This serves as an essential primer for both novice and seasoned professionals looking to enhance their understanding of injection mold design. It provides a detailed exploration of the fundamental concepts, principles, and best practices that underpin successful injection mold design. Through expert insights, illustrative examples, and practical tips, readers will acquire the basic knowledge necessary to create efficient, high-quality injection mold designs that meet the demands of modern manufacturing.
I. Introduction
A. The Importance of Injection Mold Design in Manufacturing
Injection mold design plays a pivotal role in the manufacturing process, particularly in industries that rely on plastic components. It is the foundation upon which successful production runs are built. Injection molding offers numerous advantages, including cost-effectiveness, high production rates, and the ability to create intricate and complex geometries. However, to harness these benefits, it is crucial to master the basics of injection mold design. A well-designed mold ensures efficient and consistent production, minimizes defects, reduces cycle times, and ultimately leads to high-quality end products.
B. Objectives of the Article
The objective of this comprehensive guide is to provide readers with a solid understanding of the basic principles of injection mold design. We will explore the key components of an injection mold, discuss the role of materials in mold design, delve into important design considerations, and introduce advanced techniques that can enhance the efficiency and effectiveness of mold design. Additionally, we will address common issues that arise during mold design and provide troubleshooting strategies. By the end of this article, readers will be equipped with the knowledge and insights necessary to embark on successful injection mold design projects.
II. Basic Principles of Injection Mold Design
A. Overview of Injection Molding Process
Injection molding is a widely used manufacturing process for producing plastic parts. It involves injecting molten plastic material into a mold cavity under high pressure. Once the material cools and solidifies, the mold is opened, and the finished part is ejected. The process offers exceptional versatility in terms of design possibilities, material choices, and production volumes. Successful injection mold design requires a thorough understanding of the injection molding process, including the flow behavior of molten plastic, cooling dynamics, and the interaction between the mold and the material.
B. Key Components of an Injection Mold
An injection mold consists of several essential components that work together to shape the final product. These components include:
- Mold Base: The mold base provides the foundation and support for all other mold components. It typically includes the mold cavity, core, and various inserts.
- Cavity and Core: The cavity and core form the voids into which the molten plastic is injected. They define the shape and dimensions of the final product and are often made of hardened steel for durability.
- Sprue and Runners: The sprue is the channel through which molten plastic enters the mold. The runners distribute the plastic from the sprue to the individual cavities. Proper design of the sprue and runners is crucial to ensure balanced filling and prevent flow imbalances or material wastage.
- Cooling System: The cooling system consists of channels and inserts that facilitate the rapid and uniform cooling of the molded part. Efficient cooling is essential to avoid warpage, achieve dimensional accuracy, and reduce cycle times.
- Ejection System: The ejection system aids in the removal of the finished part from the mold. It typically includes ejector pins, sleeves, and lifters that push or pull the part out of the mold cavity.
III. Materials and Their Role in Mold Design
Mold materials are an important aspect of injection molding, as they affect the quality and efficiency of the final product. we will discuss how to select the appropriate mold material for your project and how it impacts the mold performance.
There are several criteria to consider when choosing a mold material, such as:
- Thermal conductivity: This is the ability of the material to transfer heat. A high thermal conductivity means that the mold can cool down faster, resulting in shorter cycle times and better dimensional accuracy of the molded parts.
- Hardness and wear resistance: This is the ability of the material to resist deformation and abrasion from the molten plastic. A high hardness and wear resistance means that the mold can withstand repeated molding cycles without losing its shape or surface quality.
- Corrosion resistance: This is the ability of the material to resist chemical attack from the plastic, additives, or processing conditions. A high corrosion resistance means that the mold can maintain its integrity and functionality over time.
- Cost: This is the amount of money required to purchase and maintain the mold material. A low cost means that the mold can be produced and operated with minimal expenses.
Different mold materials have different properties that suit different molding applications. Some of the most common mold materials are:
- Tool steels: These are alloy steels that have been specially treated to enhance their hardness and wear resistance. They are ideal for high-volume production, as they can endure high temperatures and pressures. Examples of tool steels are P20, H13, and S7.
- Stainless steels: These are steels that contain chromium and other elements that increase their corrosion resistance. They are ideal for molding plastics that are corrosive or require sterilization. Examples of stainless steels are 420 and 440C.
- Aluminum alloys: These are metals that contain aluminum and other elements that improve their thermal conductivity and machinability. They are ideal for molding plastics that require fast cooling and low clamping force. Examples of aluminum alloys are 6061 and 7075.
The choice of mold material can have a significant impact on the mold performance, such as:
- Cycle time: This is the time required to complete one molding cycle, from closing the mold to ejecting the part. A shorter cycle time means higher productivity and lower energy consumption. Mold materials with high thermal conductivity, such as aluminum alloys, can reduce the cycle time by facilitating faster cooling.
- Dimensional stability: This is the ability of the molded part to retain its shape and size after cooling. A higher dimensional stability means lower shrinkage and warpage. Mold materials with high thermal conductivity and low coefficient of thermal expansion, such as tool steels, can improve the dimensional stability by minimizing thermal stresses.
