Copper sheet metal is a versatile and highly useful material that is widely used in various industries, including construction, manufacturing, and engineering. Its unique properties make it ideal for applications that require high thermal and electrical conductivity, corrosion resistance, and durability. In this article, we will discuss the properties, uses, and fabrication techniques of copper sheet metal.
- Properties of Copper Sheet Metal
- Uses of Copper Sheet Metal
- Fabrication Techniques for Copper Sheet Metal
- Advantages and Disadvantages of Copper Sheet Metal
- Conclusion
Properties of Copper Sheet Metal
Copper is a reddish-brown metal with excellent thermal and electrical conductivity, high ductility, and corrosion resistance. Copper sheet metal is a thin, flat piece of copper that is available in various thicknesses, sizes, and grades. The following are some of the properties of copper sheet metal:
• High Thermal and Electrical Conductivity: Copper is an excellent conductor of heat and electricity, making it ideal for applications that require heat dissipation or electrical transmission.
• Ductility: Copper sheet metal is highly ductile, meaning that it can be easily formed and shaped into different configurations without breaking or cracking.
• Corrosion Resistance: Copper is highly resistant to corrosion, making it ideal for applications that require long-term durability in harsh environments.
• Malleability: Copper sheet metal is highly malleable, meaning that it can be easily shaped and formed into different configurations without cracking or breaking.
• Durability: Copper sheet metal is highly durable and resistant to wear and tear, making it ideal for applications that require long-term use.
Uses of Copper Sheet Metal
Copper sheet metal is used in various applications, including:
• Roofing and Cladding: Copper sheet metal is commonly used in roofing and cladding applications due to its corrosion resistance and durability.
• Electrical and Electronic Applications: Copper sheet metal is widely used in electrical and electronic applications due to its high thermal and electrical conductivity.
• Automotive Industry: Copper sheet metal is used in various automotive applications, including radiators, heat exchangers, and brake lines.
• Industrial Applications: Copper sheet metal is used in various industrial applications, including heat exchangers, boilers, and pipes.
• Decorative Applications: Copper sheet metal is commonly used in decorative applications, including wall panels, sculpture, and jewelry.
Fabrication Techniques for Copper Sheet Metal
Copper sheet metal can be fabricated using various techniques, including:
• Cutting: Copper sheet metal can be cut using various methods, including shearing, laser cutting, and plasma cutting.
• Bending: Copper sheet metal can be bent into different configurations using various techniques, including press braking, roll bending, and stretch bending.
• Forming: Copper sheet metal can be formed into different shapes and configurations using various techniques, including hydroforming, spinning, and stamping.
• Joining: Copper sheet metal can be joined using various methods, including welding, soldering, and brazing.
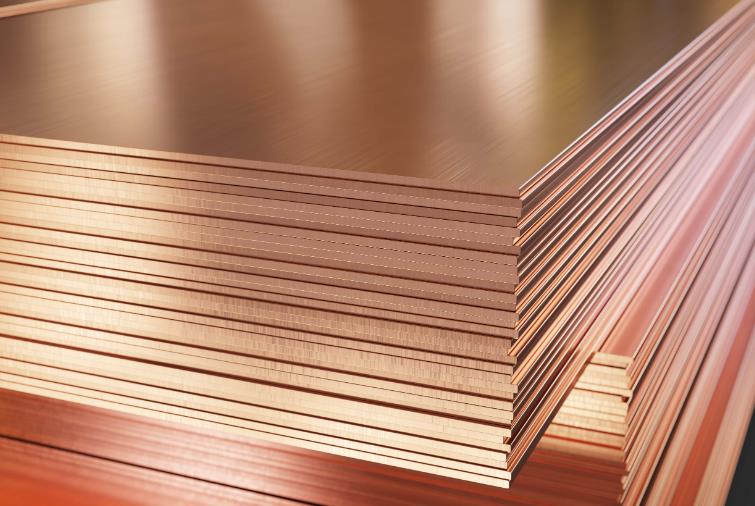
Advantages and Disadvantages of Copper Sheet Metal
Copper sheet metal offers several advantages and disadvantages, including:
Advantages:
• Excellent thermal and electrical conductivity
• Corrosion resistance
• Durability
• High ductility and malleability
• Recyclable
Disadvantages:
• Expensive compared to other materials
• Prone to tarnishing and discoloration over time
• Requires frequent maintenance to maintain its appearance
Conclusion
Copper sheet metal is a versatile and highly useful material that is widely used in various industries due to its unique properties, including high thermal and electrical conductivity, corrosion resistance, and durability.