CNC Milling Services
Parts In As Soon As 5-Days, 3 & 5-Axis Milling & Turning Plastics, Composites, Metals. Wide Variety of Materials, Finishing Options & Scalability
CNC Milling Parts
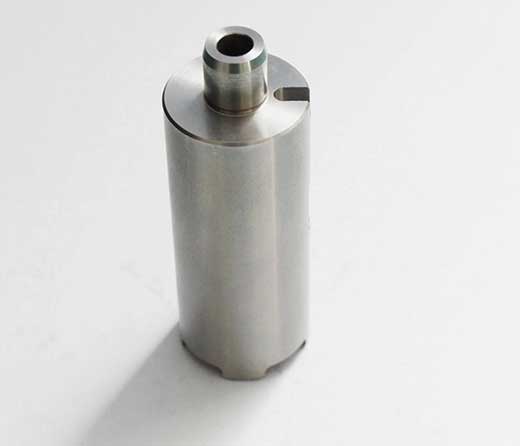
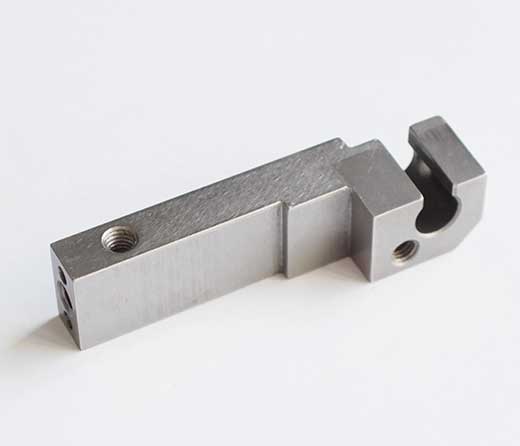
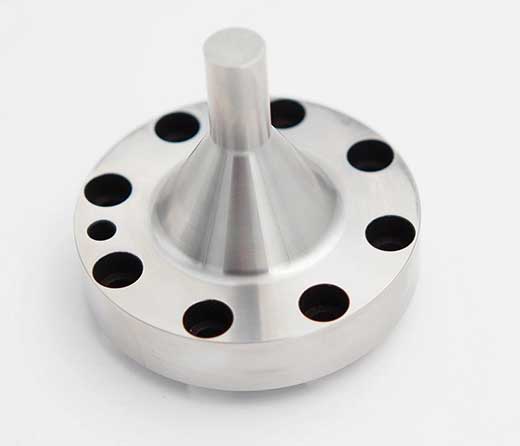
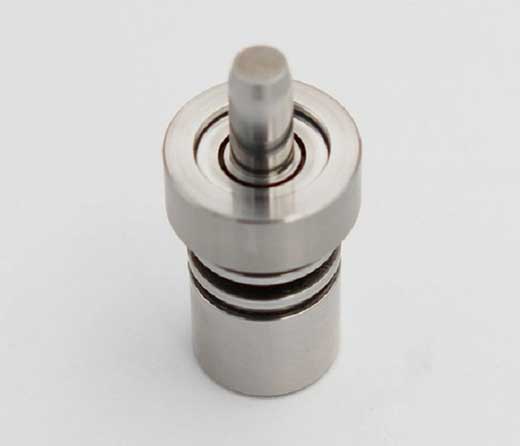
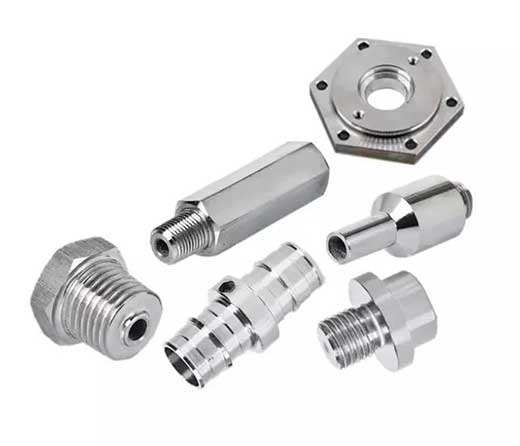
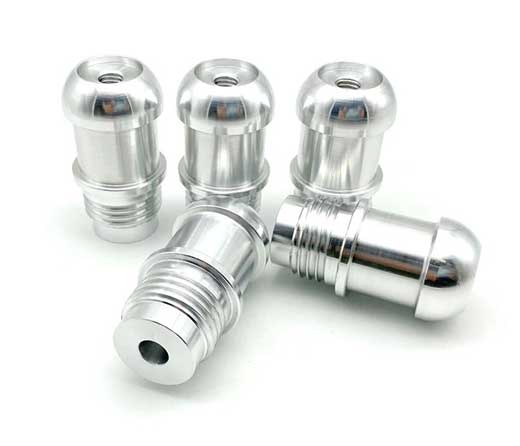
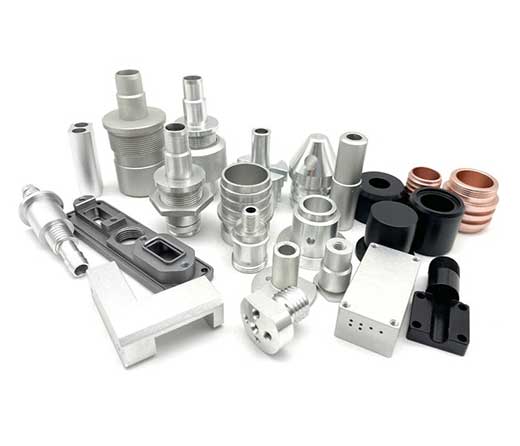
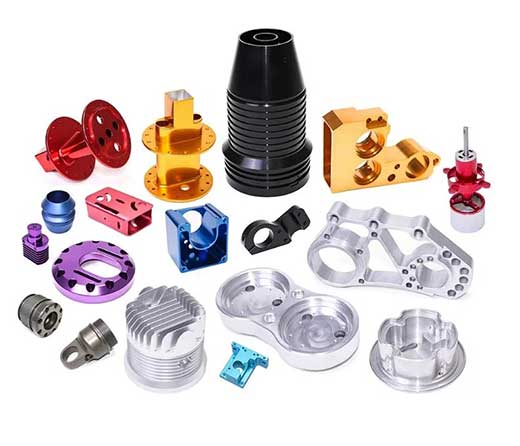
China CNC Milling Services
The CNC Milling process works by the machine reading coded instructions and then putting them into operation. It all starts with developing a 3D CAD file representing the final part. Once completed, the design is converted into a machine-readable format. CAM (Computer-Aided Manufacturing) software then exports this to a CNC machine program, usually in G-code format, which acts as the instructions, directing every move that the machine makes. This replicates the CAD design in the chosen material with high accuracy and efficiency.
