Table of Contents:
- Introduction
- Techniques of Precise Injection Molding
- Benefits of Precise Injection Molding
- Applications of Precise Injection Molding
- Challenges and Limitations of Precise Injection Molding
- Future Directions for Precise Injection Molding
- Conclusion
1.Introduction
Precise injection molding is a manufacturing process that involves injecting molten material into a mold to create a product with high dimensional accuracy and consistency. It is a highly efficient and cost-effective method used in the production of a wide range of products, from small intricate parts to larger components.
The importance of precise injection molding lies in its ability to produce high-quality products with tight tolerances, repeatability, and consistency. This results in products that meet strict industry standards and customer requirements, making them suitable for use in critical applications such as medical devices, aerospace components, and electronics. Precise injection molding has revolutionized manufacturing and has become a preferred method for producing complex and intricate parts with high precision and accuracy.
-
2.Techniques of Precise Injection Molding
Precise injection molding involves several techniques that ensure the production of high-quality and consistent products. These techniques include:
- The Injection Molding Process: The injection molding process involves several steps, including material preparation, injection, packing, cooling, and ejection. In the material preparation step, the raw material is melted and injected into the mold. In the injection step, the material is injected into the mold with high pressure to ensure that it fills the mold cavity. In the packing step, additional material is added to the mold to ensure that the product is dense and has no voids. The cooling step involves cooling the mold to solidify the material, and the ejection step involves removing the finished product from the mold.
- Factors Affecting Precise Injection Molding: Several factors can affect the quality and consistency of the final product. These factors include material selection, process parameters, mold design, and equipment quality. Material selection involves choosing the right material for the product, considering factors such as durability, strength, and flexibility. Process parameters include temperature, pressure, and speed, which affect the molding process’s efficiency and accuracy. Mold design involves selecting the right material, designing the mold with precise dimensions, and ensuring that the mold is durable and can withstand the production process. Equipment quality includes the quality of the injection molding machine, which affects the efficiency and accuracy of the injection molding process.
- Precision Mold Design and Fabrication: Precision mold design and fabrication are crucial for producing high-quality products. Mold design involves selecting the right material, designing the mold with precise dimensions, and ensuring that the mold is durable and can withstand the production process. Mold fabrication involves creating the mold based on the design specifications, using advanced techniques such as computer-aided design (CAD) and computer-aided manufacturing (CAM) to ensure precision and accuracy. The mold must be made with high-quality materials and undergo rigorous testing to ensure that it can withstand the injection molding process and produce high-quality products.
-
3.Benefits of Precise Injection Molding
Precise injection molding offers numerous benefits to manufacturers and customers alike. These benefits include:
- Cost-effectiveness: Precise injection molding is a highly efficient and cost-effective method of manufacturing. It allows manufacturers to produce high-quality products with tight tolerances and consistent quality, reducing the need for additional finishing processes and minimizing waste. This, in turn, reduces manufacturing costs and improves overall profitability.
- Enhanced Product Quality: Precise injection molding enables manufacturers to produce products with high precision and accuracy, ensuring that they meet strict industry standards and customer requirements. This results in products that are of consistent quality, have excellent surface finishes, and are free from defects such as warping, sink marks, and voids.
- Reduced Scrap Rates: Precise injection molding reduces the likelihood of defects and other issues that can lead to high scrap rates. This, in turn, reduces waste and improves the overall efficiency of the manufacturing process.
- Increased Productivity: Precise injection molding enables manufacturers to produce products more quickly and efficiently than other manufacturing methods. This results in higher production rates and improved productivity, which can help manufacturers meet demand and increase revenue.
- Environmental Sustainability: Precise injection molding is a more environmentally sustainable manufacturing method than other methods such as machining or casting. It generates less waste, uses less energy, and has a lower carbon footprint, making it a more sustainable option for manufacturers and customers alike.
-
4.Applications of Precise Injection Molding
Precise injection molding has a wide range of applications across many industries, including:
- Medical Devices: Precise injection molding is widely used in the production of medical devices such as syringes, catheters, and surgical instruments. The high precision and accuracy of the molding process ensure that these products meet strict industry standards and are safe for use in medical applications.
- Aerospace: The aerospace industry requires high-quality components that can withstand extreme conditions and perform reliably. Precise injection molding is used to produce complex and intricate parts for use in aircraft, spacecraft, and other aerospace applications.
- Electronics: Precise injection molding is used in the production of electronic components such as connectors, switches, and housings. The process enables manufacturers to produce small, intricate parts with high precision and accuracy, making it ideal for use in electronics manufacturing.
- Automotive: The automotive industry requires high-quality components that can withstand the rigors of use and provide reliable performance. Precise injection molding is used to produce parts such as fuel systems, sensors, and engine components, ensuring that they meet strict industry standards and customer requirements.
- Consumer Goods: Precise injection molding is widely used in the production of consumer goods such as toys, household appliances, and sporting equipment. The process enables manufacturers to produce high-quality products with consistent quality and excellent surface finishes, ensuring that they meet customer demands and industry standards.
-
5.Challenges and Limitations of Precise Injection Molding
While precise injection molding offers numerous benefits, it also presents some challenges and limitations, including:
- Complexity of Process: Precise injection molding is a complex manufacturing process that requires specialized knowledge, skills, and equipment. The process involves several steps, including material selection, mold design and fabrication, and process optimization. Ensuring that each step is executed correctly requires expertise and experience.
- Equipment Costs: Precise injection molding requires specialized equipment, including injection molding machines, molds, and auxiliary equipment. The cost of acquiring and maintaining this equipment can be high, making it challenging for smaller manufacturers to adopt the process.
