Custom Plastic Injection Molding Services
V1 focus on mold manufacturing processing and plastic injection molding service, molding products mainly used in Automotive, Electronics, Appliance, Medical, Housewares industries.
Plastic Injection Molding Services
V1 has been designing and building plastic injection mould since 2006, using innovative design techniques, state-of-the-art technology, exceptional craftsmanship and advanced facilities to guarantee the high quality molds and parts for our worldwide customers.
We offer a variety of tooling services including: Prototyping Mold,Multi-shot molds/2K molds and Insert overmolding. Our customers are mainly in Automotive, Electronics, Appliance, Medical, Housewares industries.
With business expanding these years, we set up offices and overseas team in European and US countries such as UK, Germany,Slovakia, Mexico etc to continually meet or exceed our customers expectations and requirements.
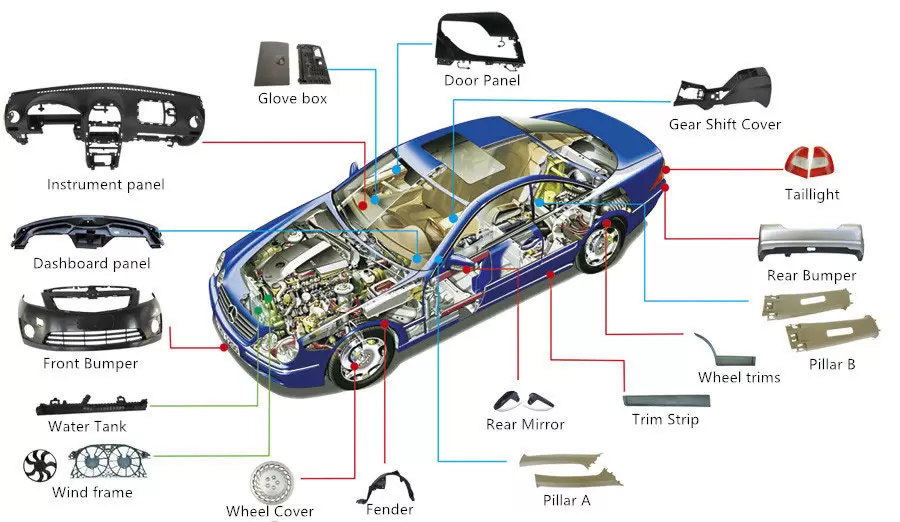
injection molding processing of automobile accessories: headlights, door panels, rearview mirrors, workbenches, handles, bumpers, taillights, other plastic material injection molding accessories.
V1 Injection Molding Service process
1> Get Quote
Get a quote for tooling and first batch production with shipping estimates in 24 to 48 hours.
2> DFM analyze
Receive DfM documentation 24 to 72 hours after ordering tooling samples. Tooling begins when you sign off on the DfM report.
3> Mold making
You get 2 free samples per part for your approval. V1 keeps a “golden sample” part for additional quality inspection.
4> Mass Production
Your parts go into production after samples are approved by injection molding.
5> Quality control
We use the golden sample to verify future orders and provide additional QC checks.
6> Delivery
provides the convenience of having goods transported from our factory to your warehouse, saving time and effort for you.
Why Choose V1 Plastic Molding Service
Professional Team
V1 mold design & engineering team has 36 skilled engineers to provide technical support for plastic mold making and plastic processing.
17+ Years Experience
V1 mould has been manufacturing plastic tools for automotive, medical device and electronics for over 17 years.
One-Stop Solution
V1 offer a one-stop solution to meet customers all demands about plastic mould and customized plastic products manufacturing.
Global After-sales Service
V1 responsible for the quality of each mold, will sign mold quality warranty with customers for every tools.
Advanced Equipment
V1 factory is equipped with advanced mold manufacturing equipment and precision measuring instruments CMM.
On-Time Delivery
V1 schedule every mold projects manufacturing process very well, can guarantee on-time delivery for each production.
V1 Mold Manufacturing and processing capacity
- 3 factories in China with advanced equipment including double-head EDM machines,mold fitting machine, large CNC machines etc.
- 20T-3500T injection molding machines to meet different customers needs.
- Maximum capable of making molds up to 35T.
- Over 30 overseas coworkers across the globe to provide our powerful local support from pre-sales communication, technical support to after-sales-service to further guarantee the high quality of molds and parts.
- Value-added service and resonable price.
Our Injection Molding partners
With our rich experience of toolmaking, powerful local support from our overseas teams and reasonable price, we have established long term win-win business cooperation with worldwide well-know companies.
