This comprehensive article delves into the SLA (Stereolithography) additive manufacturing process, exploring the materials used, and highlighting its various applications across industries. SLA, a popular 3D printing technology, offers precision and versatility in creating complex parts and prototypes. Read on to discover how SLA works, the materials compatible with this process, and how it's revolutionizing product development and manufacturing.
I. Introduction to SLA Additive Manufacturing
Overview of SLA Technology
Stereolithography (SLA) Additive Manufacturing, born in the 1980s, marked a groundbreaking shift in the world of 3D printing. Unlike traditional subtractive manufacturing, SLA builds objects layer by layer from a liquid resin using a precision laser. This laser selectively cures the resin, solidifying it into a precise 3D structure. This method allows for the creation of intricate and complex geometries that would be challenging or impossible with traditional manufacturing techniques.
Advantages and Limitations
The advantages of SLA are multifaceted. Its ability to produce high-resolution prints with exceptional surface quality makes it a preferred choice for applications demanding intricate details, such as jewelry design and dental models. However, limitations include material constraints, as SLA is primarily resin-based, and the post-processing requirements can be time-consuming. Striking a balance between these advantages and limitations is essential when considering SLA for a particular application.
II. The SLA Process: Step-by-Step
Pre-Processing: Design and File Preparation
The pre-processing phase sets the stage for successful SLA printing. Design considerations include geometry, support structures, and print orientation, ensuring optimal results. Software tools like CAD (Computer-Aided Design) play a pivotal role in translating these designs into printable files. Addressing potential challenges during pre-processing is crucial for a seamless transition to the printing phase.
The Printing Process: Layer by Layer
The core of SLA lies in its layer-by-layer printing process. Beginning with the creation of the first layer, the printer's laser scans the liquid resin, solidifying it selectively. This process repeats until the entire object is formed. Understanding the interplay between layer thickness, resolution, and printing speed is key to achieving the desired balance between precision and efficiency.
Post-Processing: Cleaning, Curing, and Finishing
Post-processing transforms raw SLA prints into refined products. Cleaning removes excess resin, and curing ensures the final object achieves its intended material properties. Finishing touches, such as sanding and polishing, enhance the aesthetic and functional aspects. Each step in post-processing contributes to the overall quality and usability of the 3D-printed object.
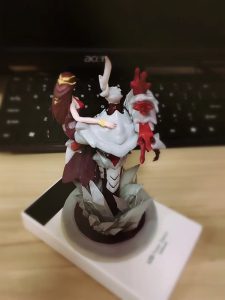
III. Materials Used in SLA Additive Manufacturing
Overview of Resins
The heart of SLA lies in its diverse range of resins. These resins, typically liquid polymers, vary in composition and properties. UV-curable resins are the most common, solidifying under the influence of ultraviolet light. The selection of resins significantly influences the mechanical, thermal, and optical properties of the final printed object.
Standard Resins
Standard resins form the foundational material for many SLA applications. They strike a balance between affordability and versatility, making them suitable for rapid prototyping and general-purpose modeling. Their properties cater to a wide range of applications, making them a go-to choice for various industries.
Engineering Resins
Engineered resins are tailored for specific performance requirements, such as high strength, heat resistance, or flexibility. These resins open up new possibilities for creating functional prototypes and end-use parts. Industries ranging from aerospace to consumer electronics benefit from the precision and durability offered by engineering resins.
Dental and Medical Resins
The dental and medical industry leverages SLA to produce highly accurate and customized solutions. Dental resins, for instance, enable the creation of detailed dental models and crowns. Medical resins are designed to be biocompatible, facilitating the production of patient-specific surgical guides and anatomical models.
Other Specialty Resins
Beyond the mainstream, specialty resins cater to niche applications. Transparent resins find utility in optical prototypes, while flexible resins contribute to the production of wearables and soft-touch components. This diversification of resins allows SLA to address a broad spectrum of industrial needs.
Material Properties and Considerations
Understanding material properties is pivotal in selecting the right resin for a given application. Factors such as tensile strength, hardness, and elongation at break play a crucial role in determining the suitability of a material for a specific use case. Material considerations extend beyond mechanical properties, encompassing factors like chemical resistance and biocompatibility.
Material Selection Guide
A material selection guide acts as a compass for manufacturers and designers navigating the vast landscape of available resins. It takes into account application-specific requirements, guiding users to choose resins that align with their project goals. This guide empowers decision-makers to make informed choices, ensuring the success of their SLA projects.
IV. Applications of SLA Additive Manufacturing
Prototyping and Product Development
SLA has become synonymous with rapid prototyping, accelerating the product development lifecycle. Its ability to produce high-quality prototypes with intricate details enables designers and engineers to iterate quickly, reducing time-to-market and overall development costs. Prototyping using SLA is prevalent across industries, from electronics to consumer goods.
Jewelry and Art
The precision and fine detailing capabilities of SLA have positioned it as a transformative tool for jewelry designers and artists. From intricate filigree work to custom-designed pieces, SLA empowers artisans to translate their visions into tangible, high-quality jewelry. The technology's role in the art world extends beyond functionality, delving into the realm of creative expression.
Dental and Medical Industry
In the healthcare sector, SLA has revolutionized the production of dental and medical components. Dental labs utilize SLA for creating detailed dental models, crowns, and bridges. Moreover, the technology enables the fabrication of patient-specific surgical guides, prosthetics, and anatomical models. The precision and customization offered by SLA contribute significantly to improved patient outcomes.
Architecture and Construction
SLA is breaking new ground in architecture and construction by facilitating the rapid prototyping of architectural models. Architects and designers leverage SLA to transform digital designs into physical prototypes, allowing for a tangible and detailed understanding of complex structures. This application streamlines the design and validation process in the architectural and construction industries.
Automotive and Aerospace
The automotive and aerospace industries benefit from SLA's ability to produce intricate and lightweight components. Prototyping critical parts, such as engine components and aerodynamic structures, allows for efficient testing and validation. SLA's contribution extends beyond prototyping to the production of end-use parts, demonstrating its versatility in these high-performance sectors.
Other Industrial Applications
SLA's impact spans a multitude of industrial applications. From creating custom tooling and molds to producing functional prototypes for testing, SLA addresses the unique needs of various industries. Its adaptability and precision make it a valuable asset in manufacturing processes where customization, speed, and accuracy are paramount.
V. Conclusion
The Future of SLA Additive Manufacturing
Looking ahead, the future of SLA is marked by continuous innovation and evolution. Advancements in materials, including biodegradable resins and hybrid materials, will broaden the application spectrum. Integration with emerging technologies, such as artificial intelligence and machine learning, holds the potential to enhance efficiency and further streamline the SLA process.
Impact on Manufacturing and Design Industries
The impact of SLA on manufacturing and design industries is transformative. Beyond its role in rapid prototyping, SLA is influencing design thinking and pushing the boundaries of what's possible. The shift towards on-demand, localized manufacturing is reshaping supply chains, reducing waste, and democratizing the production process. As SLA continues to mature, its ripple effects will be felt across industries, fostering a new era of creativity, efficiency, and sustainable manufacturing.