Using subtractive machining technology, CNC Milling can produce high and low volumes of highly complex and intricate parts. Material is removed from a blank workpiece, and the milling machine uses a rotating cylindrical tool called a milling cutter. Depending on the milling machine being used, the machine can cut in different angles and move along different axes.
The final part will have first been designed via CAD, or Computer-Aided Design, before being inputted into the milling machine for final production.
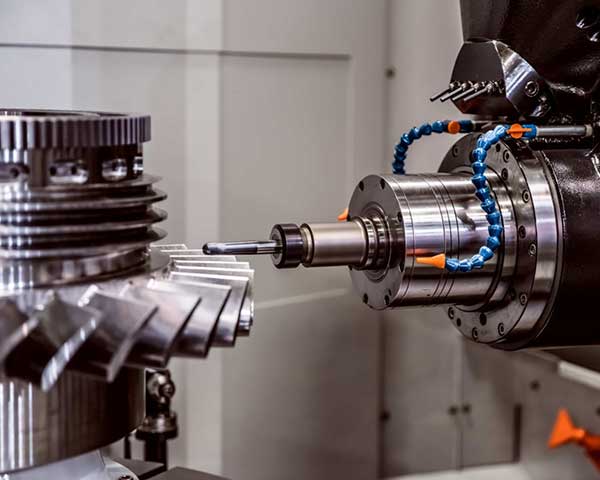
Types of CNC Milling
With vertical milling, a 3-axis milling table is the work surface, which sits below the arm, to which a spindle is attached.
The spindle can be stationary if a vertical turret mill is used. In this case, the table moved along both X and Y axes. Meanwhile, the table only moves along the X-axis if a bed vertical mill is used. The spindle travels along the length of the arm in the Y-Axis direction.
With horizontal milling, the spindle operates horizontally instead of vertically, and all other components are similar to vertical milling. Generally speaking, horizontal mills are best suited to heavier projects or longer projects. They are also suited to parts that require a large amount of material to be removed as the swarf falls away from the part and cutter.
The cutting tool’s axis of rotation is perpendicular to the surface of the workpiece.
It employs face milling cutters, with teeth both on the periphery and the tool face, the latter of which is used for finishing applications. Face milling is also used to create flat surfaces and control a finished piece. Face milling can produce higher quality finishes than other milling processes and is compatible with vertical and horizontal milling machines.
The cutting tool’s axis of rotation is parallel to the surface of the workpiece. Plain milling cutters have teeth on the periphery that perform the cutting operation. Both narrow and wide cutters are used. This allows for deeper cuts and for larger surface areas to be worked on. A course and fine-toothed cutter are both used. Slow cutting speeds and fast feed rates are used for the course cutter and vice versa for the fine-toothed cutter. This enables a more detailed final part.
This is a milling operation where the cutting tools’ axis of rotation is at an angle relative to the surface of the workpiece. Therefore, single angled milling cutters can produce more angular features, such as grooves, serrations, or chamfers.
Form milling is best used for milling operations where more irregular surfaces are involved. Contours, outlines, edges, or parts with curved, flat surfaces. It employed milling cutters or fly cutters specialised for particular applications – for example, concave cutters or corner rounding cutters. Hemispherical or semi-circular designs or other similarly intricate designs with complex parts would benefit from the form milling technique.
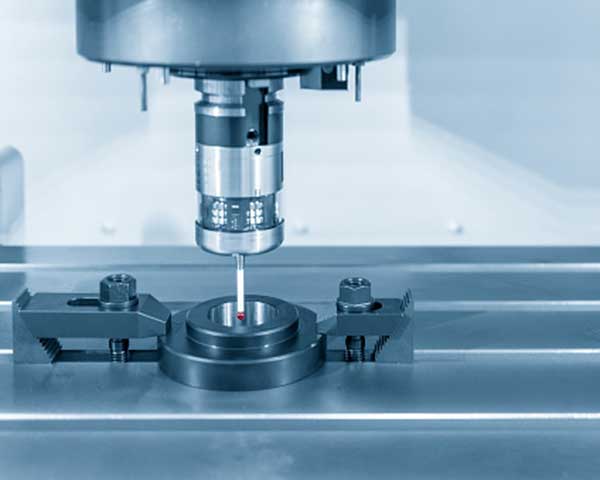
Benefits of CNC Milling process
- High quality and precision is guaranteed The very nature of CNC Machining as a process leaves very little room for error and high levels of accuracy and precision. This is because it operates from a computer led program, inputting 3D designs that have been developed via CAD (Computer-Aided Design). All operations are launched via a machine interface.The machine executes these instructions without the need for manual input. These automated processes allow for ultimate precision to ensure even the most finite and complex geometry can be technically managed.