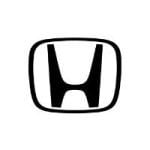
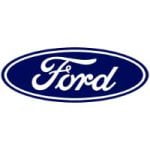
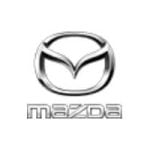
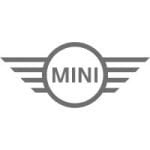
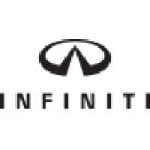
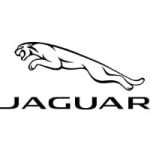
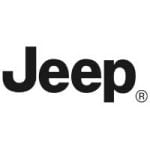
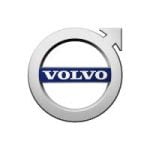
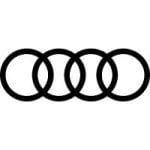
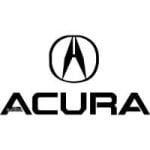

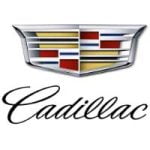
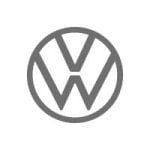
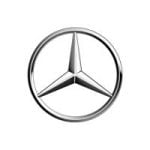
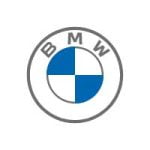
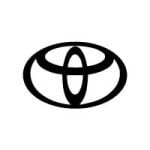
Plastic Injection Moulding FAQs
Injection molding is a manufacturing process that creates complex plastic parts by injecting molten plastic into a mold and allowing it to cool. Injection molding is typically used for high-volume production, but it can also be used to produce small batches down to a single part.
The main advantages of injection molding are its efficient production speed, low cost, highly precise control of the size and shape of the produced parts, and excellent surface quality. First of all, injection molding is extremely efficient because it can continuously produce large quantities of products in a short time. Secondly, the cost of injection molding is relatively low, mainly because its production process is simple and the required equipment and material costs are low. Furthermore, injection molding enables highly precise control of the size and shape of the parts produced, which is very important for the production of parts that require high precision. Finally, injection molding can produce parts with excellent surface quality. This is because during the production process, a very smooth film will be formed on the surface of the mold, and this film will be transferred to the surface of the part, thereby making the surface of the part The quality is very good.
Plastic injection molding is a widely used manufacturing technology in modern manufacturing. This technology is produced using several types of plastics including, but not limited to, polypropylene (PP), polyurethane (PU), polyethylene (PE), polyester (PET), and polycarbonate (PC).
Polypropylene (PP) is a common thermoplastic that has good impact resistance and heat resistance, so it is often used to manufacture products that need to withstand higher temperatures or greater impact forces. In addition, due to its low water absorption and good chemical stability, PP is also often used to manufacture food packaging and medical devices.
Polyurethane (PU) is a plastic with high strength, high toughness and good wear resistance, so it is often used to make automobile parts, furniture, shoes, etc. In addition, due to its excellent weather resistance and corrosion resistance, PU is also often used to manufacture outdoor products and building materials.
Polyethylene (PE) is a lightweight, transparent and easy-to-process plastic, so it is often used to make plastic bags, films and pipes. In addition, due to its good electrical insulation and chemical stability, PE is also often used to manufacture wires, cables and chemical containers.
Polyester (PET) is a plastic with high strength, good transparency and good heat resistance, so it is often used to make beverage bottles, food packaging and fibers. In addition, due to its excellent weather resistance and corrosion resistance, PET is also often used in the manufacture of outdoor products and building materials.
Polycarbonate (PC) is a plastic with high strength, high transparency and good heat resistance, so it is often used to make bulletproof glass, spectacle lenses and aerospace components. In addition, due to its excellent impact resistance and wear resistance, PC is also often used to manufacture automotive parts and electronic equipment.
In the injection molding process, molds are a vital component as they hold and shape plastic parts. These molds are usually made of steel or aluminum and must be precision machined to ensure that the parts produced are of the exact size and shape.
First, let's understand what a mold is. A mold is a tool used to make objects of a specific shape and size. In injection molding, the role of the mold is to inject molten plastic into the mold, which then cools and solidifies to ultimately form the desired plastic part. Therefore, the design and manufacturing of molds are crucial to the quality of the final product.
Molds are typically made of steel or aluminum because both materials are strong and durable enough to withstand the high temperatures and pressures of the injection molding process. In addition, steel and aluminum also have good thermal conductivity properties and can quickly conduct heat away from the mold surface, thereby speeding up the cooling of the plastic.
However, simply choosing the right material is not enough to ensure the quality of the mold. To ensure that the parts produced are of precise size and shape, molds must be precision machined. This means that the surface of the mold must be extremely smooth and free of any blemishes or imperfections. In addition, the dimensions of the mold must be very precise to ensure that the parts produced meet the design requirements.
To achieve this, moldmakers often use advanced CNC machining equipment and technology. These devices can precisely control the position and speed of the cutting tool to ensure the accuracy and smoothness of the mold surface. In addition, manufacturers also conduct strict quality control and testing of molds to ensure that their quality meets standards.
In short, the mold is an indispensable key component in the injection molding process. Not only do they need to be made from high-strength and durable materials, they also need to be precision machined to ensure that the parts produced are of precise size and shape. Only in this way can the quality of the final product be guaranteed to meet customer needs.
Of the many manufacturing processes, injection molding may be one of the most challenging. However, its biggest drawback may be the high tooling cost. Mold making requires precision machining, and the cost of tooling can be prohibitive for more complex parts. Therefore, if smaller quantities of parts need to be produced, the cost-effectiveness of using injection molding may need to be reconsidered.
First, we need to understand the basic process of injection molding. In this process, plastic pellets are heated to a liquid state and then injected into a pre-designed mold through high pressure. Once cooled and solidified, the mold can be opened and the finished product removed. This process may seem simple, but actually requires very precise control and a high degree of expertise.
