In the world of manufacturing, the process of machining is a crucial component that ensures the accuracy and quality of products. This article delves into the complexities of machining equipment processes, providing an in-depth analysis of how to optimize these processes for maximum efficiency and precision. Through expert insights, practical examples, and innovative strategies, readers will gain a comprehensive understanding of how to streamline their machining operations, reduce waste, and improve product outcomes.
I. Introduction
A. Overview of Machining Equipment Processes
Machining equipment processes play a crucial role in various industries, including manufacturing, aerospace, automotive, and many others. These processes involve the use of specialized tools and machines to shape and form raw materials into precise components or products. The efficiency and precision of these machining operations directly impact the quality, cost-effectiveness, and overall success of the manufacturing process.
B. Importance of Optimization in Machining
Optimization holds paramount importance in machining equipment processes. By optimizing these processes, manufacturers can achieve higher productivity, reduce costs, minimize material waste, and enhance the quality and precision of the final products. It involves strategically employing various techniques, technologies, and methodologies to maximize efficiency and accuracy throughout the machining workflow. This guide aims to provide insights into optimizing machining equipment processes, helping manufacturers achieve superior results.
II. Understanding Machining Equipment
A. Types of Machining Equipment
Machining equipment comprises a wide range of tools and machines, each designed to perform specific tasks in the manufacturing process. Some common types of machining equipment include lathes, milling machines, drilling machines, grinding machines, and CNC (Computer Numerical Control) machines. Each type offers unique capabilities and features that cater to different machining requirements, such as turning, milling, drilling, grinding, and precision cutting.
B. Basic Principles of Machining
At its core, machining involves removing material from a workpiece to shape it into the desired form and dimensions. The basic principles of machining remain consistent across different types of equipment. These principles include cutting, feeding, and speed. Cutting refers to the actual removal of material, feeding controls the rate at which the cutting tool engages with the workpiece, and speed determines the rotational or linear velocity of the cutting tool.
III. The Machining Process
A. Key Stages in the Machining Process
The machining process is a complex and intricate procedure that involves transforming raw materials into finished products. The process can vary depending on the type of material, the shape and size of the product, and the desired specifications. However, there are some general stages that apply to most machining processes. These are:
- Planning and design: This is the first and most important stage of the machining process. It involves determining the machining operations needed to produce the product, selecting the appropriate tools and equipment, and creating a detailed plan or blueprint. The planning and design stage requires careful analysis and calculation to ensure optimal efficiency and accuracy.
- Setup: This is the stage where the workpiece is prepared and positioned for machining. The workpiece is usually secured using clamps, vises, or fixtures to prevent movement or vibration during machining. The workpiece is also aligned and oriented according to the plan or blueprint. The setup stage requires attention to detail and precision to avoid errors or defects.
- Machining operations: This is the stage where the actual cutting, shaping, or drilling of the material takes place. The machining operations can be performed using various tools and equipment, such as lathes, mills, drills, saws, etc. The machining operations can be classified into two types: subtractive and additive. Subtractive machining removes material from the workpiece to create the desired shape or size. Additive machining adds material to the workpiece to create complex or intricate features.
- Inspection: This is the final stage of the machining process where the quality and accuracy of the machined product are verified. The inspection can be done using various methods and instruments, such as calipers, micrometers, gauges, etc. The inspection ensures that the product meets the specifications and standards required by the customer or industry.
B. Common Challenges and How to Overcome Them
The machining process is not without its challenges. Manufacturers often encounter various difficulties that can affect the efficiency and precision of their products. Some of these challenges include:
- Tool wear: This is a common problem that occurs when the tools used for machining become dull or damaged due to friction, heat, or impact. Tool wear can reduce the quality and performance of the tools, resulting in poor surface finish, dimensional inaccuracies, or tool breakage. To prevent tool wear, manufacturers should regularly inspect and maintain their tools, replace them when necessary, and use appropriate cutting speeds, feeds, and depths.
- Material deformation: This is a problem that occurs when the material being machined changes its shape or size due to external forces or stresses. Material deformation can cause distortions, warping, cracking, or bending of the product, affecting its functionality and appearance. To avoid material deformation, manufacturers should use proper cooling and lubrication systems to reduce heat generation and friction during machining. They should also use suitable materials that have high strength and resistance to deformation.
- Surface finish inconsistencies: This is a problem that occurs when the surface of the machined product has uneven or rough textures due to tool marks, scratches, burrs, or chips. Surface finish inconsistencies can affect the aesthetic appeal and performance of the product, such as its corrosion resistance, wear resistance, or friction coefficient. To improve surface finish consistency, manufacturers should use sharp and clean tools with smooth edges, adjust their cutting parameters accordingly, and apply finishing processes such as polishing or coating.
- Dimensional inaccuracies: This is a problem that occurs when the dimensions of the machined product deviate from the specifications or tolerances required by the customer or industry. Dimensional inaccuracies can compromise the functionality and reliability of the product, leading to rework or rejection. To ensure dimensional accuracy, manufacturers should use advanced metrology tools and techniques to measure their products with high precision and accuracy. They should also calibrate their machines regularly and follow strict quality control procedures.
