Introduction
Fused Deposition Modeling (FDM), as a revolutionary additive manufacturing technology, has emerged. Fused Deposition Modeling (FDM), as a revolutionary additive manufacturing technology, has emerged and is changing the face of various industries. By stacking molten plastic filaments layer by layer, FDM offers unparalleled flexibility in creating three-dimensional objects. This article will take an in-depth look at the various applications and innovations that are driving FDM to the forefront of additive manufacturing.
First of all, the wide application of FDM technology makes it occupy an important position in the manufacturing industry. Whether it is the automotive, aerospace, medical or consumer goods industries, FDM has brought huge changes to these fields. By using FDM technology, manufacturers are able to produce complex parts and prototypes quickly and accurately, greatly improving production efficiency and product quality.
Secondly, innovation in FDM technology continues to promote its development. With the advancement of technology, the performance of FDM equipment continues to improve, making printing faster, more precise, and more diverse in material selection. In addition, FDM is also combined with other advanced technologies, such as the combination of 3D printing and artificial intelligence, to achieve automated production and intelligent optimization, further improving production efficiency and reducing costs.
Third, the flexibility of FDM technology makes it suitable for various application scenarios. Whether it is small batch production or large-scale customized production, FDM can be flexibly adjusted according to needs. At the same time, FDM can also achieve mixed printing of multiple materials, giving products better performance and functionality. This flexibility makes FDM widely used in many industries, such as medical devices, aerospace, automobile manufacturing, etc.
Finally, the sustainable development of FDM technology has also attracted much attention. With the increasing awareness of environmental protection, FDM technology gradually adopts degradable and recycled materials to reduce the impact on the environment. In addition, FDM technology can also reduce energy consumption and waste generation by optimizing the design and production process, thereby achieving a more sustainable production model.
To sum up, Fused Deposition Modeling (FDM), as a revolutionary additive manufacturing technology, has shown great potential and advantages in various fields. Its wide range of applications, continuous innovation, flexible adaptability and sustainable development have made FDM a leader in the field of additive manufacturing. With the continuous advancement of technology and the continuous expansion of applications, it is believed that FDM will continue to lead the development trend of the manufacturing industry.
Rapid Prototyping
One of the primary applications of FDM is rapid prototyping. Designers and engineers leverage FDM technology to swiftly produce prototypes of products, parts, and tools. This process enables iterative testing, allowing for modifications and improvements before committing to mass production. The cost-effectiveness and speed of FDM make it an invaluable tool in the prototyping phase.
Customized Products
FDM's capability to produce customized products with intricate geometries and features sets it apart from traditional manufacturing methods. The technology allows for the creation of complex designs that would be challenging or impossible to achieve using conventional approaches. From personalized consumer goods to highly specialized industrial components, FDM empowers manufacturers to meet unique requirements with precision.
Aerospace Industry
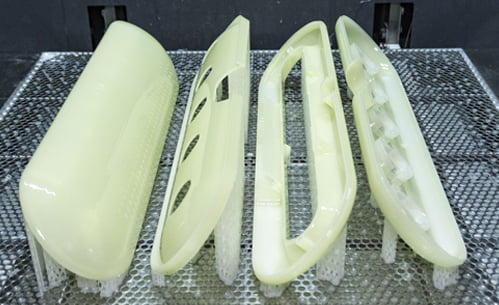
In the aerospace industry, FDM has found a niche in the production of lightweight and robust components. Brackets, panels, and molds are crafted with precision, meeting the stringent demands of aerospace engineering. The technology's ability to reduce weight without compromising strength contributes to enhanced fuel efficiency and overall performance in aircraft.
Medical Devices
FDM has made significant strides in the medical field, playing a crucial role in the production of patient-specific implants, prosthetics, and surgical guides. The customization afforded by FDM ensures a perfect fit for individual patients, improving the efficacy and success of medical procedures. This application showcases FDM's potential to revolutionize personalized healthcare.
Jewelry Making
The intricate world of jewelry making has embraced FDM for its ability to bring intricate designs and patterns to life. From detailed pendants to elaborate rings and earrings, FDM enables jewelers to push the boundaries of creativity. The technology's precision and adaptability make it a preferred choice for crafting unique and visually stunning pieces.
Education
FDM's user-friendly nature and educational value make it a staple in classrooms for teaching design, engineering, and manufacturing processes. Students gain hands-on experience in creating tangible objects, fostering a deeper understanding of the principles behind additive manufacturing. FDM's role in education paves the way for a future generation of skilled professionals in the field.
Art and Sculpture
In the realm of art and sculpture, FDM serves as a medium for artists to translate their visions into tangible creations. The technology allows for the production of intricate designs that might be impractical with traditional materials. Artists can experiment with form and structure, pushing the boundaries of what is achievable in the realm of artistic expression.
Automotive Industry
FDM has become integral to the automotive industry, where the demand for lightweight yet durable components is paramount. Engine parts, body panels, and interior trim benefit from FDM's ability to produce complex geometries with high strength-to-weight ratios. This not only enhances vehicle performance but also contributes to fuel efficiency and sustainability.
Construction
In construction, FDM is employed to produce building components such as beams, columns, and walls. The technology's efficiency in creating large-scale, durable structures adds a new dimension to construction methodologies. FDM's role in this sector signifies a shift towards more sustainable and cost-effective building practices.
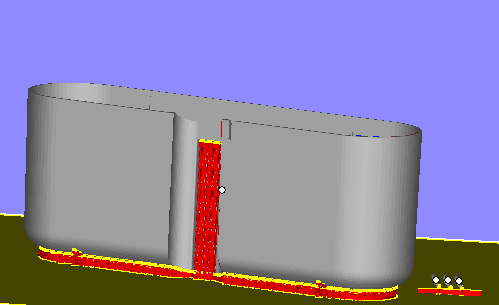
Food Industry
Even the food industry has embraced FDM for its ability to produce custom food containers and packaging. The technology allows for the creation of tailored designs that meet specific food packaging requirements. This application highlights FDM's versatility beyond traditional manufacturing domains, showcasing its potential to revolutionize diverse sectors.
Conclusion
Fused Deposition Modeling has emerged as a transformative force in additive manufacturing, with applications spanning industries as diverse as aerospace, healthcare, and art. Its versatility, cost-effectiveness, and customization capabilities have positioned FDM as a cornerstone of innovation. As technology continues to advance, FDM is poised to play an even more significant role in shaping the future of manufacturing across various sectors.