Fused Deposition Modeling (FDM) 3D Printing
FDM Parts In As Soon As Next-Day; Functional Parts: Prototyping, Production & Tooling; Material Options From Rigid To Flexible.
FDM 3D Printing Parts
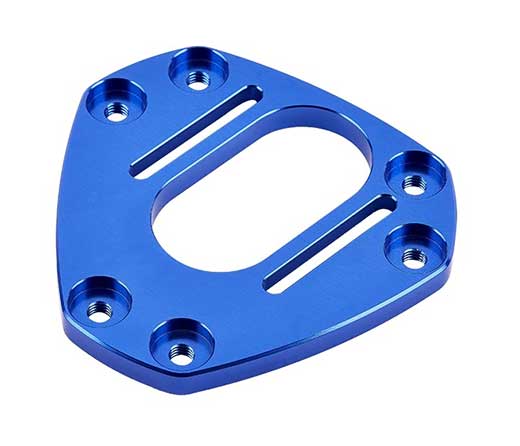
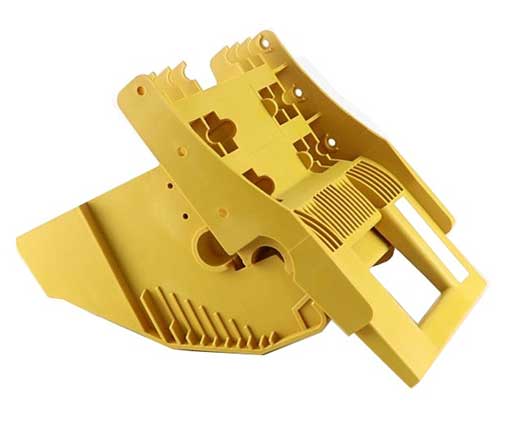
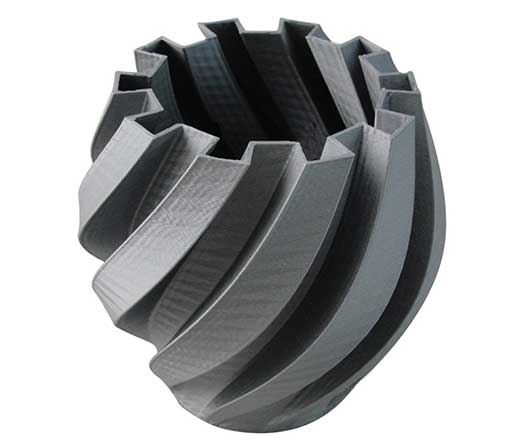
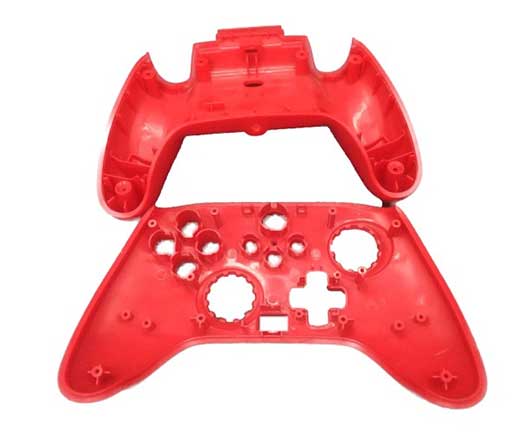
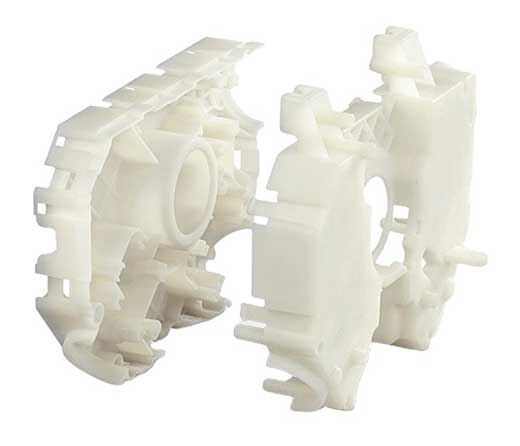
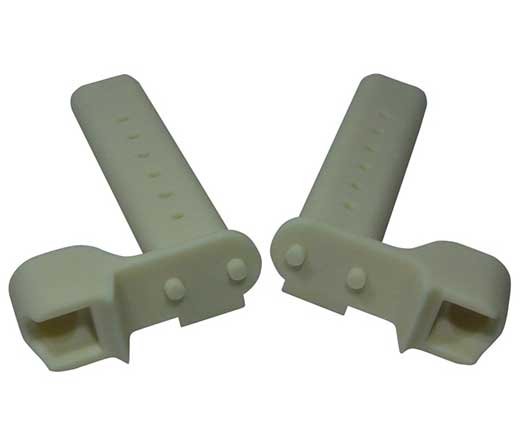
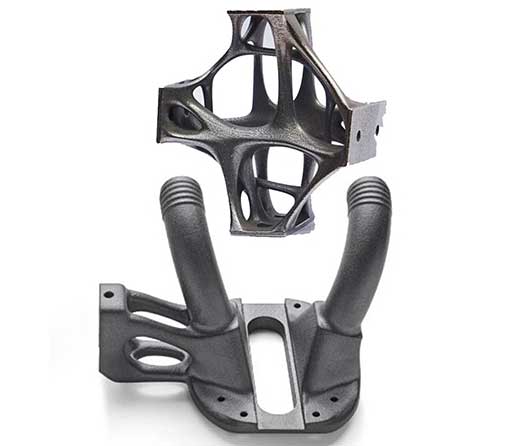
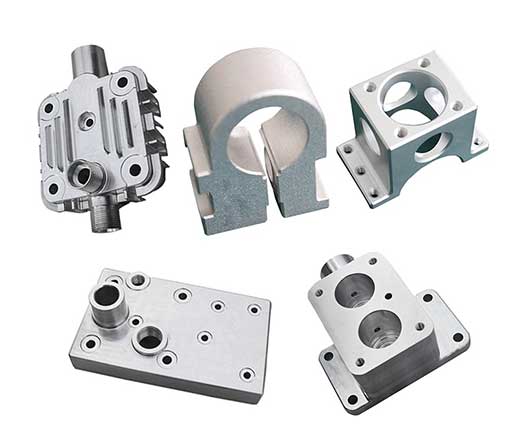
Fused Deposition Modeling (FDM) 3D Printing services
The FDM process begins when a computer-aided design (CAD) design is made. The CAD file acts as a set of instructions or blueprints for the machine. An FDM printer will use two types of materials—one for modeling and the other for support. Once the printing begins, filaments are unwound from a coil and fed into an extrusion nozzle. The nozzle is heated to melt the material and can be moved in horizontal and vertical directions, controlled by computer-aided manufacturing (CAM) software package. The model or part is produced by extruding small beads of thermoplastic material to form successive layers, with each material layer hardening immediately after extrusion from the nozzle. Once the piece is made, the support structures must be removed by force or solution. The size and complexity of the part design will impact the amount of time it will take to complete the build process.
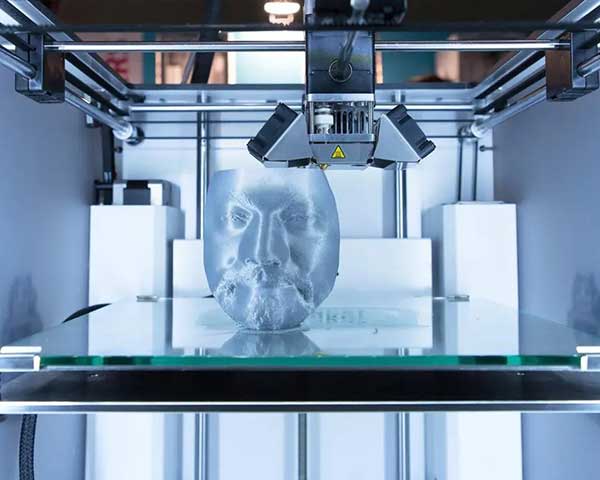
What Industries use FDM 3D Printing?
