Table of Contents:
- Introduction
- Components of 5-Axis Machines
- Applications of 5-Axis Machining
- Benefits of 5-Axis Machining
- Choosing the Right 5-Axis Machine
- Programming for 5-Axis Machining
- Common Challenges with 5-Axis Machining
- Tips for Successful 5-Axis Machining
- Conclusion
-
1.Introduction
5-axis machining is an advanced manufacturing technique that allows for precision cutting with increased efficiency and accuracy. It involves the use of a 5-axis machine that can move a part or cutting tool in five different directions at once, enabling the creation of complex geometries in one setting. This technology is crucial in several industries, including aerospace, medical, automotive, and mold-making.
The importance of 5-axis machining lies in its ability to create complex geometries in a single setup. This saves time and reduces costs by eliminating the need for multiple setups and reducing the risk of errors during repositioning. Additionally, 5-axis machining allows for greater accuracy and improved surface finish, resulting in higher quality parts that meet tight tolerances. This technology has revolutionized manufacturing processes and has become an essential tool in modern manufacturing.
-
3.Components of 5-Axis Machines
The three key components of a 5-axis machine are the machine structure, control systems, and tooling. Each of these components plays a critical role in the success of 5-axis machining.
Machine Structure:
The machine structure of a 5-axis machine must be capable of handling the multiple axes of movement associated with this technology. The structure must be robust enough to withstand the forces generated during cutting and to maintain high levels of accuracy. Typically, 5-axis machines have a gantry-style structure or a horizontal spindle. The structure also includes the table, which holds the workpiece and the spindle head, which holds the cutting tool.
Control Systems:
Control systems are critical to the operation of a 5-axis machine. These systems must be highly accurate and able to regulate each axis independently to ensure the precision required for 5-axis machining. The control system operates using a CNC controller that runs the machine’s software and manages the machine’s movements. The use of advanced control systems with advanced software tools provides manufacturers with more control over the cutting process, improving efficiency, and quality.
Tooling:
Tooling is another essential component of a 5-axis machine. The tooling must be designed to reach every feature of the part without collisions. Manufacturers use a range of cutting tools, such as end mills, ball mills, drills, and reamers, to cut the workpiece. The correct selection of these tools contributes to the quality of the final product produced.
The proper maintenance of each of these components is crucial for the success of 5-axis machining. Regular machine maintenance ensures optimal performance, while proper tool selection and workholding techniques can improve accuracy and stability during the cutting process, ultimately leading to a higher quality and faster production process.
-
3.Applications of 5-Axis Machining
5-axis machining technology has numerous applications in various industries. Its ability to cut complex geometries in a single setup has allowed manufacturers to create parts with high precision, tighter tolerances, and improved surface finishes. Here are some of the industries where 5-axis machining technology finds its applications:
- Aerospace:
Aerospace is one of the primary industries that relies on 5-axis machining technology. This industry is constantly pushing the boundaries of manufacturing to create parts with complex geometries, materials, and reduced weight. The technology has enabled manufacturers to produce critical aircraft components with tight tolerances, such as blades, engine components, and structural parts. - Medical:
The medical industry has benefitted significantly from the advanced capabilities of 5-axis machining technology. The technology enables the production of customized implants and prosthetics with complex geometries. It has also revolutionized surgical tools and devices by enabling manufacturers to produce intricate parts with high precision. - Automotive:
5-axis machining technology has gained prominence in the automotive industry for its ability to create complex and precise automotive parts, such as fuel injectors, engine components, and powertrain systems. The technology has also enabled the production of lightweight, high-performance automotive parts, improving car performance and fuel efficiency. - Mold-making:
Mold-making is another area that has benefitted from 5-axis machining technology. The technology enables the production of complex molds with high precision, which are used to create complex plastic parts. The reduction in production time along with the improved surface finish, makes the 5-axis technology crucial for manufacturers. - Other industries:
5-axis machining technology has applications in several other industries, including defense and consumer goods. It is used to create parts for missile systems, robotics, and other advanced electronic systems. In the consumer goods industry, the technology is being used to make products and parts with more complex geometries and fine details, which was hard to achieve through traditional methods.
Overall, 5-axis machining technology offers numerous benefits to the manufacturing industry, and its applications are growing every day. Its ability to create complex shapes with high precision has made it an essential tool in modern manufacturing.
-
4.Benefits of 5-Axis Machining
The benefits of 5-axis machining technology are numerous, ranging from increased efficiency to improved surface finish. Here are some of the key advantages of using 5-axis machining technology:
- Increased efficiency:
5-axis machining technology can improve productivity by reducing the number of setups needed to produce complex parts. It allows the creation of parts in a single setup, eliminating the need for multiple setups, reducing part handling, and tool changeover. This reduces production times, overall lead time, and saves significant costs. - Greater accuracy:
5-axis machining technology allows for high levels of accuracy, making it a crucial tool for the production of complex geometries with tight tolerances. The technology provides more degrees of freedom for the cutting tool, reducing the risk of errors and producing precise parts with complex geometries. - Improved Surface Finish:
5-axis machining technology allows for more efficient and accurate cutting on complex shapes, yielding better surface finishes than other traditional machining methods. This reduces the need for manual finishing operations such as sanding, polishing, which saves time, and ultimately leads to a higher quality end product. - Reduced setup times:
One of the significant benefits of 5-axis machining technology is its capability of reducing the time taken for setting up a machine. With 5-axis machining technology, you can reduce the amount of operator-dependent adjustment, simplifying the setup process, and allowing for more production, with fewer mistakes; thus, lowering production time.