However, this accuracy comes with high tool costs. Mold manufacturing is a complex and time-consuming process that requires a large amount of precision equipment and professional technical personnel. For simple parts, tooling costs may not be too high. However, for more complex parts, tooling costs can add up quickly. This is because these parts may require more complex designs and more machining steps.
Additionally, since injection molding is a mass-production process, tooling costs also need to be spread across each part. This means that if only a small number of parts are produced, the tooling cost per part can be very high. This can result in injection molding being less cost-effective than other manufacturing processes.
Therefore, when we consider using injection molding to produce parts, its cost-effectiveness must be carefully considered. If parts are produced in higher volumes, injection molding may be an ideal option. However, if smaller quantities of parts need to be produced, then we may need to reconsider using injection molding, or find other more economical manufacturing processes.
One of the biggest advantages of injection molding technology is its efficient production performance. Once the mold is made, injection molding has the ability to produce large quantities of parts quickly and accurately, making injection molding ideal for projects that require high-volume production.
The efficiency of injection molding technology is mainly reflected in the following aspects: First, the mold production process is relatively simple and can be completed quickly. Once the mold is made, it can be used repeatedly without having to make it again every time, which greatly saves time and cost. Secondly, the injection molding process is highly automated. Just set the parameters and the machine can automatically complete the entire production process without manual intervention, which greatly improves production efficiency. Thirdly, the precision of injection molding is very high, which can ensure that the size and shape of each part are exactly the same, meeting the demand for high-precision products. Finally, injection molding can produce large numbers of parts in one go, making it ideal for mass production.
Therefore, injection molding technology is widely used in many fields, such as automobiles, home appliances, electronic products, etc. The demand for products in these industries is large and the requirements for production efficiency and product quality are very high, and injection molding technology just meets these needs.
Injection molding technology is widely used in a variety of different industries, including but not limited to automobile manufacturing, medical equipment, electronic equipment, toys, furniture, and more. Any industry that produces plastic parts in large quantities is likely to use injection molding technology. The application range of this technology is very wide, covering almost every aspect of our daily life. Whether in the automobile manufacturing industry, used to produce various complex automobile parts, or in the medical equipment manufacturing industry, used to produce various precision medical instruments, injection molding technology plays an important role. In addition, the electronic equipment manufacturing industry also uses injection molding technology to produce various electronic components and accessories. In the toy manufacturing industry, injection molding technology is used to produce a variety of plastic toys. In the furniture manufacturing industry, injection molding technology is used to produce various plastic furniture and decorations. In general, injection molding technology has a wide range of applications, covering almost all industries that require mass production of plastic parts.
After injection molding, parts may require further processing, such as coloring, surface coating, assembly, etc. These additional processes improve the beauty, durability and functionality of the part.
Injection molding is a common manufacturing process in which molten plastic is injected into a mold, where it is then cooled and solidified to ultimately form the desired part. However, all needs may not be met by injection molding alone, so further processing of the part is required.
First, coloring is an important step that gives the part a specific color. By adding dyes or pigments, you can make a part blend better with its surroundings or highlight its specific functionality. Coloring not only increases the aesthetics of a part, but also improves its visibility, making it easier for users to recognize and use it.
Secondly, surface coating is another common treatment process. By spraying or brushing a layer of paint, you can provide an extra layer of protection to your parts from the outside environment and wear and tear. In addition, surface coating can change the appearance of a part, making it smoother, glossier or with a special textured effect.
Finally, assembly is the process of putting multiple parts together. In some cases, a single part may not meet the functional requirements of the product, so multiple parts need to be assembled together to form a whole. Assembly can be achieved by welding, threaded connections, buckles, etc. to ensure tight connection and stability between parts.
In general, injection molded parts may require further processing, such as coloring, surface coating, and assembly. These additional processes can improve the aesthetics, durability and functionality of the part, making it better suited to different application needs.
During the injection molding process, we need to consider a series of parameters, including injection speed, pressure, temperature, time, etc. The settings of these parameters are not static, but need to be adjusted accordingly according to different materials, part designs and mold designs. This is because only by precisely controlling these parameters can we ensure that the parts produced are of high quality.
First, injection speed is an important parameter. It determines the flow rate of plastic melt from the injection machine to the mold. If the injection speed is too fast, it may cause the plastic melt to cool too quickly in the mold, affecting the quality of the part. On the other hand, if the injection speed is too slow, it may cause the plastic melt to cool too slowly in the mold, thus affecting the shape and size of the part.
Secondly, pressure is also an important parameter. It determines how filled the plastic melt is in the mold. If the pressure is too high, it may cause the plastic melt to overflow the mold, affecting the quality of the part. On the other hand, if the pressure is too small, the plastic melt may not fully fill the mold, affecting the shape and size of the part.
Again, temperature is an important parameter. It determines the fluidity and solidification speed of the plastic melt. If the temperature is too high, it may cause the plastic melt to solidify prematurely in the mold, affecting the shape and size of the part. On the contrary, if the temperature is too low, it may cause the plastic melt to have insufficient fluidity in the mold, thus affecting the shape and size of the part.