Startups and large aerospace companies have all used Fused Deposition Modeling to produce their products. FDM parts are durable, chemical resistant and can endure extreme conditions, making them ideal for testing and end-use parts. As FDM technology continues to advance, more and more industries have adopted the technology,
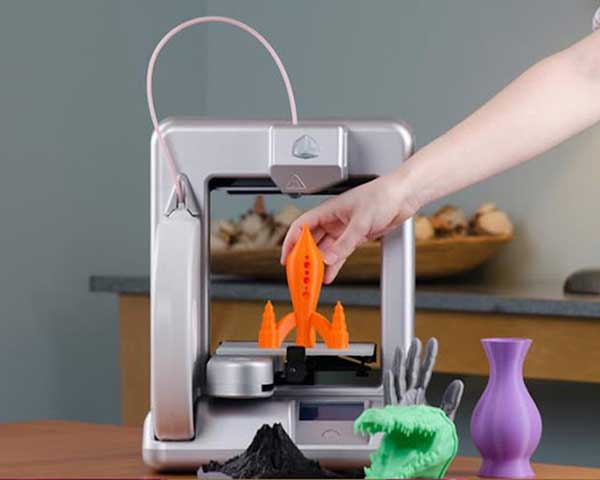
What are the Advantages of FDM 3D Printing?
There are many advantages to FDM 3D printing. One main benefit of FDM technology is its ability to produce parts and prototypes using engineering grade plastics. FDM thermoplastic parts are strong, durable and are dimensionally stable. FDM parts can be used for advanced conceptual models, functional prototyping, production parts and manufacturing tools.
Modern FDM 3D printing machines possess large build envelopes capable of producing larger pieces at higher quantities than other additive manufacturing technologies. Today’s FDM printers are so efficient that they can eliminate many of the steps necessary with traditional manufacturing. As a result, overhead costs are reduced and there is a quicker turnaround. Brands often select FDM technology due to the wide selection and lower price of materials. Multiple different types of material can be used simultaneously in the FDM process.
FDM 3D Printing Manufacturing FAQs
FDM 3D printing is a process in which thermoplastic materials are extruded from a print head and stacked layer by layer on a build platform. It is a widely used 3D printing technology.
FDM 3D printing technology has many advantages, including fast speed, high degree of customization, low modeling complexity, and relatively low cost.