- CNC Milling allows for high production output The level at which CNC Machines operate means they are capable of high levels of production due to the automated processes involved. CNC Milling is a trusted and popular option if a part needs to be produced in high volume, with every part meeting the same level of consistency in terms of quality and finish. It is particularly easy to program and operate a 3-axis machine, achieving high accuracy at a low cost.
CNC Milling Manufacturing FAQs
CNC Milling is an abbreviation for computer numerical control milling, which is a technology that controls milling machines through computer programs for automated processing. It uses a rotating tool to cut the surface of the workpiece to produce the desired shape and size.
CNC Milling, or Computer Numerical Control Milling, is an advanced manufacturing technology that offers many advantages. First of all, it is characterized by high precision, which means that the size and shape of the product can be precisely controlled during processing, thereby ensuring consistent product quality. Secondly, CNC Milling has the advantage of high efficiency. Through automated processing, it can greatly reduce the time and cost of manual operations and improve production efficiency. In addition, CNC Milling also has good repeatability, that is, when the same product is processed multiple times under the same conditions, the same processing results can be obtained, which is very beneficial for mass production.
In addition, CNC Milling also has stable processing accuracy. Due to the use of a computer control system, various parameters during the processing can be monitored and adjusted in real time to ensure the stability of the processing accuracy. In addition, CNC Milling can also perform mass production, which is suitable for manufacturing needs that require large quantities of the same product. At the same time, CNC Milling also has flexible processing technology, which can adjust and optimize the process according to different product requirements.
In addition to the above advantages, CNC Milling can also accelerate the process of product development and improvement. By using CAD/CAM software for programming and simulation, products can be simulated and verified during the design stage, thereby identifying and solving potential problems in advance. This not only improves the efficiency of product development, but also reduces development costs and risks.
To sum up, CNC Milling, as an advanced manufacturing technology, has the advantages of high precision, high efficiency, good repeatability, stable processing accuracy, mass production capacity and flexible processing technology. At the same time, by using CAD/CAM software for programming and simulation, the process of product development and improvement can be accelerated. Therefore, CNC Milling has been widely used and promoted in the manufacturing industry.
CNC Milling, the full name of Computer Numerical Control Milling, is an efficient technology widely used in processing various materials. This technology works not only on metals, but also on a variety of materials including plastics and wood. Its application range is very wide, including but not limited to aerospace, automobile manufacturing, medical equipment, electronic equipment, communications and other industries.
In the aerospace field, CNC Milling technology is used to manufacture various parts of aircraft, such as wings, fuselage, etc. These parts require high-precision and high-quality processing, and CNC Milling technology can meet these needs.
In the automobile manufacturing industry, CNC Milling technology also plays an important role. It is used to manufacture key components such as engine parts and body structures. Through CNC Milling technology, the accuracy and quality of automobile parts can be greatly improved, thereby improving the performance and safety of automobiles.
In the field of medical equipment manufacturing, CNC Milling technology is used to manufacture various precision medical equipment, such as surgical instruments, implants, etc. These equipment require high precision and stability, and CNC Milling technology can provide such processing capabilities.
In the electronic equipment manufacturing industry, CNC Milling technology is used to manufacture various precision electronic components, such as circuit boards, chips, etc. These components require high precision and consistency, and CNC Milling technology can meet these requirements.
In the communications industry, CNC Milling technology is used to manufacture various communications equipment, such as antennas, optical fibers, etc. These equipment require high precision and reliability, and CNC Milling technology can provide such processing capabilities.
Overall, CNC Milling technology has become an important tool in modern manufacturing due to its high precision, high efficiency and wide range of applications. No matter which industry you are in, as long as there are materials that require precision processing, CNC Milling technology can exert its unique advantages.
CNC Milling, also known as Computer Numerical Control Milling, is a precision machining technology that relies on two main pieces of equipment to complete its complex operations. First, we need a milling machine, which is the core equipment of CNC milling. A milling machine is a mechanical device that can perform precise cutting and engraving on a variety of materials. Its working principle is to cut the workpiece through a rotating tool to form the required shape and size.
Secondly, CNC milling also requires a computer control system. This system is the soul of CNC milling. It controls the movement of the milling machine and the position of the tool by receiving and processing instructions from the user or programming software. The computer control system can realize high-precision, high-efficiency and highly-automated milling operations, greatly improving production efficiency and product quality.
In addition to these two main equipment, CNC milling also requires some auxiliary equipment to ensure its normal operation and processing quality. For example, we need to use various types of milling cutters, which have different shapes and sizes to meet different cutting needs. In addition, we also need to use clamps to fix the workpiece to prevent it from moving or deforming during the cutting process. Tools are used to install and maintain milling cutters and other equipment. Finally, in order to protect the tool and workpiece from heat and friction damage generated during the cutting process, we also need to use coolant.
In general, CNC milling is a job that requires the cooperation of a variety of equipment and technologies. Each equipment has its own unique role and is indispensable.