Finally, time is an important parameter. It determines the residence time of the plastic melt in the mold. If the time is too long, it may cause the plastic melt to cool too much in the mold, affecting the quality of the part. On the contrary, if the time is too short, the plastic melt may not be cooled enough in the mold, thus affecting the shape and size of the part.
Therefore, we need to make precise adjustments to these parameters based on different materials, part designs, and mold designs to ensure that the parts produced are of high quality.
In the field of manufacturing, injection molding technology has higher production efficiency, lower cost and better product quality than 3D printing technology. Injection molding technology can quickly produce large quantities of parts, and the products not only have higher strength, but also have a more beautiful appearance. In addition, injection molding technology also has the advantage of using a variety of materials, which allows it to meet different needs while ensuring product quality and performance.
First, the production efficiency of injection molding technology is high, which means that a large number of parts can be produced in a short period of time. In contrast, although 3D printing technology has advantages in some aspects, it still has certain limitations in mass production. Therefore, injection molding technology is undoubtedly a more suitable choice in scenarios where mass production of parts is required.
Secondly, the cost of injection molding technology is lower. Because its production process is relatively simple and the required equipment and material costs are relatively low, the overall cost can be effectively reduced during the production process. Although 3D printing technology has advantages in some specific scenarios, because its production process is more complex and the equipment and material costs required are relatively high, it may not be as competitive as injection molding technology in terms of overall cost.
Furthermore, products produced by injection molding technology have higher strength and better appearance. This is because during the injection molding process, the molten plastic material quickly fills the mold under high pressure, making the product's internal structure tight and thus higher in strength. At the same time, injection molding technology can also control the appearance of the product by adjusting the shape and size of the mold to make it more beautiful. Although 3D printing technology has greater flexibility in product design, due to the limitations of its production process, the products produced may not be comparable to injection molding technology in terms of strength and appearance.
Finally, injection molding technology offers the advantage of using a variety of materials. During the production process, different plastic materials can be selected according to the needs of the product to meet different performance requirements. This enables injection molding technology to meet diverse needs while also ensuring product quality and performance. Although 3D printing technology also supports the use of a variety of materials, due to the limitations of its production process, there may be certain limitations in material selection and application.
To sum up, injection molding technology has obvious advantages over 3D printing technology in terms of production efficiency, cost and product quality. This has made injection molding technology widely used in manufacturing and has become an important production process.
In the plastic injection molding process, cycle time is a very important parameter. This time depends on many factors, including material selection, part design, mold design, and the efficiency of the production equipment. These factors together determine injection molding cycle time.
First, material selection is an important factor affecting injection molding cycle time. Different plastic materials have different melting temperatures and cooling rates, which will directly affect the molding time. For example, some plastics with a high melting point may take longer to completely melt, while some plastics with a low melting point may complete the process more quickly.
Secondly, the design of the part also affects the injection molding cycle time. If the design of the part is complex, the molding process may take longer. This is because complex designs may require more steps to complete, for example, require multiple injections or require a more complex mold structure.
Furthermore, the design of the mold is also an important consideration. A good mold design can improve production efficiency and shorten the molding cycle. For example, an optimized cooling system can reduce cooling time, while an efficient gate design can reduce injection time.
Finally, the efficiency of production equipment also affects injection molding cycle time. A high-efficiency piece of equipment can complete the molding process faster, thereby shortening the production cycle. Therefore, choosing efficient and reliable production equipment is the key to improving production efficiency.
In general, injection molding cycle times can range from a few seconds to a few minutes, depending on the requirements of the production. For some products that do not have high requirements on production speed, a longer molding cycle may be acceptable; while for some products that have strict requirements on production speed, the molding cycle needs to be shortened as much as possible.
Common question in Injection Molding Production
The cost of injection molding depends on several factors, including material cost, tooling cost, production lead time, part quantity and complexity, etc. Generally speaking, the cost per part is lower for high-volume production and higher for smaller batches.
There are many factors to consider when choosing the right injection mold. These factors include, but are not limited to, their work experience, equipment condition, quality control, and more. In order to ensure that you choose the supplier that best suits your project needs, it is best to communicate with multiple suppliers and carefully consider their quotations, production lead times, quality control, etc.
First, an experienced injection mold supplier can better understand your needs and provide professional advice and solutions. They may have worked on similar projects and have a deeper understanding of the issues and challenges that may arise. Therefore, when choosing a supplier, you can ask about their work experience and cases to understand their professional capabilities in related fields.
Secondly, the quality and performance of the injection mold are directly related to the quality of the final product. Therefore, when choosing a supplier, carefully examine the condition of their equipment and quality control systems. Find out whether they have advanced production equipment and technology, and how they ensure quality control during the production process. This can be achieved by visiting the supplier's factory or learning about their quality management system.
In addition, the supplier's quotation is also an important consideration. Different suppliers may offer different prices, so comparisons and evaluations need to be made. However, just pursuing low prices is not a wise choice because quality is crucial. When selecting a supplier, you must weigh the relationship between price and quality to ensure that the selected supplier can provide high-quality injection molds.
Finally, the production cycle is also one of the factors that needs to be considered. Different suppliers may have different production cycles, which directly affects the project progress and delivery time. When choosing a supplier, understand their production capabilities and delivery times and match them with your own project plan. At the same time, the stability and reliability of the supply chain must also be taken into consideration to ensure that the project can be completed on time.