First, FDM 3D printing technology is known for its fast speed. Compared with traditional manufacturing methods, FDM 3D printing can complete complex model production in a short time. This is because FDM printers build objects by stacking materials layer by layer, rather than through traditional methods such as cutting or casting. This layer-by-layer stacking process allows FDM 3D printing to produce high-quality models at a faster speed.
Secondly, FDM 3D printing technology has a high degree of customization capabilities. Due to its flexibility and programmability, FDM 3D printing can be personalized according to the user's needs and design requirements. Whether it is small batch production or mass customization, FDM 3D printing can easily handle it. This allows designers and manufacturers to realize their creativity and ideas more freely, thus providing more competitive products.
In addition, the modeling complexity of FDM 3D printing technology is relatively low. Compared to traditional manufacturing methods, FDM 3D printing does not require complex molds or tools. Designers can use computer-aided design software (CAD) to create models and import them into an FDM printer for printing. This simplified modeling process not only reduces time and costs in the manufacturing process, but also reduces the need for specialized skills.
Finally, FDM 3D printing technology is relatively low-cost compared to other manufacturing methods. Although the material cost of FDM 3D printing may be higher, the overall manufacturing cost is still relatively low due to its fast production speed and low modeling complexity. In addition, FDM 3D printing can also reduce scrap and the need for secondary processing, further reducing manufacturing costs.
To sum up, FDM 3D printing technology is favored for its fast speed, high degree of customization, low modeling complexity and relatively low cost. These advantages make FDM 3D printing have broad application prospects in various fields, including manufacturing, medical fields, aerospace, etc. With the continuous development and innovation of technology, FDM 3D printing technology will continue to bring more opportunities and development space to all walks of life.
Although FDM 3D printing technology has advantages in many aspects, it also has some disadvantages. First, the surface of objects printed by FDM 3D is usually rough, which may affect their appearance and texture. Secondly, since support structures are required to keep the shape of the object stable during the FDM 3D printing process, additional steps are required to remove these support structures after printing is completed, which increases the complexity and time cost of the production process. Finally, FDM 3D printing is slower compared to other 3D printing technologies, which means it is not suitable for mass production or rapid prototyping.
FDM 3D printing technology is a common rapid prototyping technology that uses a layer-by-layer stacking method to create three-dimensional objects. In the FDM 3D printing process, the STL file format needs to be used to describe the geometry and structure of the object to be printed.
The STL file format is a file format used to store three-dimensional model data, and its full name is "Stereolithography". It consists of a series of triangular patches, each of which has three points defining its position and normal vector. By stacking these patches in a certain order, a complete three-dimensional model can be obtained.
When using FDM 3D printing technology, you first need to convert the design model of the object to be printed into STL file format. This can be done by using professional CAD software, such as SolidWorks, AutoCAD, etc. During the conversion process, the design model requires some processing to ensure it is suitable for 3D printing. For example, defects in the model need to be repaired, mesh quality optimized, etc.
Once the design model is converted to STL file format, it can be imported into the FDM 3D printer’s software for print settings. In the software, printing parameters can be adjusted, such as printing speed, filling density, layer height, etc. At the same time, the model can also be sliced and divided into a series of thin layers to facilitate the printer to print layer by layer.
FDM 3D printing technology works by extruding molten plastic or metal wire from a nozzle and depositing it on the printing platform in a predetermined path. As the print head moves, the material gradually accumulates to form the desired three-dimensional object. After printing is completed, the printed parts can be removed from the printing platform and processed for subsequent processing.
In short, FDM 3D printing technology requires the use of STL file format to describe the geometry and structure of the object to be printed. By converting the design model into an STL file and setting the print settings in the 3D printer software, fast and accurate 3D object manufacturing can be achieved.
FDM 3D printing materials include ABS, PLA, PETG, TPU, etc. These materials are widely used in the field of 3D printing, and each material has its own unique properties and application areas.
First of all, ABS (acrylonitrile-butadiene-styrene) is a common engineering plastic with excellent strength, hardness and impact resistance. It is suitable for making durable parts such as mechanical parts, tools and housings. ABS material also has good wear and chemical resistance, making it ideal for many industrial applications.
Secondly, PLA (polylactic acid) is a biodegradable polymer made from renewable resources. It has a low melting point and good printing performance, and is suitable for making food packaging, medical equipment, toys, etc. The environmentally friendly properties of PLA materials make it an important choice for sustainable development and green manufacturing.
PETG (polyethylene terephthalate-copolymer) is a high-performance thermoplastic polyester with excellent transparency and weather resistance. It is suitable for making optical devices, automotive parts and decorations, etc. The high stiffness and heat resistance of PETG materials make them the first choice for many high-end applications.
Finally, TPU (thermoplastic polyurethane) is an elastomeric material that offers excellent resilience and abrasion resistance. It is suitable for making sports insoles, car seats and seals, etc. The softness and water resistance of TPU materials make them ideal for many applications where comfort and durability are critical.
In summary, the choice of FDM 3D printing material depends on the desired performance and application requirements. Materials such as ABS, PLA, PETG and TPU all have their own characteristics and advantages and can be selected according to specific circumstances to meet the needs of different 3D printing projects.
FDM 3D printing technology is an advanced manufacturing method that creates objects by stacking materials layer by layer. To achieve this process, we need to use two key software tools: 3D modeling software and slicing software.