There are many factors that need to be considered during the tool selection process. These factors include, but are not limited to, material, shape, size, and cutting performance. First, we need to choose materials with high hardness and good wear resistance, such as carbide and ceramics. These materials are able to withstand prolonged use, reducing wear and tear on the tool, thus extending its life.
Secondly, the shape and size of the tool also need to be selected according to the shape and size of the workpiece. This is because cutting results can only be ensured when the shape and size of the tool matches the workpiece. If the shape and size of the tool does not match the workpiece, it may result in uneven cuts and may even damage the workpiece.
Finally, the cutting performance of the tool also needs to be selected based on the characteristics of the workpiece material. Different workpiece materials have different hardness and toughness. Therefore, it is necessary to choose tools with corresponding cutting performance to obtain the best processing results. For example, for a harder workpiece material, you may want to choose a tool with a higher cutting speed and greater cutting force; while for a tougher workpiece material, you may want to choose a tool with a lower cutting force and a slower cutting speed. .
In general, tool selection is a process that requires comprehensive consideration of multiple factors. Only by fully understanding and considering these factors can we choose the most suitable tool and obtain the best processing results.
When considering tool life extension, we need to consider a variety of factors. These factors include, but are not limited to, tool material, shape, size, and cutting conditions. The service life of tools can be extended by using high-quality tool materials and tools with high machining accuracy. In addition, selecting appropriate cutting parameters, such as cutting speed, feed rate and cutting depth, can also effectively extend the service life of the tool.
First of all, the material of the tool is one of the important factors that affects its life. Different materials have different characteristics such as hardness, wear resistance and corrosion resistance, so choosing the right material is crucial to extending tool life. For example, for high-speed cutting applications, materials with good wear resistance and high-temperature stability can be selected to ensure that the tool can maintain good performance at high temperatures.
Secondly, the shape and size of the tool also affects its service life. Reasonable shape design can reduce cutting force and friction, thereby reducing tool wear. At the same time, appropriate size selection can ensure the fit between the tool and the workpiece, reduce unnecessary vibration and stress, and improve the stability and life of the tool.
In addition, cutting conditions are also one of the important factors affecting tool life. The selection of cutting speed, feed rate and cutting depth needs to be determined according to the specific processing requirements and workpiece material. Too high cutting speed and feed rate may cause tool overheating and increased wear, while too low cutting speed and feed rate may reduce processing efficiency. Therefore, reasonable selection of cutting parameters can improve the service life of the tool.
To sum up, to extend the service life of tools, we need to consider many factors such as the material, shape, size and cutting conditions of the tool. By selecting high-quality materials, reasonable shape design and size selection, and appropriate cutting parameters, we can effectively extend the service life of tools and improve production efficiency and economic benefits.
CNC Milling machining accuracy is a crucial aspect of the manufacturing process, and it is influenced by various factors that need to be carefully considered. These factors include tools, fixtures, workpiece materials, cutting parameters, and machine rigidity. Each of these elements plays a significant role in determining the overall accuracy of the CNC Milling process.
Firstly, the choice of tools is essential in ensuring precision during CNC Milling. The selection of appropriate tools depends on the specific requirements of the workpiece being processed. Different materials require different tool types, such as carbide or high-speed steel, to achieve optimal cutting performance. Additionally, the geometry and size of the tool must be compatible with the shape and size of the workpiece to ensure accurate machining.
Secondly, fixtures are used to hold the workpiece securely during the CNC Milling process. Properly designed fixtures prevent movement and vibration, which can adversely affect the accuracy of the machining operation. It is crucial to select fixtures that are specifically designed for the material and shape of the workpiece to ensure maximum stability and precision.
Furthermore, the choice of workpiece materials significantly impacts CNC Milling accuracy. Different materials have distinct properties, such as hardness, density, and thermal conductivity, that influence the cutting process. Understanding these properties is essential in selecting appropriate cutting parameters and tools to achieve optimal accuracy.
Cutting parameters, including cutting speed, feed rate, and depth of cut, also play a vital role in CNC Milling accuracy. These parameters must be carefully selected based on the specific requirements of the workpiece and the chosen tools. Incorrect parameter settings can result in poor surface finish, dimensional inaccuracies, or even damage to the workpiece.
Lastly, machine rigidity is another critical factor affecting CNC Milling accuracy. A rigid machine structure minimizes vibrations and ensures precise movement of the cutting tools. Machine rigidity can be improved by using high-quality machine components, proper alignment, and regular maintenance to ensure optimal performance throughout the machining process.
In conclusion, achieving accurate CNC Milling requires careful consideration of various factors, including tool selection, fixture design, workpiece material properties, cutting parameters, and machine rigidity. By selecting appropriate tools, fixtures, and processing parameters according to the shape, material, size, and processing requirements of different workpieces, manufacturers can ensure that their CNC Milling operations meet the required accuracy levels.
Cutting failure refers to the phenomenon that cutting tools break, wear or overheat during the processing process, which will have an impact on processing quality and efficiency. In order to avoid cutting failure, the following measures need to be taken: select appropriate tool materials and tool shapes; control cutting parameters such as cutting speed, feed rate, and depth of cut; strengthen cooling and lubrication of tools to reduce wear and heat accumulation; timely Replace damaged parts such as cutting tools and adjusting fixtures.
Failure of cutting tools is a common problem during machining. When cutting tools break, wear, or overheat, it will not only affect the processing quality, but also reduce the processing efficiency. Therefore, in order to avoid this situation from happening, we need to take some effective measures.
