The microstructure morphology and distribution characteristics of defect bands in die casting magnesium alloy were studied, and the corresponding relationships between defect bands and pressure chamber precrystallization (ESCs), air shrinkage hole and die casting process parameters were established. On this basis, the formation and evolution mechanism of defect bands were discussed. The results show that the cross section solidification microstructure of die cast magnesium alloy can be divided into three regions with obvious differences in microstructure characteristics. With the increase of the low speed, the ESCs content in the solidification microstructure of die casting magnesium alloy gradually decreases, and the defect band structure becomes more obvious and close to the center of die casting.
The width of defect band decreases, and the internal holes are more concentrated. The higher the high speed is, the more dispersed ESCs are in the solidification structure of die casting magnesium alloy, and the defect band is closer to the center of die casting. Under the condition of no high speed, the double defect band appears in the solidification structure cross section of die casting magnesium alloy. Die casting of metal flow in the process of filling determines the distribution of the defect with the position and development trend of liquid metal at high speed of scour and the pressurization pressure, close to the metal flow profile of grain crushing or rotation, the grain is greater than the remaining liquid metal is formed between product clearance, as the solidification of the defects of gathered along the flow profile holes with organization.
1.Microstructure characteristics of defect bands in die cast magnesium alloys
The defect band is a special microstructure characteristic of cold chamber die casting, which is different from the solidification microstructure obtained by other casting processes, and its morphology and distribution are more complex. Figure 1 shows the defect bands with different morphology and distribution characteristics in the cross section of magnesium alloy die castings. The defect bands usually exist in various forms, some are distributed along the cross section profile of die castings, and some are irregular. There are single defect bands, double defect bands and multiple defect bands. Previous studies have shown that the defect band is a banded structure with holes and there is a certain solute segregation. OTARAWANNA S et al. found that the width of the defect band is 7-18 times of the grain size by using electron backscattering diffraction technology. LI X B et al. found that the solute enrichment degree in the defect band on the surface of die casting is small through composition scanning. However, a large number of solute elements were enriched in the defect zone of the heart.
Different tissue observation methods were used to analyze the microstructure of the cross section of magnesium alloy die casting, as shown in Figure 2. It can be seen that the microstructure of die cast magnesium alloy can be divided into three parts from the macro perspective. The first part is the microstructure from the surface of die cast to the outer surface of defect band, which is characterized by less holes, and most ESCs are broken dendrites without aggregation, so the microstructure is relatively dense.
The second part is the defect zone at a certain distance from the surface of the die casting, in which a large number of irregular pores are enriched. Compared with the surrounding ESCs, the structure of ESCs is smaller. It can be seen from the electron microscope pictures that the pores in the defect zone are mainly distributed at the grain boundary (ESCs or α-Mg). The third part is the heart tissue surrounded by defect zone. There are more large ESCs tissues, and a large number of ESCs are clustered in the heart. There are a large number of loose tissues at the grain boundary where ESCs are clustered, so there are many pores, but the distribution is relatively random.
2.Influence of die casting parameters on microstructure of defect zone
The die casting test was carried out on the TOYO-BD-350V5 die casting machine. Table 1 shows the test parameters used in the process of die casting. The effects of different low speed, high speed, pressurization pressure and casting delay on the microstructure morphology and distribution characteristics of die casting magnesium alloy defect band were comparatively studied.
The low velocity in the die casting process parameters mainly affects the flow morphology of liquid metal in the press chamber and the morphology and content of ESCs in the final die casting, and its influence on the defect zone is shown in Figure 3. Under the condition of low speed (0.05 m/s), the whole section of die casting contains a large number of randomly distributed holes, but no obvious defect zone can be found.
As can be seen from FIG. 3, the ESCs content is large, in the form of thick dendrites, and most of them are clustered together and spread throughout the entire section of the die casting. Therefore, there is more shrinkage porosity among the ESCs dendrites in the entire die casting. With the increase of the low speed, the ESCs content gradually decreases, and the morphology tends to be long strip or spherical. At this time, the defect band structure becomes more obvious, and it is close to the center of the die casting, the width of the defect band decreases, and the internal holes are gradually dense.
Of different supercharging pressure die casting magnesium alloy microstructure was studied, found that as supercharging pressure, die casting of ESCs content gradually reduce, its morphology tend to be spherical, distribution pattern by partial poly scattered tend to die casting center, and in the die casting defects with the location, width and the morphology of internal holes did not change obviously. Die casting process parameters of casting delay effect on the defect with similar to slow speed, pouring time delay increase or reduce the low speed, the ESCs content in die casting were increase ESCs exhibits more bulky dendrite shape, at the grain boundary ESCs gathered there are a number of loose, with the defects tend to die casting surface, and the width increases.