First, 3D modeling software is a tool used to create three-dimensional models. It allows users to design and build three-dimensional representations of objects through operations such as drawing, rotation, and scaling. Users can use various modeling tools and functions to create complex geometric shapes such as lines, curves, surfaces, etc. By adjusting parameters and details, users can precisely control the shape, size and appearance of their models.
Once the user has completed the design of the 3D model, they next need to use slicing software to convert it into a G-code file that the printer can understand. Slicing software cuts the 3D model into a series of thin slices and generates corresponding instructions and parameters for each layer. These instructions include the movement path of the printer, the temperature and speed of the nozzle, etc. Slicing software can also optimize the printing process, such as automatically filling support structures, adjusting printing speed and direction, etc., to improve printing quality and efficiency.
The slicing software also provides some advanced functions, such as print preview, material settings and printing parameter adjustment. Users can view each layer during the printing process through the preview function to ensure the correctness and completeness of the model. Material settings allow the user to select parameters suitable for a specific material, such as temperature, extrusion volume and filling density. Printing parameter adjustments can optimize printing speed, print quality, and material utilization.
In short, FDM 3D printing technology relies on 3D modeling software and slicing software to realize the object manufacturing process. 3D modeling software is used to create three-dimensional models, while slicing software cuts the model into G-code files that the printer can understand. These software tools provide users with the power and flexibility to design, optimize and control the printing process to achieve high-quality print results.
FDM 3D printers require components such as an extrusion head capable of extruding thermoplastic materials, a build platform, and a control system. These components play a vital role in the 3D printing process.
First of all, the extrusion head is one of the core components of the FDM 3D printer. It is responsible for heating and extruding the thermoplastic material into filaments, which are then deposited layer by layer on the building platform through a nozzle, ultimately forming the desired three-dimensional object. The design and performance of the extrusion head directly affect the printing quality and speed. Therefore, it is very important to choose an extrusion head suitable for the required printing material.
Second, the build platform is a flat structure used to support and position the printed object. During the printing process, the build platform is gradually lowered, allowing new printed layers to be precisely aligned with already printed layers. The material and surface treatment the platform is built from can also affect print quality. Some common build platform materials include aluminum, glass, and PEI (polyetherimide).
Finally, the control system is the brain of the FDM 3D printer and is responsible for controlling the operation of the entire printing process. It receives 3D model files sent by the computer and converts them into instructions that the printer can understand. The control system is also responsible for controlling parameters such as temperature, speed and pressure of the extrusion head to ensure the stability and accuracy of the printing process. In addition, the control system can also provide a user interface to facilitate users to set up print settings and monitor print progress.
To sum up, the components of an FDM 3D printer include the extrusion head, build platform and control system. The selection and performance of these components are critical to achieving high-quality 3D printing results.
The maximum print size for FDM 3D printing depends on the printer model and configuration used. Different printer models and configurations have different printing capabilities, so the maximum print size will also vary.
First, the printer's build volume is one of the important factors that determines the maximum print size. Build volume refers to the amount of space that can fit inside the printer, usually expressed in cubic millimeters (mm³). A larger build volume means larger sized objects can be printed. Therefore, when choosing a printer, you need to determine the required build volume based on actual needs.
Secondly, the printing resolution of the printer is also one of the factors that affects the maximum printing size. Print resolution refers to the detail and precision a printer can produce per unit area. Higher print resolution provides finer print results, but also increases print time. Therefore, when choosing a printer, you need to weigh the balance between print resolution and print speed.
In addition, the printer's printing material will also affect the maximum print size. Different types of 3D printing materials have different characteristics and application ranges. Some materials may be suitable for smaller print sizes, while others are suitable for larger print sizes. Therefore, when choosing a printer, you need to consider the characteristics and application range of the printing materials used.
Finally, the printer's software settings and parameter adjustments also affect the maximum print size. Print size can be limited or optimized by adjusting the printer's software settings and parameters. For example, parameters such as minimum wall thickness and infill density can be set to control print size and quality.
To sum up, the maximum printing size of FDM 3D printing depends on factors such as the printer’s build volume, printing resolution, printing materials, software settings and parameter adjustments. When selecting and using a 3D printer, these factors need to be considered comprehensively to ensure that it can meet actual needs and obtain the best printing results.
The printing speed of FDM 3D printing depends on the printer model and configuration used, and is usually between 20-200 mm/second. This speed range can be adjusted for different printer models and settings. Generally speaking, newer printers and more advanced configurations offer higher printing speeds.
The printing speed of a printer is affected by several factors. First, the resolution and layer thickness of the printer directly affect the printing speed. Higher resolutions and smaller layer thicknesses increase print time, while lower resolutions and larger layer thicknesses speed up printing. Therefore, when choosing a printer configuration, you need to weigh the relationship between resolution and printing speed according to actual needs.
Secondly, the printer’s nozzle design and printing material selection will also have an impact on the printing speed. Some high-end printers are equipped with multiple nozzles that can print in multiple colors at the same time, thus increasing the printing speed. In addition, choosing the right printing material for your printer can also increase printing speed. Some printing materials have faster curing speeds, which can reduce print time.
In addition, the hardware performance of the printer is also an important factor affecting the printing speed. A high-performance processor, larger memory, and faster data transfer speeds increase the printer's processing power and responsiveness, resulting in faster printing.
