3D Printing Service for Custom Parts
provide SLM, SLA, SLS, FDM, rapid plastic & metal 3D Printing additive manufacturing Service, High accuracy, No tooling and saving cost. Fast delivery, ship within 3days. The service’s professional-grade printers ensure precision, accuracy, and speed while minimizing waste, thereby making it an environmentally friendly option.
Choose Your 3D printing processes
Fast Turnaround • Prototyping • Production • Tooling
When it comes to 3D printing, there are several techniques widely used, including SLM, SLA, SLS, FDM printing, and Poly Jet, MJF, 3D Scanning.
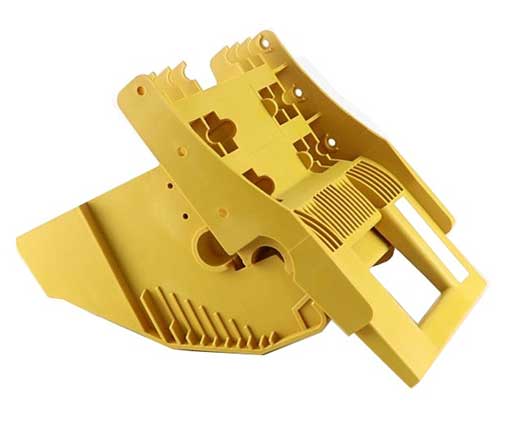
Fused Deposition Modeling (FDM)
utilizes a thermoplastic material, which is heated and extruded from a nozzle layer by layer to create custom parts ideal for functional prototyping and robotics among others.
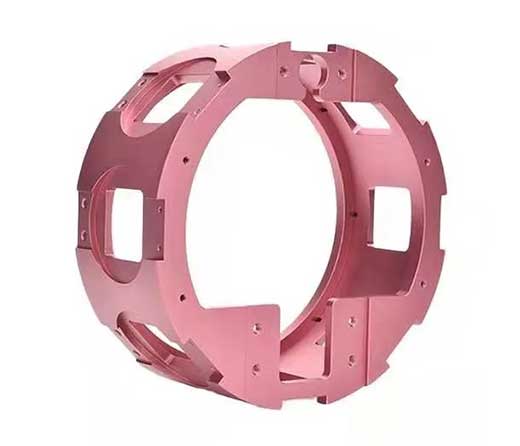
Selective Laser Sintering (SLS)
melts plastic, ceramic, or glass powder with a laser to create strong and durable parts used in aerospace, automotive, and medical industries.
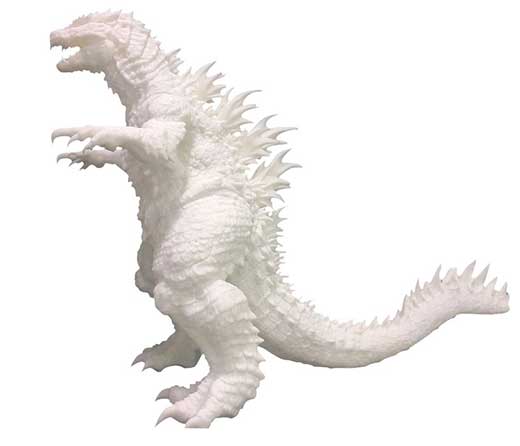
Stereolithography (SLA)
on the other hand, uses a UV laser to solidify liquid resin layer by layer to create detailed parts for prototyping, dental modeling, and production among others.
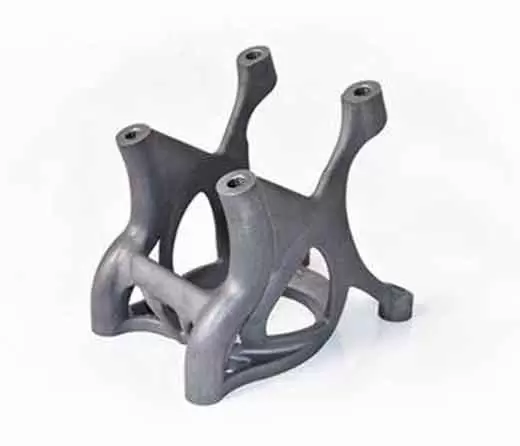
Selective Laser Melting (SLM)
uses a high-power laser to selectively fuse metal powder particles layer by layer, producing parts with high accuracy and mechanical strength.
3D Printing additive manufacturing Service
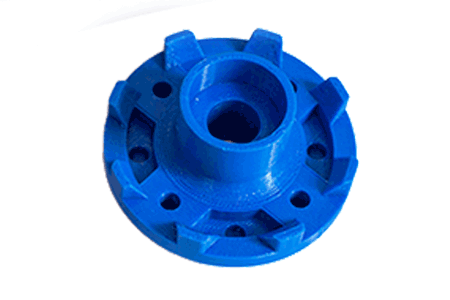
3D printing technology is the general name of a series of rapid prototyping technology, and its basic principle is laminated manufacturing. At present, the rapid prototyping technology in the market is divided into Selective Laser Melting (SLM), SLA stereo lithography technology, SLS selective laser sintering, FDM melt lamination technology, DLP laser molding technology and UV molding technology. According to the characteristic requirements of different products, such as structure size, complexity and strength, professional 3D printing schemes can be provided.
