Brief Introduction of Die Cast Zinc Alloys and Test Methods
Introduction
Die casting is a versatile and widely used manufacturing process that involves injecting molten metal into a mold under high pressure to produce intricate and high-quality metal components. Zinc alloys are one of the most popular materials for die casting due to their excellent properties and ease of casting. In this article, we will provide a brief introduction to die cast zinc alloys, their advantages, and the different test methods used to ensure the quality and integrity of the die-cast components.
Die Cast Zinc Alloys: Advantages and Properties
Zinc alloys are a family of materials that offer a range of mechanical properties suitable for various applications. The most common zinc alloy used in die casting is Zamak, which is a combination of zinc, aluminum, magnesium, and copper. Zamak alloys have several advantages that make them ideal for die casting:
- High Fluidity: Zamak alloys have excellent fluidity, allowing them to flow into intricate mold cavities with ease. This property enables the production of complex and detailed parts with tight tolerances.
- Dimensional Stability: Die cast zinc alloys exhibit minimal shrinkage upon solidification, resulting in high dimensional accuracy and consistency of the finished parts.
- Surface Finish: Zamak alloys produce parts with a smooth and aesthetically pleasing surface finish, reducing the need for additional post-processing and finishing.
- Excellent Mechanical Properties: Zamak alloys offer good strength, hardness, and impact resistance, making them suitable for a wide range of applications.
- Cost-Effectiveness: Zinc is relatively inexpensive compared to other metals, making Zamak alloys a cost-effective choice for high-volume production.
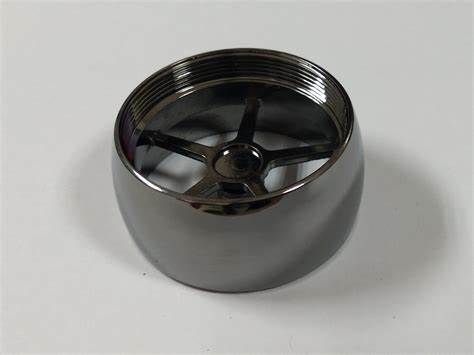
Test Methods for Die Cast Zinc Alloys
Ensuring the quality and performance of die cast zinc alloy components requires comprehensive testing throughout the manufacturing process. Several test methods are commonly used to evaluate the properties and characteristics of the die-cast parts:
1. Visual Inspection
Visual inspection is a simple yet effective test method to identify any visible defects or irregularities on the surface of the die-cast components. This inspection involves examining the parts for defects like surface blemishes, porosity, flash, and dimensional inconsistencies.
2. Dimensional Measurement
Accurate dimensional measurement is crucial to verify that the die-cast parts meet the required specifications. Coordinate measuring machines (CMM) and other precise measuring tools are used to assess dimensional accuracy and ensure that the parts adhere to design specifications.
3. Tensile Testing
Tensile testing is used to evaluate the mechanical properties of the die-cast zinc alloy, including tensile strength, yield strength, and elongation. Tensile specimens are extracted from the die-cast parts, and a force is applied until the sample fractures, allowing for the measurement of mechanical properties.
4. X-Ray Inspection
X-ray inspection is a non-destructive testing method used to identify internal defects, such as porosity and voids, that may not be visible on the surface. This inspection technique helps ensure the integrity and quality of the die-cast components.
5. Surface Roughness Measurement
Surface roughness measurement is performed to assess the smoothness and texture of the die-cast parts' surface. This measurement is crucial in industries where surface aesthetics play a significant role.
6. Chemical Analysis
Chemical analysis is conducted to verify the composition of the die-cast zinc alloy and ensure that it meets the required specifications and material standards.
7. Pressure Testing
Pressure testing is used to assess the leak-tightness and integrity of die-cast components intended for applications involving fluids or gases. The parts are subjected to a controlled pressure to determine if there are any leaks or defects.
8. Hardness Testing
Hardness testing measures the hardness of the die-cast parts, which is an essential property for evaluating wear resistance and durability.
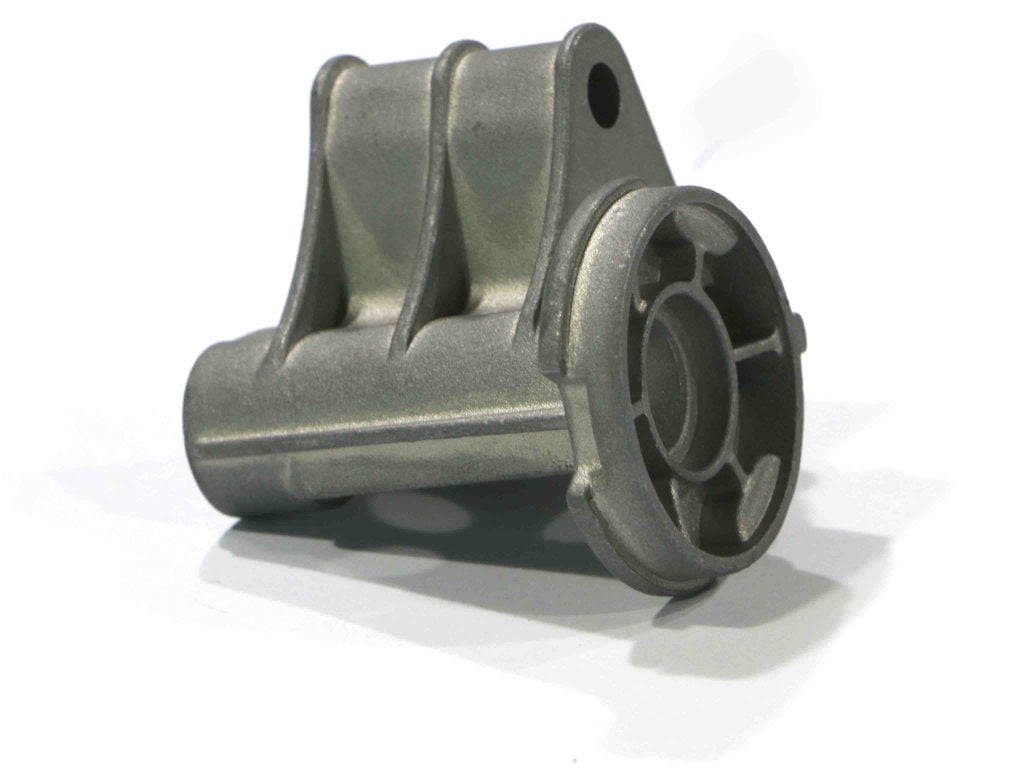
Frequently Asked Questions
Q1. What are the advantages of die cast zinc alloys?
