Table of Contents:
- Introduction
- Finding the Right Injection Molded Plastic Manufacturer
- Injection Molded Plastic Manufacturing Process
- Quality Control in Injection Molded Plastic Manufacturing
- Applications of Injection Molded Plastic Products
- Future of Injection Molded Plastic Manufacturing
- Conclusion
-
1.Introduction
Injection molding is a manufacturing process that involves injecting molten plastic into a mold to create a final product. The process is suitable for producing high volumes of consistent and intricate plastic parts and products with minimal waste. It is a tried and trusted method, commonly used in various industries, including medical, automotive, aerospace, and electronics.
Choosing injection molded plastic products offers many advantages over other traditional manufacturing methods, such as cost-effectiveness, high production rates, consistency, and accuracy. The final products are lightweight, have high strength-to-weight ratios, and are customizable to meet the specific needs of different applications. Moreover, injection molding allows you to produce complex part designs that cannot be made using other types of manufacturing methods, such as machining or casting. This makes injection molding a popular choice for producing small, intricate parts and components with high precision and accuracy.
-
2.Finding the Right Injection Molded Plastic Manufacturer
When searching for an injection mold plastic manufacturer, there are several factors that you should consider to ensure that you find the right manufacturer for your specific needs. Some of these factors include:
- Experience and Expertise: It is important to work with a manufacturer who has a track record of success, with extensive expertise in the injection molding process. Ask about their experience in injection molding and their expertise in different material grades and specifications.
- Quality Standards and Certifications: The manufacturer should adhere to strict quality control standards and hold relevant certifications such as ISO 9001, FDA, and medical certifications where applicable. This will ensure that the products they manufacture are of high quality and meet industry standards.
- Production Capacity: The manufacturer should have the capacity to produce a high volume of parts without sacrificing quality. This is especially important if you require large quantities of parts within a short turnaround time.
- Cost: While cost is an important factor, it should not be the sole consideration when choosing an injection molded plastic manufacturer. Make sure you are getting the right value for money and avoid selecting a manufacturer solely based on their pricing.
Types of Injection Molded Plastic Manufacturers:
There are different types of injection molded plastic manufacturers, each with its specific strengths and weaknesses. The types include:
- Original Equipment Manufacturers (OEMs): They specialize in producing products for their own company and use injection molding to produce plastic components for the products they manufacture.
- Custom Manufacturers: They specialize in producing custom injection molding products based on the customer’s design, needs, and requirements.
- Contract Manufacturers: They work on a project basis and provide a wide range of services to customers, including design assistance, prototyping, and production.
- Multi-Process Manufacturers: They offer a range of manufacturing processes, including injection molding and other processes such as blow molding, thermoforming, and extrusion.
-
3.Injection Molded Plastic Manufacturing Process
The injection molded plastic manufacturing process involves several steps, including melting the raw materials, injecting them into a mold, cooling, and ejecting the parts. Here are the materials used and the steps involved in the injection molded plastic manufacturing process:
Materials Used:
- Thermoplastics: These are most commonly used materials in the injection molding process due to their ability to be melted and formed into various shapes easily. Some common thermoplastics include Polypropylene (PP), Polystyrene (PS), Polyethylene (PE), and acetal.
- Additives: These are used to modify the properties of the base material before or during the injection molding process. Common additives include glass fibers, colorants, and UV stabilizers.
Steps Involved in the Injection Molded Plastic Manufacturing Process:
- Mold Closing: The two halves of the mold are closed, and the plastic pellets are fed into the barrel of the injection molding machine. The pellets are heated under high temperatures to become molten.
- Injection: The molten plastic is injected into the mold cavity under high pressure.
- Packing: Once the mold cavity is filled, the pressure is maintained to ensure that the plastic fills the mold and compensates for any shrinkage that may occur during cooling.
- Cooling: The mold is cooled to allow the molten plastic to solidify and take the shape of the mold.
- Ejection: Once the parts are cooled, the mold is opened, and the parts are ejected. The entire cycle is repeated to produce more parts.
These steps of injection molding can be done manually, but modern injection molding machines are automated, making the process fast, efficient, and accurate. Injection molding machines make use of sophisticated control systems to monitor and regulate the process, ensuring high quality and consistency of the final product.
In summary, injection molded plastic manufacturing process produces high-quality plastic products and parts that meet the required specifications and standards. The materials used, process and cycle design, and manufacturing equipment and techniques contribute to producing precise and consistent parts with high accuracy, repeatability, and efficiency.
-
4.Quality Control in Injection Molded Plastic Manufacturing
Quality control refers to the set of measures and controls used by injection molded plastic manufacturers to ensure that the final product meets the required quality, performance, and safety standards. Some of the commonly used quality control measures in injection molded plastic manufacturing include:
Importance of Quality Control:
- Ensures consistency and repeatability of the manufacturing process.