To sum up, choosing a suitable injection mold supplier is a process that requires comprehensive consideration of multiple factors. By communicating and comparing with multiple suppliers and carefully considering their work experience, equipment condition, quality control, quotation and production cycle, you can better determine the most suitable partner to ensure the success of your project. implementation.
Many factors affect the plastic injection molding production cycle, including but not limited to part size, quantity, and complexity. The specifics of these factors will directly affect the length of the production cycle.
First, let's look at the size of the parts. Generally speaking, larger parts take longer to manufacture and assemble. This is because larger parts typically require more materials and more complex production processes. Therefore, if a part is very large, its production cycle may be much longer than for smaller parts.
Secondly, the number of parts is also an important consideration. If a large number of parts need to be produced at one time, the production cycle may be extended accordingly. This is because during the production process, every part needs to be precisely controlled and inspected to ensure their quality. If there are too many parts, the process becomes more complex and time-consuming.
Finally, we also need to consider the complexity of the part. Complex parts usually require more processes to complete, which also lengthens the production cycle. For example, some parts with complex shapes or internal structures may require the use of special tools and techniques to manufacture, which increases production difficulty and time.
In general, the production cycle of plastic injection molding is determined by a variety of factors. In the actual production process, we need to determine the appropriate production cycle based on the specific parts conditions. Generally, this cycle can range from a few days to a few weeks.
Ensuring that a part is suitable for injection molding requires adequate attention to its design requirements. These design requirements include aspects such as wall thickness, structural support, and surface texture. Additionally, factors such as material selection and mold design need to be considered.
During the injection molding process, part design is crucial. First, the design of wall thickness requires careful consideration. Wall thickness refers to the thickness of the component, which directly affects the strength and stability of the component. If the wall thickness is too thin, the part may deform or break during production; if the wall thickness is too thick, it will increase manufacturing costs and extend the production cycle. Therefore, designers need to reasonably determine the size of the wall thickness based on the function and use of the component.
Secondly, structural support is also a factor that cannot be ignored in the design. Structural support refers to the support structure inside the component to enhance the stability and strength of the component. Through reasonable structural design, it can be ensured that the parts will not be deformed or damaged during the injection molding process. Designers need to consider the shape, size and stress of the component and choose appropriate structural support methods to ensure the quality and performance of the component.
In addition, surface texture is also one of the important factors to consider in design. Surface texture refers to the texture and texture of the surface of a component, which can affect the appearance and feel of the product. During the injection molding process, designers need to choose appropriate surface texture treatments based on product requirements to improve the product's aesthetics and user experience.
In addition to the above design requirements, material selection and mold design are also important factors to consider during the injection molding process. Material selection is directly related to the performance and quality of the product. Designers need to select appropriate materials according to the requirements of the product to ensure that the product has the required properties such as strength, wear resistance, and chemical corrosion resistance. At the same time, mold design is also very important, which directly affects the molding effect and production efficiency of the product. Designers need to reasonably design the structure of the mold based on the shape and size of the product to ensure that the product can be smoothly removed from the mold and meet the expected quality standards.
In summary, ensuring a part is suitable for injection molding requires a combination of factors. Designers need to carefully analyze the product requirements, reasonably determine the design requirements in terms of wall thickness, structural support, and surface texture, and select appropriate materials and mold designs to ensure that the product has good quality and performance. Only when these design requirements are fully met can the injection molding process be carried out to produce high-quality products.
During the injection molding process, many different types of defects can occur, such as bubbles, weld lines, shrinkage, etc. To avoid the occurrence of these defects, the key is to ensure that the material is completely melted, try to avoid over-injection, and properly control the molding temperature.
First, let's explore these possible pitfalls in detail. Air bubbles are a common problem during injection molding. When the material doesn't melt completely, gas can become trapped in the plastic and form bubbles. These bubbles will not only affect the appearance quality of the product, but may also cause the product to break or leak during use. Therefore, ensuring that the material is completely melted is key to avoiding air bubbles.
Secondly, weld lines are also one of the common defects in injection molding. Weld lines may form when two or more materials come into contact and fuse together. This defect usually occurs at the edges or seams of the product, causing the product surface to be uneven or have obvious dividing lines. In order to reduce the occurrence of weld lines, we can take some measures, such as optimizing mold design, adjusting injection speed and pressure, etc.
In addition, shrinkage is also one of the issues that need attention in injection molding. When plastic cools, it tends to shrink to some extent. If the shrinkage is uneven or excessive, it will cause dimensional instability or deformation of the product. To control shrinkage, we can choose appropriate materials and additives, as well as adjust factors such as mold temperature and cooling time.
Finally, over-injection is also a cause of defects. When too much is injected, the plastic may overflow the mold or create an uneven fill. This will not only affect the appearance quality of the product, but may also lead to uneven or defective internal structure of the product. Therefore, during the injection molding process, we need to strictly control the injection volume to ensure stable and reliable product quality.
To sum up, to avoid defects in injection molding, we need to ensure that the material is completely melted, avoid over-injection, and properly control the molding temperature. Through reasonable process parameters and operating skills, we can improve product quality and reliability and meet customer needs and expectations.
In the injection molding process, the quality of material life depends on the selection and use of materials. Generally speaking, molds can produce tens to hundreds of thousands of parts. If more parts need to be produced, the mold may need to be replaced.