Die cast zinc alloys, particularly Zamak alloys, offer several advantages that make them highly suitable for die casting applications:
- High Fluidity: Zamak alloys have excellent fluidity, enabling them to fill intricate mold cavities with precision and accuracy. This property is crucial for producing complex and detailed parts.
- Dimensional Stability: Die cast zinc alloys exhibit minimal shrinkage upon solidification, resulting in high dimensional accuracy and consistency of the finished parts. This ensures that the die-cast components conform to the intended design specifications.
- Surface Finish: Zamak alloys produce parts with a smooth and aesthetically pleasing surface finish. This characteristic reduces the need for additional post-processing and finishing operations, saving time and costs in production.
- Mechanical Properties: Die cast zinc alloys offer good strength, hardness, and impact resistance, making them suitable for a wide range of applications. The mechanical properties of the alloys can be tailored by adjusting the alloy composition and processing parameters.
- Cost-Effectiveness: Zinc is an abundant and relatively inexpensive metal, making Zamak alloys a cost-effective choice for high-volume production. This cost-effectiveness contributes to the overall economic viability of the die casting process.
Q2. How is visual inspection used to assess the quality of die-cast parts?
Visual inspection is a critical test method used to identify any visible defects or irregularities on the surface of the die-cast components. Trained inspectors visually examine the parts under adequate lighting conditions to detect defects like surface blemishes, porosity, flash, and dimensional inconsistencies. The inspection ensures that the die-cast parts meet the required quality standards and adhere to design specifications. Visual inspection is an essential step in the quality control process and allows for early detection of potential issues that may require further testing or corrective actions.
Q3. What are the common mechanical properties evaluated through tensile testing?
Tensile testing is a widely used method to evaluate the mechanical properties of die-cast zinc alloys. The key mechanical properties evaluated through tensile testing include:
- Tensile Strength: The tensile strength is the maximum amount of tensile stress a material can withstand before fracturing. It indicates the material's ability to resist pulling forces and is a measure of its structural integrity.
- Yield Strength: Yield strength is the stress at which a material begins to exhibit plastic deformation or permanent deformation without fracturing. It is an essential property for determining the material's ability to return to its original shape after being subjected to a load.
- Elongation: Elongation represents the percentage increase in length of a material before it fractures under tensile stress. It is an indicator of the material's ductility and ability to withstand deformation without fracturing.
- Young's Modulus: Young's modulus, also known as the modulus of elasticity, is a measure of the material's stiffness or resistance to deformation in response to an applied force. It is a critical property for assessing the material's structural behavior under load.
Tensile testing provides valuable data on the mechanical behavior of die-cast zinc alloys and helps ensure that the parts possess the required strength and performance characteristics for their intended applications.
Q4. Why is X-ray inspection crucial for die-cast components?
X-ray inspection is a non-destructive testing method used to identify internal defects, such as porosity, voids, and inclusions, that may not be visible on the surface of the die-cast components. These internal defects can compromise the integrity and quality of the parts and may lead to potential failures during service. X-ray inspection allows for a comprehensive evaluation of the part's internal structure without causing damage, ensuring that the components meet the required quality standards. This inspection technique is particularly useful for critical components used in safety-critical applications, where any defects or imperfections could have severe consequences. X-ray inspection provides valuable insights into the internal quality of die-cast components, allowing manufacturers to take corrective measures and deliver high-quality and reliable parts to their customers.
Conclusion
Die cast zinc alloys, particularly Zamak alloys, offer numerous advantages that make them a preferred choice for various die casting applications. Their high fluidity, dimensional stability, excellent surface finish, and cost-effectiveness make them suitable for producing complex and intricate metal components. To ensure the quality and integrity of die-cast parts, comprehensive testing methods are employed throughout the manufacturing process. Visual inspection, dimensional measurement, tensile testing, X-ray inspection, and other test methods are used to evaluate the properties and characteristics of die-cast zinc alloy components. By adhering to rigorous testing and quality control procedures, manufacturers can deliver high-quality die-cast components that meet the required specifications and exceed customer expectations.