Industrial-Grade Injection Molding Machines - Expert Precision and Reliability
Elevate Your Plastic Manufacturing Capabilities With Our Specialized Plastic Injection Molding Machines. Designed For Unparalleled Precision, Speed, And Efficiency, Our Machines Set The Industry Standard For Professional-Grade Performance. An Injection Molding Machine That Can Drink Water, Without Plastic Drying.
V1 Injection Molding Machines Advantage
Traditional injection molding machines require different drying times before raw materials are put into production. The exhaust type injection molding machine eliminates the need for a separate device outside the injection molding machine to perform a separate drying operation, integrates the input of raw materials into the output of the product, and reduces the number of production operations, making the production of plastic products more efficient and convenient.
At the same time, the vented injection molding machine eliminates the need for separate drying outside the machine, eliminating the potential safety hazards associated with the original drying process, and eliminating the potential risk of fire due to improper operation in the drying process. Safety is further guaranteed. At the same time, the volatile gas generated during the melting process of the raw material is discharged. In addition, the exhaust injection molding machine also further implements the new development requirements of energy saving and high efficiency.
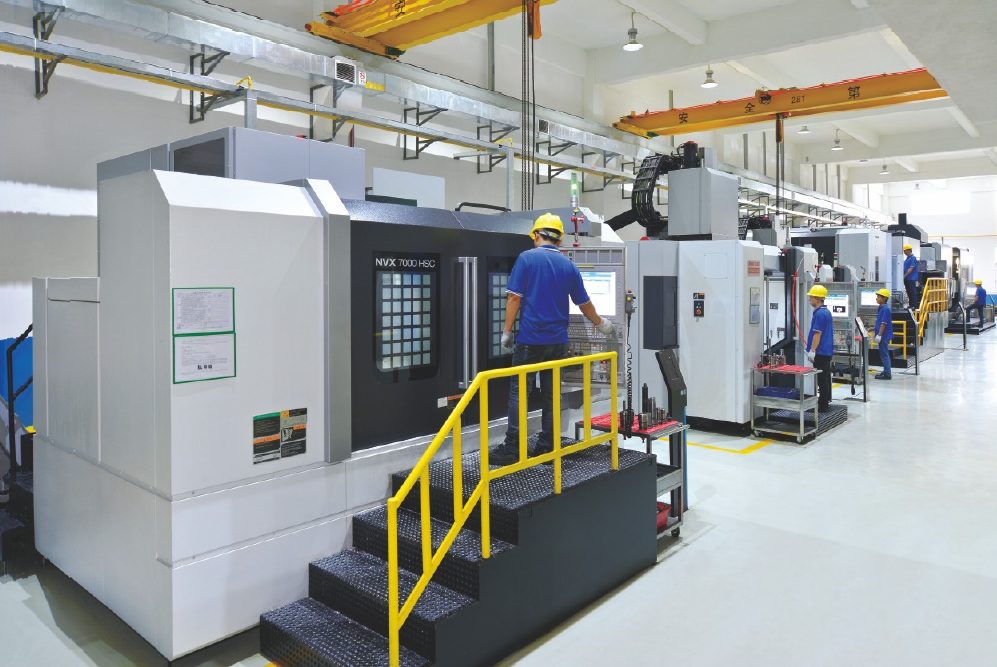
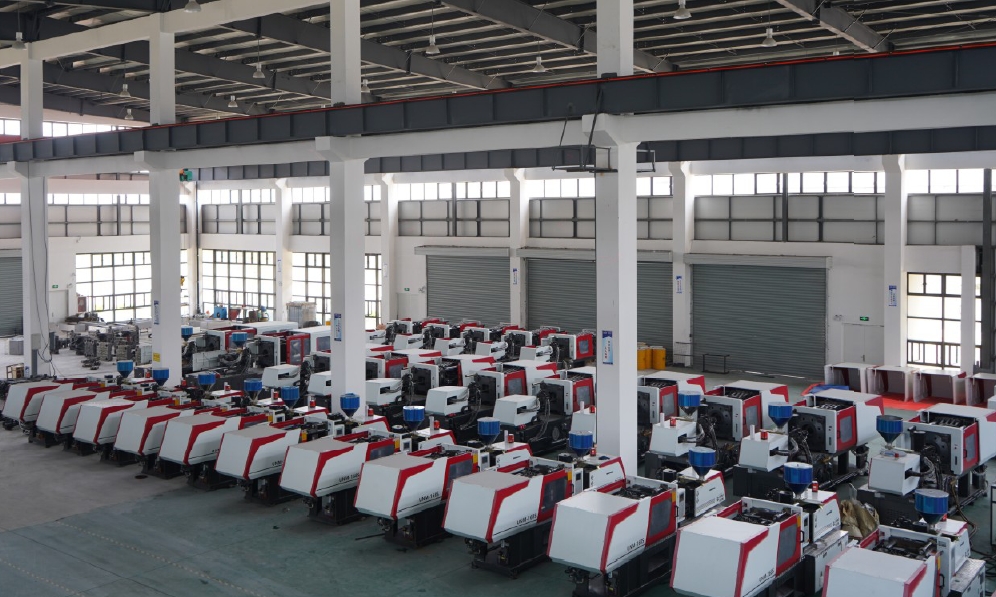
Machining Center Manufacturing Workshop
V1 company has introduced international advanced production equipment and has built advanced automated production lines, etc., to ensure that the products produced have good stability, fast production efficiency and high precision, and improve the manufacture of first-class products by optimizing the process, in order to create a first-class enterprise and establish an industry brand Foundation.
Qualification Certificate: ISO9001:2015; ISO14001:2015; IATF16949:2016.
