Table of Contents:
- Introduction to Rapid Injection Molding
- The Process of Rapid Injection Molding
- Advantages of Rapid Injection Molding
- Applications of Rapid Injection Molding
- Considerations for Choosing a Rapid Injection Molding Provider
- Future of Rapid Injection Molding
- Conclusion
-
1.Introduction to Rapid Injection Molding
Rapid injection molding is a manufacturing process that allows for the quick production of injection molded parts using an accelerated approach. It involves the use of pre-existing molds or tooling, which are typically made from aluminum or other low-cost materials, to produce parts in a matter of days rather than weeks or months.
Rapid injection molding is important because it offers a way for companies to rapidly develop and produce high-quality plastic parts without the high cost and time investment associated with traditional injection molding methods. This is particularly useful for small-scale production runs, prototyping, and product testing.
The benefits of rapid injection molding include reduced lead times, lower cost of production, improved design flexibility, and greater production efficiency. With rapid injection molding, companies can get their products to market faster, iterate on designs more quickly, and ultimately achieve greater success in a highly competitive marketplace.
-
2.The Process of Rapid Injection Molding
The process of rapid injection molding typically involves four main stages:
- Designing the Mold: In this stage, the mold is designed using computer-aided design (CAD) software. The mold design must be optimized for rapid injection molding, taking into account the specific material and part requirements. The mold is typically made from aluminum or other low-cost materials to reduce production time and cost.
- Prototyping and Testing: Once the mold design is finalized, a prototype is created using the mold. This prototype is then tested to ensure that it meets the desired specifications and requirements. Any necessary adjustments are made to the mold design based on the results of the testing.
- Injection Molding Production: Once the mold design and prototype have been finalized, the actual injection molding production process begins. The mold is loaded into the injection molding machine, and the plastic material is injected into the mold at high pressure. The part is then cooled and ejected from the mold.
- Finishing and Assembly: The finished parts are then subjected to any necessary finishing processes, such as trimming or sanding, to remove any excess material or imperfections. The parts may also undergo assembly or packaging processes, depending on the final product requirements.
Overall, the process of rapid injection molding is highly streamlined and efficient, allowing for the rapid production of high-quality plastic parts with minimal lead time and cost.
-
3.Advantages of Rapid Injection Molding
Rapid injection molding offers several advantages over traditional injection molding methods, including:
- Reduced Lead Times: One of the primary benefits of rapid injection molding is its ability to significantly reduce lead times for the production of plastic parts. With traditional injection molding methods, the process can take weeks or even months to complete. In contrast, rapid injection molding can produce parts in a matter of days, allowing companies to get their products to market faster and stay ahead of the competition.
- Lower Cost of Production: Rapid injection molding typically involves lower tooling costs, as the molds used are made from lower-cost materials such as aluminum. Additionally, the reduced lead times associated with rapid injection molding can result in lower labor costs and increased productivity, further reducing the overall cost of production.
- Improved Design Flexibility: Rapid injection molding offers greater design flexibility than traditional injection molding methods. This is because rapid injection molding allows for quicker iterations and design changes, which can be made in a matter of days rather than weeks or months. This allows companies to quickly refine and improve their products to meet evolving customer needs and preferences.
- Greater Production Efficiency: Rapid injection molding is a highly efficient process, with minimal waste and a streamlined production flow. This allows for greater production efficiency, with faster cycle times and increased throughput. As a result, companies can produce more parts in less time, with less waste, and at a lower cost.
-
4.Applications of Rapid Injection Molding
Rapid injection molding has a wide range of applications across various industries, including:
- Automotive Industry: Rapid injection molding is used extensively in the automotive industry for the production of a variety of plastic parts, such as interior components, trim pieces, and under-the-hood components. The reduced lead times and lower cost of production associated with rapid injection molding make it an attractive option for automotive manufacturers looking to streamline their production processes.
- Medical Industry: Rapid injection molding is also used in the medical industry for the production of medical devices and components. The ability to quickly produce high-quality parts with tight tolerances is particularly important in the medical industry, where precision and accuracy are critical.
- Consumer Electronics: Rapid injection molding is commonly used in the production of consumer electronics, such as mobile phone cases, laptop shells, and other electronic components. The flexibility and speed of the process make it ideal for consumer electronics manufacturers looking to quickly iterate on designs and bring new products to market.
- Aerospace Industry: Rapid injection molding is also used in the aerospace industry for the production of a variety of plastic components, such as interior panels and trim pieces. The ability to quickly produce high-quality parts with minimal waste and at a lower cost makes rapid injection molding an attractive option for aerospace manufacturers looking to streamline their production processes.
-
5.Considerations for Choosing a Rapid Injection Molding Provider
When choosing a rapid injection molding provider, there are several considerations to keep in mind, including:
- Quality and Accuracy: It is essential to choose a provider that can deliver high-quality parts with tight tolerances and consistent accuracy. Look for a provider with a proven track record of delivering quality parts and who utilizes advanced quality control processes to ensure that each part meets the required specifications.
