Table of Contents:
- Introduction to Prototype Molding Plastic
- Basic Design Principles for Prototype Molding Plastic
- Process of Prototype Molding Plastic
- Applications of Prototype Molding Plastic
- Quality Control and Inspection in Prototype Molding Plastic
- Advancements and Future Trends in Prototype Molding Plastic
- Comparison between Prototype Molding Plastic and Other Rapid Prototyping Methods
- Conclusion
-
1. Introduction to Prototype Molding Plastic:
Prototype molding plastic is a specialized injection molding process that aims to produce functional prototypes of parts or products in a short amount of time. It is a crucial step in the product development process as it enables manufacturers to validate design concepts, detect issues early, and reduce lead times. This article provides an in-depth guide on prototype molding plastic, highlighting its advantages, limitations, design principles, processes, applications, quality control measures, advancements, and comparisons with other rapid prototyping methods.
Advantages and Limitations of Prototype Molding Plastic:
The major advantage of prototype molding plastic is its cost-effectiveness and the ability to produce functional prototypes with high accuracy and detail in a shorter lead time as compared to traditional molding methods. Moreover, prototype molding plastic supports a broad range of plastic materials with varying physical properties, which makes it suitable for diverse products.
However, there are limitations as well. Prototype molding plastic is not a suitable method for producing large-scale parts, and it has a higher initial cost than other rapid prototyping methods.
-
2. Basic Design Principles for Prototype Molding Plastic:
Choosing the Right Material:
Choosing the appropriate plastic material is a crucial aspect of prototype molding plastic. The material must have the desired physical and mechanical properties to match the application of the final product.
Factors to Consider in Designing the Prototype:
While designing the prototype, factors like wall thickness, gating system, draft angles, and undercuts must be considered. The design should also leverage features like uniform wall thickness, simplified geometry, and appropriate tolerances.
Preparing the Prototype Mold:
The prototype mold is designed keeping in mind material flow, thermal properties, and the specificities of the plastic material. The mold design should be optimized to achieve consistent quality and minimize errors.
-
3. Process of Prototype Molding Plastic:
Creating the Mold Design:
The first step in prototype molding plastic is to create a mold design that matches the desired specifications of the prototype. With computer-aided design (CAD) software, engineers can create complex geometries and optimize the mold design for a higher level of precision.
Injection Molding the Prototype:
The prepared mold is loaded into the injection molding machine where the plastic material is heated to its melting point and then injected into the mold to reproduce the product’s prototype. The cooling of the plastic is carefully controlled, ensuring that the prototype is produced according to the design specification.
Post-Processing the Prototype:
Once the prototype is molded, it needs to be post-processed to meet the desired specifications. Processes like trimming, polishing, and painting are used to refine the prototype, ensuring that it matches the required dimensional accuracy and aesthetic appearance.
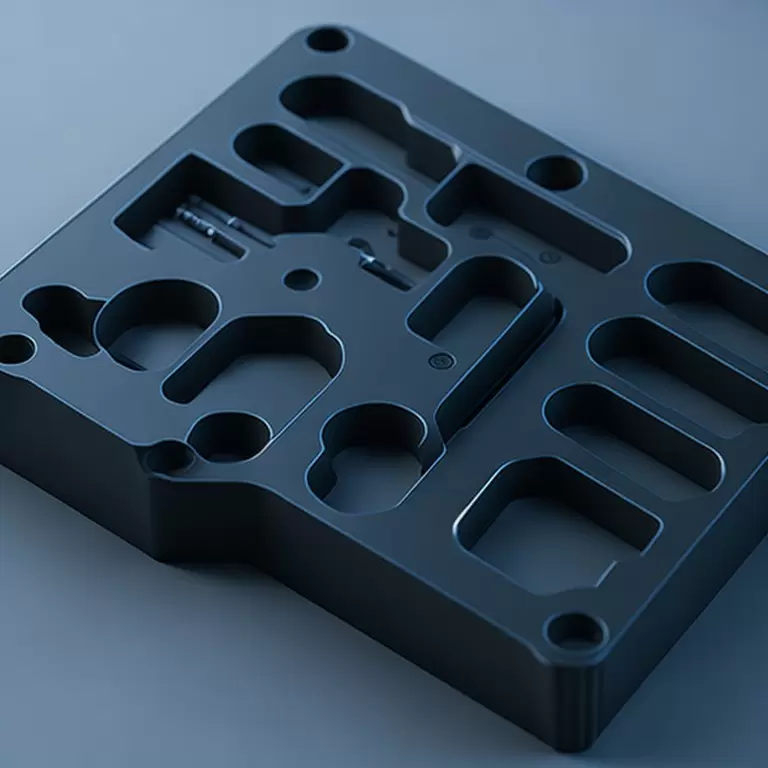
-
4. Applications of Prototype Molding Plastic:
Rapid Prototyping:
Prototype molding plastic is mainly used for the rapid prototyping of parts and products in a range of industries, including automotive, medical, electronics, and consumer goods.