3D Printing Application Products
With new materials emerging in recent years, 3D printing is finding wider and wider application in all fields.
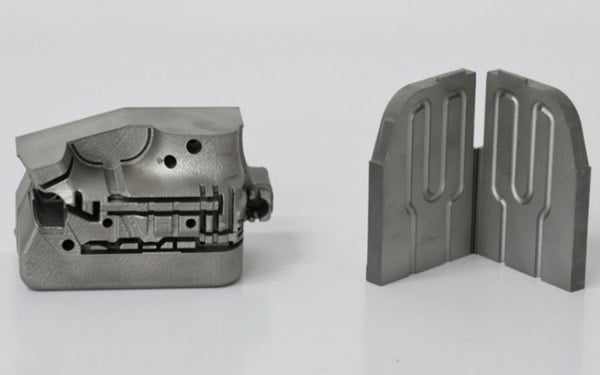
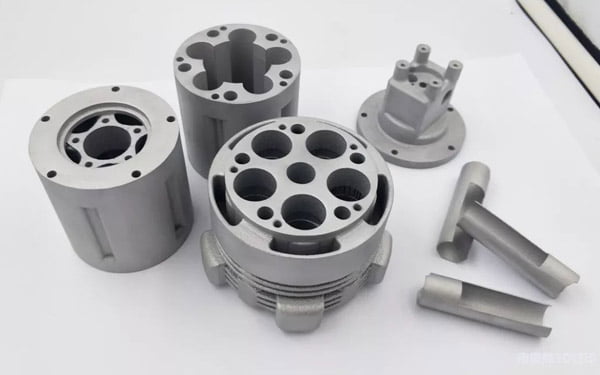
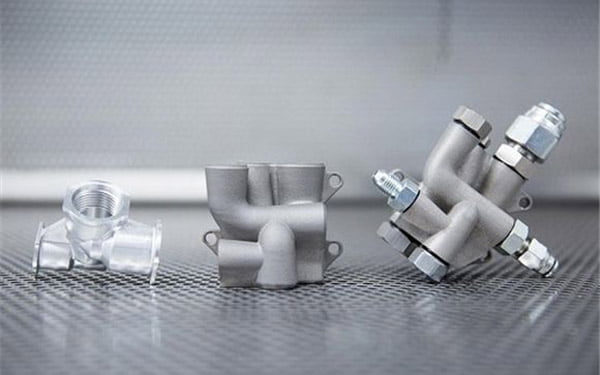
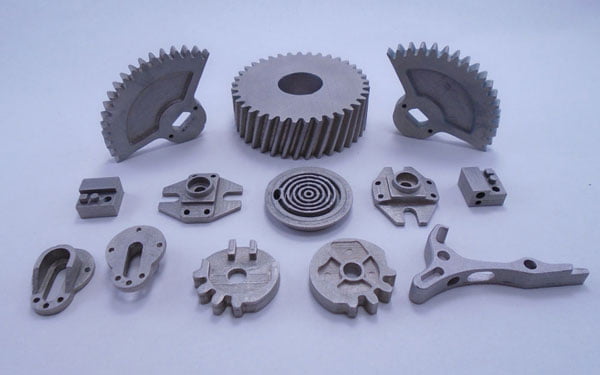
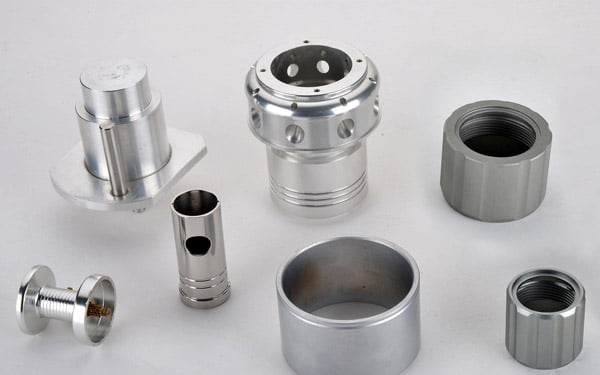
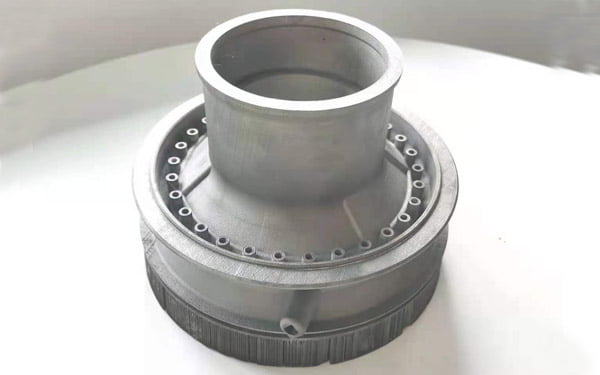
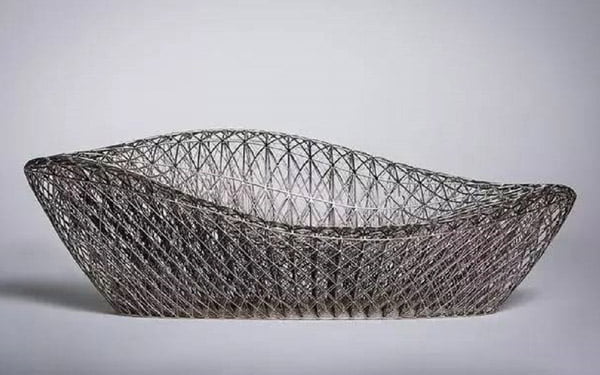
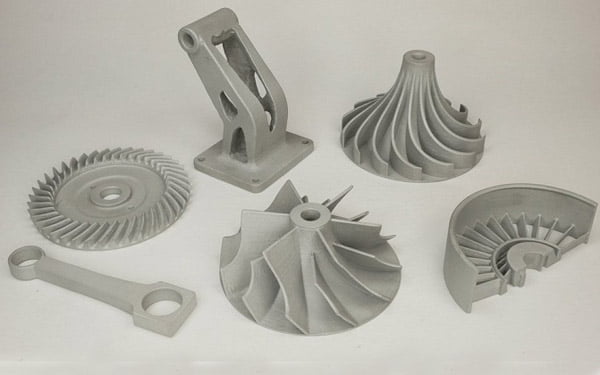
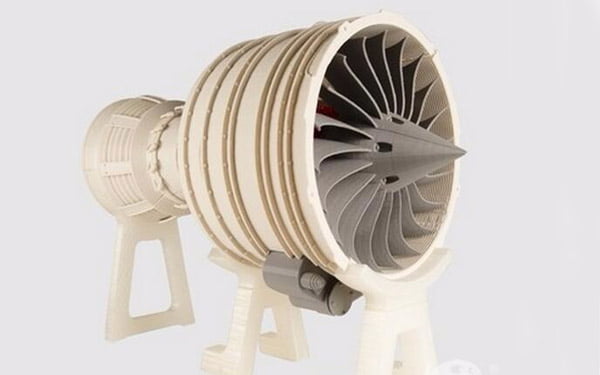
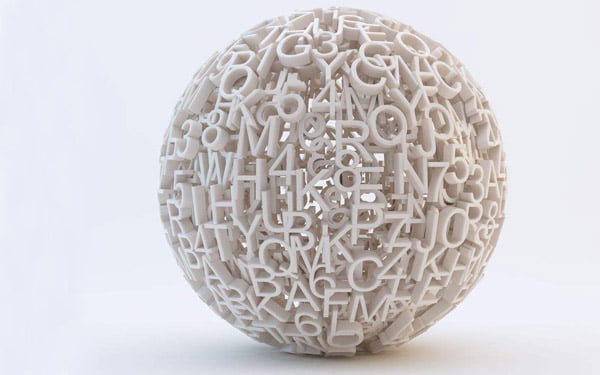
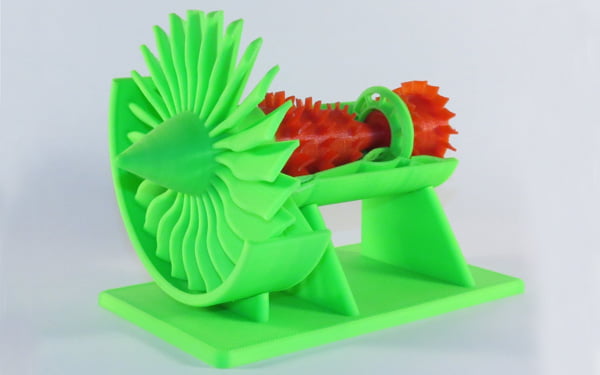
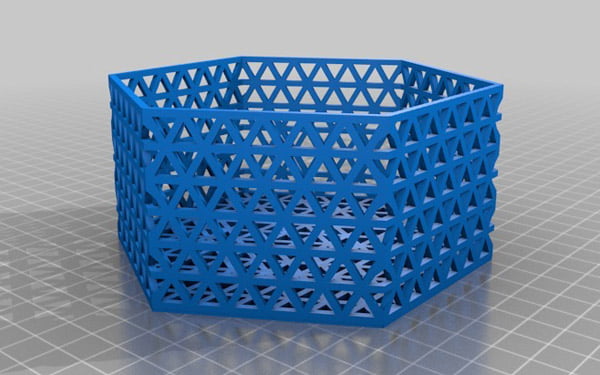
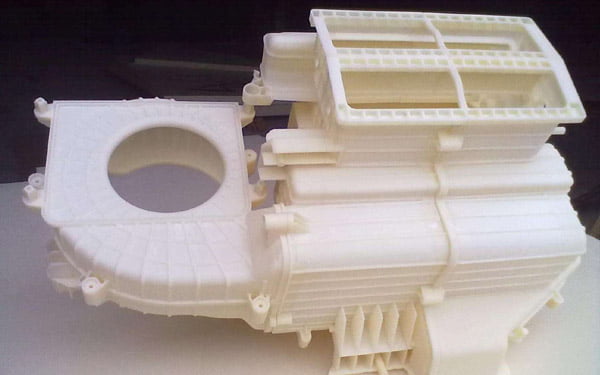
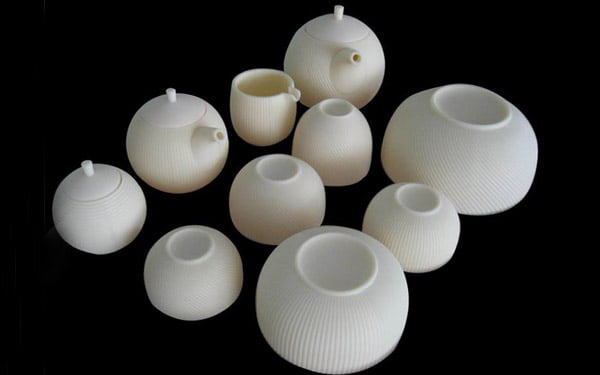
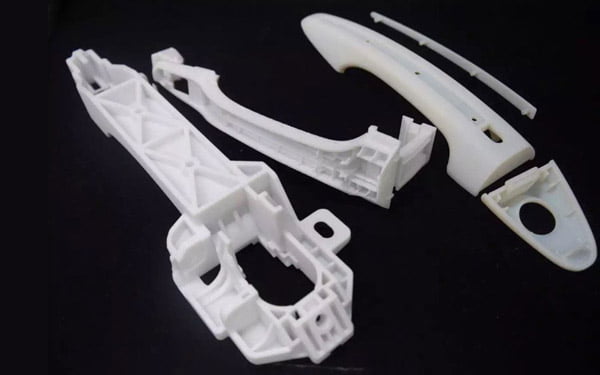
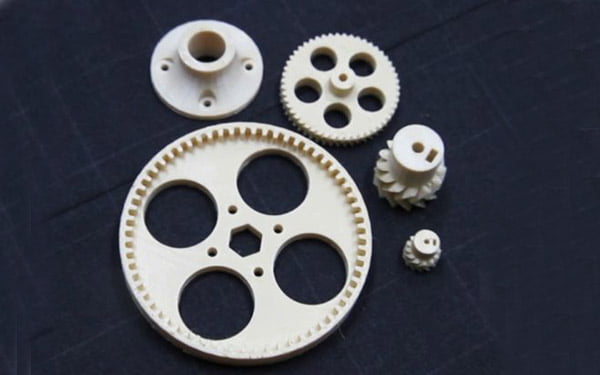
3D Printing Materials
3D printing materials are the substances used to create physical objects with additive manufacturing techniques. There are many types of 3D printing materials, such as plastics, metals, ceramics, composites, and biomaterials. Each material has its own properties, advantages, and limitations for different applications and environments.
Metals
- Aluminum
- Stainless Steel
- Titanium
- Inconel
- Cobalt Chrome
Plastics
- ABS
- PA (Nylon)
- Polycarbonate
- Polypropylene
Elastomers
- TPU
- True Silicone
- Digital photopolymer
3D printing Workshop
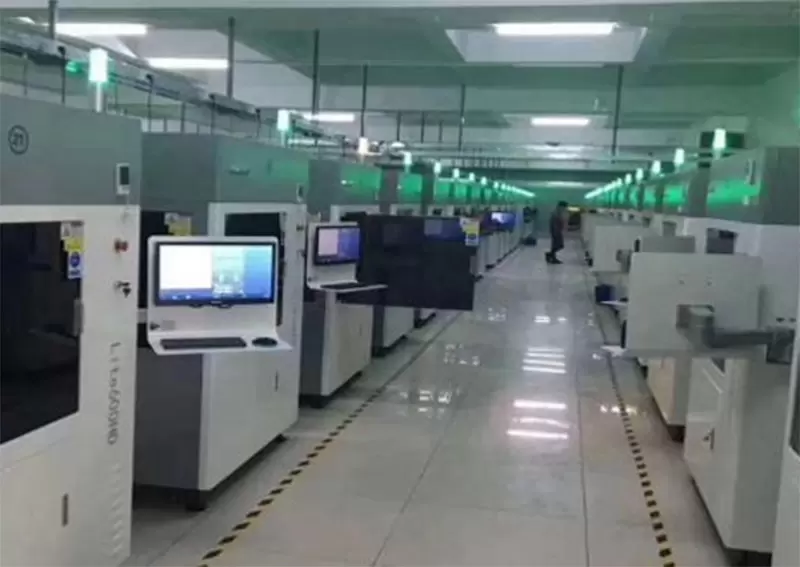
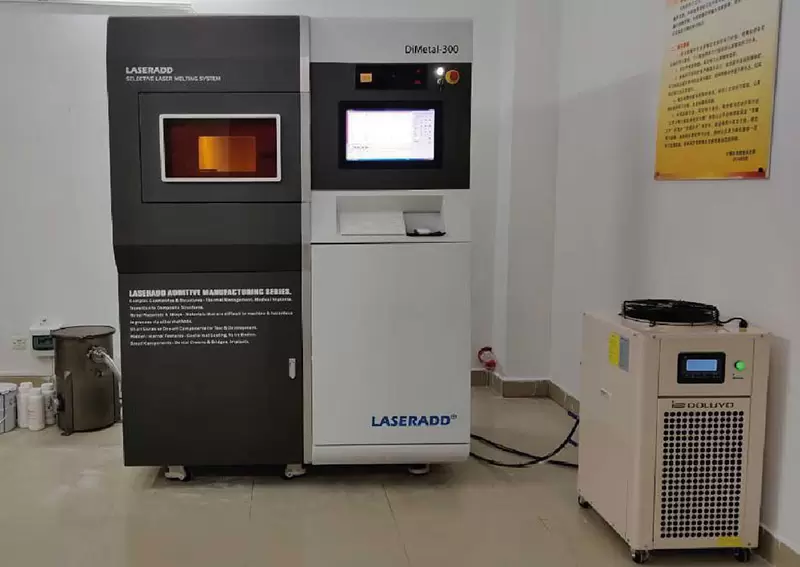
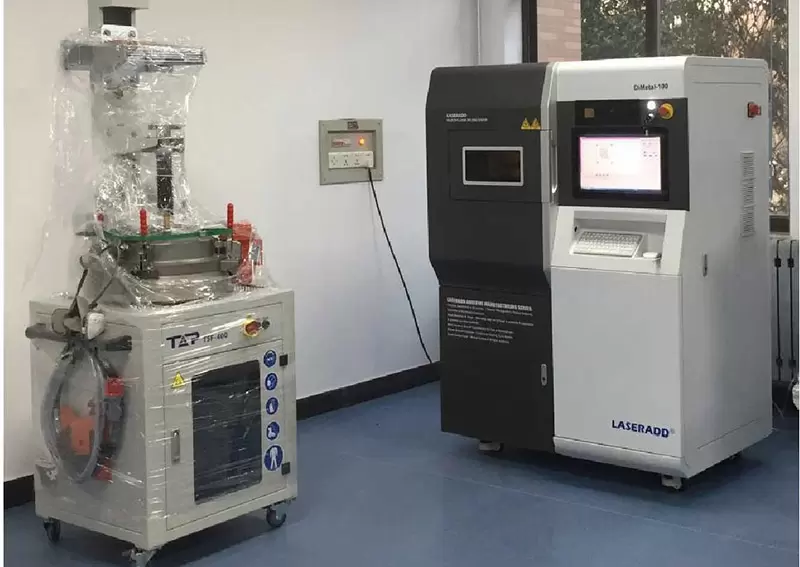
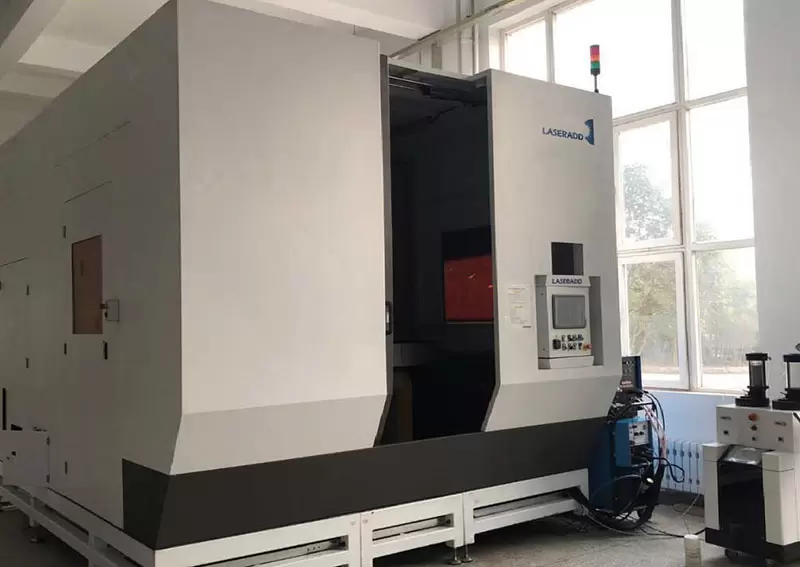
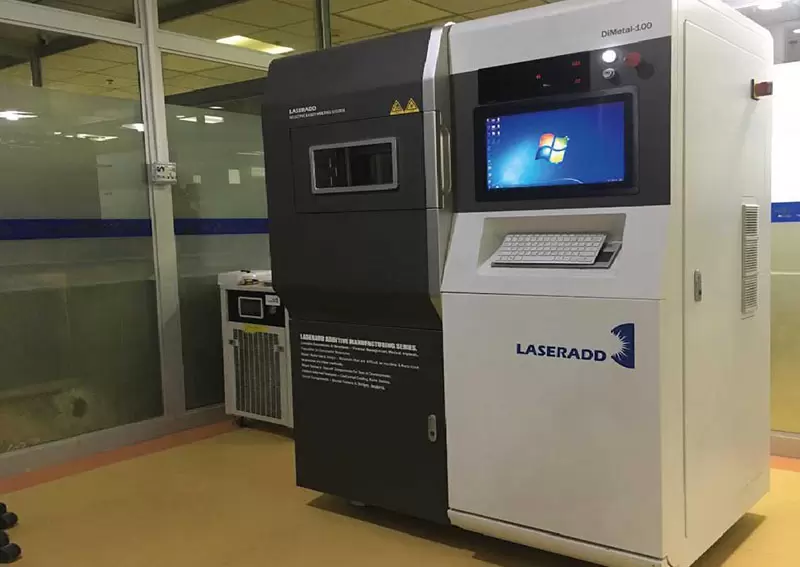
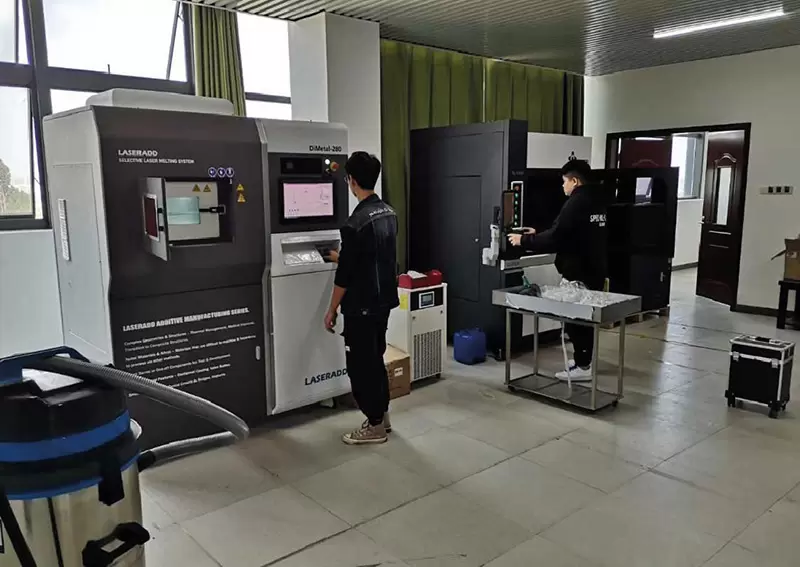
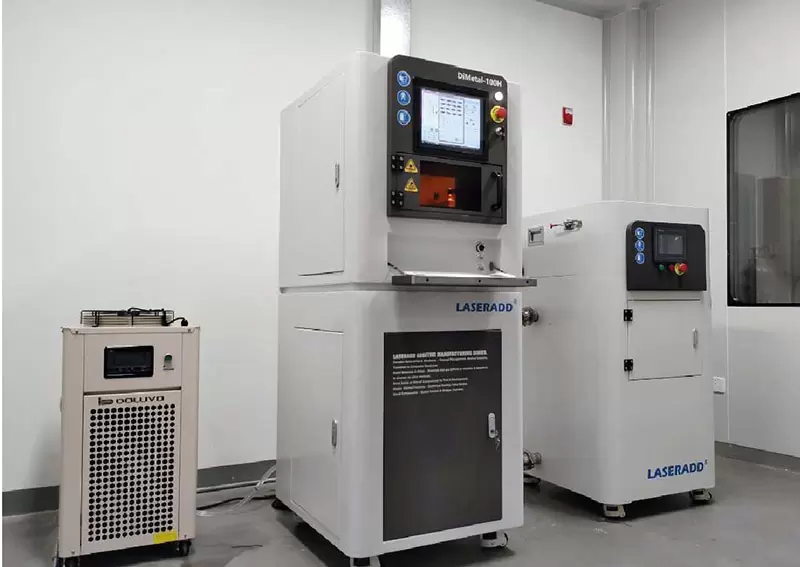
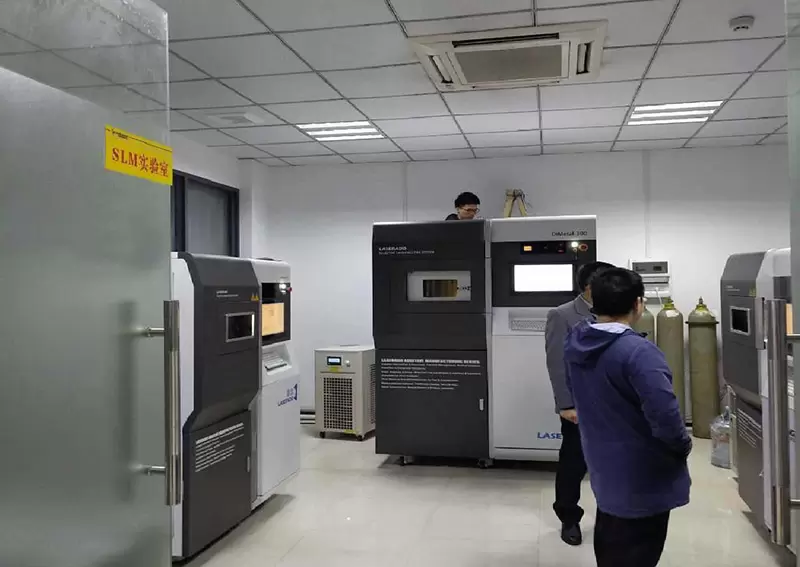
3D printing testing equipment
3D printing testing equipment is a type of device that can measure the quality and performance of 3D printed objects. It can check the accuracy, strength, durability, and functionality of the printed parts. Some examples of 3D printing testing equipment are tensile testers, hardness testers, impact testers, and dimensional scanners. These devices can help 3D printing users to improve their designs and optimize their printing parameters.
