Table of Contents:
- Introduction
- Basic Principles of Injection Moulding
- Applications of Injection Moulding Process
- Advancements in Injection Moulding Process
- Troubleshooting Injection Moulding Process
- Conclusion
-
1.Introduction
Injection moulding is a manufacturing process that involves injecting molten materials into a mould to produce complex geometries. This technique is widely used in various industries such as automotive, packaging, medical devices, consumer goods, aerospace, and electronics. This article will provide an overview of the injection moulding process, including its basic principles, applications, advancements, and troubleshooting.
-
2. Basic Principles of Injection Moulding
A. Raw Materials Used in Injection Moulding
The raw materials used in injection moulding depend on the specific application and material properties required. Common thermoplastics used include polypropylene (PP), polystyrene (PS), and polyethylene (PE). Thermoplastics are preferred because they can be easily melted and recycled.
B. Equipment and Tools Required
Injection moulding machines consist of multiple components including a hopper, heater, injection unit, clamping unit, and ejection unit. The moulds themselves are also complex, often featuring small, intricate details which require precision machining.
C. Process Steps
The injection moulding process consists of several steps including melting the plastic material, injecting the molten material into the mould, cooling and solidifying the material, and finally ejecting the finished product.
D. Types of Moulding
The two main types of injection moulding techniques are traditional moulding and insert moulding. Traditional moulding involves injecting the molten material into a single mould cavity. Insert moulding, on the other hand, involves inserting pre-formed parts or inserts into the mould prior to the injection process.
-
3. Applications of Injection Moulding Process
A. Automotive Industry
Injection moulding is widely used in the automotive industry to produce components such as bumpers, dashboards, and interior trims. These components require high strength and durability to withstand the demands of the automotive environment.
B. Consumer Goods
Consumer goods such as toys, home appliances, and personal care products utilize injection moulding due to the ability to quickly produce large quantities of products with high accuracy and consistent quality.
C. Medical Industry
The medical industry relies on injection moulding for the production of precision medical devices and components that require sterile manufacturing environments. Medical grade plastics such as polyetherimide (PEI) and polycarbonate (PC) are often used due to their biocompatibility and mechanical properties.
D. Packaging Industry
Injection moulding is widely used in the packaging industry to produce containers, caps, and closures. The use of injection moulding has allowed for improved sustainability and recyclability of packaging materials.
E. Electronics Industry
The electronics industry relies on injection moulding for the production of components such as micro switches, connectors, and relays. The use of injection moulding allows for the manufacturing of high precision components that meet strict industry requirements.
F. Aerospace Industry
The aerospace industry uses injection moulding for the manufacturing of components such as air ducts, housings, and brackets. Injection moulding allows for the production of lightweight components with high strength-to-weight ratios.
-
4. Advancements in Injection Moulding Process
A. Materials and Technology Innovations
Recent advancements in materials and technology have led to the development of new materials such as carbon fiber reinforced plastics (CFRP) and multi-component injection moulding (MCIM). These innovations have allowed for the production of lighter and more complex components with improved functionality.
B. Sustainable Inject Moulding
Sustainability is becoming an increasingly important consideration in the injection moulding process. The use of biodegradable and recycled materials, as well as energy efficient production techniques, are becoming more common in the industry.
C. Virtual Prototyping
Virtual prototyping allows for the simulation of the injection moulding process prior to actual production. This allows for the detection of potential defects and optimization of the production process.
D. Automation and Robotics
Automation and robotics technology are becoming more commonly used in injection moulding, allowing for increased production efficiency and reduced labour costs.
If you want more about Injection Moulding Process information ,You can click on the V1 Prototype website to find it.
-
5. Troubleshooting Injection Moulding Process
A. Common Defects
Common defects in the injection moulding process include warping, flash, sink marks, and air bubbles. The causes of these defects may involve improper material selection, inadequate mould design, or processing flaws.
B. Causes of Defects
Identifying the root cause of injection moulding defects can be a complex process, often involving the analysis of numerous parameters such as material properties, processing conditions, and mould design. Understanding the causes of defects is essential for implementing appropriate corrective actions.
C. Solutions to Defects
Solving injection moulding defects requires a systematic approach involving careful analysis of the problem and identification of the root cause. Appropriate corrective actions can then be implemented, such as adjusting material properties, modifying processing conditions, or re-designing the mould.
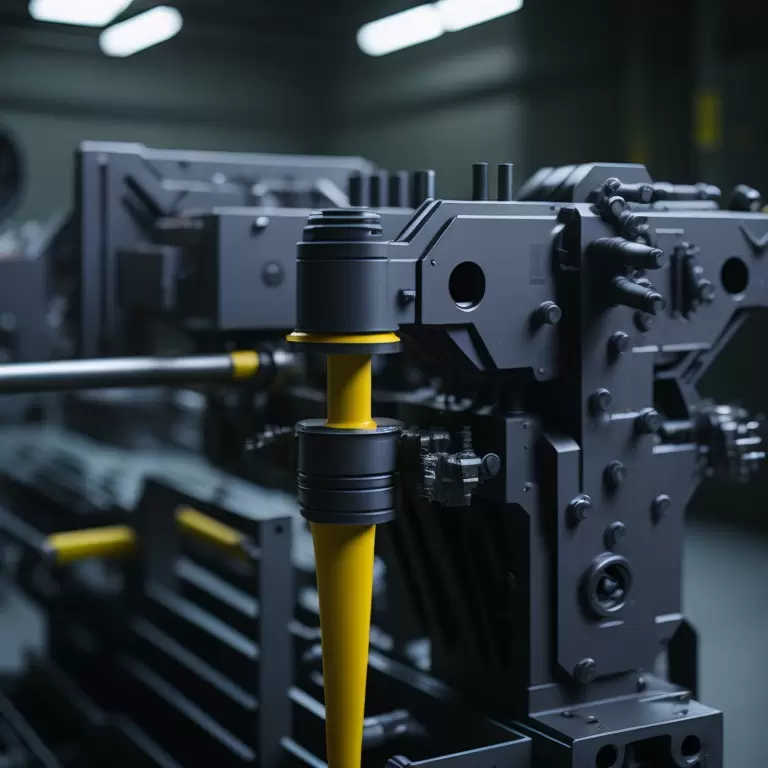
-
6. Conclusion
Injection moulding is a versatile and widely used manufacturing process with applications in numerous industries. Advances in materials and technology, as well as increased focus on sustainability and automation, are driving innovation and improvement in the injection moulding process. While troubleshooting defects can be complex, understanding the fundamentals of the process and being able to identify and correct issues is crucial for achieving consistent and high-quality results.
The injection moulding process has become an essential part of modern manufacturing, offering a fast, reliable and cost-effective way to produce complex and precise products. With continued innovation and focus on sustainability and efficiency, the injection moulding process is expected to continue to play a critical role in manufacturing for years to come.
Overall, the injection moulding process is an efficient, versatile, and effective manufacturing process with a wide range of applications across various industries. With advancements in materials, technology, and sustainable manufacturing, injection moulding is well-positioned to continue delivering high-quality products for years to come. As companies continue to invest in and refine the injection moulding process, the possibilities for innovation and progress in manufacturing are endless.