Finally, the printer's software settings can also affect print speed. By optimizing printing parameters such as printing path, infill density and support structure, printing efficiency can be improved and printing time reduced.
To sum up, the printing speed of FDM 3D printing is affected by many factors, including printer model and configuration, resolution and layer thickness, nozzle design and printing material selection, hardware performance, and software settings. Depending on your actual needs and budget, you can choose the right printer and configuration to meet your specific print speed requirements.
FDM 3D printing usually requires post-processing, such as sanding, painting, removing support structures, etc. These steps are intended to improve the quality and appearance of the print and make it more suitable for practical applications.
First, sanding is an important post-processing step to remove rough and uneven parts of the print surface. Since materials are formed by stacking layer by layer during the FDM 3D printing process, some layer patterns and steps will appear on the surface of the printed part. Sanding can make the surface of the print smoother, improving its tactile and appearance quality.
Second, painting is another common post-processing step used to add color and a protective layer to a print. FDM 3D printing typically uses plastic materials, which are susceptible to oxidation, fading, and wear when exposed to the outside environment. Painting can provide a layer of protection to the print, protecting it from the outside environment and giving it better durability and aesthetics.
In addition, removal of support structures is also an important part of FDM 3D printing post-processing. During the printing process, in order to maintain the shape and stability of the printed parts, support structures are usually used to support the suspended parts of the printed parts. However, these support structures need to be removed after printing in order for the print to fully display its design. The process of removing support structures requires care to avoid damaging the surface or shape of the print.
To sum up, FDM 3D printing usually requires a series of post-processing steps, including sanding, painting, and removing support structures. The purpose of these steps is to improve the quality and appearance of the print and make it more suitable for real-world applications. Through reasonable post-processing, the effect and value of FDM 3D printing can be further improved.
FDM 3D printing technology has the ability to print in a variety of colors, which usually requires the use of materials of different colors or processing such as painting after printing. The flexibility of this technology allows users to choose different color combinations based on their needs, thereby creating a rich variety of prints.
First, FDM 3D printing technology can mix materials of different colors in the same layer by controlling the movement of the printer nozzle and the extrusion amount of material, thereby achieving multi-color printing. This method can create objects with gradient effects, such as rainbow-colored toys, colorful decorations, etc. In addition, more precise color control can be achieved by adjusting the proportions of materials of different colors to meet specific design requirements.
Secondly, for some complex models or artworks, FDM 3D printing technology may require coloring after printing. This can be achieved by hand painting, spraying, dip dyeing, etc. Painting not only changes the color of an object, but also adds detail and texture, making printed works more vivid and interesting. In addition, coloring can also repair defects or errors that may occur during the printing process and improve print quality.
However, it should be noted that FDM 3D printing technology still has some limitations in multi-color printing. First of all, due to the limitations of the printer nozzle, only one color of material can be extruded at a time, so multi-color printing needs to be done layer by layer, which increases printing time and cost. Secondly, materials of different colors may bleed into each other or produce uneven coatings, resulting in a decrease in the quality of the print results. Therefore, when doing multi-color printing, you need to carefully select the appropriate materials and processing methods to ensure the quality and appearance of the printed work.
In short, FDM 3D printing technology has the ability to print a variety of colors, which can be achieved by mixing materials of different colors or applying color after printing. This technology provides designers and artists with more creative possibilities, allowing them to create richer and more diverse 3D printed works.
Fused deposition modeling (FDM) 3D printing materials are generally safe, but if used improperly or with low-quality materials, harmful substances can be produced.
First, we need to understand what fused deposition modeling (FDM) 3D printing is. This is a manufacturing technique that creates three-dimensional objects by melting and depositing thermoplastic filament layer by layer on a build platform. This technology is widely used in a variety of fields, including medical, construction, automotive and consumer products.
However, although FDM 3D printing materials are generally safe, there are some potential risks that can arise if used incorrectly. For example, if the user does not handle or store these materials properly, it may result in a fire or other type of accident. In addition, harmful substances may be produced if the printers used by users are not properly maintained and cleaned.
Another possible risk is using low-quality 3D printing materials. These materials may contain harmful chemicals such as heavy metals, plasticizers, and other toxic substances. If these substances are released into the environment, they may cause harm to human health and the environment.
Therefore, while FDM 3D printed materials are generally considered safe, users still need to take appropriate precautions to ensure their safety and health. This includes handling and storing materials correctly, cleaning and maintaining the printer regularly, and using only certified high-quality 3D printing materials.
Common question in FDM 3D Printing Production
The printing accuracy of FDM 3D printing depends on the printer model and configuration used, usually between 0.1-0.5mm.
FDM 3D printing usually requires the use of support structures to ensure print quality. This is because during the FDM 3D printing process, the printer stacks molten plastic layer by layer to create a three-dimensional object. However, when printing complex geometries or overhanging structures, these parts may not remain stable due to gravity.
To solve this problem, support structures are introduced into the printing process. Support structures are temporary structures automatically generated by the printer to support parts that cannot remain stable on their own. These support structures are typically made from the same material as the print material and can be removed after the print is complete.
