Table of Contents:
- Introduction
- Types of Tooling Molds
- Materials Used for Tooling Molds
- Design Considerations for Tooling Molds
- Tooling Mold Applications
- Tooling Mold Manufacturing Process
- Tooling Mold Maintenance and Repair
- Tooling Mold Quality Control and Testing
- Conclusion
-
1.Introduction
Welcome to this guide on tooling molds. Tooling molds are an essential component in the manufacturing industry, used to produce a wide range of products such as automotive parts, consumer goods, packaging materials, and more. They are critical in ensuring product consistency, precision, and quality.
The purpose of this guide is to provide a comprehensive overview of tooling molds, their types, materials used, design factors to consider, manufacturing process, maintenance, and cost. This guide aims to help you understand the importance of tooling molds in manufacturing and how to make informed decisions when selecting or designing molds for your products.
-
2.Types of Tooling Molds
Injection Molds:
Injection molds are the most commonly used type of tooling molds. They are used to produce a wide range of products, including toys, automotive parts, medical devices, and more. Injection molds are made of two halves, the cavity and the core, which are used to form the shape of the final product. Molten plastic is injected into the cavity, and when it cools and hardens, the mold is opened, and the part is ejected.
Blow Molds:
Blow molds are used to create hollow parts such as bottles, containers, and tanks. They are made of two halves, the cavity and the core, which are used to form the shape of the final product. Molten plastic is injected into the cavity, and air is blown into it to expand the plastic and create the hollow shape. When the plastic cools and hardens, the mold is opened, and the part is ejected.
Compression Molds:
Compression molds are used to produce parts that require high strength and durability, such as automotive and aerospace parts. In compression molding, the material is preheated and placed in an open mold cavity. The mold is then closed, and pressure is applied to compress the material into the desired shape. The material is then allowed to cool and harden before the mold is opened, and the part is ejected.
Transfer Molds:
Transfer molds are used to produce parts that require multiple colors or materials. In transfer molding, the material is placed in a transfer pot and then transferred to the mold cavity under pressure. The material is then allowed to cool and harden before the mold is opened, and the part is ejected.
Thermoforming Molds:
Thermoforming molds are used to produce products from thin sheets of plastic, such as food packaging, trays, and containers. In thermoforming, a sheet of plastic is heated until it becomes soft and pliable. The sheet is then placed in a mold, and a vacuum is used to draw the plastic into the shape of the mold. The plastic is then allowed to cool and harden before the mold is opened, and the part is ejected.
-
3.Materials Used for Tooling Molds
The materials used for tooling molds play a critical role in determining the quality, durability, and cost of the mold. Here are some of the most commonly used materials for tooling molds:
Steel:
Steel is the most commonly used material for tooling molds because it is strong, durable, and has excellent heat resistance. The most commonly used steel types for molds are P20, H13, and S7. P20 is a low-carbon mold steel that is easy to machine and has good wear resistance. H13 is a hot work tool steel that is highly heat-resistant and durable. S7 is a shock-resistant tool steel that is highly versatile and can be used for a wide range of applications.
Aluminum:
Aluminum is a lightweight material that is easy to machine and has excellent thermal conductivity. It is commonly used for tooling molds for products that require fast cooling, such as thin-walled products. Aluminum molds are also used for prototyping, as they are cheaper and quicker to produce than steel molds.
Copper:
Copper is an excellent conductor of heat and is used for molds that require fast cooling. It is also highly corrosion-resistant and is often used for molds that come into contact with corrosive materials.
Zinc:
Zinc is a soft and ductile metal that is commonly used for low-volume production molds. It is easy to machine and has excellent heat transfer properties. Zinc molds are also less expensive than steel or aluminum molds.
Other Materials:
Other materials that are used for tooling molds include brass, nickel, titanium, and various types of plastics. These materials are typically used for specialized applications, such as high-precision molding or molding of unique shapes.
-
4.Design Considerations for Tooling Molds
Designing a tooling mold is a complex process that requires careful consideration of various factors to ensure optimal performance and quality of the molded product. Here are some of the critical design considerations for tooling molds:
Mold Flow Analysis:
Mold flow analysis is a crucial step in designing tooling molds, as it helps to identify potential issues with flow and cooling of the plastic material. Mold flow analysis involves using computer-aided design (CAD) software to simulate the flow of plastic material through the mold and identify areas of potential problems such as weld lines, air traps, and sink marks.