- Ensures that the final product meets the expected quality, performance, and safety standards.
- Reduces the risk of defects, rejects, and product returns.
- Increases customer satisfaction and trust in the manufacturer.
- Helps to identify and correct manufacturing process problems in a timely manner.
Common Quality Control Measures:
- Visual Inspection: Manual inspection of the product to identify any visual defects such as cracks, burrs, or warping.
- Dimensional Inspection: Uses measurement tools such as calipers, coordinate measuring machines (CMM), and laser scanners to ensure that the parts have the specified dimensions.
- Functional Testing: Check the functional performance of the product by subjecting it to specific tests like pressure tests or stress tests.
- Material Analysis: Tests performed on the raw material and finished product for chemical composition, density, melt flow rate, and other essential features.
Certifications to Look for in a Manufacturer:
When selecting an injection molded plastic manufacturer, look for a company that adheres to the industry’s best practices and holds relevant certifications. The most important certifications to consider include:
- ISO 9001: This quality management system certification provides a framework for ensuring that the manufacturer has documented procedures and processes in place that meet international standards.
- Environmental Certifications: Certifications like ISO 14000 or RoHS ensure that the manufacturer is committed to reducing the environmental impact of their manufacturing process.
- Medical Certifications: If you require injection molded plastic products for medical applications, look for a manufacturer who holds certifications like ISO 13485 or FDA 21 CFR Part 820 that demonstrate their adherence to quality and safety standards.
- Other Certifications: There are a variety of other certifications that you might look for, depending on the application of the product you require. These might include AS9100 for aerospace or IATF 16949 for automotive applications.
In summary, quality control is a critical aspect of injection molded plastic manufacturing, and it’s essential to choose a manufacturer who has documented quality control measures in place that align with your specific needs. Choosing a manufacturer with relevant certifications can offer you peace of mind that your product will meet the required quality, performance, and safety standards.
-
5.Applications of Injection Molded Plastic Products
Injection molded plastics are used in various industries and products due to their versatility, low cost, high production rates, and excellent material properties. Some industries and products that benefit from the use of injection molded plastics include:
Industries:
- Automotive: Many automotive components, such as dashboards, door panels, and bumpers, are made using injection molding.
- Medical: Injection molding is commonly used for producing medical devices and equipment like syringes, valves, and catheters.
- Aerospace: Injection molded plastics are used to construct many aerospace components, including control panels and other interior components.
- Electronics: Many electronic devices, such as keyboards, computer housings, and cell phone cases, utilize injection molding for their manufacturing.
- Packaging: Injection molding is used to produce various packaging products like bottles, lids, and caps.
Products:
- Toys: Injection molding is a popular method for producing plastic toys of different shapes, sizes, and colors.
- Household items: Products like utensils, plates, cups, and containers are commonly made using injection molding.
- Construction materials: Products such as pipes, fittings, and insulation materials are manufactured using injection molding.
- Sports equipment: Many sports equipment items, including balls, helmets, and protective gear, are made using injection molding.
Benefits of Using Injection Molded Plastic Products:
- Customizable: Injection molding allows you to create unique and customized products, tailored to specific needs and requirements.
- Economical: Injection molding is an economical process, especially when producing high volumes of units.
- Lightweight: Plastic products are lightweight, ideal for applications that require this feature.
- Accurate: Injection molding produces highly accurate parts and products due to its high precision and repeatability.
- Durable: Injection molded plastic products are strong, durable, and robust, with the ability to withstand harsh conditions.
- Versatile: Injection molding can be used to produce different types of products, materials, shapes and sizes.
- Fast: The injection molding process allows for faster production rates, which can translate to quicker order deliveries.
In summary, injection molded plastic products are versatile and used in different industries and products due to their many benefits. They are durable, lightweight, economical, accurate, and customizable, making them an ideal manufacturing choice for a variety of applications.
-
6.Future of Injection Molded Plastic Manufacturing
The injection molded plastic manufacturing industry is evolving, with advancements in technology and materials aimed at improving productivity, efficiency, and sustainability. Here are some trends and advancements in the industry and new materials and technologies on the horizon:
Trends and Advancements in the Industry:
- Smart Manufacturing: Smart manufacturing using the Internet of Things (IoT) is gaining traction in the injection molding industry, enabling manufacturers to optimize production processes and reduce scrap and waste.
- Automation: Automation is becoming more popular, especially for repetitive tasks, as it can result in faster production rates and reduce costs.
- Lightweight and High-Strength Materials: There is a growing demand for lightweight and high-strength materials in different industries, and injection molded plastics offer a viable solution.