In the injection molding process, material quality is a key factor that is directly affected by the material chosen and how it is used. Therefore, when performing injection molding, it is very important to select suitable materials and use them rationally.
First of all, the mold is an indispensable tool in the injection molding process. Depending on different needs, molds can produce thousands or even hundreds of thousands of parts. This means that by selecting the appropriate mold, we can achieve large-scale production and meet market demand.
However, when more parts need to be produced, we may need to consider changing the mold. This is because the capacity of the mold is limited, and once the maximum output is reached, a new mold needs to be replaced to continue production. This process may bring about certain costs and time delays, but it is necessary to ensure the smooth progress of production.
In summary, the material quality of life in the injection molding process depends on the selection and use of materials. Through reasonable selection of materials and appropriate use of molds, we can achieve large-scale production and meet market demand. When more parts need to be produced, changing molds is necessary, although this may come with some additional cost and time delays.
There are many factors to consider when choosing the right injection molding material. These factors include the material's strength, hardness, toughness, heat resistance, and other properties. In addition, factors such as cost, material availability and environmental friendliness need to be considered.
First, we need to focus on the strength of the material. Strength refers to the maximum stress that a material can withstand when subjected to external forces. When selecting injection molding materials, we need to consider whether their strength is sufficient to meet the needs of the product to ensure that the product will not crack or deform during use.
Secondly, hardness is also an important consideration. Hardness refers to a material’s ability to resist surface damage such as scratches and indentations. For some products that require a certain degree of wear resistance, we can choose injection molding materials with higher hardness to improve the durability of the product.
In addition to strength and hardness, toughness is also a factor that cannot be ignored. Toughness refers to the ability of a material to maintain its shape and properties when subjected to external forces such as impact or vibration. For some products that require a certain degree of impact resistance, we can choose injection molding materials with higher toughness to ensure that the product will not be damaged due to impact during use.
In addition, thermal stability is also an important factor to consider when selecting injection molding materials. Thermal stability refers to the ability of a material to maintain its shape and properties in high-temperature environments. In some products that require a certain degree of heat resistance, we can choose injection molding materials with higher thermal stability to ensure that the products can work normally in high temperature environments.
In addition to the above physical properties, we also need to consider factors such as cost, availability and environmental protection of injection molding materials. Cost is a factor that must be considered when choosing injection molding materials. We need to choose materials with reasonable prices while ensuring product quality. At the same time, material availability is also very important, and we need to ensure that the selected materials are easily available in the market to meet production needs. Finally, environmental protection is also a factor that is getting more and more attention. We need to choose materials that meet environmental protection requirements to reduce the impact on the environment.
To sum up, choosing the right injection molding material is a complex and important task. We need to comprehensively consider factors such as material strength, hardness, toughness, thermal stability, cost, availability and environmental protection to ensure that the selected materials can meet the needs of the product and comply with relevant requirements.
Injection ports are a recurring problem during injection molding, especially when manufacturing complex parts. To avoid injection holes, the injection molding process needs to be carefully designed and analyzed, and the material must be fully melted and injected.
Injection port issues are a common challenge in injection molding, especially when it comes to manufacturing complex parts. In order to solve this problem, we need to take a series of measures to avoid the appearance of injection holes. First, we need to carefully design and analyze the injection molding process. This includes considerations such as mold design, material selection, and injection parameter setting. Through reasonable design, we can reduce the probability of injection hole formation.
Secondly, we need to ensure that the material is fully melted and injected. During the injection molding process, the material needs to be heated and melted before it can be injected into the mold. Therefore, we need to control the heating temperature and time to ensure that the material can be fully melted. At the same time, we also need to choose the appropriate injection speed and pressure to ensure that the material can be injected into the mold smoothly.
In addition to the above two points, we also need to pay attention to some other details. For example, when designing the mold, we can use a special cooling system to reduce the formation of injection holes. In addition, we can also optimize the location and shape of the injection port to reduce the appearance of injection holes.
In conclusion, avoiding injection holes is an important task in the injection molding process. Through careful design and analysis, as well as ensuring that the material is fully melted and injected, we can effectively solve this problem. This will help improve the quality and efficiency of injection molding to meet the production needs of complex parts.
In the injection molding process, quality control is a vital link. It involves inspecting and testing the quality of raw materials, parts and molds to ensure that high-quality parts are produced. In order to achieve this goal, various testing equipment and technologies need to be used, such as metrological testing, X-ray testing, mechanical property testing, etc. These testing methods help us understand the performance of materials and parts to ensure they meet design requirements and customer needs.
When conducting quality control, we need to pay attention to the following aspects:
1. Raw material quality: Choosing high-quality raw materials is the basis for ensuring the quality of the final product. Therefore, when purchasing raw materials, suppliers should be strictly screened to ensure that the selected raw materials meet relevant standards and requirements.
2. Part quality: During the production process, each part needs to be inspected and tested in detail to ensure that its size, shape, surface roughness, etc. meet the design requirements. In addition, mechanical property testing of parts, such as strength, hardness, wear resistance, etc., is also required to evaluate their performance in practical applications.