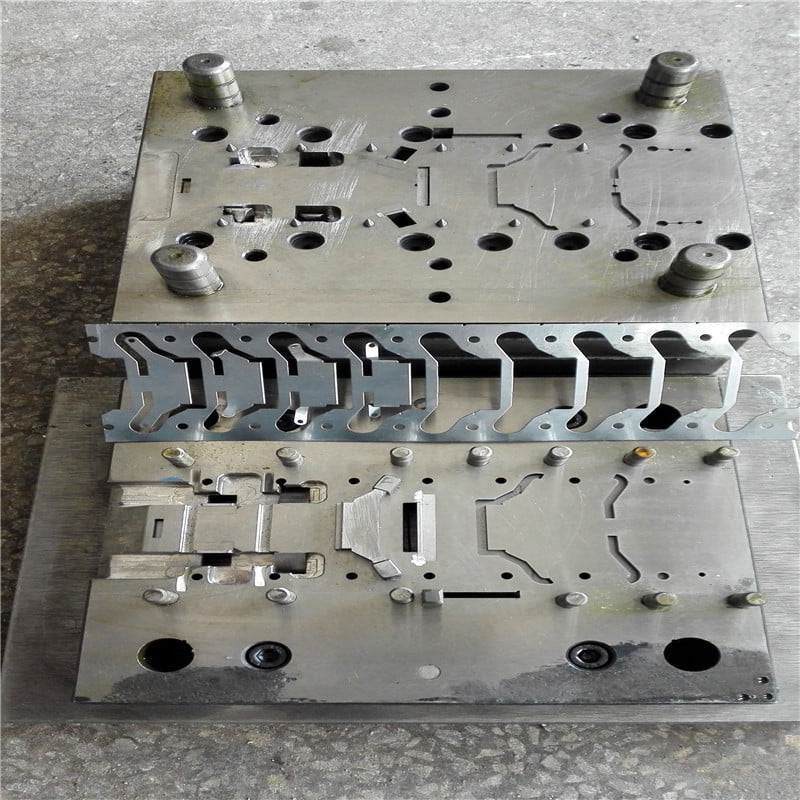
3.Formation mechanism of defect bands
The defect band is a special microstructure characteristic in cold chamber die casting, and its morphology and distribution are complex. The defect band is usually a ribbon structure with shrinkage cavity and shrinkage porosity, and the thickness is wide. The location of the defect band is often related to the distribution of the precrystallized structure of the thick pressure chamber, which directly causes great harm to the mechanical properties of the die casting. Therefore, it is of great significance to understand the formation mechanism of defect bands in die cast magnesium alloys to control and improve the microstructure of die cast magnesium alloys and improve the mechanical properties of die cast magnesium alloys.
Based on the precrystallization theory of pressure chamber, DAHLE A K et al. tried to describe the formation mechanism of defect bands in die casting, as shown in Figure 5. It is considered that the grains grown in prenucleation in the pressure chamber are biased toward the center of the die casting cavity under the action of fluid as the cavity is filled with melt at high speed. Around these nascent grains, the liquid metal in the center of the cavity begins to solidify, and the solidification interface moves from inside to outside. At the same time, the liquid metal, which has not solidified in the pressure chamber and filling process, begins to solidify and form the surface cold layer immediately after contacting the type wall.
Due to the heat transfer of the wall and the cooling layer, the solidification process in the die casting cavity is formed from the outside to the inside. When the two solidification fronts meet, that is, the final solidification position of the die casting, due to the difficulty of feeding, serious loose structure often appears in the solidification structure. This is applicable to explain the single defect band along the section profile of die casting, but it cannot explain the occurrence of double defect band and other irregular defect bands. CAO H et al. [21] studied the double defect bands in the die casting and concluded that the formation of the defect bands near the heart of the die casting was related to the precrystallization of the pressure chamber, while the formation of the defect bands near the surface was not related to the distribution of the precrystallization structure of the pressure chamber.
4.conclusion
(1) The cross section solidification microstructure of die casting magnesium alloy can be divided into three regions with obvious differences in microstructure characteristics by taking the defect zone as the boundary. A large number of irregular pores are gathered in the defect zone, and the ESCs structure is smaller than the surrounding ESCs, and the pores are mainly distributed at the grain boundary (ESCs or α-Mg).
(2) Increase the low speed or shorten the casting time, the ESCs content in the solidification structure of die casting magnesium alloy gradually decreases, the defect band structure becomes more obvious and close to the center of die casting, the width of defect band decreases, and the internal holes become more clustered. The higher the high speed is, the more dispersed ESCs are in the solidification structure of die casting magnesium alloy, and the defect band is closer to the center of die casting. In the case of no high speed, the double defect band appears in the solidification structure section of die casting magnesium alloy.
(3) defect with the formation and distribution of the liquid metal flow in the process of die casting mould filling, the influence of liquid metal at high speed of severe erosion and boost pressure, under the action of outside near the metal flow profile of grain crushing or rotation, the grain size is greater than the remaining liquid metal is formed between product clearance, as the solidification of the defects of gathered along the flow profile holes with organization.
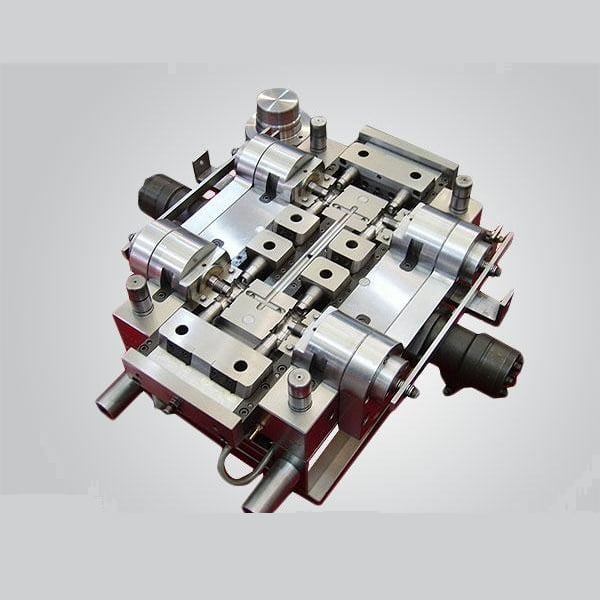