- Sustainability: There is a growing focus on sustainability and the use of recycled materials in the production of injection molded plastic products.
- 3D Printing: 3D printing is becoming a viable alternative to traditional injection molding, with the ability to produce intricate and complex parts without the need for expensive tooling.
New Materials and Technologies:
- Bioplastics: Bioplastics made from renewable sources are becoming an increasingly popular choice, especially for environmentally conscious companies.
- 3D Printing Technologies: Developments in 3D printing technology are enabling the production of injection molds with more complex geometry and intricate features.
- Carbon Fiber Composites: Carbon fiber composites offer high strength, stiffness and lightweight properties while also reducing material use.
- Nanocomposites: the use of nanoparticle fillers creates materials that are physically stronger, heat-resistant, and self-reinforcing.
- In-Mold Electronics: In-Mould decoration (IMD) and In-Mould labelling (IML) allow electrical circuits and touch surfaces, to be produced in a single production stage, reducing part assemblies.
In summary, the injection molded plastic manufacturing industry is continually evolving, driven by technology advancements, material improvements, and growing sustainability concerns. Smart manufacturing, automation, sustainable materials, 3D printing, and composite materials are among the key trends and advancements shaping the future of the industry. These developments offer opportunities to create more efficient, cost-effective, and sophisticated injection molded plastic products to meet evolving market demands.
If you need about Plastic Injection Molding Services,You can click on the V1 Prototype website to find it.
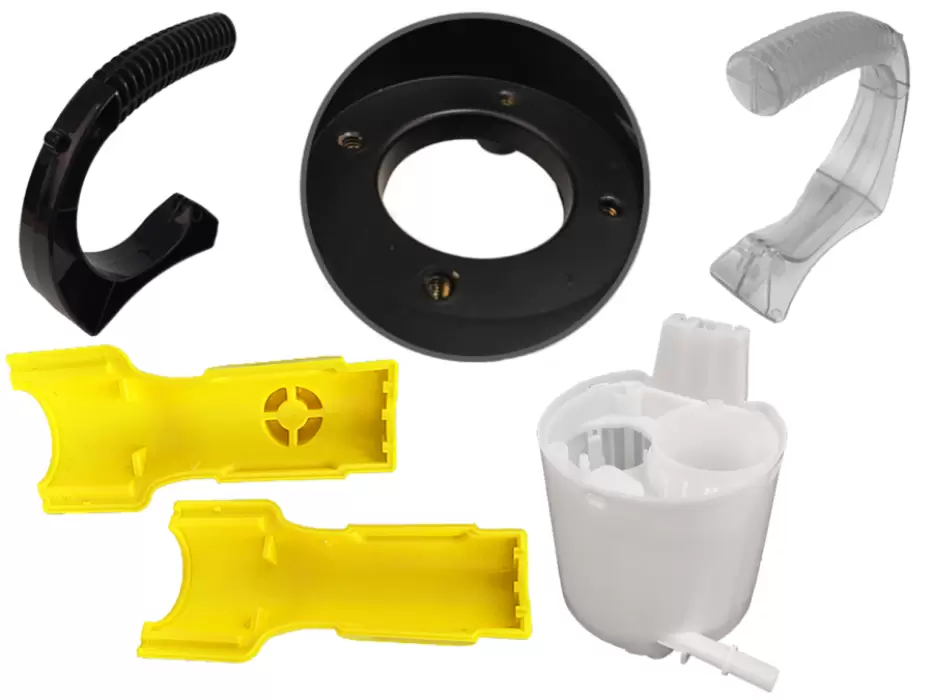
-
7.Conclusion
To recap, injection molded plastic manufacturing is a versatile and cost-effective process used to produce plastic products and parts for various industries and applications. The process involves heating molten plastic, injecting it into a mold, cooling it, and ejecting the final product. Quality control measures, certifications, and advancements in technology and materials play a vital role in ensuring that the products meet the required standards and specifications.
In terms of the future, the injection molded plastic manufacturing industry is evolving, with trends and advancements in smart manufacturing, automation, lightweight and high-strength materials, sustainability, 3D printing, and composite materials.
Based on the above, it is recommended that when choosing an injection molded plastic manufacturer, consider their quality control measures, certifications, and experience in the industry. Additionally, it will be worthwhile if manufacturers adopt new technologies and materials to produce their products, such as 3D printing, carbon fiber composites or in-mold electronics, to ensure they stay ahead of the competition.
In conclusion, the injection molded plastic manufacturing process is efficient, effective, and evolving, producing versatile and cost-effective products for various industries and applications. With advances in technology and materials, the industry is going to become even more efficient and capable of producing sophisticated products that meet the evolving needs of the market.