Table of Contents:
- Introduction
- Materials Used in Prototype Sheet Metal Stamping
- Prototype Sheet Metal Stamping Process
- Advantages of Prototype Sheet Metal Stamping
- Limitations of Prototype Sheet Metal Stamping
- Applications of Prototype Sheet Metal Stamping
- Conclusion
-
1.Introduction
Prototype sheet metal stamping is a critical component of the product development process. It involves the creation of small quantities of stamped sheet metal parts, which can be used for prototyping, testing, and validation purposes. Prototype sheet metal stamping is an essential step in product design because it helps designers identify and correct any issues with the product’s design before it goes into full production. This article provides an overview of prototype sheet metal stamping, including the materials used, the process involved, the advantages and limitations, and the applications.
-
2.Materials Used in Prototype Sheet Metal Stamping
Sheet metal stamping is a process that involves the shaping and forming of sheet metal into desired shapes using a press machine and a series of dies. The quality and properties of the final stamped part depend on the properties of the sheet metal material used. In this section, we will discuss the different types of sheet metal materials used in prototype sheet metal stamping, their characteristics and properties, and the selection criteria used to determine the most appropriate material for a given application.
Types of Sheet Metal Materials
There are several types of sheet metal materials used in prototype sheet metal stamping, including:
- Aluminum: This is a lightweight material that is easy to form and work with. It has good corrosion resistance and is commonly used in the aerospace and automotive industries.
- Steel: This is a strong and durable material that is used in a wide range of applications, including automotive, construction, and appliances. There are several types of steel used in sheet metal stamping, including carbon steel, stainless steel, and galvanized steel.
- Copper: This is a soft and ductile material that is commonly used in electrical and plumbing applications.
- Brass: This is a corrosion-resistant material that is commonly used in decorative applications.
- Titanium: This is a lightweight and strong material that is commonly used in the aerospace and medical industries.
Characteristics and Properties of Sheet Metal Materials
The properties of sheet metal materials can vary depending on the type of material and the manufacturing process used. However, there are some general characteristics and properties that are common to most sheet metal materials:
- Ductility: Sheet metal materials must be ductile to allow for easy deformation and shaping during the stamping process.
- Strength: Sheet metal materials must be strong enough to withstand the stresses and strains of the stamping process and the intended application.
- Thickness: The thickness of the sheet metal material can vary depending on the application and the required strength of the final stamped part.
- Corrosion resistance: Some sheet metal materials, such as aluminum and stainless steel, have good corrosion resistance and are commonly used in outdoor or corrosive environments.
Selection Criteria for Sheet Metal Materials
The selection of the appropriate sheet metal material for a given application depends on several factors, including:
- Application requirements: The intended use of the stamped part will determine the required strength, thickness, and other properties of the sheet metal material.
- Cost: The cost of the sheet metal material can vary depending on the type of material, thickness, and quantity required.
- Manufacturing process: The stamping process used will determine the required ductility and other properties of the sheet metal material.
- Environment: The environmental conditions in which the stamped part will be used will determine the required corrosion resistance of the sheet metal material.
In conclusion, the selection of the appropriate sheet metal material is critical to the success of the prototype sheet metal stamping process. The properties and characteristics of the selected material will determine the quality and durability of the final stamped part, as well as its suitability for the intended application.
-
3.Prototype Sheet Metal Stamping Process
The prototype sheet metal stamping process involves several stages, from design to finishing, to create a stamped part with the desired shape, size, and quality. In this section, we will discuss the stages of the prototype sheet metal stamping process, the equipment and tools used, and the factors that can affect the stamping process.
Stages of Prototype Sheet Metal Stamping
- Design: The first stage of the process is the design stage, where the part is designed using computer-aided design (CAD) software. The design must take into account the intended application and the properties and characteristics of the selected sheet metal material.
- Tool design and fabrication: Once the part design is complete, the tooling design and fabrication stage begins. The tooling is the set of dies used to shape the sheet metal material into the desired shape. The tooling must be designed to ensure the correct shape, size, and accuracy of the final stamped part.
- Part fabrication: In this stage, the sheet metal material is fed into the stamping press and shaped using the tooling dies. The stamping process involves a series of operations, including bending, punching, and cutting, to achieve the desired shape and size of the final stamped part.
- Finishing: Once the part has been stamped, it may require additional finishing operations, such as deburring, cleaning, and painting, to improve its appearance and performance.