The design and placement of support structures is a very important step in FDM 3D printing. They must be placed exactly where they need to be supported to ensure the stability and integrity of the printed object. At the same time, the design of the support structure also needs to take into account the subsequent disassembly process so that it can be easily removed from the printed object.
The use of support structures can greatly improve the success rate and print quality of FDM 3D printing. They help the printer remain stable in areas with complex geometries or overhangs, which can prevent print failures or defects. In addition, the support structure can also reduce the deformation and warping of the printed object, improving its surface quality and accuracy.
However, the use of support structures also presents some challenges and limitations. First, the addition of support structures increases printing time and cost because they require additional materials and processing steps. Secondly, the design and placement of support structures requires a certain amount of experience and skill to ensure they function correctly and have minimal impact on the printed object. Finally, the support structure removal process may require additional time and effort to ensure that they can be completely removed from the printed object without leaving any residue or damage.
To sum up, FDM 3D printing usually requires the use of support structures to ensure print quality. Although the use of support structures poses some challenges and limitations, they remain one of the key factors in achieving high-quality 3D printing. Through proper design and placement of support structures, as well as careful removal processes, more stable and accurate FDM 3D printing results can be achieved.
FDM 3D printing materials can be recycled.
FDM (Fused Deposition Modeling) is a common 3D printing technology that uses thermoplastics as the printing material. FDM 3D printing offers many advantages over traditional manufacturing methods, one of which is the recyclability of the material.
When FDM 3D printing is completed, the printed object usually consists of unused plastic filaments and support structures. These unused plastic filaments can be collected and reprocessed into new 3D printing materials. With proper processing and recycling processes, these discarded plastic filaments can be reused for printing, thus reducing the waste of resources.
In addition, the support structures produced during the FDM 3D printing process can also be recycled. These support structures are usually made of dissolvable materials, such as water-soluble polymers. After printing is completed, the printed object is immersed in water, and the support structure will gradually dissolve, leaving the complete printed object. This way, the support structure can be recycled and reprocessed into new dissolvable material for use in the next print.
Recycling FDM 3D printing materials can not only reduce resource consumption, but also reduce environmental pollution. By repurposing discarded plastic filaments and support structures, the need for virgin plastic is reduced, reducing reliance on non-renewable resources such as petroleum. In addition, recycling can reduce the emission of waste plastics and help protect the health of the environment and ecosystems.
In summary, the recyclability of FDM 3D printing materials provides a feasible solution for sustainable development. By recycling discarded plastic filaments and support structures, we can reduce resource consumption, reduce environmental pollution, and create a more sustainable material supply chain for future 3D printing applications.
FDM 3D printing technology requires some adjustments during use to ensure printing quality and efficiency. Here are some common tuning parameters:
1. Distance between print head and build platform: This distance is critical to print quality. If the distance is too large, it may cause the printed object to deform or peel off between layers; if the distance is too small, it may cause friction between the print head and the build platform, affecting the printing effect. Therefore, this distance needs to be adjusted based on actual printing needs and material properties.
2. Extrusion speed: Extrusion speed refers to the speed at which the printer extrudes molten plastic from the nozzle. This parameter directly affects the printing speed and print quality. If the extrusion speed is too fast, it may cause the plastic to shrink during the cooling process, causing the printed object to deform; if the extrusion speed is too slow, it may cause the printing speed to decrease and affect production efficiency. Therefore, the extrusion speed needs to be adjusted based on actual printing needs and material properties.
3. Temperature: Temperature is one of the key factors that affects the 3D printing effect. If the temperature is too high, the plastic may melt excessively, affecting the printing quality; if the temperature is too low, the plastic may not fully melt, affecting the printing effect. Therefore, the temperature needs to be adjusted based on actual printing needs and material properties.
4. Layer height: Layer height refers to the height of each layer of printing. This parameter directly affects the printing speed and print quality. If the layer height is too high, the printing speed may be reduced; if the layer height is too small, the surface of the printed object may be uneven. Therefore, the layer height needs to be adjusted based on actual printing needs and material properties.
5. Filling density: Filling density refers to the proportion of filling inside the printed object. This parameter directly affects the strength and weight of the printed object. If the filling density is too high, the printed object may be too heavy; if the filling density is too small, the printed object may not be strong enough. Therefore, the filling density needs to be adjusted based on actual printing needs and material properties.
In short, when using FDM 3D printing technology, the above parameters need to be adjusted according to the actual situation to ensure printing quality and efficiency. At the same time, the printer also needs to be maintained and cleaned regularly to ensure its normal operation.
During the FDM 3D printing process, you may encounter some problems. These problems may include poor print quality, slow printing speed, deformation of printed objects, etc. However, these problems can be solved in some ways.
First, we can solve the problem by adjusting the printing parameters. This includes changing parameters such as print speed, layer height, etc. For example, if we find that the printing speed is too slow, we can reduce the printing speed to improve printing efficiency. Likewise, if we find that the printed object is deformed, we can increase the layer height to reduce the possibility of deformation.
Secondly, we can also solve the problem by replacing the material. Different 3D printing materials have different properties, such as strength, flexibility, etc. If we find that our current materials do not meet our needs, we can try to replace them with other types of materials.
Additionally, we can solve the problem by cleaning the printer. Dust or other impurities may accumulate inside the printer, which may affect print quality. Therefore, regular cleaning of the printer is very necessary.