Parting Line Design:
The parting line is the line where the two halves of the mold come together. It is essential to design the parting line correctly to ensure that the molded part is of the desired shape and size. The location of the parting line should be chosen carefully to avoid visible parting lines or areas where the plastic material may trap air.
Draft Angles:
Draft angles are the angles on the sides of the mold that allow the molded part to be removed from the mold easily. Draft angles are necessary to ensure that the part does not get stuck in the mold, and there is no damage to the mold or the part during ejection.
Gate Design:
The gate is the opening in the mold where the plastic material enters. The design of the gate is crucial to ensure that the plastic material flows correctly and that there are no air traps or other defects in the molded part. The size and location of the gate should be chosen carefully to ensure optimal flow and minimal waste.
Cooling System Design:
The cooling system is a crucial aspect of the mold design, as it helps to control the cooling rate of the plastic material and prevent warpage or other defects in the molded part. The cooling system should be designed to ensure that the plastic material cools uniformly and quickly without creating stress in the part.
By taking into account these design considerations, tooling molds can be designed to produce high-quality, defect-free molded products efficiently and cost-effectively.
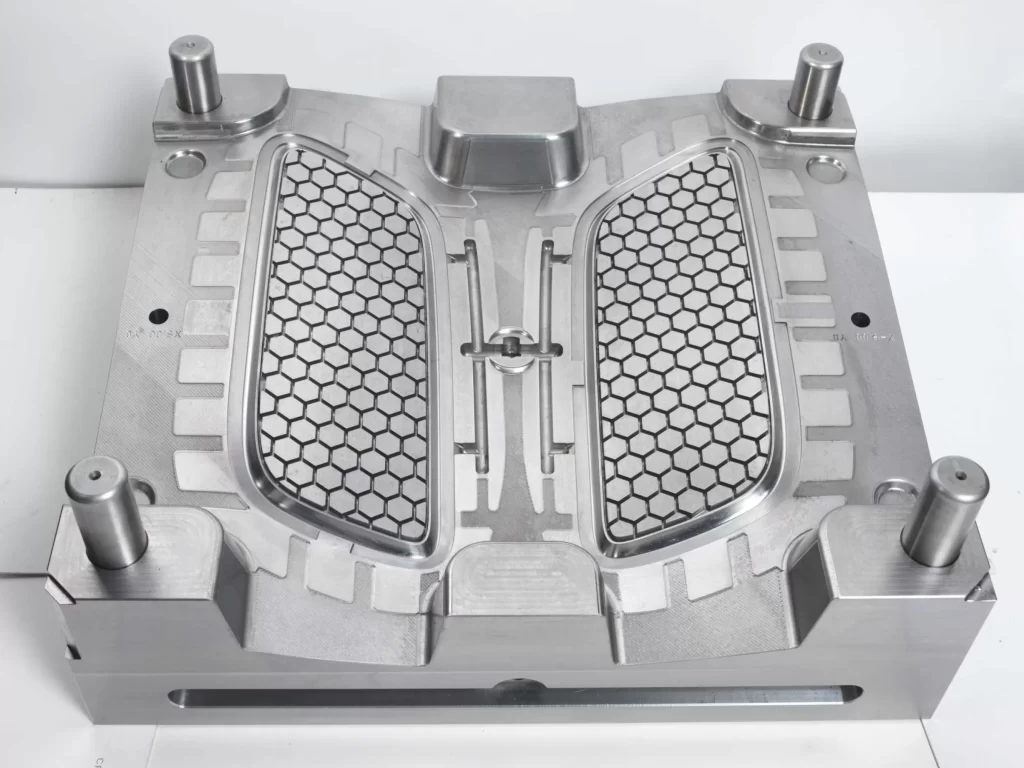
-
5.Tooling Mold Applications
Tooling molds find their applications in various industries, such as the automotive industry, packaging industry, consumer goods industry, medical industry, and aerospace industry. Here are some of the applications of tooling molds in different industries:
The automotive industry uses tooling molds extensively for the production of various parts, such as dashboards, seats, engine components, and body panels. Injection molds are commonly used in the automotive industry due to their ability to produce large volumes of parts quickly and accurately.
Packaging Industry:
The packaging industry uses tooling molds for the production of packaging materials such as bottles, caps, and containers. Blow molds are commonly used in the packaging industry due to their ability to produce hollow containers with intricate shapes and sizes.
