Table of Contents:
- Introduction
- Types of Rapid Prototyping Technologies
- Benefits of Rapid Prototyping
- Rapid Prototyping Process
- Industrial Applications of Rapid Prototyping
- Limitations and Challenges of Rapid Prototyping
- Future Scope of Rapid Prototyping in Industrial Models
- Conclusion
-
1.Introduction
Rapid prototyping is a process that has transformed the product development landscape across various industries. It involves the creation of a physical model or prototype of a product from a digital design, providing a quick and cost-effective way to test and refine product ideas.
The importance of rapid prototyping in product development cannot be underestimated, as it enables manufacturers to identify design flaws early in the development process, which can save time and money. Rapid prototyping also allows for faster product iterations, which can help bring products to market more quickly and with improved quality.
The use of rapid prototyping is not only restricted to large industries, but also is widely adopted by small businesses and entrepreneurs who are looking to develop new products, reduce product development risks and accelerate the commercialization process.
In the following sections, we will dive deeper into the benefits of rapid prototyping and the various techniques available to achieve these benefits.
-
2.Types of Rapid Prototyping Technologies
There are several types of rapid prototyping technologies utilized in the manufacturing industry, including:
- Stereolithography (SLA) - This method uses a laser to cure liquid resin layer by layer, creating a 3D model.
- Fused Deposition Modeling (FDM) - FDM involves extruding a thin layer of thermoplastic material that is heated in the printer head. This process creates a solid model from the ground up.
- Selective Laser Sintering (SLS) - This technique involves the use of a laser to sinter powdered material, such as nylon, into a solid shape layer by layer.
- Digital Light Processing (DLP) - DLP is similar to SLA, but instead of a laser, a projector is used to cure the liquid resin into a solid shape layer by layer.
- Continuous Liquid Interface Production (CLIP) - CLIP used a light source to cure a liquid resin continuously, allowing for the creation of complex and robust shapes.
Each technique has its advantages and disadvantages, with choices being largely dependent upon the application, materials, and end-use requirements. For example, while SLA produces a smooth surface finish, it may not be appropriate for larger models due to its limited size. Conversely, FDM is suitable for producing larger models, although its layer lines may be visible, requiring additional post-processing steps.
By selecting the appropriate technology for the project at hand, manufacturers can optimize product development processes, reduce costs, and improve product quality.
-
3.Benefits of Rapid Prototyping
The benefits of rapid prototyping are numerous and include, but are not limited to:
- Cost and Time Efficiency - Rapid prototyping is a cost-effective solution for companies to produce prototypes quickly and efficiently. This technique reduces the need for tooling, molds or dies, and streamlines product development, allowing the manufacturing process to move more swiftly. It lowers production costs and lowers the risk of design errors, making the prototyping process more effective.
- Increased Design Flexibility - Rapid prototyping enables designers to have a high degree of design flexibility as it makes modifications feasible at the early stages of product development. Prototyping allows iterative changes to be made to a design, enabling product line evolution and implementation of custom features to meet specified requirements.
- Production Efficiency and Quality Improvement - By using rapid prototyping, the manufacturing process can move faster and more efficiently, reducing lead times and time-to-market. Additionally, rapid prototyping allows for quicker feedback, hence, manufacturers can improve product quality by identifying design flaws and correcting errors. This ensures that the final product meets all the expected quality standards.
The benefits of rapid prototyping go beyond manufacturing processes as it is essential in developing and testing products such as medical devices, automotive equipment, and consumer electronics. With increased flexibility in design, better quality control, and reduced costs and lead times, rapid prototyping is widely regarded as a beneficial technology by product developers in various industries.
-
4.Rapid Prototyping Process
The rapid prototyping process consists of three key stages, which are:
- Input File Preparation - The first stage of the rapid prototyping process involves creating a digital 3D model of the product design. The 3D model is created using Computer-Aided Design (CAD) software, which can be easily modified at this stage to ensure product requirements are satisfied. The final 3D design file is then imported into the rapid prototyping machine in preparation for the next stage.
- 3D Printing Process - This is the stage where the 3D model is physically produced. The 3D printing process can involve different techniques and materials, depending on the method being used. For instance, in FDM, the printer head uses melted plastic in a process that can take several hours to produce the final product. In SLA, a liquid resin is cured using a light source in quick successions to create an intricate and accurate model.
- Post-Processing and Finishing - This is the last stage and involves refining the finished product to meet the required specifications. The finishing part can include post-processing operations such as smoothing the surfaces, painting, trimming off excess materials, or other finishing touches required for the final product to be completed.
In each of the stages, the 3D model is carefully examined to ensure that it meets the specified requirements, and every aspect of the product development is documented for future reference. Modifications can also be made as required to add new designs, materials, or improve the final product. By utilizing these stages, manufacturers can ensure that a well-refined and manufactured product is delivered to the market at a faster rate than traditional methods, in addition to lower production costs made possible by the reduced labor cost, shortened time-to-market and optimized product performance.