In general, although FDM 3D printing may encounter some problems, we can effectively solve these problems by adjusting printing parameters, replacing materials, and cleaning the printer.
FDM 3D printers require regular maintenance, such as cleaning the print head, building the platform, checking cable connections, etc. These maintenance tasks are critical to maintaining proper printer operation and print quality.
First of all, cleaning the print head is one of the key steps to ensure that the printer is working properly. Over time, the printhead can accumulate dust, residue, or other impurities, which can cause print quality to degrade or even stop printing properly. Therefore, regular cleaning of the print head is necessary. You can use a special cleaning solution or soft cloth to gently wipe the print head to ensure that its surface is clean and dust-free.
Secondly, building the platform is another important maintenance task. During the printing process, the model will gradually rise from the platform, so the surface of the platform may become uneven or damaged. This can result in poor contact between the model and the platform, affecting print quality. To solve this problem, periodically use sandpaper or a whetstone to lightly sand the surface of the platform to make it smooth and even.
In addition, checking the cable connections is also an important part of maintaining the printer. The stability and reliability of the cable connection are critical to the proper operation of the printer. If the cable connection is loose or damaged, data transfer may be interrupted or the printer may not function properly. Therefore, it is necessary to regularly check whether the cable connection is firm and reliable, and to repair or replace damaged cables in a timely manner.
In addition to the above maintenance tasks, there are some other common maintenance measures that are worth noting. For example, regularly replace the printer's consumables (such as printing materials and nozzles) to ensure its performance and life; regularly calibrate the printer's parameters to obtain more accurate printing results; regularly clean dust and debris inside and outside the printer to maintain Its neat and in good working order.
In short, regular maintenance of an FDM 3D printer is key to ensuring its normal operation and print quality. With maintenance tasks like cleaning the printhead, building the platform, and checking cable connections, you can extend the life of your printer and get higher-quality prints.
The service life of an FDM 3D printer depends on a variety of factors, including frequency of use, quality of maintenance, and quality. Generally speaking, the lifespan of an FDM 3D printer is usually between 2 and 5 years.
First of all, the frequency of use is one of the important factors affecting the life of FDM 3D printers. Frequent use causes greater stress and wear on the various parts of your printer, shortening its lifespan. Therefore, if the printer is used frequently, its lifespan may be relatively short.
Secondly, maintenance quality is also one of the key factors that determine the lifespan of FDM 3D printers. Regular cleaning and maintenance ensures that all parts of your printer are functioning properly and extend their service life. For example, timely replacement of key components such as the print head and cleaning of the print bed and nozzle can reduce the risk of failure and damage, thus improving the reliability and life of the printer.
In addition, the quality of FDM 3D printers will also affect their lifespan. High-quality printers typically use more durable materials and advanced manufacturing processes to better resist wear and damage. In contrast, a lower-quality printer may be more prone to failure and damage, resulting in a shorter lifespan.
To sum up, the service life of FDM 3D printer is affected by many factors. Through proper use, regular maintenance, and choosing a high-quality printer, you can extend its life and ensure its proper operation.
The cost of FDM 3D printing depends on several factors, including the materials used, printer model, and print quality. Generally speaking, the cost of FDM 3D printing ranges from a few dollars to hundreds of dollars.
First of all, the materials used are one of the important factors that affect the cost. Different types of 3D printing materials have different prices and characteristics. Common 3D printing materials include plastics, metals, ceramics, etc. Among them, plastic is one of the most common and affordable 3D printing materials, while metal materials are often used to make high-strength and wear-resistant parts. Therefore, choosing different materials for 3D printing projects will directly affect the cost.
Secondly, the printer model is also one of the key factors that determine the cost. There are a variety of 3D printers available on the market, ranging in price and performance. Generally speaking, higher-end 3D printers have greater accuracy and wider material compatibility, but are also priced accordingly. Conversely, lower-end 3D printers may be more affordable, but their print quality and speed may be relatively low.
Finally, print quality is also a factor that affects cost. High-quality 3D printing requires higher printing resolution and finer detail, which may require longer printing times and more material usage. Therefore, if the print quality requirements are higher, the cost will increase accordingly.
To sum up, the cost of FDM 3D printing is affected by many factors, including the materials used, printer model and print quality. Depending on specific needs and budget, suitable 3D printing projects and equipment can be selected to balance the relationship between cost and quality.
FDM 3D printing technology is widely used in various fields, including medical, education, construction, automotive, aerospace, etc.
In the medical field, FDM 3D printing technology is used to manufacture customized medical devices and prostheses. Through the precise printing process, doctors can design and manufacture devices suitable for patients' specific needs, improving treatment effects and patients' quality of life. In addition, FDM 3D printing can also be used to manufacture biomaterials and tissue engineering scaffolds, providing new possibilities for regenerative medicine and tissue repair.
In the field of education, FDM 3D printing technology provides students with a more intuitive and practical learning method. Students can use 3D printed models to demonstrate and understand complex concepts and structures, and deepen their understanding and memory of knowledge. In addition, FDM 3D printing can also be used to produce teaching tools and experimental equipment to improve teaching effects and students’ learning interest.