Consumer Goods Industry:
The consumer goods industry uses tooling molds for the production of various products such as toys, electronics, and appliances. Injection molds and thermoforming molds are commonly used in the consumer goods industry due to their ability to produce parts with complex shapes and designs.
The medical industry uses tooling molds for the production of various medical devices and equipment such as syringes, implants, and prosthetics. Injection molds and compression molds are commonly used in the medical industry due to their ability to produce parts with high precision and accuracy.
The aerospace industry uses tooling molds for the production of various parts, such as engine components, landing gear, and fuselage parts. The molds used in the aerospace industry are typically made of high-strength materials such as steel and aluminum to withstand the extreme conditions of space travel.
In conclusion, tooling molds are an essential component in various industries and play a vital role in the production of high-quality, precise parts and products.
If you need more about Tooling Mold information ,You can click on the V1 Prototype website to find it.
-
6.Tooling Mold Manufacturing Process
The tooling mold manufacturing process involves several stages, starting from design and engineering to assembly and finishing. Here are the different stages involved in the tooling mold manufacturing process:
Design and Engineering:
The first stage in the tooling mold manufacturing process is design and engineering. In this stage, the mold design is created based on the product specifications and requirements. Mold flow analysis is conducted to ensure the mold design is optimized for efficient production and quality control.
Machining and Fabrication:
Once the mold design is finalized, the next stage is machining and fabrication. The mold is typically machined from a block of raw material such as steel, aluminum, or copper. CNC machines are used to cut the mold into the desired shape and size. This stage is critical as the precision of the mold directly impacts the quality of the finished product.
Heat Treatment:
After the mold has been machined, it undergoes a heat treatment process. The heat treatment process involves heating the mold to a specific temperature and then rapidly cooling it to harden the mold material. This process helps to improve the strength and durability of the mold, allowing it to withstand the stress of the injection or blow molding process.
Assembly and Finishing:
The final stage in the tooling mold manufacturing process is assembly and finishing. In this stage, the different components of the mold, such as the core and cavity, are assembled together. The mold is then finished and polished to improve its surface finish and reduce the risk of defects in the finished product.
In conclusion, the tooling mold manufacturing process is a complex and multi-stage process that requires expertise and precision at every stage. Each stage is critical in ensuring that the mold is of high quality and able to produce parts that meet the required specifications and standards.
-
7.Tooling Mold Maintenance and Repair
Tooling molds are expensive and critical components in the manufacturing process, and their proper maintenance and repair are essential to their longevity and continued efficiency. In this section, we will explore the importance of mold maintenance and repair, common issues with tooling molds, and the different methods used for mold cleaning, storage, repair, and modification.
Importance of Mold Maintenance and Repair:
Proper mold maintenance is essential to ensure that molds function optimally, produce quality parts, and last as long as possible. Failure to maintain tooling molds can result in production downtime, increased scrap rates, and higher manufacturing costs. Regular mold maintenance can prevent problems such as wear and tear, corrosion, and damage caused by repeated use.
Common Issues with Tooling Molds:
Tooling molds can experience various problems, such as corrosion, wear and tear, and damage caused by repeated use. Some of the most common issues with tooling molds include warping, cracking, and damage to the cooling system. Additionally, environmental factors, such as temperature and humidity, can also impact the performance and longevity of molds.
Mold Cleaning and Storage:
Proper mold cleaning and storage are essential to maintain the integrity of tooling molds. Mold cleaning involves removing any residue or contaminants from the mold surface, while mold storage involves storing molds in a dry, temperature-controlled environment to prevent corrosion and other types of damage.
Mold Repair and Modification:
In some cases, tooling molds may require repair or modification to improve their performance or accommodate changes in product design or materials. Common mold repair and modification techniques include welding, grinding, and polishing. Additionally, mold modification can involve adding or removing sections of the mold to change its shape or accommodate new product designs.
In conclusion, proper tooling mold maintenance and repair are essential to their longevity and continued performance. By taking steps to prevent common mold issues, such as wear and tear and damage, and implementing proper cleaning and storage techniques, manufacturers can ensure that their tooling molds produce quality parts and last as long as possible.
-
8.Tooling Mold Quality Control and Testing
Quality control is a crucial aspect of tooling mold manufacturing and maintenance, as it ensures that molds meet the required standards for quality and functionality. In this section, we will explore the different quality control measures, mold inspection and testing techniques, and mold validation and certification procedures used in the tooling mold industry.