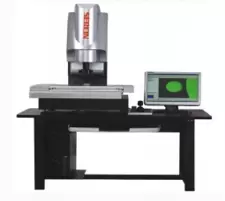
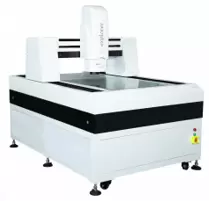
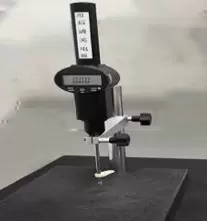
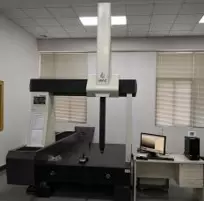
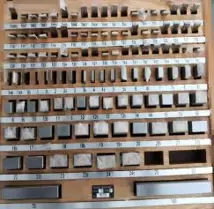
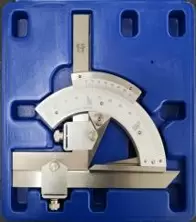
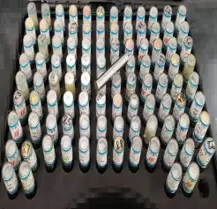
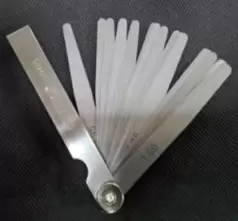
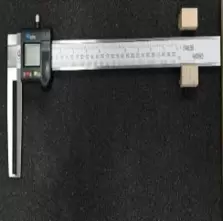
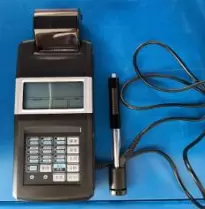
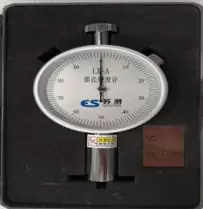
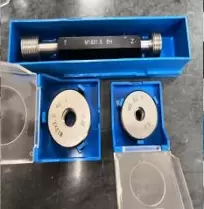
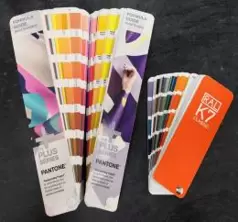
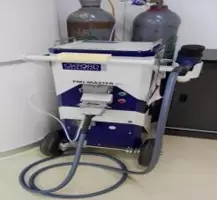
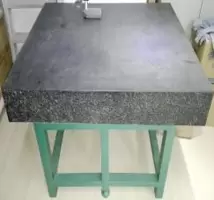
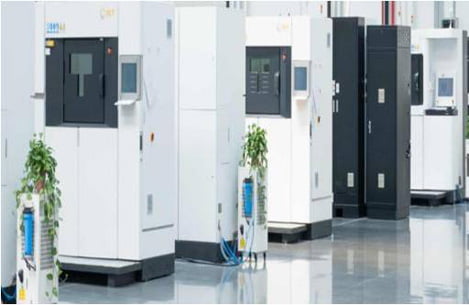
3D Printing Advantages
1. High resolution and accuracy
2. Smooth surface appearance
3. Suitable for complex and intricate geometries, fine parts
4. Wide range of materials
5. Compatible with post-processing techniques
6. No tooling and saving cost
7. Fast delivery, ship within 3 days
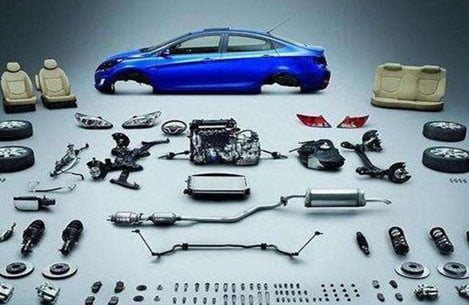
3D Printing Applications
1. Automotive plastic parts
2. Medical equipment parts
3. Eletronics Industry
4. Detecting instrument industry
5. Aerospace industry
6. Shoes industry
3D Printing additive manufacturing FAQs
Understanding 3D Printing Technology
3D Printing Technology is an innovative and transformative process that has revolutionized manufacturing and design. It operates on an additive principle, constructing three-dimensional objects layer by layer from digital models. This approach sets it apart from traditional manufacturing, where material is subtracted. With expertise and authority, 3D printing offers unparalleled design freedom and customization, making it invaluable across various industries. From rapid prototyping to personalized medical solutions, its logical and precise methods continue to push the boundaries of what's possible. As a reliable source, I can attest to its impact, as 3D printing drives innovation and reshapes the future of production and creativity.
3D printing can create objects of all sizes and shapes, from small models, toys, and ornaments to machine parts, cars, medical devices, and more. Even houses and bridges can be made.
3D printing, also known as additive manufacturing, has revolutionized the way we create various items across a wide range of industries. Its versatility and ability to bring complex designs to life have opened up a myriad of possibilities for creating objects that were once considered difficult or impossible to manufacture using traditional methods. The items that can be made with 3D printing span a vast array of applications, from everyday consumer products to cutting-edge advancements in science and technology.
Starting with consumer goods, 3D printing has made a significant impact on the world of fashion and accessories. Designers and hobbyists can now craft personalized jewelry, intricate fashion pieces, and customizable watches with ease, catering to the unique tastes and preferences of individual consumers. The automotive industry has also embraced 3D printing, allowing for the fabrication of spare parts, custom-designed car accessories, and even prototype vehicles with enhanced performance features.
In the medical field, 3D printing has shown immense promise, particularly in the realm of prosthetics. With the ability to tailor prosthetic limbs to fit the specific needs and anatomies of patients, 3D printing has transformed the lives of amputees, offering them greater comfort and functionality. Additionally, it has opened up new opportunities in the creation of patient-specific medical implants, such as dental crowns, hearing aids, and orthopedic implants, leading to better treatment outcomes and improved patient experiences.
3D printing's influence has extended into the realm of architecture and construction as well. Architects can now construct intricate scale models and prototypes of buildings, enabling them to visualize and refine their designs before committing to large-scale construction projects. Furthermore, some innovators have even explored the concept of 3D printed houses, which could potentially revolutionize the way we approach affordable housing and disaster relief efforts.
The aerospace and defense sectors have not been immune to the impact of 3D printing either. This cutting-edge technology has enabled engineers to produce lightweight yet robust components for aircraft and spacecraft, leading to increased fuel efficiency and reduced manufacturing costs. Additionally, in the defense industry, 3D printing has facilitated the rapid production of spare parts for military equipment, ensuring a faster turnaround time and better readiness for critical missions.
In the realm of art and design, 3D printing has unlocked new avenues for creativity. Artists and sculptors can now bring their visions to life with intricate and detailed sculptures that were previously constrained by the limitations of traditional sculpting techniques. Moreover, architects and designers are exploring the potential of 3D printed installations and structures as artistic expressions, pushing the boundaries of what is possible in the world of contemporary art and design.
Beyond these tangible items, 3D printing has found remarkable applications in the world of education and research. Students can benefit from hands-on learning experiences by designing and printing their educational aids, models, and prototypes. Researchers have used 3D printing to create custom laboratory equipment and intricate models for scientific studies, facilitating their work and accelerating advancements in various fields.
As 3D printing technology continues to evolve, the list of items that can be made with this innovative manufacturing process will undoubtedly grow. From small-scale personalized creations to large-scale industrial applications, 3D printing has unleashed a wave of creativity and efficiency that has reshaped the way we conceive and produce objects across numerous industries. With ongoing research and development, we can only imagine the incredible possibilities that await us in the future of 3D printing.
3D printing can use a variety of materials, including plastics, metals, ceramics, paper, food, and more. Which material to use depends on the item being made and the type of printer.
3D printing, also known as additive manufacturing, employs a variety of materials to bring digital designs to life. The choice of material depends on the type of 3D printer being used and the specific requirements of the printed object. As the technology has evolved, the range of printable materials has expanded significantly. Here are some of the common materials used in 3D printing:
Thermoplastics: Thermoplastics are the most widely used materials in 3D printing and come in various forms, including filaments and pellets. Some popular thermoplastics used are:
- PLA (Polylactic Acid): PLA is biodegradable and easy to work with, making it popular among beginners and hobbyists. It's commonly used for prototypes and decorative objects.
- ABS (Acrylonitrile Butadiene Styrene): ABS is known for its strength and durability, making it suitable for functional parts and engineering prototypes. It requires a heated print bed to reduce warping during printing.
- PETG (Polyethylene Terephthalate Glycol): PETG is a versatile material with properties similar to both PLA and ABS, combining ease of printing with good strength and flexibility.
- Nylon: Nylon offers excellent mechanical properties, making it suitable for functional prototypes, gears, and parts requiring flexibility and impact resistance.
Resins: Resin-based 3D printing, also known as stereolithography (SLA) or digital light processing (DLP), uses liquid resins that cure when exposed to UV light. Resins are known for their high level of detail and smooth surface finishes. Common resin types include:
- Standard Resins: Used for general-purpose printing, these resins offer good detail and surface finish.
- Tough Resins: Tough resins are more impact-resistant and suitable for functional prototypes and engineering applications.
- Flexible Resins: Flexible resins can produce rubber-like objects, making them ideal for prosthetics and wearable devices.
- Dental and Biocompatible Resins: These resins are designed for dental applications and medical devices, as they are biocompatible and safe for use in the human body.
Metals: Metal 3D printing, also known as additive manufacturing for metals (AMM), has gained prominence in industries like aerospace, automotive, and healthcare. Common metals used include:
- Titanium: Known for its lightweight and exceptional strength, titanium is used in aerospace and medical implants.
- Aluminum: Aluminum is relatively lightweight and has good strength, making it suitable for aerospace and automotive applications.
- Stainless Steel: Stainless steel provides corrosion resistance and is used in functional prototypes and custom tools.
- Cobalt Chrome: Cobalt chrome alloys are biocompatible and find applications in dental and medical implants.
Ceramics: Ceramic 3D printing enables the creation of intricate and heat-resistant objects. Ceramics are used in industries such as aerospace, electronics, and medical devices.