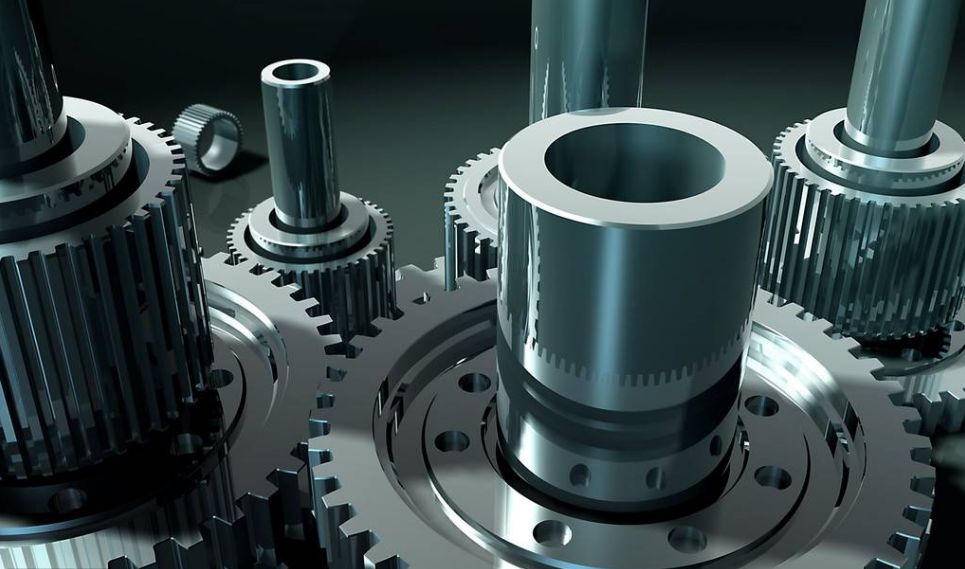
IV. Strategies for Optimizing Machining Equipment Processes
A. Techniques for Improving Efficiency
- Process Planning and Optimization: Thoroughly analyze the machining requirements and select the most suitable equipment and cutting parameters. Optimize tool paths and minimize unnecessary tool changes or idle time.
- Workpiece Material Selection: Choose materials that balance strength, machinability, and cost-effectiveness. Consider alternative materials or alloys that offer improved machinability without compromising performance.
- Cutting Tool Selection and Optimization: Select cutting tools based on the specific machining operation, material, and desired surface finish. Optimize cutting tool geometries, coatings, and speeds to maximize efficiency and tool life.
- Automation and Robotics: Integrate automated systems and robotic solutions to streamline machining processes, reduce human error, and increase productivity. Automated loading and unloading systems can minimize setup and changeover times.
B. Methods for Enhancing Precision
- Machine Calibration and Maintenance: Regularly calibrate and maintain machining equipment to ensure accuracy and repeatability. Periodic checks and alignments of machine components, such as spindles, slides, and tool holders, help maintain precision.
- Advanced Workpiece Fixturing: Invest in sophisticated workpiece fixturing techniques to securely hold and position the workpiece during machining. Proper fixturing minimizes vibrations and deflections, leading to improved precision.
- Tool Monitoring and Adaptive Control: Utilize advanced tool monitoring systems to detect tool wear, breakage, or abnormal conditions during machining. Implement adaptive control strategies to automatically adjust cutting parameters in real-time for enhanced precision.
- Metrology and Inspection: Employ high-precision metrology tools, such as coordinate measuring machines (CMMs) and non-contact measurement systems, to verify dimensional accuracy and ensure adherence to specified tolerances.
V. Innovative Approaches to Machining Optimization
A. Advancements in Machining Technology
- High-Speed Machining (HSM): HSM techniques involve using higher cutting speeds and feeds to remove material more rapidly while maintaining accuracy. This approach reduces cycle times and improves overall productivity.
- Additive Manufacturing Integration: Combining traditional machining with additive manufacturing techniques allows for the creation of complex geometries and the repair or modificationof existing components. This integration expands the possibilities for customization and optimization in machining processes.
- Hybrid Machining Systems: Hybrid machining systems merge multiple machining technologies, such as milling, grinding, and laser machining, into a single platform. These systems offer versatility and flexibility, enabling manufacturers to optimize processes for different applications without the need for separate machines.
B. The Role of Artificial Intelligence in Machining
Artificial Intelligence (AI) has emerged as a transformative technology in machining optimization. AI-powered systems can analyze vast amounts of machining data, including sensor readings, cutting parameters, and historical performance, to identify patterns and optimize machining processes. Some key applications of AI in machining optimization include:
- Predictive Maintenance: AI algorithms can predict machine failures or tool wear based on real-time data analysis, enabling proactive maintenance and minimizing unplanned downtime.
- Adaptive Control: AI algorithms can dynamically adjust cutting parameters, tool paths, and feed rates based on real-time feedback, optimizing machining processes for improved precision and efficiency.
- Quality Control and Inspection: AI-powered vision systems can detect surface defects, dimensional variations, and other quality issues during machining, ensuring higher product quality and reducing scrap rates.
- Intelligent Tool Selection: AI algorithms can recommend the most suitable cutting tools and parameters based on material properties, machining requirements, and historical data, enhancing efficiency and reducing errors.
VI. Conclusion
A. Recap of Key Points
In this guide, we explored the world of machining equipment processes and the significance of optimization in achieving efficiency and precision. We discussed the types of machining equipment, basic principles of machining, key stages in the machining process, common challenges, and strategies for overcoming them. Additionally, we delved into techniques for improving efficiency and methods for enhancing precision in machining equipment processes.
B. Final Thoughts on the Future of Machining Optimization
The future of machining optimization looks promising, with advancements in technology and the integration of AI-driven solutions. Manufacturers can expect further improvements in efficiency, precision, and productivity. The continued development of high-speed machining, additive manufacturing integration, and hybrid machining systems will expand the possibilities for optimization. Moreover, the utilization of AI algorithms and data-driven insights will enable manufacturers to unlock new levels of efficiency and precision in machining processes, paving the way for innovation and competitiveness in various industries. By embracing these advancements and staying informed about emerging trends, manufacturers can position themselves at the forefront of machining optimization and drive their success in the dynamic landscape of modern manufacturing.