Quality Control Measures:
Tooling mold manufacturers and maintenance teams implement several quality control measures to ensure that molds meet the required quality standards. These measures may include visual inspections, dimensional inspections, material inspections, and mechanical inspections, among others. Additionally, quality control may involve the use of statistical process control techniques to monitor the performance of molds over time and identify potential issues before they result in quality problems.
Mold Inspection and Testing:
Mold inspection and testing involve a variety of techniques to assess the quality and functionality of tooling molds. These techniques may include visual inspections, dimensional inspections using measurement tools such as calipers and micrometers, material testing, and mechanical testing. Additionally, some mold inspection and testing techniques use advanced technologies such as x-ray imaging, ultrasound, and laser scanning to detect defects or measure surface characteristics.
Mold Validation and Certification:
Mold validation is a process that ensures that a mold is capable of producing parts that meet the required quality standards. The validation process may involve running test shots on the mold and analyzing the results to identify any quality issues. Once a mold has passed the validation process, it may be certified for use in production.
Certification of tooling molds involves verifying that the mold meets specific industry standards or customer requirements. This certification may involve testing the mold’s performance, assessing its design and construction, and ensuring that it meets any relevant regulatory requirements.
In conclusion, tooling mold quality control and testing are essential to ensure that molds meet the required quality standards for functionality and durability. By implementing quality control measures, conducting regular mold inspection and testing, and validating and certifying molds for use, manufacturers can ensure that their tooling molds produce quality parts and maintain optimal performance over time.
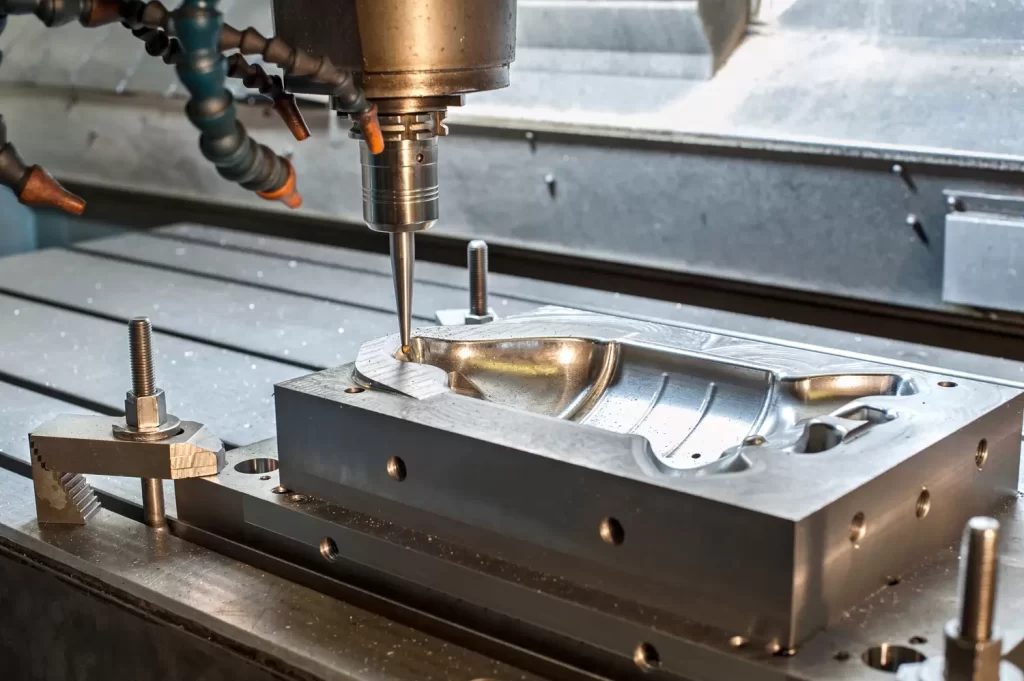
-
9.Conclusion
In conclusion, tooling molds play a critical role in the manufacturing industry, enabling the production of high-quality and consistent parts for various applications. The choice of mold type and materials is dependent on the specific application and production requirements. Proper design considerations, manufacturing processes, maintenance, and quality control measures ensure optimal mold performance and longevity.
As technology advances, the tooling mold industry is also evolving, with new materials and manufacturing techniques being developed to meet the changing demands of various industries. It is, therefore, important to keep up-to-date with the latest advancements in tooling molds to maximize their benefits in production.
Overall, tooling molds are a vital investment for any manufacturing operation, and proper attention and care should be given to ensure optimal performance and long-term profitability.