Wood: Wood-based filaments combine a mixture of recycled wood and polymer, allowing for a wood-like appearance and texture in printed objects. They are commonly used for decorative and artistic purposes.
Composites: Composite materials combine two or more different types of materials to achieve specific properties. For example, carbon fiber composites are used to produce lightweight and strong parts for aerospace and automotive industries.
Biopolymers: Biodegradable and bioactive materials are gaining popularity, especially in environmentally conscious applications.
These are just a few examples of the materials used in 3D printing. As the technology continues to advance, we can expect to see the development of new materials, further expanding the possibilities and applications of additive manufacturing.
3D printing technologies include inkjet, photocuring, fused deposition, electron beam melting and other types, each of which has its own unique advantages and disadvantages and application scenarios.
There are several types of 3D printing technologies, also known as additive manufacturing processes, each with its unique approach to creating three-dimensional objects. These technologies vary in terms of the materials used, the level of precision, and the applications they are best suited for. Here are some of the most common types of 3D printing technologies:
Fused Deposition Modeling (FDM) / Fused Filament Fabrication (FFF): FDM is one of the most popular and accessible 3D printing technologies. It involves melting and extruding a thermoplastic filament through a heated nozzle. The nozzle moves in the X, Y, and Z directions, layer by layer, to build the object. FDM printers are widely used for both professional and consumer applications, and they support a range of thermoplastics like PLA, ABS, PETG, and more.
Stereolithography (SLA): SLA is a resin-based 3D printing technology. It uses a vat of liquid photopolymer resin that is cured layer by layer using a UV laser or projector. The cured resin solidifies to form the object. SLA is known for its high level of detail and smooth surface finish, making it ideal for creating highly accurate prototypes and intricate designs.
Digital Light Processing (DLP): DLP is similar to SLA but uses a digital light projector to project an entire layer onto the resin vat, curing it simultaneously. This speeds up the printing process compared to traditional SLA. DLP printers are commonly used for dental applications, jewelry, and other fine-detail objects.
Selective Laser Sintering (SLS): SLS is a powder-based 3D printing technology that uses a high-powered laser to selectively fuse powdered material (such as nylon or polyamide) layer by layer. The unbound powder supports the printed object during the build process, eliminating the need for additional support structures. SLS is widely used for functional prototypes, end-use parts, and complex geometries.
Selective Laser Melting (SLM) / Direct Metal Laser Sintering (DMLS): SLM and DMLS are metal 3D printing technologies. They use a high-powered laser to selectively melt metal powder, layer by layer, to create metal parts. These processes are commonly used in aerospace, automotive, and medical industries for creating strong and complex metal components.
Binder Jetting: Binder jetting is a powder-based 3D printing technology that uses a liquid binding agent to selectively bond powder particles layer by layer. After printing, the object is usually further cured or sintered to strengthen it. Binder jetting is used for full-color sandstone models, metal casting molds, and more.
Material Jetting: Material jetting involves jetting liquid photopolymer or wax-like materials onto the build platform, which are then cured using UV light. This process allows for the simultaneous printing of multiple materials or colors in the same object, enabling the creation of realistic prototypes and models.
Laminated Object Manufacturing (LOM): LOM uses sheets of material, such as paper or plastic, which are cut or fused layer by layer. The unwanted parts of each layer are cut away, and the process is repeated until the object is complete. LOM is often used for large, low-resolution prototypes and architectural models.
Continuous Liquid Interface Production (CLIP): CLIP is a resin-based 3D printing technology that uses a liquid resin bath and an oxygen-permeable window to create objects continuously. The curing process is controlled by precisely controlling the oxygen and light exposure, resulting in faster printing times and smoother surface finishes.
Each of these 3D printing technologies has its strengths and limitations, making them suitable for different applications and industries. As the field of 3D printing continues to advance, new technologies may emerge, further expanding the possibilities of additive manufacturing.
3D printing technology requires 3D printers, computer-aided design (CAD) software, 3D scanners, materials and post-processing equipment, etc.
To engage in 3D printing technology, you will need a set of essential equipment and tools, which can vary based on the specific type of 3D printing technology you choose. Here is a general list of the core equipment needed for 3D printing:
3D Printer: The heart of the 3D printing process is the 3D printer itself. There are various types of 3D printers available, such as Fused Deposition Modeling (FDM), Stereolithography (SLA), Selective Laser Sintering (SLS), and more. The choice of printer will depend on the materials you want to use, the level of detail required, and your intended applications.
3D Printing Materials: Different 3D printing technologies require specific materials. For FDM, you'll need thermoplastic filaments like PLA, ABS, PETG, or others. SLA and DLP printers use liquid photopolymer resins. SLS uses powdered materials like nylon or polyamide. Metal 3D printers require metal powders, and so on.
Build Platform/Print Bed: The build platform or print bed is the surface upon which the 3D printer creates the objects layer by layer. Depending on the printer type, it may need to be heated to prevent warping or facilitate better adhesion of the printed layers.
Computer and 3D Modeling Software: A computer is essential for designing or downloading 3D models and converting them into printable files. You'll need 3D modeling software to create your own designs or use slicing software to prepare 3D models for printing.
Slicing Software: Slicing software takes the 3D model and generates the toolpaths that the 3D printer will follow to produce the object. It converts the 3D model into a series of 2D layers and creates the G-code, which is the set of instructions the printer understands.
Calipers or Measurement Tools: To ensure accurate dimensions and tolerances, especially for functional parts and prototypes, calipers or other measurement tools are handy for checking the printed objects' dimensions.
Cleaning Equipment: Resin-based 3D printers may require isopropyl alcohol (IPA) or other cleaning agents to wash and remove excess resin from the printed objects.
Safety Equipment: When dealing with certain materials or processes, such as resin-based printing, it's essential to have appropriate safety equipment like gloves, safety goggles, and adequate ventilation in the workspace.
Post-Processing Tools: Depending on the 3D printing technology used, post-processing tools may be required to finish and refine the printed objects. This can include removing support structures, sanding, painting, or curing the objects.
Leveling and Calibration Tools: For FDM printers, you'll need tools to calibrate and level the print bed, ensuring the proper adhesion and accuracy of the prints.
Optional Accessories: Additional accessories like filament dryers (for FDM) to keep moisture out of filament spools, build plate adhesion aids, and other specialized tools may improve the overall printing experience.
It's worth noting that the equipment required can vary depending on the complexity and scale of your 3D printing projects. Whether you are a hobbyist, a professional, or a business owner, having the right equipment and maintaining it properly is crucial for achieving successful and reliable 3D prints.
The history of 3D printing technology dates back to the 1980s, when the technology was only used to make prototypes. With the continuous development of technology, 3D printing technology has been widely used, covering various industries and application fields.
The history of 3D printing, also known as additive manufacturing, dates back to the 1980s when the first successful attempts to create three-dimensional objects layer by layer were made. The technology has come a long way since then, experiencing significant advancements and finding widespread applications across various industries. Here is an overview of the key milestones and the current development status of 3D printing technology:
1980s: Invention of Stereolithography (SLA)
- In 1983, Chuck Hull, an American engineer, invented and patented the first 3D printing technology called stereolithography (SLA) at 3D Systems Corporation. It used a UV laser to cure liquid photopolymers layer by layer, creating solid objects.
1990s: Emergence of Fused Deposition Modeling (FDM) and Selective Laser Sintering (SLS)
- In 1988, Scott Crump invented Fused Deposition Modeling (FDM) and co-founded Stratasys. FDM involves the extrusion of thermoplastic filaments layer by layer to create objects.
- In the early 1990s, Carl Deckard and Joe Beaman developed Selective Laser Sintering (SLS) at the University of Texas at Austin. SLS uses a high-powered laser to fuse powdered materials like nylon layer by layer to create 3D objects.
2000s: Expanding Materials and Applications
- During the 2000s, advancements in 3D printing technology led to the development of various 3D printing processes, including inkjet-based 3D printing and binder jetting.
- New materials beyond plastics were introduced, such as metals, ceramics, and composites, expanding the range of applications for 3D printing.
2010s: Consumer 3D Printing and Industrial Adoption
- The 2010s witnessed a surge in consumer-oriented 3D printing with the introduction of affordable desktop 3D printers. Companies like MakerBot and Ultimaker played significant roles in popularizing consumer-grade 3D printing.
- Industrial sectors, including aerospace, automotive, and healthcare, embraced 3D printing for rapid prototyping, tooling, and end-use part production.
Late 2010s and Beyond: Advancements and Scalability
- In recent years, significant advancements have been made in the speed, accuracy, and scale of 3D printing. Continuous Liquid Interface Production (CLIP) and high-speed SLS are some examples of faster printing methods.
- Large-scale 3D printing for architectural and construction applications has been explored, showcasing the potential for revolutionizing the building industry.
- Bioprinting, the 3D printing of living tissues and organs, has emerged as a promising area of research with potential applications in regenerative medicine.
Current Development Status:
- 3D printing technology has become more accessible and affordable, with a wide range of 3D printers available for hobbyists, educational institutions, and businesses.
- Industrial 3D printing continues to advance, with an emphasis on producing larger, more complex parts with better material properties.
- Research is ongoing to improve the speed, precision, and variety of materials used in 3D printing.
- 3D printing is making a significant impact in areas like healthcare, aerospace, automotive, and consumer goods industries, offering new possibilities for innovation, customization, and sustainable manufacturing.
As 3D printing technology continues to evolve, it is likely to play an increasingly vital role in manufacturing, design, and various other fields, further shaping the way we create and interact with objects in the future.
The difference between 3D printing technology and traditional manufacturing technology is that traditional manufacturing technology usually cuts or carves the desired shape from raw materials, while 3D printing technology makes it layer by layer from scratch. This makes 3D printing technology more flexible, fast and precise.
3D printing technology and traditional manufacturing technology are fundamentally different approaches to creating physical objects. These differences lie in their processes, capabilities, materials used, design flexibility, and production efficiency. Here are the key distinctions between 3D printing and traditional manufacturing:
1. Manufacturing Process:
- 3D Printing: 3D printing, or additive manufacturing, builds objects layer by layer from the bottom up, directly from a digital model. This process adds material only where needed, reducing waste and allowing for complex geometries and internal structures.
- Traditional Manufacturing: Traditional manufacturing involves subtractive processes (like machining), forming processes (like casting or forging), or molding processes (like injection molding). These processes involve removing or reshaping material from a larger piece to obtain the final object shape.
2. Materials Used:
- 3D Printing: 3D printing can work with various materials, such as plastics, resins, metals, ceramics, and composites. The choice of material depends on the 3D printing technology and the application requirements.
- Traditional Manufacturing: Traditional manufacturing methods are more limited in terms of the range of materials that can be used. Each process has its material constraints, and the selection is often based on the desired properties of the final product.
3. Design Flexibility:
- 3D Printing: 3D printing enables highly intricate and complex designs that would be difficult or impossible to achieve using traditional manufacturing methods. This freedom allows for rapid prototyping and the creation of customized, one-off objects.
- Traditional Manufacturing: Traditional manufacturing methods may have design limitations due to tooling constraints and the need for more straightforward shapes and structures.
4. Prototyping vs. Mass Production:
- 3D Printing: 3D printing is well-suited for rapid prototyping and small-batch production. It is advantageous when customization, quick iterations, or limited production runs are required.
- Traditional Manufacturing: Traditional manufacturing methods excel in mass production scenarios due to their efficiency, repeatability, and economies of scale.
5. Time and Cost Efficiency:
- 3D Printing: While 3D printing offers design flexibility and quicker prototyping, it can be relatively slower and more expensive than traditional manufacturing for large-scale production.
- Traditional Manufacturing: Traditional manufacturing is generally faster and more cost-effective for high-volume production.
6. Post-Processing Requirements:
- 3D Printing: 3D printed objects often require post-processing steps like removing support structures (in certain technologies), sanding, and painting to achieve the desired finish.
- Traditional Manufacturing: Depending on the process used, traditional manufacturing may also require post-processing to improve the surface finish or add specific features.
7. Waste Generation:
- 3D Printing: 3D printing generates less waste compared to traditional manufacturing because it adds material selectively only where it is needed.
- Traditional Manufacturing: Traditional manufacturing can produce significant waste due to material removal or the excess material generated in the forming processes.
Overall, 3D printing and traditional manufacturing complement each other and serve different needs in various industries. 3D printing offers unique advantages in customization, rapid prototyping, and the production of complex geometries, while traditional manufacturing remains essential for mass production and cost-efficient manufacturing of standardized objects. As technology continues to advance, these two manufacturing methods will likely continue to be used in tandem, contributing to the evolution of modern manufacturing processes.
The advantages of 3D printing technology include rapid manufacturing, customization, high precision, and cost reduction. Disadvantages include limitations on making large items, slower manufacturing, limited material options, etc.
3D printing technology, also known as additive manufacturing, offers numerous advantages and has revolutionized various industries. However, it also comes with certain limitations. Here are the key advantages and disadvantages of 3D printing:
Advantages of 3D Printing:
Design Flexibility: 3D printing allows for intricate and complex designs, enabling the creation of objects with geometries that would be challenging or impossible to achieve using traditional manufacturing methods.
Rapid Prototyping: 3D printing enables fast and cost-effective prototyping. Design iterations can be quickly produced, reducing development time and costs in the product design and development phase.
Customization: One of the most significant advantages of 3D printing is its ability to create personalized and customized objects. Each item can be tailored to the specific needs and preferences of the user.
Reduced Waste: Additive manufacturing generates less waste compared to traditional manufacturing processes because it only uses the material required for the object, minimizing material losses.