- Surface finish: This is the appearance and texture of the molded part's surface. A better surface finish means higher aesthetic appeal and functionality. Mold materials with high hardness and wear resistance, such as tool steels and stainless steels, can enhance the surface finish by preventing scratches and marks.
Choosing the right mold material for your injection molding project is crucial for achieving optimal results. You should consider the properties of the mold material in relation to the characteristics of the plastic, the design of the part, and the requirements of the process. By doing so, you can ensure that your mold performs well and lasts long.
IV. Design Considerations for Injection Molds
A. Tolerances and Dimensional Accuracy
Achieving tight tolerances and dimensional accuracy is a crucial aspect of injection mold design. Factors that influence dimensional accuracy include:
- Shrinkage: Plastic materials undergo a certain degree of shrinkage as they cool and solidify. Understanding and accounting for this shrinkage in the mold design is essential to achieve the desired dimensions in the final product.
- Mold Precision: The precision of the mold components, suchas the cavity and core, directly impacts dimensional accuracy. High-quality machining and precise assembly are necessary to ensure tight tolerances.
- Cooling System Design: Proper cooling system design helps control the temperature distribution within the mold, minimizing dimensional variations due to uneven cooling. Strategic placement of cooling channels and inserts can optimize cooling efficiency.
B. Cooling System Design
The cooling system in an injection mold plays a critical role in the overall molding process. Key considerations for cooling system design include:
- Channel Layout: Channels should be strategically positioned to ensure uniform cooling across the mold surface. They should be placed close to areas that require efficient cooling and away from thick sections that tend to cool slower.
- Cooling Channel Diameter and Design: The diameter and design of the cooling channels impact heat transfer rates. Optimal channel diameter and design maximize cooling efficiency and reduce cycle times.
- Cooling Medium: The choice of cooling medium, such as water or oil, depends on factors such as cooling requirements, temperature control, and the specific characteristics of the molding process. Proper selection and circulation of the cooling medium are crucial for maintaining consistent mold temperatures.
C. Ejection and Venting Systems
Effective ejection and venting systems are vital for smooth mold operation and high-quality part production.
- Ejection System: The ejection system must be designed to minimize part distortion or damage during ejection. Properly positioned ejector pins, sleeves, or lifters should be incorporated to ensure controlled and uniform ejection of the parts.
- Venting System: Venting is essential to allow trapped air or gases to escape during the injection process. Insufficient venting can lead to defects such as burns, voids, or short shots. Well-designed venting systems prevent such issues and promote high-quality part production.
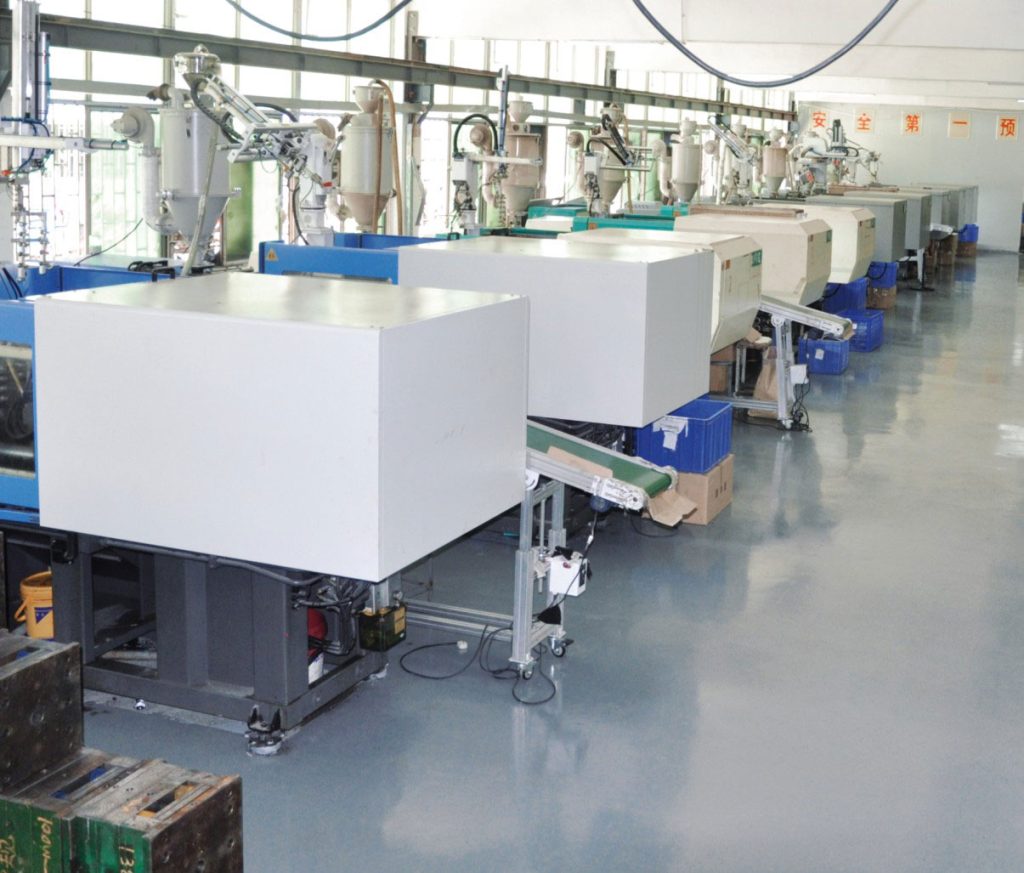
V. Advanced Techniques in Mold Design
A. Use of CAD/CAM Software
Computer-Aided Design (CAD) and Computer-Aided Manufacturing (CAM) software have revolutionized injection mold design. These tools enable designers to create detailed 3D models, simulate the molding process, optimize designs, and generate accurate tool paths for machining. CAD/CAM software streamlines the design and manufacturing workflow, reduces design iterations, and allows for efficient collaboration between designers and manufacturers.