- Speed of Production: Rapid injection molding is all about speed, so it’s essential to choose a provider that can deliver parts quickly and efficiently. Look for a provider that can offer fast turnaround times without sacrificing quality or accuracy.
- Cost and Affordability: While rapid injection molding can be cost-effective compared to traditional injection molding, it’s still important to choose a provider that offers affordable pricing. Look for a provider that offers transparent pricing and who can work with you to find cost-effective solutions for your specific project needs.
- Materials and Capabilities: Different rapid injection molding providers may have varying capabilities in terms of the materials they can work with, the size and complexity of parts they can produce, and the production volume they can handle. Be sure to choose a provider that has the capabilities and expertise needed to meet your specific project requirements.
-
6.Future of Rapid Injection Molding
The future of rapid injection molding looks promising, with several advancements, industry trends, and developments shaping its growth. Some of the factors that will influence the future of rapid injection molding include:
- Technological Advancements: Rapid injection molding is a technology-driven industry, and the future will see significant advancements in technology, including the use of advanced materials, automation, and robotics, which will further improve the efficiency and accuracy of the process.
- Industry Trends and Developments: The rapid injection molding industry is expected to grow significantly in the coming years, driven by increasing demand from industries such as automotive, medical, and consumer electronics. Industry trends such as increasing use of 3D printing and increasing demand for customization will also influence the future of rapid injection molding.
- Environmental Sustainability: As environmental sustainability becomes an increasingly crucial factor for businesses, rapid injection molding providers will need to ensure that their processes and practices are sustainable and eco-friendly. This may include the use of recycled materials, energy-efficient processes, and responsible waste management practices.
Overall, the future of rapid injection molding looks bright, with the potential for continued growth and innovation in the coming years. As technology continues to evolve, and industry trends continue to shift, rapid injection molding providers will need to remain adaptable, flexible, and responsive to stay ahead of the curve.
Click on the V1 Prototype website to gain more information.
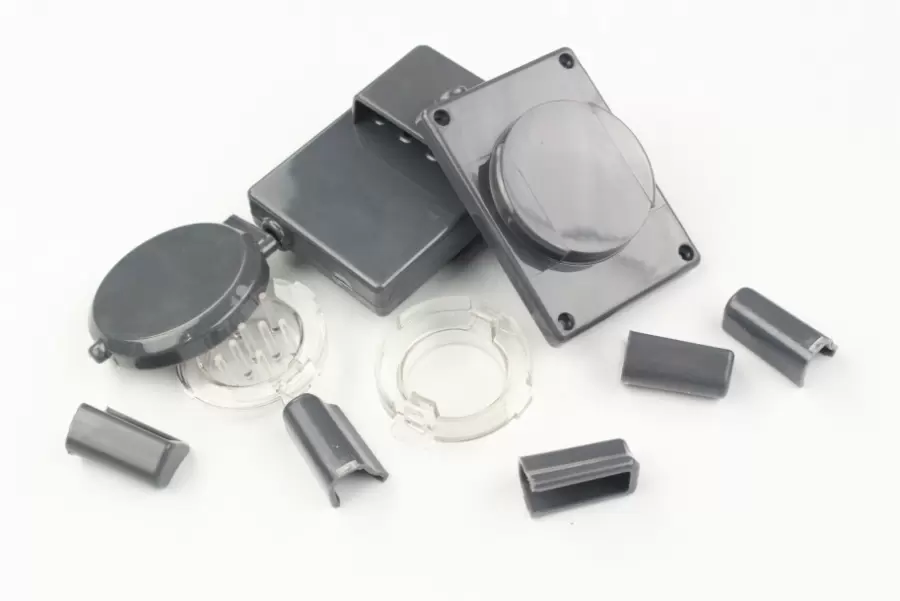
-
7.Conclusion
In today’s fast-paced business world, companies must innovate and move quickly to gain a competitive advantage. Rapid injection molding offers a way for companies to do just that, with fast and efficient manufacturing processes that can help reduce lead times, lower costs, and improve design flexibility.
By utilizing rapid injection molding, companies can produce high-quality plastic parts in a matter of days, rather than weeks or months. This speed and efficiency can help companies get their products to market faster, iterate on designs more quickly, and ultimately gain a competitive advantage in a crowded marketplace.
In the future, the rapid injection molding industry is poised for continued growth, driven by technology advancements, increasing demand from various industries, and a growing emphasis on environmental sustainability.
Overall, rapid injection molding is an essential tool for businesses looking to gain a competitive edge in a constantly evolving marketplace. With its ability to speed up production, reduce costs, and improve design flexibility, rapid injection molding is a key to success in today’s fast-paced business environment.