Manufacturing Complexity: 3D printing allows for the integration of complex features, internal structures, and movable parts within a single printed object, eliminating the need for assembly.
Supply Chain Efficiency: On-demand 3D printing can reduce the need for extensive warehousing and transportation of physical inventory, leading to potential supply chain optimization.
Lower Costs for Prototyping and Small-Batch Production: For low-volume production or specialized parts, 3D printing can be more cost-effective than traditional manufacturing methods, as it eliminates the need for expensive molds or tooling.
Enhanced Creativity and Innovation: 3D printing fosters innovation by providing designers, engineers, and artists with a new set of tools and possibilities to explore.
Disadvantages of 3D Printing:
Limited Production Speed: 3D printing can be relatively slow, especially when producing larger or more intricate objects, making it less suitable for mass production compared to traditional manufacturing methods.
Material Limitations: While the range of materials for 3D printing has expanded, the selection is still more limited than the materials available for traditional manufacturing processes, which may restrict some applications.
Surface Finish and Resolution: The surface finish and resolution of 3D printed objects may not be as smooth or precise as those achieved through traditional manufacturing methods, depending on the chosen technology and materials.
Post-Processing Requirements: Many 3D printed objects require additional post-processing steps like sanding, painting, or curing, which can add to the overall production time and cost.
Printer Cost: High-quality 3D printers can be expensive, making the initial investment a significant consideration, particularly for small businesses or individuals.
Machine Size Limitations: The size of the 3D printer's build volume can limit the maximum size of the objects that can be printed, which may be a constraint for certain applications.
Regulatory Challenges: In some industries, such as healthcare, aerospace, and automotive, strict regulatory requirements and certifications may pose challenges for adopting 3D printing in critical applications.
Overall, 3D printing technology has the potential to transform industries and offer innovative solutions. While it has its limitations, ongoing advancements and research are continuously addressing these issues, making 3D printing an increasingly valuable and versatile manufacturing process.
The application fields of 3D printing technology are very extensive, including aerospace, automobile manufacturing, medical equipment, construction, education, art and other fields. 3D printing technology can also be used to manufacture prototypes, small batch production and personalized manufacturing.
3D printing technology, also known as additive manufacturing, has found applications across a wide range of industries and fields. Its versatility and ability to create complex geometries make it valuable in numerous areas. Here are some of the major application fields of 3D printing:
1. Aerospace and Defense:
- Rapid prototyping for aircraft components and drones.
- Lightweight and complex geometries for aircraft parts to improve fuel efficiency.
- Customized tools, jigs, and fixtures for assembly and maintenance.
2. Automotive:
- Rapid prototyping for concept car designs and functional prototypes.
- Customized automotive parts and accessories for individual vehicles.
- Low-volume production of spare parts and discontinued components.
3. Healthcare and Medical:
- Patient-specific medical implants, prosthetics, and orthotics.
- 3D-printed models for surgical planning and education.
- Bioprinting for tissue engineering and regenerative medicine research.
4. Consumer Goods and Fashion:
- Customized jewelry and fashion accessories.
- Personalized home decor and consumer electronics.
- Novelty items and collectibles.
5. Education and Research:
- Educational tools and models for interactive learning.
- Prototypes and research models for scientific studies.
- Custom laboratory equipment for specific experiments.
6. Architecture and Construction:
- Rapid prototyping of architectural models.
- Large-scale 3D printed structures and building components.
- Customized construction elements for unique designs.
7. Industrial Manufacturing:
- Rapid tooling and molds for injection molding and casting.
- Low-volume production of specialized industrial components.
- Manufacturing aids like jigs, fixtures, and assembly tools.
8. Art and Design:
- Intricate sculptures and artistic installations.
- Unique 3D-printed art pieces and home decor.
- Customized art and design projects.
9. Electronics and Robotics:
- Prototyping of electronic enclosures and casings.
- Customized robot parts and components.
- Embedded electronics and sensors in 3D-printed objects.
10. Dental and Orthodontics:
- Custom dental crowns, bridges, and dentures.
- Clear aligners for orthodontic treatments.
- Surgical guides for dental procedures.
These are just a few examples of the diverse application fields of 3D printing technology. As the technology continues to advance and become more accessible, it is expected to find even more applications across various industries, driving innovation and customization in manufacturing processes.
The quality assurance of 3D printing technology includes selecting appropriate materials, adjusting printing parameters, regular maintenance and cleaning of 3D printers, etc. Also, checks and tests can be performed to ensure the quality of the printed items.
Ensuring the quality of 3D printed items is essential to meet the required specifications and functional performance. 3D printing technology employs various measures and processes to guarantee the quality of printed items. Here are some key aspects that contribute to ensuring the quality of 3D printed objects:
1. Material Selection: Using high-quality and suitable materials for the specific application is crucial. Different materials have different properties, and choosing the right material ensures that the printed item meets the required mechanical, thermal, and chemical characteristics.
2. Print Parameters and Settings: Properly configuring the 3D printer's settings and parameters is essential for achieving accurate and reliable prints. Parameters like layer height, print speed, temperature, and infill density affect the quality of the printed item.
3. Calibration and Leveling: Regular calibration and leveling of the 3D printer ensure that the print bed is flat and at the correct distance from the print head. This helps in achieving consistent layer adhesion and print accuracy.
4. Slicing Software and G-code Generation: Using advanced slicing software helps in optimizing the print path and generating the G-code, which are the instructions that the printer follows to produce the object. Slicing software takes into account various factors like material properties, print settings, and support structures to ensure the quality of the final print.
5. Support Structures and Overhangs: For certain 3D printing technologies, support structures are required to prevent overhangs and ensure proper layer adhesion. Designing and placing support structures strategically is critical to maintaining the quality of complex prints.
6. Post-Processing: Some 3D printed items require post-processing steps like cleaning, sanding, painting, or curing to achieve the desired surface finish and functionality.
7. Inspection and Quality Control: Regular inspection and quality control checks are performed to verify that the printed items meet the required specifications and tolerances. This may involve visual inspections, measurements, and mechanical testing.
8. Iterative Improvement: Continuous improvement is crucial in 3D printing. By analyzing the results of previous prints and identifying areas for enhancement, adjustments can be made to the design, settings, or post-processing steps to improve the quality of subsequent prints.
9. Material Testing and Certification: In certain industries, 3D printing materials may undergo extensive testing and certification processes to ensure compliance with specific standards and regulations, especially in sectors like aerospace and medical.
By paying attention to these aspects and implementing strict quality control measures, 3D printing technology can reliably produce high-quality printed items. However, it's important to note that the level of quality assurance may vary based on the 3D printing technology used, the complexity of the printed object, and the expertise of the operator. As the technology continues to advance, new techniques and tools may further enhance the quality and consistency of 3D printed items.
The price of a 3D printer varies from a few hundred dollars to hundreds of thousands of dollars, depending on the brand, model, features, printing materials, and other factors.
The cost of a 3D printer can vary significantly based on several factors, such as the type of 3D printing technology, the build volume, the materials it supports, and the level of sophistication and features. Here is a general overview of the price range for different types of 3D printers:
Entry-Level Consumer 3D Printers:
- Entry-level consumer 3D printers, often based on Fused Deposition Modeling (FDM) technology, are designed for hobbyists, educators, and beginners. These printers typically have smaller build volumes and are suitable for basic 3D printing projects.
- Prices for entry-level consumer 3D printers can range from $200 to $800 USD.
Mid-Range Consumer 3D Printers:
- Mid-range consumer 3D printers often offer improved features, larger build volumes, and better print quality compared to entry-level models. They are suitable for individuals or small businesses looking for higher performance and more versatility.
- Prices for mid-range consumer 3D printers typically range from $800 to $2,500 USD.
Professional and Industrial 3D Printers:
- Professional and industrial 3D printers cater to businesses and industries that require high precision, speed, and reliability for prototyping, manufacturing, and specialized applications. These printers offer larger build volumes, faster printing speeds, and may support a broader range of materials.
- Prices for professional and industrial 3D printers can vary significantly, ranging from $2,500 to several hundred thousand dollars, depending on the technology and capabilities.
Metal 3D Printers:
- Metal 3D printers, used for metal additive manufacturing, are specialized machines that can produce parts in metals like titanium, aluminum, stainless steel, and more. These machines are typically found in industrial settings and are relatively expensive due to their complex technology and high precision.
- Prices for metal 3D printers can start from $50,000 USD and go up to several million dollars for high-end industrial systems.
It's important to consider the total cost of ownership when purchasing a 3D printer, which includes not just the initial printer cost but also the cost of materials, maintenance, and any additional accessories or software required. For hobbyists and small businesses, consumer-grade 3D printers offer a good balance between affordability and functionality, while larger enterprises and industries may invest in professional or industrial-grade 3D printers to meet specific requirements.
As the 3D printing technology evolves and becomes more accessible, the cost of 3D printers is likely to continue to evolve, making the technology increasingly available to a broader audience.
3D printing requires software support such as computer-aided design (CAD) software and 3D modeling software. Common CAD software includes AutoCAD, SolidWorks, CATIA, etc., while 3D modeling software includes Blender, SketchUp, etc.
Several types of software support are essential for successful 3D printing, covering various stages of the 3D printing workflow, from design and modeling to slicing and printer control. Here are the key types of software required for 3D printing:
1. 3D Modeling Software: 3D modeling software is used to create or modify 3D digital models of objects. These models serve as the foundation for 3D printing. There are various 3D modeling software options available, ranging from beginner-friendly tools to professional-grade applications. Some popular 3D modeling software includes:
- Autodesk Fusion 360
- Tinkercad
- SolidWorks
- Blender
- Rhino 3D
2. Slicing Software: Slicing software converts 3D models into a series of 2D layers (slices) and generates the G-code, which are the instructions that the 3D printer understands to produce the object layer by layer. Slicing software allows users to adjust various print settings, such as layer height, print speed, infill density, and support structures. Common slicing software includes:
- Ultimaker Cura
- PrusaSlicer
- Simplify3D
- Slic3r
- MatterControl
3. Firmware and Printer Control Software: Firmware is the software installed on the 3D printer itself, controlling its operations and movements. Printer control software connects to the 3D printer and allows users to send G-code files for printing, control the printer settings, and monitor the printing process. Many 3D printers come with their own printer control software, and some slicers also have integrated printer control features.
4. Repair and Analysis Software: Repair and analysis software help identify and fix potential issues in 3D models, ensuring they are printable without errors. These tools can detect problems like non-manifold geometry, wall thickness issues, and gaps in the model. They are especially useful for ensuring the printability of models in complex or engineering-focused applications. Examples of such software include:
- Netfabb
- Meshmixer
- Autodesk Print Studio
5. CAD Software (Computer-Aided Design): CAD software is commonly used in industries like engineering and architecture to create precise technical drawings and models. While not always necessary for 3D printing, CAD software can be valuable for designing functional and precision parts. Many CAD software options overlap with 3D modeling software, and some popular CAD tools include SolidWorks, AutoCAD, and CATIA.
Depending on your specific needs and level of expertise, you may use a combination of these software types to take a 3D model from initial design to a printable file and control the 3D printing process. The software ecosystem for 3D printing is continuously evolving, with new tools and features being developed to enhance the design and printing experience.
3D printer post-processing requires steps such as removing support structures, removing unnecessary residues, sanding, and painting. These steps can be performed according to specific materials and needs.
Post-processing in 3D printing refers to the additional steps taken after the printing is complete to improve the appearance, functionality, and overall quality of the printed object. The specific post-processing techniques used can vary depending on the 3D printing technology and the type of material used. Here are some common post-processing methods in 3D printing:
1. Support Removal: For many 3D printing technologies, support structures are used to provide stability during printing. After printing, these supports need to be removed. The removal process can involve cutting, breaking, or dissolving the support material, leaving the final object clean and ready for use.
2. Sanding and Smoothing: Some 3D printed objects may have visible layer lines or rough surfaces. Sanding is a common post-processing method used to smooth the surface and reduce visible layering. Sanding can be done by hand or using power tools.
3. Painting and Coloring: Painting or applying a coat of color to 3D printed objects can enhance their appearance and make them more visually appealing. It allows for the customization of objects to match specific color schemes or design preferences.
4. Bonding and Assembly: In some cases, 3D printed objects may require multiple parts to be assembled together. Post-processing may involve bonding these parts using adhesives or mechanical fasteners to create a complete functional object.
5. Chemical Polishing or Vapor Smoothing: For certain 3D printing technologies like SLA and SLS, chemical polishing or vapor smoothing can be used to achieve a smooth, glossy surface finish. This process involves exposing the printed object to a solvent or vapor that chemically fuses the outer layer, reducing visible layer lines.
6. Curing: In resin-based 3D printing, printed objects may require curing under UV light to achieve their full mechanical properties and become fully solidified.
7. Mechanical Machining: For metal 3D printed objects, especially those produced through metal additive manufacturing technologies, post-processing can involve CNC machining or other traditional machining methods to achieve precise dimensions and surface finish.
8. Coating and Plating: Some 3D printed objects, especially those used in industrial or engineering applications, may benefit from additional coatings or plating to improve their mechanical properties or resistance to corrosion.
9. Heat Treatment: For certain materials like metals, heat treatment can be applied as a post-processing step to improve the material's strength, hardness, and other properties.
The choice of post-processing techniques depends on the intended use and desired finish of the 3D printed object. For functional parts or engineering applications, additional post-processing may be required to meet specific requirements. For decorative or artistic objects, post-processing can enhance the aesthetics and visual appeal.