3. Mold quality: Mold is a key component in the injection molding process, and its quality directly affects the quality and production efficiency of parts. Therefore, during the production process, the mold needs to be inspected and maintained regularly to ensure that it is always in good working condition.
4. Production process monitoring: Through real-time monitoring of the production process, problems in the production process can be discovered and solved in time, thereby improving product quality. In addition, data analysis can also be used to optimize the production process and improve production efficiency.
5. Quality control system: Establishing a complete quality control system is an important guarantee for ensuring product quality. This includes formulating detailed quality control processes, training employees to master relevant knowledge and skills, establishing effective communication mechanisms, etc.
In summary, quality control is a complex and important task during the injection molding process. By using advanced testing equipment and technology, as well as strict monitoring and adjustment of the production process, we can ensure the production of high-quality parts to meet the needs of customers and the market.
Warpage and shrinkage are common problems during injection molding, especially for large and complex parts. In order to avoid these problems, multiple factors need to be considered comprehensively, such as material selection, mold design, and control of injection molding process parameters. In addition, in order to ensure the dimensional and shape stability of the part, proper mold preheating, injection temperature control and appropriate cooling are also required.
First, material selection is one of the key factors in solving warpage and shrinkage issues. Different materials have different thermal expansion coefficients and fluidities, so choosing the right material can effectively reduce the occurrence of warping and shrinkage. When selecting a material, factors such as its physical properties, thermal properties, and compatibility with the mold material need to be considered.
Secondly, mold design is also one of the important factors affecting warpage and shrinkage. Proper mold design can reduce stress concentrations and temperature gradients, thereby reducing the risk of warpage and shrinkage. In mold design, factors such as the shape of the part, wall thickness distribution, gate location, and cooling system design need to be taken into consideration.
In addition, the control of injection molding process parameters also has an important impact on warpage and shrinkage. By precisely controlling parameters such as injection speed, pressure, temperature and holding time, the flow and cooling process of the material can be effectively controlled, thereby reducing the occurrence of warpage and shrinkage. At the same time, reasonable process parameters can also improve the quality and surface finish of parts.
Finally, proper mold preheating, injection temperature control and cooling measures are also important means to ensure part dimensional and shape stability. Mold preheating can reduce the temperature difference between the mold and the material, thereby reducing the occurrence of warpage and shrinkage. Injection temperature control ensures material temperature uniformity during the injection process, thereby reducing the risk of warping and shrinkage. Appropriate cooling measures can control the cooling rate of parts and avoid problems such as warping and shrinkage caused by too fast or too slow cooling.
To sum up, to solve the warpage and shrinkage problems in injection molding, multiple factors such as material selection, mold design, process parameter control, and appropriate mold preheating, injection temperature control, and cooling measures need to be comprehensively considered. Only when these aspects are fully considered and controlled can the dimensional and shape stability of parts be ensured, thereby improving product quality and production efficiency.
Bubbles and pores in the material are common defects during the injection molding process, and these defects can adversely affect the strength and appearance of the part. In order to solve these problems, some methods can be taken to improve the dryness of the material, reduce the flow rate of the material, and strengthen the ventilation of the mold.
First, improving the dryness of the material is key to solving the problem of bubbles and pores. When a material contains too much moisture, during the injection molding process, the water evaporates and forms air bubbles, which can lead to voids in the material. Therefore, the moisture content of the material can be controlled to ensure that it reaches an appropriate degree of dryness before injection molding, thereby reducing the generation of bubbles and pores.
Secondly, reducing the flow rate of materials is also one of the effective ways to solve the problem of bubbles and pores. When material flows too fast, it causes the material to fill unevenly in the mold, creating bubbles and voids. Therefore, the flow rate of the material can be reduced by adjusting the parameters of the injection molding machine, such as injection speed, pressure, etc., so that it can better fill the mold and reduce the formation of bubbles and pores.
In addition, strengthening the ventilation of the mold is also one of the important measures to solve the problem of bubbles and pores. During the injection molding process, the air inside the mold needs to be exhausted to avoid air being trapped in the material and forming bubbles. Therefore, the ventilation effect of the mold can be enhanced by increasing the vents of the mold and optimizing the structure of the mold to ensure that the air can be discharged smoothly and reduce the generation of bubbles and pores.
In summary, by improving the dryness of the material, reducing the flow rate of the material, and strengthening the ventilation of the mold, the problems of bubbles and pores during the injection molding process can be effectively solved, thereby improving the strength and appearance quality of the parts. The application of these methods will help improve the manufacturing efficiency and quality level of products, bringing greater competitive advantages to enterprises.
There are many factors to consider when choosing the right injection molding equipment. These factors include but are not limited to production needs, part design, material selection, production efficiency, etc. According to different needs, you can choose different types of injection molding machines, such as horizontal injection molding machines, vertical injection molding machines, etc.
First of all, production needs are one of the important considerations when choosing injection molding equipment. Different products may require different production processes and production capabilities. Therefore, when selecting equipment, you need to fully understand the production volume, production cycle, and required accuracy requirements of the product. Only by ensuring that the selected equipment can meet production needs can the smooth progress of the production process be guaranteed.
Secondly, part design is also one of the important factors to consider when selecting injection molding equipment. Different part designs may require different mold structures and injection molding processes. Therefore, when selecting equipment, it is necessary to carefully analyze the design characteristics of the part to ensure that the selected equipment can adapt to the manufacturing requirements of the part.