Exhaust Injection Molding Machine Process Flow Chart
- Add Moisture To Plastic
- Exhaust Screw High Temperature Extrusion Stirring
- Exhaust Device Releases Water Vapor
- Moisture Separation In Plastics
- Moisture-Free Plastic Flows Out Of The Nozzle
- Injection Mold
Injection Moulding Machine Application Product
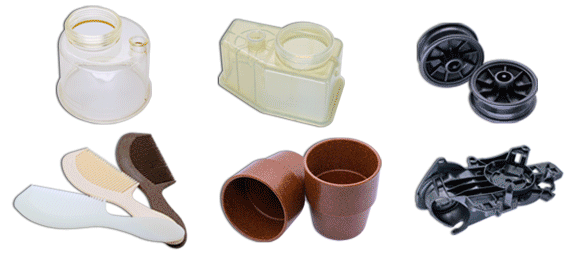
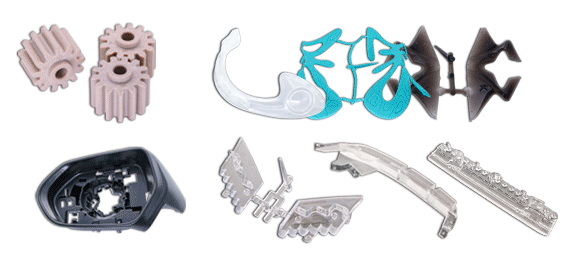
Disadvantage Of Traditional Hydraulic Injection Molding Machine
The drying process requires a lot of power consumption, which is inconsistent with my country's national policy of energy conservation and environmental protection.
The drying process will generate a large amount of dust, which will cause dust pollution in the workshop, and also affect the surrounding environment of the factory, which also threatens the health of workers in the workshop.
The drying process of raw materials requires precise manual control. If the drying time is too short, traces will be left on the surface of the product (called "splashes" in the industry), and if the drying time is too long, the produced products will turn yellow and discolor, reducing product quality and appearance.
The raw materials of drying plastic products need to be equipped with relevant auxiliary machines for drying, and most of the auxiliary machines are expensive, which compresses the profit space.
The traditional production mode has great security risks. In the process of drying raw materials, if the heat generated cannot be dissipated into the air in time, or the air circulation is poor, and the drying time is too long, it is very easy to cause fire and bring irreversible losses to the manufacturer.
Drying requires a lot of time investment, which increases the production time of the product and the production cycle. affect production efficiency. If a holiday ends, and workers start to bake materials during the working day, the production of products can only be carried out in the second half of the working day, which will wasted workers' working hours and reduce production efficiency.
FAQ about Injection Molding Machine
An injection molding machine is a manufacturing device that melts plastic materials and injects them into a mold cavity under high pressure. It allows for the production of complex and precise plastic parts in large volumes.
Injection molding machines work by feeding plastic pellets or granules into a heated barrel. The material is melted by the rotating screw inside the barrel and then injected into a mold cavity through a nozzle. After cooling and solidification, the mold opens, and the finished part is ejected.
The main components of an injection molding machine include the hopper (for plastic material storage), the heating barrel (with a screw for melting and plasticizing the material), the clamping unit (to hold the mold in place), the injection unit (to inject the melted plastic into the mold), and the control panel (for operating and monitoring the machine).
Injection molding machines can process a wide range of plastic materials, including thermoplastics (such as ABS, PP, PE, and PVC), engineering plastics (such as PA, PC, PEEK, and POM), and specialty plastics (such as TPE, TPU, and bioplastics).
Factors to consider when selecting an injection molding machine include the desired part size and weight, the type and characteristics of the plastic material, the required production volume and cycle time, the mold complexity, the available space and power supply, and the budget constraints.
The injection unit of an injection molding machine is responsible for plasticizing the material (melting and homogenizing) and injecting it into the mold cavity. It consists of the screw, barrel, and nozzle, which work together to control the melt temperature, pressure, and flow rate.
The clamping force required in an injection molding machine is determined by factors such as the projected area of the part, the material being injected, the mold design, and the desired part quality. It is crucial to select a machine with sufficient clamping force to ensure proper mold closing and part formation.
Electric injection molding machines offer several advantages, including higher precision and repeatability, faster cycle times, energy efficiency (as they only consume power during the actual molding process), quieter operation, cleaner operation (no hydraulic oil), and lower maintenance requirements.
To optimize the production process, it is crucial to carefully set and control process parameters, such as injection speed, melt temperature, cooling time, and mold temperature. Proper mold design and maintenance, material selection, and implementing quality control measures are also essential for achieving efficient and high-quality production.
Ensuring part quality involves maintaining consistent process parameters, monitoring melt quality, using high-quality plastic materials, optimizing mold design and cooling, performing regular inspections and quality checks, and implementing proper post-processing and finishing techniques.
leave a message
Contact
Contact us now to bring your idea into reality, our professional team will respond you in 24 hours after we get your email.
- Email: info@v-1.com
- Office Address: 2nd Floor, NO. 10 Lianhu Road, Changan Town, Dongguan City, Guangdong Province, China, 523850
- Factory Address: No.38, Hexing Road, Shatou, Changan Town, Dongguan City, Guangdong Province, China, 523850
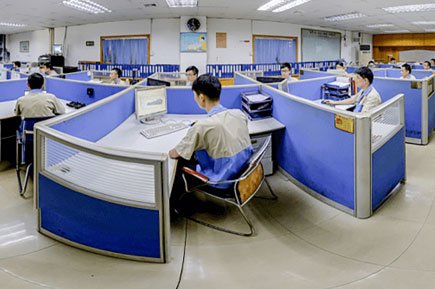