Small Batch Production:
Prototype molding plastic is also widely adopted for small production runs where traditional injection molding is not a viable option due to higher tooling costs.
Testing and Validation:
Prototype molding plastic can be used to validate part viability in its function, form and fit testing, and detect design defects early in the development process.
-
5. Quality Control and Inspection in Prototype Molding Plastic:
Key Metrics in Prototype Molding Plastic Quality Control:
The key metrics that are used to monitor product quality include dimensional accuracy, surface finish, internal structure, and mechanical strength.
QC Techniques and Approaches:
A range of techniques such as visual inspection, non-destructive testing, and measurement gauges are used to perform quality control checks on prototype molded parts.
Safety and Regulatory Challenges and Considerations:
When designing and producing prototype molded parts, care must be taken to ensure that the production processes conform to industry regulatory requirements and health and safety standards.
-
6. Advancements and Future Trends in Prototype Molding Plastic:
Advancements in Plastic Materials and Technology:
In recent years, there have been significant advances in the types of plastic materials and technology that are available for prototype molding plastic. These new materials and technologies offer enhanced performance properties, a wider range of options, and greater adaptability for prototyping applications.
Integration with Industry 4.0:
The integration of prototype molding plastic with Industry 4.0 enables faster production and more accurate parts. Using artificial intelligence, computer vision, and robotics, manufacturers can optimize every aspect of the prototype mold production process.
Increasing Sustainability:
Advancements in material science are driving the adoption of biodegradable and renewable materials in prototype molding plastic, making the process more carbon-neutral and sustainable.
If you want more about Prototype Molding Plastic information ,You can click on the V1 Prototype website to find it.
-
7. Comparison between Prototype Molding Plastic and Other Rapid Prototyping Methods:
Comparison with 3D Printing:
3D printing is a widely adopted rapid prototyping method, but it has limitations to produce functional prototypes that can match the mechanical and material properties of the final product. In contrast, prototype molding plastic can produce functional parts with greater dimensional accuracy, surface finish, and strength.
Comparison with CNC Machining:
CNC machining produces parts with higher dimensional accuracy and uniformity than prototype molding plastic but is less cost-effective, slower, and not suitable for large-scale production runs.
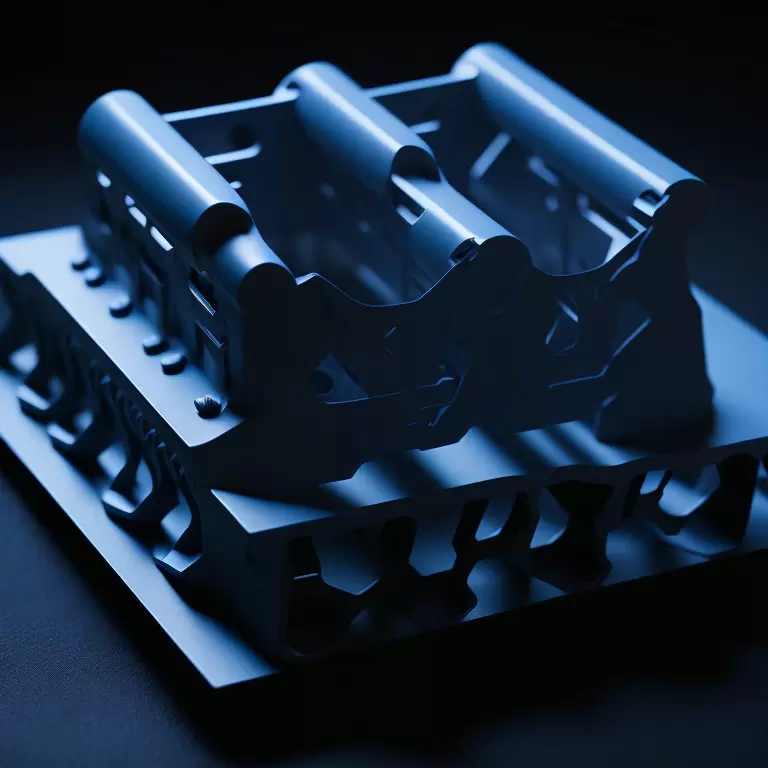
-
8. Conclusion:
Prototype molding plastic is a cost-effective and efficient method for producing functional prototypes at a high level of accuracy in a shorter lead time. The process supports a wide range of plastic materials with varying physical and mechanical properties, making it a suitable solution for various industries. To ensure that the prototype molding plastic process produces quality parts, it must conform to industry regulatory requirements and health and safety standards. The process is continuously evolving, with advancements in materials, technology, and sustainability driving its growth. As such, prototype molding plastic will continue to play an integral role in the product development process and will be a vital tool for manufacturers in the years to come.