- Quality inspection and testing: The final stage of the process involves quality inspection and testing to ensure that the stamped part meets the required specifications and standards.
Equipment and Tools Used in Prototype Sheet Metal Stamping
The equipment and tools used in prototype sheet metal stamping include:
- Stamping press: This is the main equipment used in the stamping process. The press applies force to the sheet metal material using the tooling dies to shape the material into the desired form.
- Tooling dies: These are the dies used to shape the sheet metal material into the desired shape. The tooling must be designed and fabricated to ensure the correct shape, size, and accuracy of the final stamped part.
- Material handling equipment: This includes equipment such as cranes and forklifts used to move and transport the sheet metal material and stamped parts.
- Finishing equipment: This includes equipment such as deburring machines, sanders, and paint booths used to finish the stamped parts.
Factors Affecting the Prototype Sheet Metal Stamping Process
Several factors can affect the prototype sheet metal stamping process, including:
- Sheet metal material properties: The properties and characteristics of the selected sheet metal material can affect the stamping process, including its ductility, strength, and thickness.
- Tooling design and fabrication: The design and fabrication of the tooling must be precise and accurate to ensure the correct shape, size, and accuracy of the final stamped part.
- Stamping press settings: The press settings, such as the applied force, speed, and stroke length, can affect the stamping process and the quality of the final stamped part.
- Environmental conditions: The environmental conditions, such as temperature and humidity, can affect the sheet metal material properties and the stamping process.
In conclusion, the prototype sheet metal stamping process involves several stages, from design to finishing, to create a stamped part with the desired shape, size, and quality. The process requires the use of specialized equipment and tools, and several factors can affect the stamping process, including the sheet metal material properties, tooling design and fabrication, stamping press settings, and environmental conditions.
-
4.Advantages of Prototype Sheet Metal Stamping
Prototype sheet metal stamping offers several advantages in product development, including cost savings, improved design and functionality, and faster time to market. In this section, we will discuss each of these advantages in detail.
- Cost savings: Prototype sheet metal stamping can help reduce the overall cost of product development. By creating a prototype of the part before mass production, design flaws can be identified and corrected early on, preventing costly mistakes and delays in production. Additionally, sheet metal stamping allows for the creation of complex parts with high precision and accuracy, reducing the need for additional machining or assembly operations, which can add to the overall cost of production.
- Improved design and functionality: Sheet metal stamping offers a high level of design flexibility, allowing for the creation of complex shapes and geometries that may not be possible with other manufacturing processes. This can lead to improved functionality and performance of the final product. Additionally, by creating a prototype of the part, designers and engineers can test and evaluate the part’s performance and make necessary adjustments before mass production.
- Faster time to market: Prototype sheet metal stamping allows for the creation of functional parts quickly, reducing the time needed for design iterations and testing. This can accelerate the product development process and get the final product to market faster, giving companies a competitive edge.
Overall, prototype sheet metal stamping offers several advantages in product development, including cost savings, improved design and functionality, and faster time to market. By creating a prototype of the part before mass production, design flaws can be identified and corrected early on, leading to a better final product and a more efficient production process.
Click on the V1 Prototype website to gain more information.
-
5.Limitations of Prototype Sheet Metal Stamping
While prototype sheet metal stamping has several advantages, there are also some limitations to consider. In this section, we will discuss some of the main limitations of this process.
- Material and design constraints: The materials used in sheet metal stamping are often limited to those with high formability, such as aluminum and steel. Additionally, the stamping process can put limitations on the design of the part, as certain shapes and geometries may be difficult or impossible to achieve. Designers and engineers must carefully consider these constraints when developing parts.
- Tooling and setup costs: The tooling and setup costs associated with prototype sheet metal stamping can be significant. This is because each stamping tool must be custom-designed and manufactured for each specific part. These costs can add up quickly, especially for smaller production runs.
- Limitations on batch sizes: Prototype sheet metal stamping is typically more cost-effective for smaller production runs, but as batch sizes increase, the costs associated with tooling and setup become less significant. Therefore, larger production runs may be more cost-effective with other manufacturing processes.
It’s essential to keep these limitations in mind when deciding whether to use prototype sheet metal stamping in product development. While it may be an excellent option for smaller production runs and complex parts, other manufacturing processes may be more suitable for larger runs or parts with specific material or design requirements.
-
6.Applications of Prototype Sheet Metal Stamping
Prototype sheet metal stamping has a wide range of applications across various industries. In this section, we will discuss some of the main industries that use this process.
