To date, most 3D printing materials are still made from fossil-based materials such as plastics and resins, and although TAs have good prospects for use in automotive and marine applications, the production of these materials does not do well in terms of climate change and green recyclability. For this reason, the NOVUM project team in Europe is working on cellulose-based 3D printing materials for more environmentally friendly additive manufacturing in a wider range of industries.
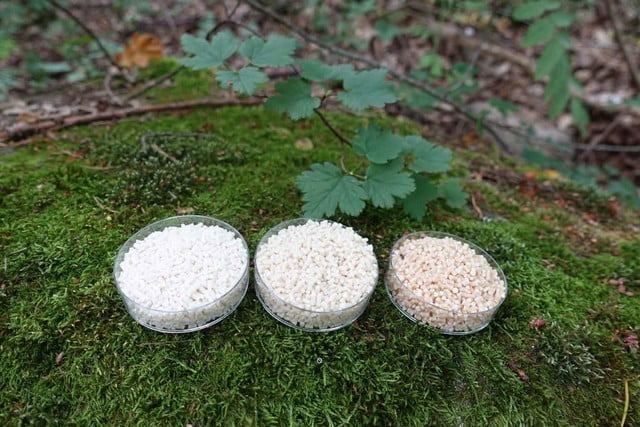
The thermoplastic materials developed during the project contain cellulose derivatives, cellulose powders and bio-based plasticisers and have a cellulose content 60% higher than the "commercial reference". Nevertheless, they still have the same or better material strength properties and can be adapted to the requirements of the end use.
Cellulose was chosen as the basis for the materials developed in this project because of its potential as a natural, sustainable and versatile alternative to many synthetic materials. When considering the use of cellulose in conjunction with 3D printing, the fact that cellulose is not inherently thermoplastic was a key challenge for the project participants to address.
It is possible to print the developed cellulose-based material using common 3D printing techniques (e.g. Fused Filament Fabrication (FFF)) and have a light weight and smooth surface end product. The material development and printing process will be demonstrated during the project lifecycle by creating components for use in the electrical insulation, marine and automotive industries.
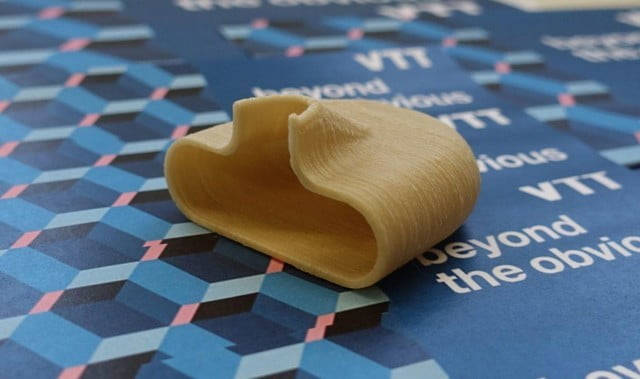
Cellulose is already a common raw material in the manufacture of electrical insulation components, however, according to the project participants, current production methods are inefficient in terms of labour, time, energy and waste generation. By developing a method of 3D printing cellulose-based materials to create components suitable for this sector, the participants hope to increase the efficiency of the production process without the use of moulds.
Elsewhere, outdoor decorative elements for cruise ships are a possible use case for the technology developed within the marine sector, while in the automotive sector bio-based materials could replace fossil-based materials and help improve the sustainability of the industry.
The project is also exploring 3D printing of wood fibre foam to create thick and porous fibre structures that do not collapse when dried. While the technology to produce such structures in 2D has been established, the creation of such structures in 3D through additive manufacturing is reportedly new territory. Participants in the project are investigating the best fibre foam mixes for the 3D printing process, layer bonding considerations and how to minimise drying times.
The project has already conducted successful trials to print wood fibre foam structures using extruder-style nozzles, and the next step is to explore how commercial 3D printers can be applied to the process. Participants saw potential applications for these types of structures located in the construction and transport sectors as sound and vibration resistant materials.
Introduction
In recent years, 3D printing technology has rapidly advanced, revolutionizing the manufacturing landscape across various industries. One of the most exciting areas of development in 3D printing is the exploration of sustainable and eco-friendly materials. NOVUM, a leading innovator in the field of 3D printing, has made significant strides by developing a cellulose-based bio-3D printing material. This breakthrough has the potential to transform the additive manufacturing industry and contribute to a more sustainable and environmentally friendly approach to production. In this blog post, we will delve into the significance of NOVUM's cellulose bio-3D printing material, its unique properties, and the potential applications it offers.