First, it is important to choose the right tool material and tool shape. Different materials require different tool materials to be processed to ensure that the tool can withstand the pressure and temperature during processing. In addition, the shape of the tool will also affect the cutting effect and stability. Therefore, when selecting a tool, it is necessary to determine the appropriate tool material and shape according to the specific processing requirements.
Secondly, controlling cutting parameters is also the key to avoiding cutting failure. Cutting speed, feed rate and cutting depth are important factors affecting the cutting effect. If these parameters are set incorrectly, excessive wear or overheating of the tool may occur, resulting in cutting failure. Therefore, before processing, these parameters need to be carefully considered and set appropriately to ensure the stability and efficiency of the cutting process.
In addition, strengthening the cooling and lubrication of cutting tools is also one of the important measures to prevent cutting failure. During the machining process, the tool will generate a large amount of heat. If the heat is not dissipated in time, it will cause the tool to overheat and accelerate wear. Therefore, measures need to be taken to enhance the cooling of the tool, such as using coolant or cooling devices to reduce the temperature of the tool. At the same time, lubrication is also essential, which can reduce the friction between the tool and the workpiece and extend the service life of the tool.
Finally, timely replacement of damaged parts is also an important step to avoid cutting failure. If tools or other parts are found to be damaged or severely worn, they should be replaced immediately. This ensures the stability and safety of the processing process and avoids cutting failures due to component damage.
To sum up, in order to avoid cutting failure, we need to choose the appropriate tool material and shape, control the cutting parameters, strengthen the cooling and lubrication of the tool, and replace damaged parts in a timely manner. By taking these measures, processing quality and efficiency can be improved, and the stability and safety of the processing process can be guaranteed.
During the programming process, we need to follow a series of steps. First, we need to determine the shape and size of the workpiece. This is a very important step because the shape and size of the workpiece will directly affect the tools and cutting parameters we choose.
Next, we need to choose the appropriate tool and cutting parameters. This step requires us to make a decision based on factors such as the material, hardness, and shape of the workpiece. We need to ensure that the selected tools and cutting parameters can effectively complete the cutting task, while also taking into account the efficiency and quality of the cut.
After determining the tool and cutting parameters, we need to plan the cutting path. The planning of the cutting path requires us to fully consider the shape, size and cutting parameters of the workpiece to ensure the smooth progress of the cutting process.
After planning the cutting path, we need to write a CNC program. CNC program is a program that controls the work of CNC machine tools. It needs to describe in detail the cutting path, the tools used, cutting parameters and other information.
After writing the CNC program, we need to simulate and debug it. Through simulation and debugging, we can check whether the CNC program is correct and whether the cutting task can be completed smoothly.
Finally, we need to upload the program to the milling machine and process it. During the processing, we need to pay close attention to the accuracy and stability of the program to avoid program errors and operational errors.
Overall, program design is a process that requires care and patience, and we need to be precise at every step to ensure that the final cutting result can meet our needs.
During operation and maintenance, we need to follow the following important precautions:
First of all, we need to be proficient in the operation methods and preventive measures of the milling machine. This includes understanding how a milling machine works, mastering the correct operating procedures, and understanding possible problems and how to deal with them. In this way, we can ensure that no errors will occur during operation and avoid unnecessary damage to the equipment.
Secondly, we need to pay attention to safety at all times to avoid accidents. This means we need to be vigilant during operations, follow all safety regulations, use appropriate protective equipment, and stop operations immediately and seek help if we encounter any problems.
In addition, we also need to regularly inspect and maintain milling machines and other tools to ensure the normal operation of the equipment. This includes cleaning equipment, replacing worn parts, and carrying out necessary repairs. In this way, we can ensure that the equipment is always in good working order, thereby increasing production efficiency.
At the same time, we also need to promptly clean up the waste materials and chips generated during the milling process. This not only avoids the impact of waste materials and chips on the working environment, but also prevents them from causing damage to the equipment.
Finally, we need to keep our working environment clean and tidy. This means we need to regularly clean the work area, discard discarded items, and keep the space around the equipment clear of obstructions.
At the same time, we also need to record processing data and fault information in a timely manner. This information can not only help us understand the operation of the equipment, but also provide us with a basis for subsequent work. For example, if we find that the equipment often fails of some kind, we can use this information to find the cause and take appropriate measures to solve the problem.
Common question in CNC Milling Production
CNC Milling processing is widely used in various fields of manufacturing industry, including aerospace, automobile, electronics, communication, medical equipment, mold and so on. In these fields, CNC Milling processing can realize high-precision, high-efficiency and high-stability processing to meet the requirements of different workpieces. For example, the aerospace field needs to process complex parts of high-strength and high-temperature-resistant materials; the automotive field needs to process auto parts with complex shapes; the electronics and communication fields need to process high-precision electronic components, etc.
In order to ensure the processing accuracy of CNC milling, we need to start from the following aspects: first, select appropriate tools, fixtures and processing parameters; second, reasonably arrange the processing sequence and path planning; third, perform pre-processing inspection and calibration; in addition, Replace damaged tools in time and adjust fixtures, etc.; at the same time, cool and lubricate cutting tools to reduce wear and heat accumulation; finally, use high-precision control systems and measuring instruments.
While implementing these measures, we also need to strengthen the skills training and quality awareness of employees to ensure operating standards and stable quality. Through the implementation of these comprehensive measures, we can effectively improve the processing accuracy of CNC milling, thereby ensuring product quality and performance.
