Introduction
Die casting is a versatile manufacturing process used to produce metal components with high precision and complex geometries. The success of the die casting process relies heavily on the design specifications and the choice of metal materials. In this comprehensive guide, we will explore the crucial factors involved in designing die castings and selecting appropriate metal materials for various applications.
Design Specifications for Die Castings
1. Wall Thickness
Maintaining uniform and appropriate wall thickness is essential for the successful die casting process. Wall thickness impacts the flow of molten metal during injection, solidification, and cooling. Ideally, uniform wall thickness should be achieved to avoid issues like shrinkage, porosity, and warpage.
2. Draft Angles
Draft angles are necessary for easy ejection of the part from the mold. Adequate draft angles prevent the part from sticking to the mold, reducing the risk of defects and improving the overall production efficiency.
3. Fillets and Radii
Fillets and radii at sharp corners and edges help distribute stress and reduce the risk of stress concentration, which can lead to premature failure of the part.
4. Ribs and Bosses
Ribs provide additional strength to the part without significantly increasing its weight, while bosses act as mounting points or inserts for other components.
5. Undercuts and Cores
The design should avoid complex undercuts or features that require complex cores, as they can complicate the mold design and increase production costs.
6. Gating and Venting
Proper gating and venting designs are crucial to ensure the uniform filling of the mold cavity and to minimize the risk of defects like porosity and shrinkage.
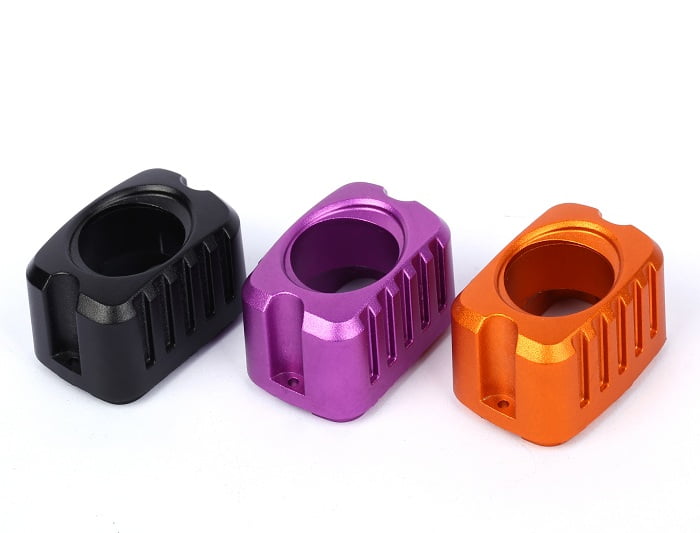
Metal Materials for Die Castings
1. Aluminum Alloys
Aluminum alloys are one of the most commonly used materials for die castings. They offer a good balance of strength, lightweight, and corrosion resistance, making them suitable for various applications, including automotive, electronics, and consumer goods.
2. Zinc Alloys
Zinc alloys are known for their excellent fluidity, allowing for intricate and thin-walled designs to be cast with ease. They are often used in applications where high precision and surface finish are required, such as in the automotive and electronics industries.
3. Magnesium Alloys
Magnesium alloys offer exceptional strength-to-weight ratios, making them ideal for applications where lightweight and high-performance components are needed, such as in aerospace and automotive industries.
4. Copper Alloys
Copper alloys are preferred for their excellent thermal and electrical conductivity, making them suitable for electrical and electronic components.
5. Brass Alloys
Brass alloys, a combination of copper and zinc, offer good machinability and corrosion resistance, making them suitable for decorative and functional components.
6. Steel Alloys
Steel alloys can be used for die castings in certain applications where higher strength and durability are required.