- Material Selection: The success of precise injection molding depends on selecting the right material for the product. Different materials have different properties, and selecting the wrong material can lead to defects, inconsistent quality, and other issues.
- Skilled Labor: Precise injection molding requires skilled labor to operate and maintain the equipment and carry out the manufacturing process. Finding skilled labor can be challenging, and training employees in the specialized knowledge and skills required can be time-consuming and expensive.
-
6.Future Directions for Precise Injection Molding
The future of precise injection molding is promising, with advancements in technology, innovation in materials, and emerging applications driving its growth and development. Some of the future directions for precise injection molding include:
- Advancements in Technology: As technology continues to advance, precise injection molding is likely to become more efficient, accurate, and cost-effective. Advancements in machine learning, artificial intelligence, and automation are expected to improve the process by optimizing material selection, mold design, and process control.
- Innovation in Materials: New materials are constantly being developed, and innovation in material science is likely to have a significant impact on precise injection molding. Advances in materials such as biodegradable plastics, nanocomposites, and high-performance polymers are expected to expand the range of products that can be produced using the process.
- Emerging Applications: Precise injection molding is being applied to new and emerging applications, such as 3D printing, microfluidics, and bioengineering. These applications are expected to drive innovation in the process by requiring new materials, designs, and manufacturing methods.
Click on the V1 Prototype website to gain more information.
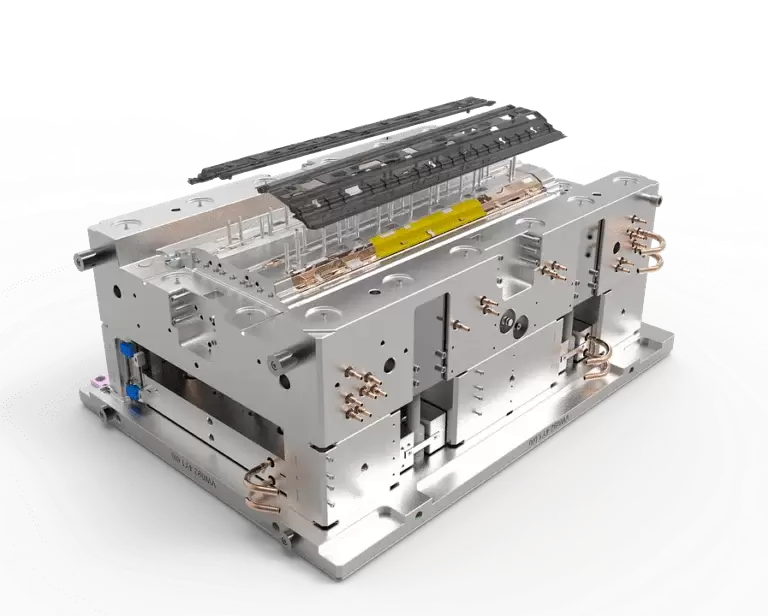
-
7.Conclusion
Precise injection molding is a highly versatile and efficient manufacturing process that enables the production of complex and high-quality products with consistent accuracy and excellent surface finishes. This article has discussed the various aspects of precise injection molding, including the techniques, benefits, applications, challenges, and future directions for the process.
Some of the key takeaways from this discussion include:
- Precise injection molding is a complex process that requires specialized knowledge, skills, and equipment.
- The process offers numerous benefits, including cost-effectiveness, enhanced product quality, reduced scrap rates, increased productivity, and environmental sustainability.
- Precise injection molding has a wide range of applications across many industries, including medical devices, aerospace, electronics, automotive, and consumer goods.
- The process presents some challenges and limitations, including the complexity of the process, equipment costs, material selection, and the need for skilled labor.
- The future of precise injection molding is promising, with advancements in technology, innovation in materials, and emerging applications driving its growth and development.
In conclusion, precise injection molding is a highly effective and efficient manufacturing process that offers numerous benefits for many industries. As technology continues to advance and materials science continues to innovate, precise injection molding is likely to become an increasingly popular method of manufacturing for many applications, enabling the production of complex and high-quality products with consistent accuracy and excellent surface finishes.
Precise injection molding is a process that produces high-quality plastic parts with complex geometries and tight tolerances. Precise injection molding involves the use of advanced equipment, software, and techniques to optimize the design, fabrication, and assembly of plastic components. Precise injection molding can offer several benefits for various applications, such as:
- Improved product performance and functionality
- Reduced material waste and production costs
- Enhanced aesthetic appeal and customer satisfaction
- Increased design flexibility and innovation
Some of the techniques that are used in precise injection molding include:
- Computer-aided design (CAD) and computer-aided engineering (CAE) software to create and simulate the optimal mold design and injection parameters
- Rapid prototyping and 3D printing to test and validate the product concept and functionality
- High-precision mold making and machining to ensure the accuracy and quality of the mold cavity and core
- High-performance injection molding machines and controllers to control the temperature, pressure, speed, and time of the injection cycle
- In-mold sensors and monitors to measure and adjust the process variables in real time
- Post-molding inspection and testing to verify the dimensional accuracy, mechanical properties, and surface quality of the molded parts
Precise injection molding can be applied to various industries and products, such as:
- Medical devices and equipment
- Automotive parts and accessories
- Aerospace and defense components
- Consumer electronics and appliances
- Industrial machinery and tools
Precise injection molding is a challenging and demanding process that requires a high level of expertise, experience, and quality control. However, when done correctly, precise injection molding can deliver superior results that meet or exceed the customer's expectations.