Compared with traditional milling machines, CNC milling has the following significant advantages: First, it has a high degree of processing accuracy and can achieve high-precision, high-efficiency and high-stability processing. This high-precision processing capability makes CNC milling widely applicable in many precision manufacturing fields. Secondly, CNC milling is highly adaptable and can handle workpieces of various complex shapes and materials. Whether it is metal, plastic or composite materials, CNC milling can easily handle it, providing great convenience to the manufacturing industry.
In addition, CNC milling also features high production efficiency and can achieve automated and continuous production. By writing programs to control the movement of machine tools, CNC milling can greatly improve production efficiency and reduce the possibility of manual operations and human errors. This not only helps reduce production costs but also improves product quality and consistency.
Fourth, CNC milling is easy to operate, and the machine tool can be controlled by writing programs. This programmed operation method not only reduces the skill requirements for operators, but also reduces the risk of production accidents caused by human operating errors. At the same time, CNC milling can also be simulated and simulated through computer-aided design (CAD) software to discover and solve potential problems before formal processing.
Finally, CNC milling is highly reliable. Through real-time monitoring and feedback mechanisms, CNC milling can detect and eliminate faults in time to ensure the stability and quality of production. This high degree of reliability has made CNC milling widely used in many key areas, such as aerospace, automotive manufacturing and medical devices.
To sum up, CNC milling has become an important tool in modern manufacturing due to its advantages of high precision, strong adaptability, high production efficiency, easy operation and high reliability. With the continuous development and innovation of technology, CNC milling will play a greater role in more fields in the future, promoting the progress and development of the manufacturing industry.
When selecting the appropriate tool, several factors need to be considered: the material and shape of the workpiece; cutting conditions, such as cutting speed, feed rate, and depth of cut; the material and shape of the tool; machining quality requirements; and economy. In the process of selecting tools, the appropriate tool material and shape must be selected according to the characteristics of the workpiece and processing needs to ensure processing quality and efficiency.
First, we need to pay attention to the material and shape of the workpiece. Different materials have different hardness, toughness and thermal conductivity properties, so you need to choose a tool suitable for that material. For example, for materials with higher hardness, we may need to choose more wear-resistant tool materials to ensure the service life and cutting effect of the tool. In addition, the shape of the workpiece will also affect the choice of tool. For example, for workpieces with complex curved surfaces or many grooves, we may need to choose a tool with a specific shape to better adapt to the shape of the workpiece and achieve precise cutting.
Secondly, cutting conditions are also one of the important considerations in tool selection. Cutting speed, feed rate and depth of cut will directly affect the efficiency and quality of the machining process. For example, too high a cutting speed may lead to tool overheating and increased wear, thereby reducing processing quality; while too low a cutting speed may result in low processing efficiency. Therefore, when selecting tools, we need to determine the appropriate cutting conditions based on the material properties and processing requirements of the workpiece.
Furthermore, the material and shape of the tool are also key factors affecting the processing quality and efficiency. The selection of tool materials should take into account its wear resistance, hardness, corrosion resistance and other properties to ensure that the tool can maintain good cutting performance during the machining process. At the same time, the shape of the tool also needs to match the shape of the workpiece to achieve precise cutting and efficient processing.
In addition, machining quality requirements are also important factors to consider when selecting tools. Different processing tasks may have different requirements for processing quality. For example, for the processing of some precision parts, we need to choose tools with higher precision to ensure that the processed parts meet the design requirements. For some parts with low roughness requirements, we can choose tools with lower precision but lower cost.
Finally, economics is also an aspect to consider when choosing a tool. On the premise of meeting the processing quality and efficiency, we also need to consider the cost of the tool. Choosing tools with higher cost performance can reduce production costs and improve the competitiveness of enterprises.
To sum up, when selecting appropriate tools, we need to comprehensively consider multiple factors such as the material and shape of the workpiece, cutting conditions, tool material and shape, processing quality requirements, and economy. By rationally selecting tools, we can ensure the quality and efficiency of the processing process, thereby improving production efficiency and corporate competitiveness.
In order to ensure the surface quality of the workpiece, we need to start from the following aspects: first, select the appropriate tool and cutting parameters; second, control the machining accuracy and stability; then, strengthen the cooling and lubrication of the tool to reduce heat accumulation and wear ; In addition, it is necessary to control vibration and resonance during the machining process; then, select appropriate tool paths and tool compensation; finally, replace damaged tools in time and adjust fixtures, etc. At the same time, according to the characteristics and processing requirements of the workpiece, different processing methods and processes are used to achieve different surface quality requirements.
In the process of ensuring the surface quality of the workpiece, we must first pay attention to the selection of tools and the setting of cutting parameters. Suitable cutting tools can effectively complete cutting tasks, and reasonable cutting parameters can ensure the stability and efficiency of the machining process. Therefore, when selecting tools, we must fully consider factors such as the material, shape, and size of the workpiece to ensure that the performance of the tool can meet the processing requirements. At the same time, when setting cutting parameters, we must comprehensively consider factors such as the material characteristics of the workpiece, cutting speed, and feed rate to ensure the stability and efficiency of the processing process.
During the processing, we also need to pay close attention to the control of processing accuracy and stability. Through precise measurement and adjustment, we can ensure that the dimensional accuracy and shape accuracy of the workpiece meet the expected requirements. In addition, in order to ensure the stability of the machining process, we also need to perform regular maintenance and inspections on the machine tools to ensure that the performance of the machine tools is always maintained at its best.