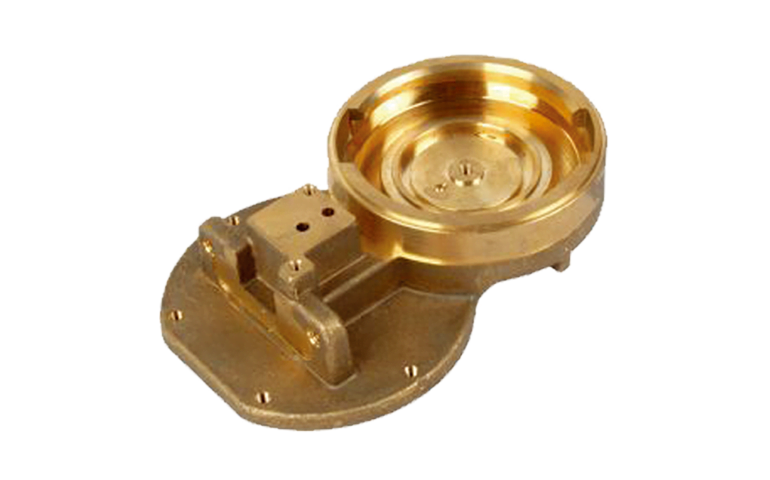
Frequently Asked Questions
Q1. What are the key design specifications for die castings?
The design specifications for die castings are crucial for achieving successful and defect-free parts. Some key design specifications include:
- Wall Thickness: Maintaining uniform and appropriate wall thickness is essential for proper flow of molten metal and to avoid defects like shrinkage and porosity.
- Draft Angles: Adequate draft angles allow for easy ejection of the part from the mold, reducing the risk of sticking and defects.
- Fillets and Radii: Incorporating fillets and radii at sharp corners and edges helps distribute stress and prevents stress concentration, enhancing the part's durability.
- Ribs and Bosses: Ribs add strength to the part without increasing its weight significantly, while bosses serve as mounting points or inserts for other components.
- Undercuts and Cores: The design should avoid complex undercuts or features that require complex cores, as they can complicate the mold design and increase production costs.
- Gating and Venting: Proper gating and venting designs are critical to ensure the uniform filling of the mold cavity and to minimize defects like porosity and shrinkage.
Q2. Which metal materials are commonly used for die castings?
Several metal materials are commonly used for die castings, each offering specific properties suitable for different applications:
- Aluminum Alloys: Known for their good balance of strength, lightweight, and corrosion resistance, aluminum alloys are widely used in various industries.
- Zinc Alloys: Zinc alloys are preferred for applications requiring high precision and surface finish, thanks to their excellent fluidity.
- Magnesium Alloys: Magnesium alloys offer exceptional strength-to-weight ratios, making them ideal for lightweight and high-performance components.
- Copper Alloys: Copper alloys are chosen for their excellent thermal and electrical conductivity, making them suitable for electrical and electronic components.
- Brass Alloys: A combination of copper and zinc, brass alloys provide good machinability and corrosion resistance, making them suitable for decorative and functional components.
- Steel Alloys: Steel alloys are used in specific applications requiring higher strength and durability.
Q3. What factors should be considered when selecting metal materials for die castings?
When selecting metal materials for die castings, several factors should be considered:
- Application Requirements: Consider the specific mechanical, thermal, and electrical properties required for the application.
- Cost: Evaluate the cost-effectiveness of the material in relation to the desired properties.
- Manufacturability: Assess the ease of die casting the material and its flowability during injection.
- Surface Finish: Consider the desired surface finish and aesthetics of the final part.
- Weight: Evaluate the weight requirements and consider materials with suitable strength-to-weight ratios.
- Corrosion Resistance: Determine if the part will be exposed to harsh environments and select materials with appropriate corrosion resistance.
- Recyclability: Consider the sustainability and recyclability of the material.
Q4. How can design optimization improve the quality of die castings?
Design optimization plays a crucial role in improving the quality of die castings. By carefully considering design specifications, such as wall thickness, draft angles, fillets, and ribs, manufacturers can ensure a uniform and defect-free filling of the mold cavity. Proper gating and venting designs prevent defects like porosity and shrinkage. Additionally, well-designed mold cores and undercuts contribute to easier ejection and reduce the risk of defects. Design optimization also allows for the production of complex geometries with tight tolerances, improving the overall performance and functionality of the final part. By leveraging design expertise and experience, manufacturers can enhance the quality, efficiency, and cost-effectiveness of the die casting process.