The Significance of Cellulose-Based 3D Printing Material
Cellulose is a fundamental component of the cell walls in plants, making it the most abundant organic polymer on Earth. Harnessing cellulose for 3D printing represents a significant leap towards sustainability in additive manufacturing. Traditional 3D printing materials, such as plastics and metals, often rely on non-renewable resources, and their production can contribute to environmental pollution. In contrast, cellulose is a renewable and biodegradable material, making it a promising candidate for eco-friendly 3D printing.
NOVUM's development of a cellulose-based 3D printing material opens up exciting opportunities for creating sustainable products with reduced environmental impact. As the world embraces more eco-conscious practices, the demand for cellulose bio-3D printing materials is expected to soar.
Unique Properties of NOVUM's Cellulose Bio-3D Printing Material
NOVUM's cellulose bio-3D printing material possesses several unique properties that set it apart from traditional 3D printing materials:
1. Biodegradability
Cellulose is inherently biodegradable, meaning that products made from this material can break down naturally over time, reducing waste and pollution.
2. Renewable Resource
Cellulose is sourced from plants, making it a renewable resource that can be sustainably harvested without depleting natural reserves.
3. Low Carbon Footprint
The production of NOVUM's cellulose bio-3D printing material results in a lower carbon footprint compared to traditional 3D printing materials, contributing to climate change mitigation efforts.
4. Non-Toxic and Safe
Cellulose is non-toxic and safe to handle, making it suitable for various applications, including those in the medical and food industries.
5. Versatility
NOVUM's cellulose bio-3D printing material offers excellent versatility, allowing for the creation of a wide range of products with varying complexities.
Potential Applications of NOVUM's Cellulose Bio-3D Printing Material
NOVUM's cellulose bio-3D printing material opens up numerous possibilities for sustainable manufacturing across various industries. Some potential applications include:
1. Sustainable Packaging
Cellulose-based materials can be used to produce sustainable and biodegradable packaging solutions, reducing the environmental impact of single-use plastics.
2. Biomedical Devices
The biocompatibility of cellulose makes it suitable for medical applications, including the production of surgical implants, tissue engineering scaffolds, and drug delivery systems.
3. Eco-Friendly Consumer Goods
NOVUM's cellulose bio-3D printing material can be utilized to create eco-friendly consumer goods, such as household items, toys, and accessories.
4. Sustainable Construction Materials
Cellulose-based materials may be employed to manufacture sustainable construction materials, including biodegradable building components and insulation.
5. Green Electronics
Cellulose can be incorporated into electronics manufacturing, contributing to greener and more sustainable electronic devices.
Advancing Sustainability in Additive Manufacturing
NOVUM's development of a cellulose-based bio-3D printing material represents a significant step forward in advancing sustainability in additive manufacturing. By harnessing the potential of renewable and biodegradable materials, the company is setting a positive example for the 3D printing industry. The introduction of NOVUM's cellulose bio-3D printing material showcases the importance of research and innovation in developing eco-friendly alternatives that reduce the environmental impact of manufacturing processes.
As 3D printing technology continues to evolve, further exploration of sustainable materials and manufacturing methods will drive progress towards a greener and more sustainable future. NOVUM's cellulose bio-3D printing material is a testament to the power of innovation and serves as a beacon of hope for a more environmentally conscious approach to additive manufacturing.
Conclusion
NOVUM's development of a cellulose-based bio-3D printing material marks a significant advancement in the quest for sustainable and eco-friendly additive manufacturing solutions. The unique properties of cellulose, including its biodegradability, renewability, and low carbon footprint, make it a promising material for various applications in the automotive industry and beyond.
As companies like NOVUM pave the way for sustainable practices in manufacturing, the adoption of cellulose-based bio-3D printing materials is expected to gain momentum. This transformative technology has the potential to reshape the future of production, making it more environmentally responsible and aligned with the principles of sustainability. By supporting research and development in sustainable 3D printing materials, we can collectively work towards a greener and more sustainable future for the manufacturing industry.