The benefits of 5-axis technology extend beyond the four above, there are numerous applications in various industries, and as technology continues to improve continually, there will be significant progress in higher efficiency, accuracy, and cost-cutting applications.
-
5.Choosing the Right 5-Axis Machine
Choosing the right 5-axis machine is crucial for maximizing the benefits of this technology. Several factors need to be considered when selecting a 5-axis machine, such as the material that will be machined, the size and complexity of the parts, the accuracy required, and the production volume. Here are some factors to consider when choosing a 5-axis machine:
- Rigidity and accuracy:
The machine’s rigidity and accuracy are critical as it ensures the production of quality parts. The machine must be able to maintain high accuracy while cutting complex geometries, and its structure should be robust enough to handle the forces generated during the cutting process. - Size and speed:
When selecting a 5-axis machine, it is important to consider the size of the machine, as it should be appropriately sized for the parts being machined. The spindle speed should also be considered as it plays a crucial role in the cutting process’s overall efficiency. - Control systems:
The control system of a 5-axis machine is another essential consideration. The control system should be capable of regulating each axis independently, have simple and intuitive software and allow for high speeds with long tool life, all compatible with the machining processes. - Tooling options:
Different 5-axis machines may require varying types of tooling, which can impact production time and cost. It is essential to consider the availability of compatible tooling for the 5-axis machine model and the specific needs of the machining job.
Types of 5-axis machines:
There are several types of 5-axis machines, such as table-table, head-table, and head-head machines. Table-table 5-axis machines have both the spindle head and workpiece mounted on a tilting swiveling table. Head-table 5-axis machines fix the spindle on the carriage structure and pivot the workpiece. Head-head 5-axis machines fix the spindle and workpiece on the machine’s axes, allowing the cutting tool angle to change in relation to the angle of the part.
Click on the V1 Prototype website to gain more 5 Axis CNC Machining Services information.
-
6.Programming for 5-Axis Machining
Programming for 5-axis machining requires CAD/CAM software that generates complex toolpath strategies for the cutting tool. The software allows manufacturers to develop 3D models of parts and create tool paths for the cutting tools to follow. Here are the key elements of programming for 5-axis machining:
CAD/CAM software:
CAD/CAM software is the primary tool for programming 5-axis machines. The software generates tool paths for the cutting tool based on the input geometry, speeds, and feeds, along with other critical considerations for high-speed cutting. This software accounts for the machine’s axis movements and ensures that the tool is in contact with the material throughout the operation.
Programming considerations:
When programming 5-axis machines, certain considerations are crucial to ensure accuracy and efficiency. Some of the programming considerations are:
- Tool selection:
The chosen cutting tool should provide sufficient reach to access all the geometric features of the part. - Workholding and fixtures:
Proper work holding and fixtures are required to maintain parts at a desired orientation, reducing the risk of collisions during the cutting process. - Axis motion:
It is vital to take into account the movement of each axis and develop a program that will minimize repositioning and optimize the tool’s path, thus increasing efficiency. - Cutting parameters:
Cutting parameters are also critical to successfully program 5-axis machines. Proper combination of speed, feed, cutting depth and other factors have to be considered, ensuring efficient chip evacuation and minimum tool wear.
-
7.Common Challenges with 5-Axis Machining
5-axis machining delivers many benefits, but there are challenges that need to be overcome to maximize these advantages. Here are some of the most common challenges with 5-axis machining:
- Collision Detection:
Collision detection refers to the risk of collision between the cutting tool and the workpiece or other machine components. The movement of the machine on several axes means that there is an increased risk of collisions. Efficient programming and simulation software that alerts the operator to impending collisions can help mitigate the risk of any damage while also ensuring operator safety. - Tool Positioning:
With 5-axis machining, the cutting tool approaches the workpiece from multiple angles, which can lead to tool position errors. These errors can cause premature tool failure, damage to the workpiece, and lower quality parts. Proper tool selection along with a rigorous toolpath calculation and optimizing strategy can help reduce the risk of tool positioning errors. - Surface Quality:
5-axis machining with an improper cutting strategy or improperly chosen tool selection can sometimes cause surface errors on the workpiece. Quality surface finishes require consideration of many parameters, such as cutting speed, spindle RPM, feed rates, chip evacuation, and material properties. Proper programming and a review of tooling, spindle, and workpiece compatibility are crucial for achieving the best possible finished workpiece quality.