In the field of architecture, FDM 3D printing technology can be used to quickly manufacture architectural models and prototypes. Designers can use 3D printing technology to verify the feasibility of design solutions and optimize and improve them. In addition, FDM 3D printing can also be used to manufacture customized building components and building materials to improve the personalization and sustainability of buildings.
In the automotive field, FDM 3D printing technology can be used to manufacture automotive parts and prototypes. Through 3D printing technology, manufacturers can reduce the manufacturing cost and production cycle of parts, and improve the accuracy and quality of parts. In addition, FDM 3D printing can also be used to manufacture lightweight automotive parts to improve vehicle performance and fuel efficiency.
In the aerospace field, FDM 3D printing technology can be used to manufacture structural parts and components of aerospace vehicles. Through 3D printing technology, manufacturers can reduce the weight and complexity of parts and increase their strength and durability. In addition, FDM 3D printing can also be used to manufacture customized aerospace parts to meet the needs of specific missions.
FDM 3D printing technology is an advanced manufacturing process that can create objects of various shapes by stacking materials layer by layer in three-dimensional space according to design files. This technology has a wide range of applications and can be used to print a variety of items, including but not limited to parts, models, and artwork.
First of all, FDM 3D printing technology plays an important role in manufacturing. It can be used to produce complex parts and assemblies that may be difficult or costly to achieve with traditional manufacturing methods. By importing design files into a 3D printer, precise parts can be quickly manufactured as needed, thereby increasing production efficiency and reducing costs. This is especially useful for prototyping, low-volume production and customized products.
Secondly, FDM 3D printing technology also plays an important role in the education field. Students and teachers can use 3D printers to create teaching models and experimental setups to help them better understand and learn complex concepts. This hands-on approach to learning increases student engagement and creativity and sparks interest in fields such as science, engineering and design.
In addition, FDM 3D printing technology also provides new possibilities for artistic creation. Artists can use 3D printing technology to create unique sculptures, installations and artworks. Compared with traditional art media, 3D printing technology allows artists to explore combinations of shapes, structures and materials more freely to create stunning works.
Finally, FDM 3D printing technology also plays an important role in the medical field. Doctors and researchers can use 3D printing technology to create human organ models, surgical models, and customized medical devices. These models can help doctors plan and train surgeries, improving the accuracy and safety of surgeries. In addition, 3D printing technology can also be used to create personalized prostheses and dentures to meet the specific needs of patients.
In short, FDM 3D printing technology, as an innovative manufacturing process, has broad application prospects. It can not only be used to manufacture parts and models of various shapes, but also play an important role in education, art, medical and other fields. As technology continues to develop and improve, FDM 3D printing technology will continue to bring more innovation and convenience to all walks of life.
FDM 3D printing materials have some environmental impacts, including plastic pollution and energy consumption.
First of all, the materials used in FDM 3D printing technology are usually thermoplastics, such as ABS, PLA, etc. These plastics require a lot of energy to heat and melt during the production process, resulting in a certain amount of energy consumption. In addition, due to the widespread application of 3D printing technology, the demand for plastic materials is also increasing, leading to over-exploitation and waste of plastic resources. These problems have had a certain impact on the environment.
Secondly, the waste generated during the FDM 3D printing process is also a problem. When printing is complete, the unused plastic material is typically discarded or recycled. However, due to the non-degradable nature of plastic materials, they may remain in the environment for a long time, causing contamination of soil and water sources. In addition, if discarded plastic materials are not properly disposed of, they may enter the marine ecosystem and cause harm to marine life.
To reduce the environmental impact of FDM 3D printing materials, there are some measures that can be taken. First, the use of degradable 3D printing materials, such as biodegradable plastics or recyclable thermoplastics, can be promoted. These materials can be broken down or recycled more easily after use, reducing negative impact on the environment. Secondly, the recycling and reuse of waste plastic materials can be strengthened to ensure that they are properly treated and recycled. In addition, users can be encouraged to save more materials and avoid waste when using 3D printing technology.
In summary, FDM 3D printing materials have some environmental impacts, including plastic pollution and energy consumption. By promoting degradable materials, strengthening recycling and saving materials, these impacts can be reduced and sustainable development achieved.
FDM 3D printing and SLA 3D printing are two different 3D printing technologies. FDM uses thermoplastic materials, while SLA uses light-curing resin.
FDM (Fused Deposition Modeling) is a common 3D printing technology that heats thermoplastic materials to a molten state and then deposits them layer by layer on a build platform through a nozzle, ultimately forming a three-dimensional object. This technology is suitable for various plastic materials, such as ABS, PLA, etc., and can produce parts with good mechanical properties and durability.
In contrast, SLA (stereolithography) is a 3D printing technology based on photosensitive resin. In this technology, a light source shines on the photosensitive resin through a transparent building platform, causing a photochemical reaction to solidify it into a solid state. As the light source moves, a new layer of photosensitive resin is solidified, eventually forming a complete three-dimensional object. SLA technology is suitable for manufacturing parts with complex geometries and smooth surfaces, and is commonly used in fields such as medicine, jewelry and art.
Although FDM and SLA are two different 3D printing technologies, they both have their own advantages and application areas. FDM technology is suitable for mass production with relatively low cost, while SLA technology is suitable for manufacturing high-precision and complex parts. Therefore, when choosing a 3D printing technology, you need to decide which technology to use based on your specific needs and project requirements.