In order to reduce tool wear and heat accumulation, we need to strengthen the cooling and lubrication of the tool. Through effective cooling and lubrication measures, we can reduce the temperature of the tool, thereby reducing tool wear and heat accumulation. At the same time, cooling and lubrication can also improve the efficiency of the machining process and extend the service life of the tool.
During processing, we also need to pay attention to controlling vibration and resonance. Vibration and resonance will lead to an increase in machining errors and affect the surface quality of the workpiece. Therefore, we need to take effective measures to reduce the effects of vibration and resonance, such as using vibration absorbers, optimizing tool paths, etc.
In addition, selecting appropriate tool paths and tool compensation are also key to ensuring the surface quality of the workpiece. Through reasonable tool path planning, we can reduce the idle stroke of the tool during processing and improve processing efficiency. At the same time, through reasonable tool compensation settings, we can eliminate processing errors caused by tool wear and other reasons, and ensure the dimensional accuracy and shape accuracy of the workpiece.
During the processing process, we also need to replace damaged tools and adjust fixtures in time. Damaged tools can affect machining quality and efficiency, while ill-fitting or worn fixtures can cause workpiece positioning errors. Therefore, we must regularly check the use of cutting tools. Once damaged or severely worn tools are found, they must be replaced in time. At the same time, we also need to regularly check the use of the clamps and make adjustments as necessary.
Finally, according to the characteristics and processing requirements of the workpiece, we need to use different processing methods and processes to achieve different surface quality requirements. For example, for some high-strength and high-hardness materials, we can use grinding, electrochemical processing and other methods to improve the surface quality of the workpiece; and for some precision parts, we can use high-precision processing methods such as CNC machining and laser processing. to meet its surface quality requirements. In short, through the comprehensive use of various processing methods and processes, we can optimize and improve the surface quality of the workpiece.
In order to prevent workpiece deformation, we need to start from the following aspects: First, select the appropriate workpiece material and processing method. Different workpiece materials have different characteristics and processing requirements, so selecting appropriate materials and processing methods is crucial to prevent workpiece deformation. Secondly, control the cutting conditions and cutting depth. Cutting conditions and cutting depth directly affect the dimensional accuracy and surface quality of the workpiece, so reasonable control needs to be carried out according to the requirements of the workpiece.
Third, use appropriate fixtures and processing sequences. The selection and use of fixtures is very important to maintain the stability of the workpiece and prevent deformation. At the same time, reasonable arrangement of the processing sequence can also reduce the stress and deformation of the workpiece during processing. Fourth, carry out appropriate cutting allowance and relaxation processing. The size of the cutting allowance and the way it is relaxed will have an impact on the dimensional accuracy of the workpiece, so reasonable control is required.
Fifth, control tool cooling and lubrication to reduce heat accumulation and wear. The cooling and lubrication of cutting tools can lower the temperature of the cutting tools, reduce heat accumulation and wear, thereby ensuring the processing quality of the workpiece and the service life of the cutting tools. Finally, strengthen the inspection and calibration of workpieces. Before processing, strict inspection and calibration of the workpiece to ensure that it meets the requirements can reduce errors and deformation during processing.
At the same time, it is also necessary to strengthen the skills training and quality awareness of employees. Only employees with good skill levels and quality awareness can ensure the standardization of operations and the stability of quality. By strengthening skills training and cultivating quality awareness, the professional quality and work efficiency of employees can be improved, thereby better preventing workpiece deformation and ensuring processing quality and production efficiency.
Tool maintenance and replacement are important links in ensuring CNC milling quality and efficiency. Tool maintenance includes regular cleaning, oiling, and checking for wear, as well as grinding and calibrating the edges of the tools. When changing tools, it is necessary to select appropriate tool shapes and materials according to different workpiece materials and shapes, and select appropriate cutting parameters according to processing requirements and cutting conditions. When changing tools, tool compensation and tool calibration are required to ensure machining accuracy and stability. At the same time, the service life and replacement cycle of tools need to be reasonably arranged to extend the service life of tools and reduce production costs.
In order to ensure the quality and efficiency of CNC milling, tool maintenance and replacement is a crucial link. First of all, it is necessary to regularly clean, oil and check the degree of wear of the tools. This keeps the tool in good condition and reduces the chance of failure. In addition, grinding and calibrating the edges of the tool are steps that cannot be ignored. Through grinding and calibration, the cutting effect of the tool can be ensured to be more precise and stable.
When it's time to replace tools, it's important to choose the right tool shape and material. Different workpiece materials and shapes require the use of corresponding tools for processing. Therefore, when selecting tools, comprehensive considerations must be made based on the specific situation. At the same time, it is also essential to select appropriate cutting parameters according to processing requirements and cutting conditions. This ensures that the tools can perform optimally during processing and improve production efficiency.
When changing tools, you also need to pay attention to the issues of tool compensation and tool calibration. These operations ensure the accuracy and stability of processing. Through reasonable tool compensation and calibration, processing problems caused by tool errors can be avoided and product quality and consistency can be improved.
In addition to the above operations, it is also crucial to reasonably arrange the service life and replacement cycle of the tools. By properly planning the use time of the tools, the service life of the tools can be extended and the number of frequent tool replacements can be reduced. This can not only improve production efficiency, but also reduce production costs. Therefore, when performing tool maintenance and replacement, the service life and replacement cycle must be fully considered.
In summary, tool maintenance and replacement have an important impact on the quality and efficiency of CNC milling. Keep your tools in good condition by regularly cleaning, oiling, checking for wear, grinding and aligning edges. When changing tools, select the appropriate shape and material, and select appropriate cutting parameters according to the processing requirements and cutting conditions. At the same time, tool compensation and calibration are performed to ensure the accuracy and stability of processing. Finally, rationally arranging the service life and replacement cycle of tools can extend the service life of tools and reduce production costs.