-
8.Tips for Successful 5-Axis Machining
Successful 5-axis machining requires a combination of several key factors, including the use of good machining practices and high-quality machining equipment, along with efficient process planning, and skilled operators. Here are some tips for achieving success in 5-axis machining:
- Machine Maintenance:
Proper machine maintenance is essential for effective 5-axis machining. Regular maintenance checks, including checking axis alignment, lubrication of bearings, and verifying machine controls, are critical for reducing machine downtime and ensuring the machine’s efficiency and longevity. - Tool Selection:
Tool selection plays an important role in 5-axis machining. The appropriate tool selection ensures minimal tool wear, tolerable surface finish, and high accuracy. High-quality tooling also reduces machine downtime, saving costs and reducing waste. - Workholding Techniques:
Workholding techniques such as proper fixture and workpiece positioning, have a significant impact on the success of 5-axis machining. Workpieces must be held securely in position to ensure the cutting tool reaches every required point on the workpiece. Proper machining fixture design, clamping locations, and fixture pressure must be considered for optimal results. - Efficient Programming:
Efficient programming is key in reducing production time, achieving desired tolerances, and ensuring part accuracy. This includes selecting the correct cutting strategies, toolpaths, programming feeds and speeds, and ensuring the correct tool is selected for the desired surface finishes. - Skilled Operators:
Skilled operators are crucial for successful 5-axis machining. Advanced training in programming, operating and maintenance, and understanding the key operational factors of the machine such as vibration, wear, and positioning will enable the operator to detect and correct any issues with the machine in a timely manner.
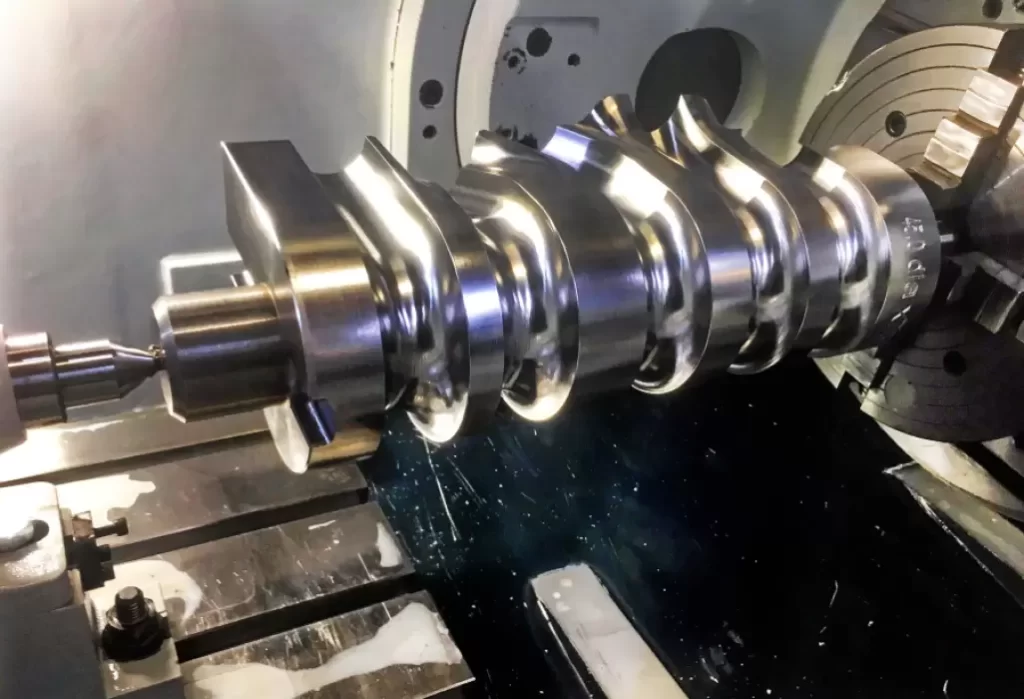
-
9.Conclusion
5-axis machining is an advanced technology that provides manufacturers with significant advantages, such as accuracy, efficiency, and flexibility in complex part production. As 5-axis machining continues to evolve, new developments will shape the technology’s future.
Future developments in 5-axis machining will focus on the advancement of cutting-edge software and the use of artificial intelligence (AI). With these advances, manufacturers will be able to improve upon existing programs, integrate sophisticated algorithms and models, streamline the production process by optimizing feeds and speeds, and ultimately drive continuous improvement in the overall manufacturing process.
In conclusion, 5-axis machining technology has proven to be a powerful tool for manufacturing, expanding the possibilities of part design and increasing efficiency in part manufacturing. As technology advances, this manufacturing technology continues to evolve, and new applications continue to develop, such as the integration of AI and advanced software. To maximize the benefits of 5-axis machining, manufacturers must leverage the technology’s advantages while also being mindful of potential challenges and the need to upgrade their hardware, software, and skilled labor. By partnering with a trusted 5-axis machining partner and optimizing processes, manufacturers can fully realize the technology’s advantages and stay ahead in today’s competitive market.