operations, improving part quality by reducing the risk of damage during ejection, and increasing the efficiency and speed of the injection molding process.
In summary, injection molding lifters are used in a wide range of applications and provide several key benefits in the injection molding process. By using lifters, manufacturers can produce high-quality parts with complex features at a lower cost and with greater efficiency.
If you need about Plastic Injection Molding Services,You can click on the V1 Prototype website to find it.
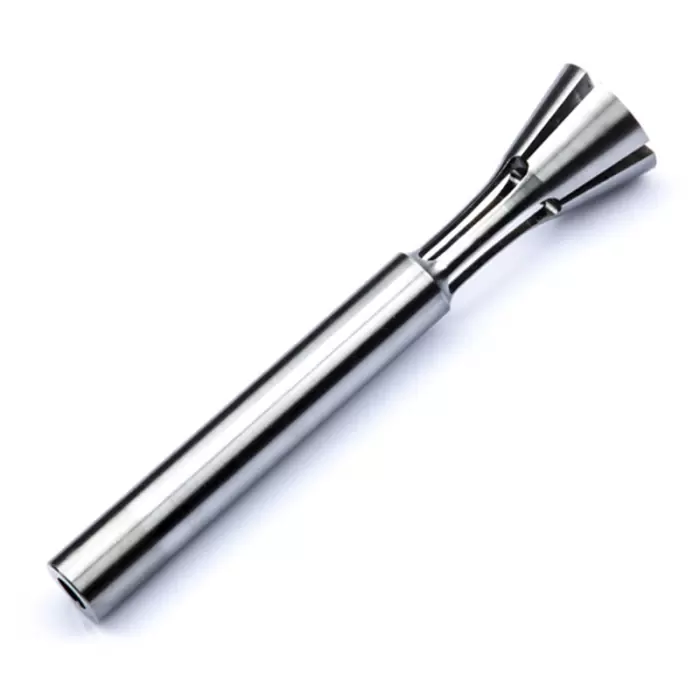
-
6.Conclusion
In conclusion, injection molding lifters play a critical role in the injection molding process and are essential for producing high-quality parts with complex features. The proper design, material selection, placement, and maintenance of lifters are crucial considerations to ensure the success of the injection molding process.
Some key points to remember about injection molding lifters include the different types of lifters, design considerations, lifter activation, troubleshooting common issues, and the benefits of using lifters in injection molding. By understanding these key points, manufacturers can optimize their injection molding process and produce high-quality parts at a lower cost.
As for future developments in injection molding lifters, it is expected that the demand for more complex and intricate parts will increase, leading to the need for more advanced and innovative lifter designs. Additionally, advancements in materials science and manufacturing technology will likely lead to the development of new lifter materials and manufacturing techniques. These advancements will undoubtedly lead to improvements in the injection molding process and enable manufacturers to produce even more complex and high-quality parts.