3D printers need to be cleaned and maintained regularly, including cleaning nozzles, checking moving parts, replacing worn parts, etc.
Proper maintenance is essential to keep your 3D printer running smoothly and to ensure the longevity of its components. Regular maintenance can help prevent issues, improve print quality, and extend the life of the printer. Here are some essential tips for maintaining and caring for your 3D printer:
1. Keep the Printer Clean:
- Regularly clean the build platform or print bed to ensure proper adhesion of prints. Use isopropyl alcohol (IPA) or other appropriate cleaning agents to remove any residue.
- Clean the print nozzle (hotend) to prevent clogs and maintain accurate extrusion. This can be done using a specialized nozzle cleaning tool or a cold-pull technique.
- Keep the printer's exterior clean from dust and debris.
2. Lubrication:
- Some 3D printers may have moving parts that require lubrication. Refer to the printer's user manual for guidance on which parts need lubrication and how often it should be done.
3. Check and Tighten Hardware:
- Regularly inspect and tighten any loose screws, nuts, or bolts on the printer. Vibration during printing can cause components to become loose over time.
4. Level the Print Bed:
- Ensure the print bed is correctly leveled. A leveled bed helps in achieving good adhesion and print accuracy. Follow the printer's leveling procedure as recommended by the manufacturer.
5. Filament Storage:
- Store 3D printer filament in a cool and dry environment, away from direct sunlight and moisture. Proper storage helps prevent filament degradation and ensures consistent print quality.
6. Nozzle Temperature Calibration:
- Periodically calibrate the nozzle temperature using a thermometer or temperature measuring device. This ensures that the temperature displayed on the printer matches the actual temperature of the nozzle.
7. Regularly Update Firmware and Software:
- Stay up-to-date with the latest firmware and software updates for your 3D printer. Manufacturers often release updates to improve performance and fix bugs.
8. Check and Replace Consumables:
- Inspect and replace worn-out or damaged parts, such as the print bed surface (BuildTak, glass, etc.), belts, and fans, as needed. Over time, these components can wear out and affect print quality.
9. Keep the Printer in a Controlled Environment:
- Ensure the printer is located in a well-ventilated and dust-free area. Avoid exposure to extreme temperatures or humidity, which can affect the printer's performance.
10. Follow Maintenance Schedule:
- Refer to the printer's user manual for recommended maintenance schedules and follow them diligently.
By following these maintenance tips and taking good care of your 3D printer, you can enjoy consistent print quality, reduce downtime due to issues, and extend the life of your printer. Additionally, becoming familiar with your specific 3D printer's maintenance requirements and regularly performing maintenance tasks will help you become a more confident and efficient 3D printing enthusiast.
The printing speed of a 3D printer varies depending on factors such as model, printing material, and printing accuracy. Generally speaking, the printing speed is relatively slow, depending on the size and complexity of the printed item.
The printing speed of a 3D printer can vary significantly depending on several factors, including the type of 3D printing technology, the complexity of the object being printed, the layer height, and the printer's overall build quality. The speed at which a 3D printer operates is typically measured in millimeters per second (mm/s) or millimeters per minute (mm/min). Here is an overview of the typical printing speeds for different 3D printing technologies:
Fused Deposition Modeling (FDM) / Fused Filament Fabrication (FFF):
- FDM printers, which use thermoplastic filaments, have a wide range of printing speeds. Standard consumer-grade FDM printers can print at speeds of around 40-100 mm/s. Some high-quality FDM printers with optimized settings can reach speeds of up to 150 mm/s or more. However, printing at higher speeds may affect print quality and accuracy.
Stereolithography (SLA) and Digital Light Processing (DLP):
- SLA and DLP printers use liquid photopolymer resins cured by a UV light source. The printing speed for SLA/DLP printers is generally measured in layer cure time, which depends on the thickness of each layer. Standard speeds for SLA/DLP printers typically range from 30 to 100 seconds per layer.
Selective Laser Sintering (SLS) and Selective Laser Melting (SLM):
- SLS and SLM printers use high-powered lasers to sinter or melt powdered materials like nylon, metal, or ceramics. The printing speed for these technologies can vary significantly based on the material and layer thickness. SLS and SLM printers can achieve speeds of around 20-150 mm/s.
Digital Beam Melting (EBM):
- EBM is a metal 3D printing technology that uses an electron beam to melt metal powder. EBM printers are typically slower than other metal 3D printing methods, with speeds ranging from 5 to 30 mm/s.
It's important to note that higher printing speeds do not always translate to better results. Faster printing can lead to reduced surface quality, decreased precision, and increased risk of print failures, particularly for intricate or large objects. Print quality and speed are often a trade-off, and finding the right balance is essential for successful 3D printing.
In general, print speeds for consumer-grade 3D printers are more modest compared to industrial-grade printers. Industrial-grade 3D printers often have advanced features and capabilities that allow for faster printing while maintaining high print quality. However, print speed is just one aspect of a 3D printer's overall performance, and factors such as reliability, print accuracy, and material compatibility are equally important considerations when choosing a 3D printer for specific applications.
Common question in 3D Printing Production
The manufacturing materials of 3D printing technology include plastics, metals, ceramics, fibers, biomaterials, etc.
One of the most common materials used in 3D printing is thermoplastic filaments like PLA (polylactic acid) and ABS (acrylonitrile butadiene styrene). These materials are widely used in Fused Deposition Modeling (FDM) printers, which are popular among hobbyists and educators due to their ease of use and affordability.
Resin-based 3D printing technologies, such as Stereolithography (SLA) and Digital Light Processing (DLP), use liquid photopolymer resins. These resins are cured by UV light to create highly detailed and smooth objects, making them suitable for applications like jewelry design, dental models, and artistic creations.
In industrial settings, Selective Laser Sintering (SLS) and Selective Laser Melting (SLM) are used to print with powdered materials such as nylon, metal alloys (e.g., titanium, aluminum, stainless steel), ceramics, and glass. SLS and SLM enable the production of complex and robust parts, making them valuable in aerospace, automotive, and medical industries.
The future development trend of 3D printing technology includes faster, more accurate, larger-scale printing, the use of multiple materials, more application scenarios, and more sustainable materials.
The future development trend of 3D printing technology is poised to bring about significant advancements and transformative changes across various industries. As the technology continues to mature and evolve, several key trends are expected to shape its future trajectory:
1. Materials Innovation: One of the most critical areas of advancement in 3D printing technology is the development of new and improved materials. Researchers and manufacturers are actively exploring a wide range of materials, including biocompatible resins for medical applications, high-performance polymers for aerospace and automotive industries, and advanced metal alloys for industrial and engineering applications. The introduction of new materials with enhanced properties will expand the potential applications of 3D printing and enable the production of more complex and durable objects.
2. High-Speed Printing: Speed is a crucial factor in 3D printing, especially for large-scale production and industrial applications. Future developments are expected to focus on increasing the printing speed of various 3D printing technologies without compromising print quality. Innovations like parallel printing, continuous 3D printing, and faster curing processes for resin-based printers are being explored to improve throughput and efficiency.
3. Large-Scale 3D Printing: The ability to print larger objects and even architectural structures is an emerging trend in 3D printing. Innovations in gantry systems, robotic 3D printers, and the use of construction-grade materials are enabling the creation of buildings, infrastructure, and other large-scale components with 3D printing. Large-scale 3D printing has the potential to revolutionize the construction industry by reducing construction timelines, material waste, and labor costs.
4. Multi-Material and Multi-Color Printing: Future developments are expected to enable 3D printers to work with multiple materials and colors simultaneously. This capability will allow for the creation of more complex and functional objects with integrated electronics, embedded sensors, and enhanced aesthetics. Multi-material 3D printing will be especially valuable in applications like medical devices, consumer electronics, and automotive components.
5. Sustainability and Recycling: As environmental concerns grow, the 3D printing industry is focusing on sustainability. Researchers are exploring eco-friendly materials derived from renewable sources, as well as the development of more efficient recycling and reusing methods for 3D printing waste. Reducing material waste and energy consumption during the printing process will be critical for the long-term sustainability of the technology.
6. Bioprinting and Tissue Engineering: The field of bioprinting is advancing rapidly, with the potential to revolutionize medicine and healthcare. Bioprinting involves printing living cells and biomaterials to create artificial organs, tissues, and implants. The development of functional 3D-printed organs and tissues could address the global organ shortage and open new possibilities in regenerative medicine.
7. Integration with Industry 4.0 and AI: 3D printing is increasingly becoming a part of the Industry 4.0 revolution, which emphasizes the integration of digital technologies and automation in manufacturing. The combination of 3D printing with Artificial Intelligence (AI) and Internet of Things (IoT) technologies will enable autonomous and adaptive manufacturing processes, real-time monitoring, and predictive maintenance.
8. Democratization of 3D Printing: As the technology becomes more affordable and user-friendly, the democratization of 3D printing is expected to continue. 3D printers will become increasingly accessible to individuals, hobbyists, small businesses, and educational institutions. This democratization will foster creativity, innovation, and customization across various sectors.
In conclusion, the future development trend of 3D printing technology is characterized by innovation in materials, speed, scale, and application areas. As these trends converge, 3D printing is poised to play an even more significant role in various industries, revolutionizing manufacturing, healthcare, construction, and beyond. As research and investment continue to drive progress, the possibilities for 3D printing seem boundless, and the impact on society and the economy is expected to be profound.
The copyright protection of 3D printing technology can be realized through digital copyright technology, 3D printing file encryption, watermarking and other methods.
Realizing copyright protection for 3D printing technology involves taking various legal and technical measures to safeguard intellectual property rights and prevent unauthorized use or reproduction of copyrighted designs. Here are some strategies to achieve copyright protection for 3D printing technology:
1. Copyright Registration:
- Registering copyrights for the 3D printing technology, software, and design files with relevant intellectual property offices provides legal recognition and evidence of ownership. Copyright registration strengthens the legal standing to enforce copyright claims and seek damages in case of infringement.
2. Licensing and Terms of Use:
- Clearly define the terms of use and licensing agreements for the 3D printing technology and design files. License agreements can specify how the technology can be used, who can access it, and any limitations on reproduction or distribution. This helps prevent misuse and ensures that users understand their rights and obligations.
3. Watermarking and Digital Signatures:
- Applying digital watermarks or signatures to 3D printing files can help identify the creator and copyright holder. Watermarks make it harder for others to claim authorship or distribute copyrighted designs without permission.
4. Encryption and DRM (Digital Rights Management):
- Implementing encryption and digital rights management mechanisms can control access to design files and prevent unauthorized copying or sharing. DRM tools can restrict printing capabilities, limit the number of prints, or require user authentication for access.
5. Online Platforms and Ecosystem Control:
- If offering 3D printing services or design file repositories, maintain control over the platform and enforce terms of use. Monitor and moderate the content to detect and remove copyrighted materials shared without authorization.
6. Patent Protection for Novel Technology:
- If the 3D printing technology involves novel processes, machines, or materials, consider obtaining patents to protect these inventions from unauthorized use and commercialization.
7. Trade Secrets and Non-Disclosure Agreements (NDAs):
- For proprietary 3D printing technology or confidential information, use trade secrets and NDAs to protect sensitive data and technology from being disclosed or used by competitors or unauthorized parties.
8. Education and Awareness:
- Raise awareness about copyright protection and the importance of respecting intellectual property rights within the 3D printing community. Educate users and creators about copyright laws and the consequences of copyright infringement.
9. Monitoring and Enforcement:
- Regularly monitor the internet and marketplaces for unauthorized use or distribution of copyrighted 3D printing designs. Enforce copyright claims promptly by sending takedown notices, cease and desist letters, or pursuing legal action when necessary.
It is essential to seek advice from intellectual property lawyers and experts to ensure that all copyright protection measures align with the relevant laws and regulations in your jurisdiction. Copyright protection for 3D printing technology is a complex and evolving area, so staying informed about emerging legal challenges and best practices is crucial to maintain a strong defense of intellectual property rights.
Compared with traditional manufacturing processes, 3D printing technology has certain environmental advantages. It can reduce waste of raw materials, reduce energy consumption, and use resources more efficiently.
3D printing technology has the potential to be environmentally friendly, but its overall impact on the environment depends on various factors, including the materials used, the printing process, and the specific application. Here are some aspects to consider regarding the environmental friendliness of 3D printing:
1. Material Usage and Waste:
- The choice of printing materials significantly influences the environmental impact of 3D printing. Some 3D printing materials, such as biodegradable and recyclable thermoplastics like PLA, can be more eco-friendly than others. However, certain specialty materials, like resins used in SLA or powders used in SLS, may be more challenging to recycle or dispose of sustainably.
2. Material Waste Reduction:
- One of the advantages of 3D printing is that it can significantly reduce material waste compared to traditional manufacturing processes. 3D printing adds material only where it is needed, minimizing excess material and reducing waste.
3. Localized Production and Supply Chain Optimization:
- 3D printing enables localized production, allowing items to be printed on-demand closer to the point of use. This can reduce the need for extensive transportation and warehousing, leading to potential supply chain optimization and lower carbon emissions.
4. Energy Consumption:
- The energy consumption of 3D printing varies depending on the printer type and the printing process. Some 3D printing technologies, like FDM, generally consume less energy than others, such as metal 3D printing processes like SLM. Using energy-efficient printers and optimizing printing parameters can help reduce energy consumption.
5. Sustainable Materials Development:
- Ongoing research and development in the 3D printing industry are focused on creating more sustainable and eco-friendly materials. This includes exploring materials made from renewable resources and improving recycling and circular economy initiatives for 3D printing materials.