Processing quality inspection is an important means to ensure the quality of CNC milling processing. In order to ensure processing quality, processing quality inspection can be carried out in various ways, such as visual inspection, three-dimensional coordinate measurement, surface roughness inspection, hardness measurement, material composition analysis, etc. When conducting processing quality inspection, it is necessary to select appropriate testing methods and equipment based on the characteristics of the workpiece and processing requirements, formulate testing standards and methods, and record and analyze testing data. At the same time, it is also necessary to strengthen the quality awareness and skills training of employees to ensure operational specifications and stable quality.
In processing quality inspection, visual inspection is a commonly used method to determine whether the workpiece meets the requirements by observing the appearance and surface condition. Three-coordinate measurement is a high-precision measurement method that can accurately measure the size, shape and position of workpieces. Surface roughness inspection is used to evaluate the smoothness of the workpiece surface, which is especially important for some workpieces that require high smoothness. Hardness measurement can determine the hardness of the workpiece material to determine whether it meets the usage requirements. Material composition analysis can determine the composition proportion of the workpiece material to ensure that it meets the design requirements.
When performing processing quality inspection, it is necessary to select appropriate testing methods and equipment based on the characteristics of the workpiece and processing requirements. Different workpieces may require different inspection methods and equipment, so the selection needs to be based on the actual situation. At the same time, corresponding testing standards and methods need to be developed to ensure the accuracy and reliability of testing results. During the inspection process, inspection data needs to be recorded and analyzed so that problems can be discovered in a timely manner and corresponding measures can be taken for improvement.
In addition to selecting appropriate testing methods and equipment, it is also necessary to strengthen employee quality awareness and skills training. Only with good quality awareness and skilled skills can employees perform standardized operations and ensure the stability of processing quality. Therefore, companies should strengthen training and education for employees to improve their quality awareness and skill levels.
In short, processing quality inspection is an important part of ensuring the quality of CNC milling processing. By selecting appropriate testing methods and equipment, formulating testing standards and methods, and strengthening employee quality awareness and skill training, the stability and reliability of processing quality can be effectively improved. This is of great significance for ensuring product quality and corporate competitiveness.
Ensuring machining safety is an important task in CNC milling. In order to ensure processing safety, we need to start from the following aspects: first, establish a complete safety management system and rules and regulations; second, strengthen employees' safety awareness and skills training; third, strictly implement operating procedures and safe operating procedures; third, Fourth, keep equipment and facilities in good condition and perform regular maintenance; fifth, take effective safety protection measures against equipment failures and potential safety hazards, such as protective covers, safety switches, emergency shutdown devices, etc.; sixth, conduct regular maintenance Safety inspections and assessments to ensure a safe environment at the processing site. At the same time, we also need to strengthen safety awareness and safety culture construction to create a good safety atmosphere.
During the CNC milling process, it is crucial to ensure machining safety. In order to achieve this goal, we need to start from many aspects. First of all, establishing a sound safety management system and rules and regulations is the foundation. These systems and regulations should cover all aspects related to processing safety, including employee codes of conduct, equipment operating procedures, emergency plans, etc. By establishing such a system, we can provide a clear guidance framework for the processing process.
Secondly, strengthening employees’ safety awareness and skills training is key. Employees are the most important participants in the processing process, and their safety awareness and skill levels directly affect the safety of the entire processing process. Therefore, we should organize safety training regularly to improve employees’ safety awareness and teach them the necessary safe operation skills.
Third, strict implementation of operating procedures and safe operating procedures is an important part of ensuring processing safety. Operating procedures and safe operating procedures are scientifically proven and can minimize the occurrence of accidents. Therefore, we must require our employees to strictly abide by these regulations and not change or ignore them without authorization.
Fourth, keeping equipment and facilities in good condition and performing regular maintenance is the basis for ensuring processing safety. The proper operation of equipment and facilities is critical to the safety of the processing process. Therefore, we should regularly inspect and maintain the equipment, discover and solve potential problems in a timely manner, and ensure that the equipment is always in good working order.
Fifth, it is necessary to take effective safety protection measures against equipment failures and potential safety hazards. For example, we can use protective covers to protect employees from splashing objects, use safety switches to prevent equipment from accidentally starting, use emergency stop devices to quickly stop the operation of equipment, etc. These measures can effectively reduce the occurrence of accidents.
Sixth, regular safety inspections and assessments are important means to ensure a safe environment at the processing site. Through regular safety inspections and assessments, we can promptly discover and resolve potential safety issues to ensure that the processing site is always in a safe working environment.
Finally, strengthening safety awareness and building safety culture is the key to creating a good safety atmosphere. We should continuously strengthen employees' safety awareness through various channels, such as publicity, training, rewards and punishments, etc., so that they always keep the principle of safety first in mind. At the same time, we should also advocate a positive safety culture so that employees can consciously abide by safety regulations and jointly create a safe working environment.
To sum up, ensuring the safety of machining is a complex and important task. Only by starting from multiple aspects, comprehensively strengthen safety management and training, strictly implement operating procedures and safe operating procedures, maintain equipment and facilities in good condition and perform regular maintenance, take effective safety protection measures, conduct regular safety inspections and assessments, and strengthen Safety awareness and safety culture construction can ensure that the processing process in CNC milling is always in a safe working environment.