In addition, material selection is also one of the factors that need to be considered when selecting injection molding equipment. Different materials have different characteristics such as fluidity, shrinkage and heat resistance, so it is necessary to choose an injection molding machine suitable for the material. At the same time, factors such as the availability and cost of materials also need to be considered to ensure that the selected equipment is economical and sustainable.
Finally, production efficiency is also one of the factors that needs to be considered when selecting injection molding equipment. Efficient production equipment can improve production efficiency, reduce production costs, and improve product quality. Therefore, when selecting equipment, factors such as the equipment's operating speed, energy consumption, and degree of automation need to be evaluated to ensure that the selected equipment can achieve efficient production.
In summary, choosing the right injection molding equipment is a complex process that requires the consideration of multiple factors. Only with a full understanding of production needs, part design, material selection, and production efficiency can we make wise choices to ensure the smooth progress of the production process.
The color of the material being processed is a crucial consideration during the injection molding process. Usually, we can change the color of a material by adding pigments or color masterbatch. In addition, by controlling the injection molding process parameters and mold temperature, we can also adjust the uniformity and brightness of the color.
First, let’s dive into why the color of the material being processed is so important in injection molding. Injection molding is a process widely used to manufacture various plastic products, and color is one of the important components of the product's appearance. Different products require different colors to meet market demand and consumer preferences. Therefore, being able to flexibly change the color of materials is crucial for manufacturers.
To achieve this, there are two main methods we can use: adding pigments or using color masterbatches. Pigments are tiny particles that can dissolve or disperse in plastic, changing its color. By choosing the right pigments, we can achieve almost unlimited color variations. Color masterbatch, on the other hand, is a plastic pellet that is premixed with pigments and other additives and can be added directly to the plastic raw material. This method is more convenient because the color masterbatch has been precisely proportioned and mixed to ensure color consistency and stability.
In addition to changing the color, we can also adjust the uniformity and brightness of the color by controlling the injection molding process parameters and mold temperature. The injection molding process involves multiple parameters, such as injection speed, pressure, cooling time, etc. Changes in these parameters will directly affect the flow and cooling of plastic materials, thereby affecting the color performance of the final product. By optimizing these parameters, we can achieve more uniform and vivid color effects.
In addition, mold temperature is also one of the important factors affecting color. An increase in mold temperature causes the plastic material to become more fluid, making it easier for the color to spread evenly. However, excessively high mold temperatures may cause degradation and discoloration of plastic materials. Therefore, when adjusting the mold temperature, we need to comprehensively consider the characteristics of the material and the requirements of the product to obtain the best visual effect.
To sum up, handling the color of materials is an important task in injection molding. By adding pigments or using color masterbatch, we have the flexibility to change the color of the material. At the same time, by controlling the injection molding process parameters and mold temperature, we can also adjust the uniformity and brightness of the color. The application of these technologies will help manufacturers produce more attractive and competitive products to meet market needs and consumer expectations.
Mold wear is a common problem during the injection molding process, which not only affects the quality of the parts but also reduces production efficiency. In order to solve the problem of mold wear, we need to perform regular mold care and maintenance, which includes mold cleaning, lubrication and repair.
First of all, mold cleaning is an important part of maintenance work. In the daily production process, the mold will absorb a large amount of plastic residue. If these residues are not cleaned in time, they will cause damage to the mold and accelerate the wear of the mold. Therefore, we need to deep clean the mold regularly to remove all plastic residue.
Secondly, mold lubrication is also an important part of maintenance work. During the injection molding process, the mold needs to withstand high temperature and pressure. Without good lubrication, the wear of the mold will be accelerated. Therefore, we need to lubricate the mold regularly to reduce friction and extend the service life of the mold.
Finally, mold repair is also an important part of maintenance work. During long-term use, the mold may have problems such as cracks and deformation. If these problems are not repaired in time, they will cause serious damage to the mold. Therefore, we need to regularly check the status of the mold and repair it immediately if a problem is found.
In addition to the above maintenance work, we can also extend the service life of the mold by using highly wear-resistant materials to manufacture the mold. This material has excellent wear resistance and can resist long-term wear and tear, thus extending the service life of the mold. In general, through regular maintenance and maintenance, as well as the use of highly wear-resistant materials, we can effectively solve the problem of mold wear and ensure the quality and efficiency of injection molding.
leave a message
Contact
Contact us now to bring your idea into reality, our professional team will respond you in 24 hours after we get your email.
- Email: [email protected]
- Office Address: 2nd Floor, NO. 10 Lianhu Road, Changan Town, Dongguan City, Guangdong Province, China, 523850
- Factory Address: No.38, Hexing Road, Shatou, Changan Town, Dongguan City, Guangdong Province, China, 523850
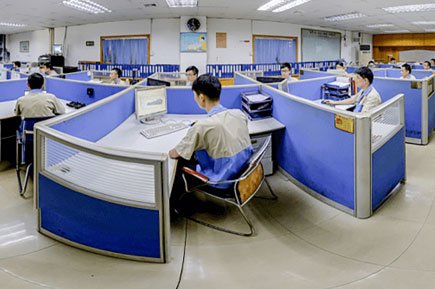