B. Rapid Prototyping and Its Applications
Rapid prototyping technologies, such as 3D printing, have become invaluable in the field of mold design. Prototyping allows designers to quickly validate their designs, verify fit and function, and identify potential issues before committing to expensive tooling. By leveraging rapid prototyping, designers can reduce development time, improve design accuracy, and make informed decisions based on physical prototypes.
VI. Troubleshooting Common Issues in Mold Design
A. Warpage and Sink Marks
Warpage and sink marks are common challenges faced in injection mold design. Warpage refers to the distortion or deformation of the molded part after ejection, while sink marks are depressions or indentations on the surface of the part. Several factors can contribute to these issues, including:
- Inadequate Cooling: Insufficient cooling can result in uneven cooling rates, leading to differential shrinkage and subsequent warpage or sink marks. Optimizing the cooling system design and ensuring proper cooling channel placement can help mitigate these issues.
- Poor Gate Placement: Improper gate placement can cause uneven material flow and differential cooling, resulting in warpage or sink marks. Selecting appropriate gate locations based on part geometry and flow analysis can minimize these defects.
- Material Selection: Some plastics are more prone to warpage or sink marks due to their inherent properties. Understanding the material's behavior and selecting suitable materials with lower shrinkage or better flow characteristics can help mitigate these issues.
B. Short Shots and Flashes
Short shots occur when the injected plastic material does not completely fill the mold cavity, resulting in incomplete parts. Flashes, on the other hand, are excess material that escapes between mold parting surfaces, leading to thin protrusions along the parting line. Several factors can contribute to these issues, including:
- Insufficient Injection Pressure or Time: Inadequate injection pressure or short injection times can prevent the proper filling of the mold cavity, resulting in short shots. Optimizing the injection parameters and ensuring sufficient pressure and time are crucial for complete part filling.
- Poor Mold Venting: Inadequate venting can trap air or gases, preventing complete filling of the cavity and resulting in short shots or flashes. Proper venting design and placement can mitigate these issues by allowing trapped air or gases to escape.
- Mold Misalignment or Wear: Improper mold alignment or excessive wear can lead to flash formation. Regular maintenance and inspection of the mold, including proper alignment and replacement of worn components, are essential to prevent flash defects.
VII. Conclusion
A. Recap of Key Points
In this comprehensive guide to injection mold design, we have explored the fundamental principles, design considerations, and advanced techniques necessary for mastering the basics of mold design. We discussed the importance of mold design in manufacturing, the key components of an injection mold, the role of materials in mold design, and the impact of material choice on mold performance. We also examined design considerations such as tolerances and dimensional accuracy, cooling system design, and ejection and venting systems. Additionally, we explored advanced techniques including the use of CAD/CAM software and the applications of rapid prototyping in mold design.
We also addressed common issues that arise during mold design, including warpage, sink marks, short shots, and flashes. These issues can be mitigated through proper cooling system design, gate placement, material selection, injection parameters optimization, mold venting, and regular maintenance.
B. Encouragement for Continued Learning and Experimentation in Mold Design
Injection mold design is a complex and dynamic field that requires continuous learning and experimentation. As technology advances and new materials and techniques emerge, mold designers must stay updated to remain at the forefront of the industry. It is essential to engage in ongoing professional development, attend industry conferences, and participate in collaborative forums to exchange knowledge and experiences with fellow mold designers.
Furthermore, experimentation is crucial for pushing the boundaries of mold design and discovering innovative solutions. By exploring new materials, optimizing design parameters, and embracing emerging technologies, mold designers can unlock new possibilities and achieve exceptional results.
In conclusion, mastering the basics of injection mold design is a fundamental step towards becoming an expert in the field. By understanding the principles, considering material choices, implementing proper design considerations, utilizing advanced techniques, and troubleshooting common issues, mold designers can create molds that deliver efficient and high-quality production. The journey to becoming an authority in mold design requires continuous learning, experience, and a commitment to excellence. So, embrace the challenges, expand your knowledge, and keep pushing the boundaries of injection mold design.