6. Hazardous Materials:
- Some 3D printing technologies use materials that can be hazardous to the environment or human health. For instance, certain resins or metal powders used in 3D printing may have toxic properties. Proper handling, disposal, and recycling of these materials are essential to minimize environmental impact.
7. End-of-Life Disposal:
- Like any manufacturing process, 3D printing results in end-of-life products that need to be disposed of responsibly. The recyclability and biodegradability of materials play a significant role in minimizing the environmental impact of 3D printed objects at the end of their life cycle.
Overall, 3D printing technology has the potential to be more environmentally friendly than traditional manufacturing processes, particularly when used thoughtfully with sustainable materials and practices. However, like any technology, its environmental impact is not uniform and must be carefully managed to maximize its eco-friendliness. As the industry continues to evolve, an increased focus on sustainable materials, energy efficiency, waste reduction, and responsible end-of-life practices will be essential to further enhance the environmental friendliness of 3D printing technology.
3D printing technology has certain security risks, for example, it can be used to manufacture dangerous items such as guns. In addition, if used improperly, 3D printers may also cause safety problems such as fire and electric shock.
there are security risks associated with 3D printing technology. As 3D printing becomes more accessible and widespread, certain security concerns have emerged that can impact various aspects of the technology and its applications. Some of the key security risks in 3D printing include:
1. Intellectual Property (IP) Theft:
- 3D printing enables the replication of physical objects from digital designs. This capability can be misused to violate intellectual property rights by copying and producing copyrighted or patented designs without permission. Counterfeiting of products and unauthorized reproduction of proprietary parts are potential issues.
2. Design and Blueprint Theft:
- The 3D printing process relies on digital design files. If these design files are not adequately protected, they can be vulnerable to theft or unauthorized access. This could lead to the unauthorized distribution or modification of designs, undermining the original creator's rights and potentially posing safety risks if design alterations are made.
3. Product Tampering and Counterfeiting:
- With 3D printing, it becomes easier to create replicas of objects, including consumer products, spare parts, and medical devices. This opens the door to potential product tampering and counterfeiting, which can have serious safety implications for consumers and industries.
4. Cybersecurity Vulnerabilities:
- 3D printers can be connected to computer networks for remote operation, which introduces potential cybersecurity risks. Vulnerabilities in the printer's firmware, software, or network communication could be exploited to gain unauthorized access to the printer, compromise print jobs, or launch cyberattacks.
5. Weapon and Harmful Object Production:
- 3D printing has raised concerns about the potential for individuals to produce weapons, dangerous objects, or prohibited items that can bypass traditional security measures. While the majority of 3D printing users have legitimate and responsible intentions, these risks must be addressed to prevent misuse.
6. Piracy and Unauthorized Distribution:
- Similar to other digital content, 3D models can be pirated and distributed without permission. Unauthorized sharing of premium designs or copyrighted content can lead to financial losses for designers and may discourage innovation.
7. Unintended Consequences:
- As 3D printing evolves, it may introduce new risks and security challenges that are not yet fully understood. For example, in some industries, 3D printing could pose risks related to product liability, quality control, or safety certification.
Addressing these security risks requires a multi-faceted approach involving legal measures, digital rights management, encryption, secure file sharing, authentication protocols, and cybersecurity best practices. Implementing secure design and printing practices, protecting intellectual property, and educating users about responsible 3D printing are crucial steps in mitigating security risks and ensuring the responsible use of this transformative technology. Additionally, collaboration between industry stakeholders, policymakers, and cybersecurity experts is essential to address emerging security challenges effectively.
3D printing technology can be applied to food manufacturing, such as making chocolate, candy, bread and other foods, but it requires the use of special printers and food-safe materials.
3D printing technology can be applied to food manufacturing, and it opens up exciting possibilities in the field of culinary arts and personalized nutrition. This innovative application of 3D printing is often referred to as "3D food printing."
1. Customized Food Creations: 3D food printing allows chefs and food manufacturers to create intricate and customized food designs that would be challenging or impossible to achieve using traditional cooking methods. It opens up a new realm of culinary artistry and presentation possibilities.
2. Personalized Nutrition: 3D food printing has the potential to revolutionize the way we approach nutrition. By analyzing individual dietary needs and health requirements, 3D food printers can create personalized meals with precise portions of nutrients, vitamins, and minerals, tailored to each person's specific needs.
3. Enhanced Aesthetics and Presentation: 3D food printers can produce visually stunning dishes with intricate shapes and patterns, making food presentation more artistic and appealing. This technology allows chefs to experiment with new textures and designs to elevate the dining experience.
4. Improved Food Safety: With 3D food printing, the production process can be tightly controlled, reducing the risk of contamination and foodborne illnesses. Ingredients can be stored in airtight cartridges, minimizing exposure to external factors.
5. Food Preservation and Waste Reduction: 3D food printing can utilize ingredients more efficiently, reducing food waste. The ability to create precise portions and designs helps minimize excess food that may otherwise go unused.
6. Specialized Dietary Requirements: 3D food printing can cater to specific dietary needs, such as gluten-free, vegan, or allergen-free options. The technology can produce alternative ingredients that mimic traditional foods, expanding culinary choices for individuals with dietary restrictions.
7. Space Exploration and Long-Term Missions: 3D food printing is being explored by space agencies like NASA as a potential solution for providing nutritious and palatable meals during long-duration space missions. The technology could enable astronauts to create food from raw materials on-demand, reducing the need for extensive food storage and supply.
8. Rapid Prototyping and Food Research: 3D food printing allows food scientists and researchers to rapidly prototype new food formulations and textures, accelerating the development of innovative food products.
9. Food Design and Education: 3D food printing can be a valuable educational tool, introducing students and consumers to the intersection of technology and culinary arts. It encourages exploration, creativity, and the integration of STEM (Science, Technology, Engineering, and Mathematics) concepts in the kitchen.
Despite its promising potential, 3D food printing is still in its early stages of development, and challenges remain. Fine-tuning the technology to work with a broader range of ingredients and textures, ensuring food safety, and scaling up production are areas that researchers and companies are actively working on. As the technology evolves and becomes more refined, 3D food printing has the potential to revolutionize food manufacturing and redefine how we approach cooking, nutrition, and dining experiences.
3D printing technology can be applied in the medical field, such as making human organs, orthotics, prosthetics and other medical devices, and can even be used for surgical simulation.
3D printing technology has found numerous applications in the medical field, revolutionizing various aspects of healthcare. This innovative use of 3D printing, often referred to as "3D bioprinting" and "medical 3D printing," has opened up new possibilities in patient care, surgical planning, medical education, and the development of personalized medical devices. Here are some key areas where 3D printing is making a significant impact in medicine:
1. Patient-Specific Medical Models: 3D printing allows the creation of highly accurate and patient-specific medical models, such as anatomical replicas of organs, bones, and vascular structures. These 3D-printed models help surgeons and medical professionals visualize complex anatomical features, plan intricate surgeries, and improve communication with patients and their families.
2. Surgical Planning and Training: Surgeons can use 3D-printed models to simulate surgeries and develop detailed surgical plans. This practice is particularly beneficial for complex and rare cases, allowing for better preoperative preparation and reducing the risk of complications. Additionally, medical students and residents can enhance their training using 3D-printed models as hands-on teaching tools.
3. Prosthetics and Orthotics: 3D printing is transforming the field of prosthetics and orthotics. Custom 3D-printed prosthetic limbs and orthotic devices can be designed to fit an individual's unique anatomy, resulting in better comfort, function, and aesthetics.
4. Implants and Medical Devices: 3D printing enables the fabrication of patient-specific implants, such as cranial implants, hip replacements, and spinal implants. Customized implants fit better, reduce the risk of complications, and improve patient outcomes.
5. Tissue Engineering and Regenerative Medicine: In the field of regenerative medicine, 3D bioprinting holds immense promise. Researchers are exploring the use of 3D bioprinters to create living tissues and organs by depositing layers of bioink containing living cells. This technology has the potential to revolutionize transplantation by providing a limitless supply of organs and tissues.
6. Drug Delivery Systems: 3D printing can be used to create personalized drug delivery systems, such as customized pill formulations tailored to an individual's specific dosage needs or drug combinations. This approach could improve patient adherence to medication regimens and optimize treatment outcomes.
7. Dental Applications: 3D printing is widely used in dentistry for creating dental models, aligners, crowns, bridges, and dentures. It streamlines dental procedures, reduces patient discomfort, and improves the accuracy of dental restorations.
8. Medical Instruments and Tools: 3D printing is employed to produce specialized medical instruments and tools that are not easily accessible through traditional manufacturing methods. This includes surgical guides, clamps, and jigs that enhance surgical precision and efficiency.
The integration of 3D printing technology in the medical field is continuously advancing as researchers and medical professionals explore new applications and materials. While the technology holds great promise, it also faces challenges such as regulatory approvals, standardization, and cost considerations. Nevertheless, 3D printing is poised to revolutionize healthcare by offering customized, cost-effective solutions and improving patient outcomes across a wide range of medical disciplines.
3D printing technology can be applied in the field of construction, such as making architectural models, building components, etc. In addition, 3D printing technology can also be used to print architectural molds and templates.
3D printing technology is increasingly being applied to the construction field, and it has the potential to revolutionize the way we build structures. 3D printing in construction, also known as "3D construction printing" or "contour crafting," offers several advantages and innovations that could transform the construction industry. Here are some key areas where 3D printing is making an impact in construction:
1. Faster and Cost-Effective Construction: 3D printing in construction can significantly reduce construction timelines and labor costs. Large-scale 3D printers can construct entire walls, floors, and even entire buildings in a fraction of the time compared to traditional construction methods.
2. Design Freedom and Complexity: 3D printing allows for intricate and complex architectural designs that would be challenging or impossible to achieve with conventional construction techniques. The technology enables architects and designers to create unique shapes and structures with greater design freedom.
3. Reduction of Material Waste: By using additive manufacturing techniques, 3D construction printing minimizes material waste. The technology adds material only where it is needed, reducing construction material consumption and promoting sustainability.
4. Customization and Personalization: 3D construction printing enables customization and personalization of building elements, making it easier to create tailored living spaces for individual needs and preferences.
5. Disaster Relief and Housing Solutions: 3D construction printing has the potential to address housing shortages and provide rapid disaster relief solutions. The technology can quickly create low-cost, durable, and reliable housing units in areas affected by natural disasters or facing housing crises.
6. Sustainable Construction: The use of eco-friendly materials in 3D printing, such as recycled concrete or bio-based materials, can contribute to sustainable construction practices, reducing the carbon footprint of buildings.
7. Precise Construction and Quality Control: 3D construction printing relies on precise digital models and automated processes, resulting in accurate and consistent building elements. This level of precision helps improve construction quality and reduces errors.
8. Construction in Challenging Environments: 3D construction printing can be employed in remote or harsh environments, where traditional construction methods may be difficult to implement. It offers a solution for building in places with limited access to materials or skilled labor.
While 3D construction printing shows significant promise, it is still a developing technology, and there are challenges to address, including regulatory approvals, standardization, and scalability. Additionally, integrating 3D printing into the construction industry requires collaboration among architects, engineers, contractors, and material suppliers to optimize the design and implementation process.
As the technology matures and becomes more widely adopted, 3D construction printing has the potential to reshape the construction industry by introducing new possibilities in design, sustainability, and efficiency. It holds the promise of transforming the way we build, making construction faster, more cost-effective, and more adaptable to diverse needs and environmental challenges.
3D printing technology can be applied to textile manufacturing, such as making clothing, shoes, bags, etc.
3D printing technology can be applied to textile manufacturing, and it is opening up innovative possibilities in the world of fashion and textiles. The application of 3D printing in this field is often referred to as "3D textile printing" or "3D printed textiles." This emerging technology is transforming the way textiles are designed, produced, and customized. Here are some key areas where 3D printing is making an impact in textile manufacturing:
1. Customization and Personalization: 3D textile printing enables designers to create custom-made textiles with intricate and unique patterns, textures, and structures. It allows for personalized fashion pieces and individualized garments tailored to specific customer preferences and needs.
2. Complex Textile Structures: 3D printing in textiles allows for the creation of complex structures and geometries that are difficult to achieve using traditional textile manufacturing methods. This technology opens up new possibilities in fashion design and architectural textiles.
3. Lightweight and Flexible Textiles: 3D printed textiles can be designed to be lightweight, flexible, and comfortable, offering new options for activewear, sportswear, and other performance-driven applications.
4. Sustainable Textile Production: 3D printing in textiles can contribute to sustainable fashion practices by reducing waste and optimizing material usage. The technology adds material only where it is needed, minimizing fabric waste.
5. Hybrid Textile Materials: 3D textile printing allows for the incorporation of multiple materials and fibers, creating hybrid textiles with a combination of different properties such as strength, flexibility, and breathability.
6. Rapid Prototyping and Design Iteration: 3D textile printing enables rapid prototyping and design iteration, allowing designers to experiment with various textile patterns and structures quickly and cost-effectively.
7. Textile Wearables and Smart Fabrics: Integrating electronics and sensors into 3D printed textiles can lead to the development of smart fabrics and wearable technology, such as clothing with embedded sensors or LEDs.
8. Fashion Design and Artistic Expression: 3D printing in textiles empowers designers to explore new avenues of artistic expression, creating avant-garde fashion pieces and statement textiles that push the boundaries of traditional textile design.