-
5.Industrial Applications of Rapid Prototyping
Rapid prototyping technology has become increasingly popular across various industries as it offers producers and manufacturers immense benefits when creating prototypes. Some of the industries that have adopted rapid prototyping techniques include but are not limited to;
- Automotive Industry - In the automotive industry, rapid prototyping has become essential in the production and design of engines, transmissions, or even entire vehicles. A prototype can be quickly produced, tested, and modified to yield a product that meets the performance specifications, while at the same time reducing the production time and costs, which is fundamental in a highly competitive industry.
- Aerospace Industry - The aerospace industry has also seen significant growth in rapid prototyping application, offering more precise and reliable 3D printed models that enable engineers to test designs quickly and efficiently. Rapid prototyping has enabled the development of intricate and complex designs, such as aerodynamic testing, engine parts, and structural brackets, improving the process of product creation and the characteristics of the final product.
- Medical Industry - The medical industry leverages rapid prototyping in manufacturing custom-made medical devices, such as surgical instruments, implants, and prosthetics. By utilizing rapid prototyping, the design process can be faster, more precise, and more affordable, offering quick and efficient customization to meet specific patient sizes or shapes.
- Consumer Goods Industry - Rapid prototyping within the consumer goods industry has enabled manufacturers to test and develop a wide range of products, such as toys, gadgets, appliances, or household items. With rapid prototyping, designers can test multiple variants of their models, improving the overall design quality, and reducing production costs and development time.
In summary, rapid prototyping is a revolutionary technology that has revolutionized product development across various industries by offering cost-effective, time-efficient, and highly precise 3D models. It has led to design improvements by lowering barriers for testing, improving the final product, and ultimately shaping market competition by creating higher-quality products at a faster rate while significantly reducing production costs.
-
6.Limitations and Challenges of Rapid Prototyping
Despite the numerous benefits of rapid prototyping, there are several limitations and challenges that manufacturers should consider, including:
- Material Limitations - The choice of material for rapid prototyping is limited to those that can be processed under specific rapid prototyping techniques. The cost of producing a prototype also depends on the type of material, with some materials being more expensive than others. This limitation may impact the design and functionality of the final product.
- Equipment Limitations - The size and capacity of the rapid prototyping machine affect the size of the product that can be created. Rapid prototyping machines also require regular maintenance to ensure their efficiency, which may result in potential downtime.
- Intellectual Property Issues - Rapid prototyping can lead to potential intellectual property issues that need to be carefully considered. Digital files of product designs can be easily downloaded, shared, or reverse-engineered, posing a risk in terms of copyright and patent infringement.
- Cost - Although rapid prototyping is cost-effective when compared to traditional prototyping, it still requires an initial investment in terms of machinery, materials, and skilled labor. It may also be costly when used for large-scale production, which is a setback for companies that work on a tight budget.
- Surface Quality - Some rapid prototyping techniques may not produce a high-quality surface finish or texture, hence, post-processing such as smoothing, sanding, or painting may be necessary to improve the model’s appearance.
To overcome these limitations, manufacturers need to fully understand the costs and benefits of rapid prototyping and choose the appropriate technique that best complements their production processes. It is crucial to consider these limitations and challenges when selecting a rapid prototyping technique to maximize efficiency and quality.
-
7.Future Scope of Rapid Prototyping in Industrial Models
The future scope of rapid prototyping is expected to be even more revolutionary than it currently is, with the following developments anticipated:
- Advancements in Materials and Equipment - Rapid prototyping has been dependent on the development of new materials; however, continuous research and improvements are expected to result in an even wider range of materials being available in the future. Also, equipment advancements are expected to reduce cost, improve time efficiency, and enable more significant production volume. Industrial-grade 3D printers with unmatched capabilities will allow businesses to build complex geometries and reduce design time significantly.
- Integration with Artificial Intelligence (AI) and Machine Learning - There are already developments aimed at integrating advanced and learning machines into the rapid prototyping process, which will enable designers and engineers to automate some of the key stages of product development such as testing and optimization. Through integrating AI with rapid prototyping machines, it will be much easier to identify and fix design problems, and move to the next iteration of the product idea quickly, thus enhancing the overall product development process.
- Potential of 4D Printing - Future research is expected to enable the development of 4D-printing technologies, where the fourth dimension is time. This technology would allow materials to change shape, orientation, adapting to certain environments and can add some exciting and innovative methods to create self-assembling structures, smart materials or products that can adjust themselves to different temperature levels, lighting or water.
The future of rapid prototyping in industrial models is bright, and its potential is yet to be fully realized. Rapid prototyping has revolutionized the way manufacturers create prototypes, and the integration of AI and machine learning will be a massive milestone for product development by improving efficiency and scaling production. By integrating 4D printing, design flexibility and functionality will also be magnified, leading to better products that align with specific user needs.
Click on the V1 Prototype website to gain more Rapid Prototyping information.