- Automotive industry: Prototype sheet metal stamping is widely used in the automotive industry for creating a wide range of parts, including body panels, brackets, and brackets. By using sheet metal stamping, manufacturers can produce complex parts with high precision and accuracy, resulting in a better final product. Additionally, the speed of the process makes it ideal for the automotive industry, where time-to-market is essential.
- Aerospace industry: The aerospace industry also uses prototype sheet metal stamping to create various parts, including brackets, panels, and enclosures. The high precision and accuracy of the process are critical for ensuring the safety and reliability of aerospace components. Additionally, the lightweight and durable nature of sheet metal make it an ideal choice for many aerospace applications.
- Medical equipment industry: Prototype sheet metal stamping is also used in the medical equipment industry for creating parts such as surgical instruments and implantable devices. The high precision and accuracy of the process are essential for ensuring the safety and efficacy of these medical devices. Additionally, sheet metal is biocompatible and can be sterilized, making it a suitable material for medical applications.
These are just a few examples of the many industries that use prototype sheet metal stamping in their manufacturing processes. As technology advances, we can expect to see this process become even more prevalent in industries around the world.
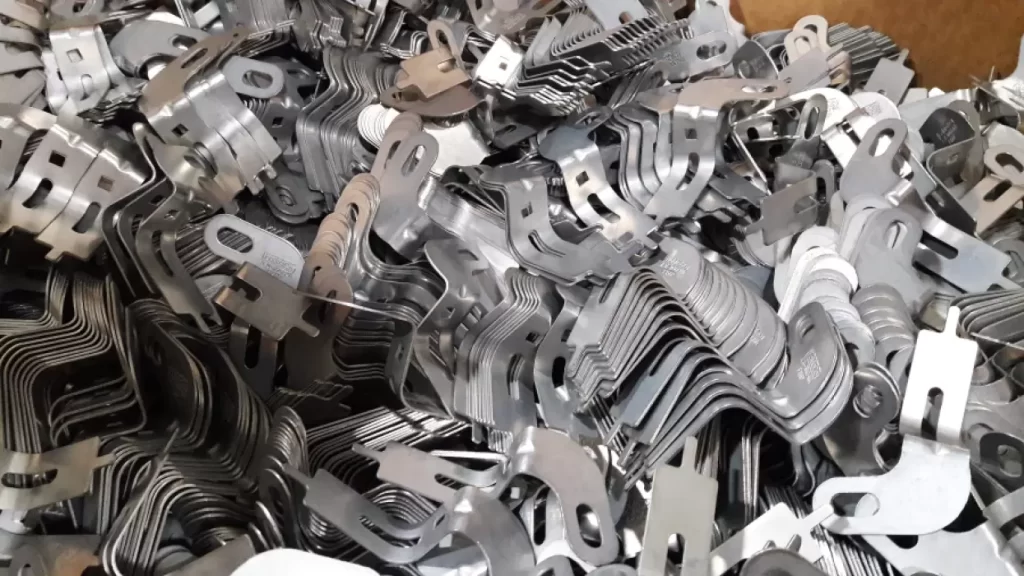
-
7.Conclusion
Prototype sheet metal stamping is a critical component of the product development process. It enables designers to test and validate product designs quickly and cost-effectively, identify and correct any issues early in the development process, and reduce the time to market for new products. While prototype sheet metal stamping has many benefits, it also has some limitations, including material and design constraints, tooling and setup costs, and limitations on batch sizes. Despite these limitations, prototype sheet metal stamping has a wide range of applications across many industries, including the automotive, aerospace, and medical equipment industries.
As technology continues to evolve, it is likely that prototype sheet metal stamping will become even more critical in the product development process. Advances in computer-aided design (CAD) and computer-aided manufacturing (CAM) have already made the design and fabrication of tooling more efficient and accurate. Additionally, the use of simulation and modeling software can help designers identify and correct potential issues before the stamping process begins. These advancements will help to further reduce costs and improve the speed and accuracy of the prototype sheet metal stamping process.
In conclusion, prototype sheet metal stamping is a valuable tool for product designers and manufacturers. By enabling quick and cost-effective prototyping and testing, prototype sheet metal stamping helps to improve the quality and functionality of products and reduce time to market. As technology continues to evolve, it is likely that prototype sheet metal stamping will become even more critical in the product development process, enabling even greater efficiency and accuracy in the creation of new products.