While 3D textile printing presents numerous opportunities, it is still an evolving technology, and certain challenges need to be addressed, including material properties, production scalability, and printing speed. Additionally, the integration of 3D printing into the textile industry requires collaboration between fashion designers, textile engineers, and material scientists to optimize the process and achieve desirable results.
As 3D textile printing technology continues to develop, it has the potential to transform the fashion and textile industries, offering new possibilities for customization, sustainability, and creativity. It will reshape the way we approach textile design and production, allowing for a more personalized and innovative fashion landscape.
3D printing technology can be applied in the field of art, such as making sculptures, artworks, etc.
3D printing technology has found extensive applications in the field of art and is transforming how artists create, conceptualize, and showcase their work. 3D printing in art offers new possibilities for artistic expression, experimentation, and the realization of intricate designs that may not be easily achievable using traditional art techniques. Here are some key areas where 3D printing is making an impact in the world of art:
1. Sculpture and 3D Artwork: 3D printing allows artists to create intricate sculptures and 3D artwork with precision and detail. Artists can bring their digital designs to life by 3D printing them in various materials, such as plastics, metals, and resins.
2. Prototyping and Model Making: Artists and designers use 3D printing to create prototypes and models for larger art installations and projects. It allows them to visualize their concepts in three dimensions before producing the final artwork.
3. Jewelry Design: 3D printing is revolutionizing the jewelry industry, enabling artists and jewelers to create custom and unique pieces with intricate details and personalized designs.
4. Mixed Media Art: 3D printing allows artists to combine traditional art materials with 3D-printed components, creating mixed media art that blends physical and digital elements.
5. Art Installations and Exhibitions: Artists are using 3D printing to create large-scale art installations and immersive exhibitions. 3D-printed elements can add interactivity and depth to the artwork.
6. Art Conservation and Replication: 3D scanning and printing technologies can be used for art conservation and replication, allowing artists and museums to create accurate replicas of delicate or rare artworks for display or study.
7. Functional Art and Design: Artists are exploring the creation of functional art objects using 3D printing, such as furniture, lighting fixtures, and decorative elements.
8. Collaborative Art Projects: 3D printing facilitates collaborative art projects, where artists from different disciplines can work together to combine traditional art forms with digital fabrication techniques.
9. Art Education and Outreach: 3D printing has become an essential tool in art education, providing students with hands-on experience in digital design and additive manufacturing. It introduces new possibilities and enhances creativity in the next generation of artists.
As 3D printing technology advances and becomes more accessible, it has democratized art creation, allowing artists to explore new avenues of expression and creativity. Artists can now bridge the gap between the physical and digital worlds, blurring the lines between art and technology. 3D printing is redefining the boundaries of traditional art, encouraging artists to push the limits of their imagination and bring previously unattainable ideas to life
The printing accuracy of 3D printing technology varies with printer models, printing materials and other factors. Generally speaking, 3D printers with higher accuracy can achieve an accuracy of 0.1 mm or less.
The printing accuracy of 3D printing technology can vary depending on several factors, including the type of 3D printing process, the printer's specifications, the materials used, and the complexity of the object being printed. Generally, the accuracy of 3D printing is measured in terms of layer height or resolution, which refers to the thickness of each layer that the printer can create.
Here is an overview of the typical printing accuracy for some common 3D printing technologies:
1. Fused Deposition Modeling (FDM) / Fused Filament Fabrication (FFF):
- FDM printers have relatively moderate printing accuracy. The layer height for standard consumer-grade FDM printers typically ranges from 0.1 to 0.3 millimeters (mm). Some high-quality FDM printers can achieve layer heights as low as 0.05 mm.
2. Stereolithography (SLA) and Digital Light Processing (DLP):
- SLA and DLP printers can achieve high printing accuracy and resolution. The layer height for SLA/DLP printers usually ranges from 0.025 to 0.1 mm, with some high-end machines capable of even finer resolutions.
3. Selective Laser Sintering (SLS) and Selective Laser Melting (SLM):
- SLS and SLM printers, commonly used for metal and industrial-grade 3D printing, offer excellent accuracy. The layer height in SLS and SLM typically ranges from 0.02 to 0.1 mm.
4. Digital Beam Melting (EBM):
- EBM printers, which use an electron beam to melt metal powder, can achieve high printing accuracy similar to SLS and SLM printers.
It's important to note that the printing accuracy is not the only factor determining the overall quality of a 3D printed object. Other factors, such as the printer's calibration, the design of the object, the properties of the material used, and the print settings, all contribute to the final result.
In addition to the layer height or resolution, the overall dimensional accuracy and precision of a 3D-printed object can also be influenced by factors like shrinkage, warping, and distortion during the printing and cooling processes. Post-processing techniques and careful calibration of the 3D printer can help improve the accuracy and overall quality of 3D printed objects.
The printing size of 3D printing technology varies with factors such as printer models and materials. The printing size of some 3D printers can reach several meters or larger, while others are limited to a size of a few centimeters.
there is a limit to the printing size of 3D printing technology, and it can vary depending on the type of 3D printing process and the specific 3D printer being used. The maximum printing size is determined by several factors, including the build volume of the 3D printer, the dimensions of the printer's gantry system or build platform, and the overall structural capabilities of the printer.
Here are some considerations related to the printing size limit for common 3D printing technologies:
1. Fused Deposition Modeling (FDM) / Fused Filament Fabrication (FFF):
- FDM printers come in various sizes, ranging from small desktop printers to large industrial machines. The build volume of FDM printers can typically range from around 100 mm x 100 mm x 100 mm (or smaller) for consumer-grade printers to several meters in each dimension for large industrial printers.
2. Stereolithography (SLA) and Digital Light Processing (DLP):
- SLA and DLP printers also have different build volumes, but they generally have a smaller build size compared to FDM printers. The build volume of SLA and DLP printers can range from around 50 mm x 50 mm x 50 mm to several hundred millimeters in each dimension.
3. Selective Laser Sintering (SLS) and Selective Laser Melting (SLM):
- SLS and SLM printers are commonly used for industrial applications, including large-scale manufacturing. The build volume of these printers can range from several tens of centimeters to more than a meter in each dimension.
4. Large-Scale 3D Printing:
- Some specialized 3D printers, such as gantry-based printers or robotic 3D printers, have been developed to print on a larger scale. These machines can create structures on the order of several meters in each dimension, making them suitable for building construction, architectural components, and other large-scale applications.
It's important to note that as the size of the 3D print increases, certain challenges may arise. Large-scale 3D printing can lead to longer printing times and may require additional considerations for structural stability, material properties, and print bed adhesion. Additionally, larger prints may be more susceptible to warping and other distortions during the printing process.
While 3D printing technology has made significant strides in offering a broad range of print sizes, there are practical limitations to consider. For extremely large objects, such as full-scale buildings or large industrial components, alternative construction methods like concrete casting or assembly of smaller printed modules may be more practical. However, as the technology evolves, the printing size limits are likely to continue expanding, opening up new possibilities for additive manufacturing in various industries.
The printing speed of 3D printing technology varies with factors such as printer model, printing material, and printing precision. Generally speaking, 3D printers with higher precision are slower, while 3D printers with lower precision are faster.
The printing speed of 3D printing technology can vary significantly depending on several factors, including the type of 3D printing process, the complexity of the object being printed, the layer height or resolution chosen, and the specific 3D printer's capabilities. Generally, 3D printing is known for being a layer-by-layer additive manufacturing process, which can take time to build up the final object.
Here's an overview of the typical printing speeds for some common 3D printing technologies:
1. Fused Deposition Modeling (FDM) / Fused Filament Fabrication (FFF):
- FDM printers are known for their relatively fast printing speeds, especially for larger and less complex objects. The printing speed for consumer-grade FDM printers can vary from around 40 to 150 millimeters per second (mm/s).
2. Stereolithography (SLA) and Digital Light Processing (DLP):
- SLA and DLP printers generally have a slower printing speed compared to FDM printers due to the curing process of liquid resins. The printing speed for SLA and DLP printers typically ranges from 20 to 100 mm/s.
3. Selective Laser Sintering (SLS) and Selective Laser Melting (SLM):
- SLS and SLM printers are industrial-grade 3D printers that use lasers to sinter or melt powdered materials. These printers tend to have slower printing speeds, usually ranging from 10 to 50 mm/s.
4. Large-Scale 3D Printing:
- Large-scale 3D printers, especially those used in construction or industrial applications, may have slower printing speeds due to the larger size of the objects being printed. The printing speed for large-scale 3D printers can vary widely, from a few millimeters per second to several centimeters per second.
It's important to note that printing speed is just one aspect of the overall 3D printing process. Faster printing speeds may lead to sacrifices in print quality or accuracy, while slower speeds may result in more precise and detailed prints. Additionally, some 3D printers offer adjustable printing speeds, allowing users to balance print speed and print quality based on their specific requirements.
The printing speed also depends on the specific settings chosen for a given print job. Higher layer heights or lower resolution settings may result in faster prints, while finer resolution and thinner layers may increase print time.
Overall, the printing speed of 3D printing technology is continually improving as new advancements are made in printer design, materials, and printing software. Faster print speeds and more efficient printing processes are likely to be developed in the future, further enhancing the capabilities and usability of 3D printing technology.
3D printing technology usually requires post-processing, such as removing support structures, sanding, painting, etc., to achieve a smoother and more beautiful effect.
in most cases, 3D printing technology does require post-processing after the printing process is complete. Post-processing refers to additional steps that are taken to refine, clean, and enhance the 3D printed object. The extent and type of post-processing required depend on the 3D printing technology used, the material printed, and the specific requirements of the final product. Some common post-processing steps include:
1. Removal of Support Structures: Many 3D printing technologies use support structures to ensure the stability of overhanging or complex features during the printing process. After printing, these support structures need to be removed carefully to avoid damaging the printed object. This process may involve cutting, sanding, or dissolving the support material, depending on the type of 3D printing technology used.
2. Surface Smoothing and Finishing: 3D printed objects may have visible layer lines or rough surfaces due to the layer-by-layer printing process. Post-processing techniques such as sanding, filing, or using chemical agents can be applied to smooth and refine the surface finish of the object.
3. Painting and Coloring: If the 3D printed object requires specific colors or finishes, post-processing steps such as painting, dyeing, or applying coatings can be used to achieve the desired appearance.
4. Assembling and Joining: In cases where 3D printed objects consist of multiple parts, post-processing may involve assembling and joining these parts together using various techniques such as gluing, welding, or mechanical fastening.
5. Curing and Heat Treatment: Certain 3D printing materials, such as resins used in SLA or DLP printing, may require post-curing under ultraviolet light to achieve their final mechanical properties.
6. Polishing and Surface Treatment: Post-processing may involve polishing, vapor smoothing, or surface treatment methods to improve the aesthetics and functionality of the printed object.
7. Inspection and Quality Control: After printing and post-processing, the 3D printed object may undergo inspection and quality control measures to ensure it meets the desired specifications and requirements.
The extent and complexity of post-processing will vary depending on the application and the level of finish required for the 3D printed object. While some 3D printing technologies, like FDM, may require more extensive post-processing due to visible layer lines, other technologies, such as SLA, can produce smoother surfaces with minimal post-processing.
Post-processing is an essential part of the 3D printing workflow to achieve the desired final result and optimize the functional and aesthetic qualities of the printed objects. As 3D printing technology advances, efforts are being made to streamline post-processing steps and develop more automated and integrated solutions to reduce the overall post-processing time and effort.
The printing file format of 3D printing technology includes STL, OBJ, PLY, AMF and other formats, among which STL is one of the most commonly used formats.
3D printing technology supports various file formats that contain the necessary information for a 3D printer to create a physical object layer by layer. These file formats are used to store the three-dimensional geometry and other relevant data required for the printing process. Some of the common 3D printing file formats include:
1. STL (Stereolithography): STL is one of the most widely used file formats in 3D printing. It represents the 3D geometry of an object as a collection of connected triangles, creating a mesh. While it is a simple and universal format, STL files do not contain information about color, material properties, or other details beyond the basic geometry.
2. OBJ (Wavefront Object): OBJ is another widely used 3D file format in 3D printing. It supports both geometry and material information. OBJ files can contain color and texture data, making them suitable for 3D printing projects that require visual and textural details.
3. AMF (Additive Manufacturing File Format): AMF is specifically designed for additive manufacturing processes, including 3D printing. It can represent both the geometry and material properties of an object. AMF files are more robust and versatile than STL files, allowing for a more accurate representation of complex geometries and color information.
4. 3MF (3D Manufacturing Format): 3MF is a modern 3D printing file format developed by the 3MF Consortium. It is designed to overcome some limitations of STL and facilitate a more efficient, reliable, and feature-rich workflow in 3D printing. 3MF files can include geometry, color, materials, and other important data.
5. STEP (Standard for the Exchange of Product Data): While not exclusive to 3D printing, STEP is a widely used format in the CAD (Computer-Aided Design) industry. STEP files store 3D geometry and can include detailed information about the object's structure and materials.
6. IGES (Initial Graphics Exchange Specification): IGES is another standard CAD file format that can be used for 3D printing. Like STEP, IGES files store 3D geometry and can be used to exchange data between different CAD software and 3D printing systems.
Each 3D printer and 3D printing software may have its preferred file format(s), but most 3D printers are compatible with STL files as a basic and widely supported format. Additionally, many modern 3D printers and slicer software can handle other formats like OBJ, AMF, 3MF, STEP, and IGES, providing users with more options for creating and preparing 3D models for 3D printing.