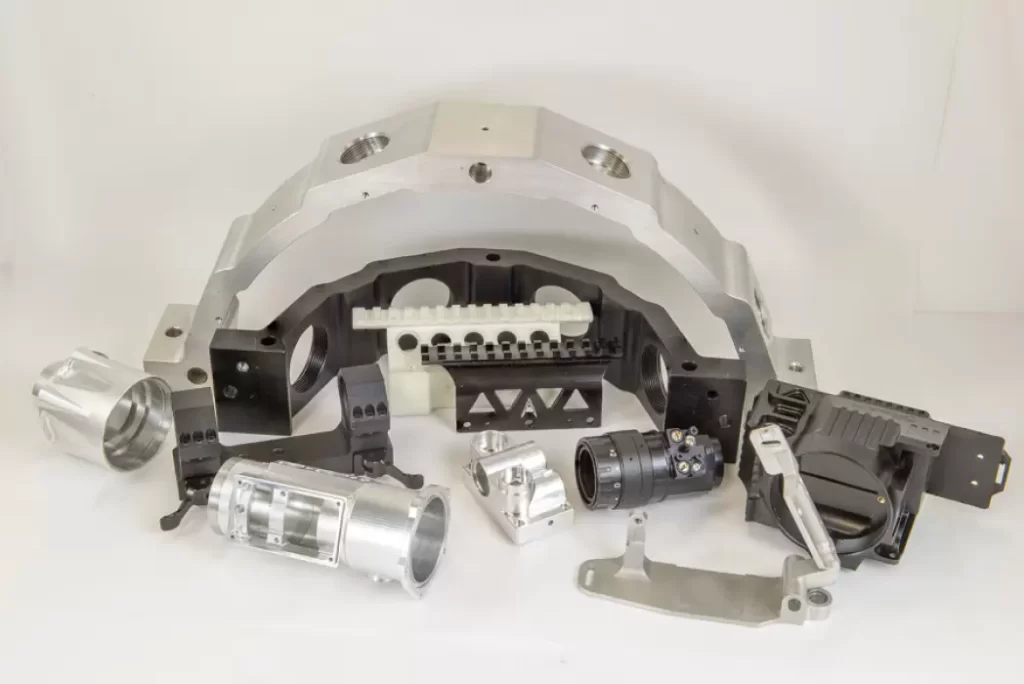
-
8.Conclusion
In conclusion, rapid prototyping has become an essential technology for manufacturers and designers across industries, allowing for faster, more efficient and cost-effective product development, leading to increased market competitiveness. The benefits of rapid prototyping, such as increased design flexibility, improved quality control and production efficiency, are numerous, as detailed above. However, some limitations also exist, such as material availability limitations and intellectual property issues.
Future research and development in rapid prototyping are expected to lead to advancements in materials, techniques, and equipment, leading to higher quality products and more cost-effective production. Also, integration with AI and machine learning and 4D printing technology presents opportunities for innovations in product design and greater efficiencies in the development process.
Overall, rapid prototyping remains an essential technology for businesses that want to stay ahead of their competition, and the potential use cases and possibilities for innovation are considerable. It is, therefore, crucial that businesses take advantage of the technology’s current capabilities while carefully monitoring the latest advancements and adopting them when justified by the cost-benefit observations.
Q1: What is rapid prototyping, and how does it apply to industrial models in product development?
A1: Rapid prototyping is a technology-driven process that involves quickly creating physical models or prototypes of products using computer-aided design (CAD) data. In the context of industrial models for product development, rapid prototyping allows engineers and designers to visualize and test their concepts swiftly before proceeding to full-scale production. It enables them to identify design flaws, make necessary improvements, and gain valuable insights into the functionality and aesthetics of the final industrial model.
Q2: How does rapid prototyping enhance the product development process in industrial settings?
A2: Rapid prototyping offers several advantages in industrial product development:
- Accelerated Iteration: The quick turnaround time in creating prototypes allows for multiple iterations, speeding up the design and development process.
- Design Validation: Physical prototypes help validate design concepts, ensuring they meet performance requirements and user expectations.
- Cost Savings: Early identification of design flaws and improvements minimizes the need for costly modifications during later stages of production.
- Stakeholder Collaboration: Physical prototypes facilitate communication and collaboration among various stakeholders, including designers, engineers, and clients.
Q3: What are some common rapid prototyping technologies used in industrial model development?
A3: There are several rapid prototyping technologies employed in industrial model development, including:
- 3D Printing/Additive Manufacturing: Utilizing additive processes to build models layer by layer using materials like plastics, metals, or resins.
- CNC Machining: Employing computer-controlled machines to carve out models from solid blocks of materials like metals or plastics.
- Vacuum Casting: Creating silicone molds from master patterns and then casting replicas using various materials like polyurethane resins.
- Sheet Metal Prototyping: Utilizing sheet metal fabrication techniques to create prototypes of industrial components and enclosures.
Q4: How does rapid prototyping impact the overall success of industrial product development?
A4: Rapid prototyping significantly contributes to the success of industrial product development in the following ways:
- Faster Time-to-Market: Rapidly developing and iterating prototypes allows for quicker product launches, gaining a competitive edge.
- Improved Design Optimization: Early identification and resolution of design issues lead to higher-quality, more functional, and user-friendly products.
- Enhanced Innovation: The ability to experiment and explore different design concepts fosters innovation and creativity within the development process.
- Customer Satisfaction: By ensuring the final industrial model meets or exceeds customer expectations, rapid prototyping contributes to higher customer satisfaction and loyalty.