Table of Contents:
- Introduction
- Understanding Injection Moulding
- Advantages of Injection Moulding Products
- Design Considerations for Injection Moulding Products
- Materials Used in Injection Moulding
- The Injection Moulding Process
- Quality Control in Injection Moulding
- Applications of Injection Moulding Products
- Conclusion
Introduction:
Injection moulding is a manufacturing process that is widely used in the production of a wide variety of products. This process involves the creation of complex shapes and designs by injecting molten material into a mould cavity, which is then allowed to cool and solidify. Injection moulding is commonly used for the production of plastic products, but it can also be used for the production of metal, ceramic, and composite products. This article will provide an in-depth look into the world of injection moulding products, including their advantages, design considerations, materials used, the injection moulding process, quality control, and applications.
Understanding Injection Moulding:
Injection moulding is a manufacturing process that involves the creation of products by injecting molten material into a mould cavity. The process can be broken down into several steps:
- Clamping: The mould is held together by a clamping unit, which exerts a force on the mould to keep it closed during the injection and cooling process.
- Injection: Molten material is injected into the mould cavity through a nozzle, where it fills the cavity and takes on the shape of the mould.
- Cooling: The molten material is allowed to cool and solidify within the mould, which can take several seconds to several minutes, depending on the material and the size and complexity of the product.
- Ejection: The product is ejected from the mould by the ejection system, which can be a plate, pins, or air blasts.
Advantages of Injection Moulding Products:
There are several advantages to using injection moulding for the production of products, including:
- Cost-effective: Injection moulding can be an incredibly cost-effective process, especially when producing large quantities of products.
- High production rates: Injection moulding can produce large quantities of products in a relatively short amount of time, making it a popular choice for mass production.
- Versatility: Injection moulding can be used to create a wide variety of products, from small and simple to large and complex.
- High accuracy and consistency: Injection moulding is a highly precise process that produces products with a high level of accuracy and consistency.
Design Considerations for Injection Moulding Products:
There are several design considerations that must be taken into account when designing products for injection moulding, including:
- Wall thickness: The thickness of the product's walls should be as uniform as possible to ensure proper filling and cooling of the mould.
- Draft angles: Draft angles are included in the design to ensure that the product can be easily ejected from the mould.
- Undercuts: Undercuts are areas where the product's geometry prevents it from being ejected from the mould in a straight line, and must be designed to accommodate the ejection system.
- Gate location: The location of the gate, which is where the molten material is injected into the mould, must be carefully chosen to ensure proper filling and cooling of the mould.
Materials Used in Injection Moulding:
Injection moulding can be used with a variety of materials, including plastics, metals, ceramics, and composites. The material used will depend on the requirements of the product, such as strength, durability, and heat resistance.
- Plastics: Plastics are the most commonly used material in injection moulding, and include a variety of types such as thermoplastics, thermosets, and elastomers. Thermoplastics are the most commonly used and include materials such as polyethylene, polypropylene, and polystyrene. These materials are known for their flexibility, durability, and resistance to heat and chemicals. Thermosets, on the other hand, are harder and more brittle, and include materials such as epoxy and phenolic. Elastomers are rubber-like materials that are flexible and stretchy, and include materials such as silicone and polyurethane.
- Metals: Metals can also be used in injection moulding, but the process is more complex and requires higher temperatures and pressures than plastic injection moulding. Commonly used metals include aluminum, magnesium, and zinc, which are known for their strength and durability.
- Ceramics: Ceramics are another material that can be used in injection moulding, but the process is more difficult due to the brittleness of the material. Commonly used ceramics include alumina and zirconia, which are known for their strength and resistance to heat and wear.
- Composites: Composites are materials that are made up of multiple materials, such as plastics and fibers, and can be used in injection moulding to create products that are strong and lightweight. Commonly used composites include carbon fiber and fiberglass.
The Injection Moulding Process:
The injection moulding process involves several steps, including material preparation, mould preparation, injection, cooling, and ejection.
- Material preparation: The material used in injection moulding must be prepared before it can be injected into the mould. This involves heating the material to a specific temperature and mixing it with any necessary additives, such as colorants or reinforcing fibers.
- Mould preparation: The mould must also be prepared before the injection process can begin. This involves cleaning and lubricating the mould, as well as ensuring that it is properly aligned and securely clamped.
- Injection: Once the material and mould are prepared, the molten material is injected into the mould cavity through a gate. The pressure and temperature of the injection process must be carefully controlled to ensure proper filling and cooling of the mould.
- Cooling: After the material has been injected into the mould, it must be allowed to cool and solidify. The cooling time will depend on the material and the size and complexity of the product.
- Ejection: Once the product has cooled and solidified, it can be ejected from the mould. This is done using the ejection system, which can be a plate, pins, or air blasts.
Quality Control in Injection Moulding:
Quality control is an important part of the injection moulding process, and involves several steps to ensure that the products meet the necessary specifications and standards.
- Material testing: The material used in injection moulding must be tested to ensure that it meets the necessary specifications, such as strength, durability, and resistance to heat and chemicals.
- Mould testing: The mould must also be tested to ensure that it is properly aligned and securely clamped, and that the gate location and cooling channels are correct.
- Product testing: The finished products must be tested to ensure that they meet the necessary specifications, such as size, shape, and strength.
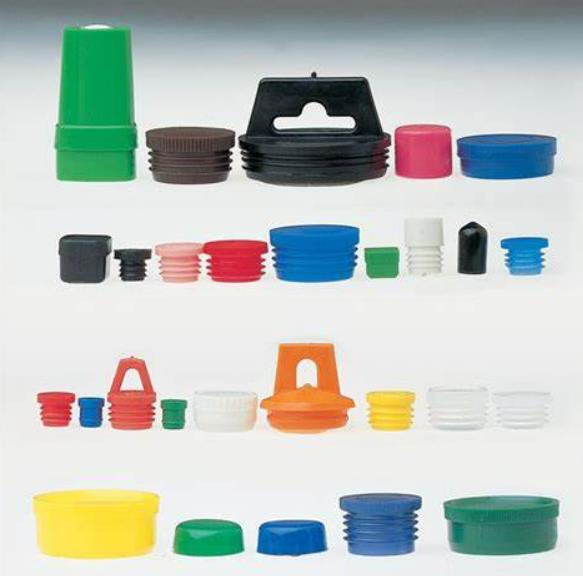
Applications of Injection Moulding Products:
Injection moulding products are used in a wide variety of applications, including:
- Automotive industry: Injection moulding products are commonly used in the production of car parts, such as dashboards, door panels, and bumpers.
- Electronics industry: Injection moulding products are used in the production of electronic components, such as computer housings and phone cases.
- Medical industry: Injection moulding products are used in the production of medical devices and equipment, such as syringes, surgical instruments, and IV components
- Packaging industry: Injection moulding products are used in the production of a wide range of packaging materials, such as bottles, containers, and caps.
- Consumer goods industry: Injection moulding products are used in the production of a wide range of consumer goods, such as toys, household appliances, and sports equipment.
Advantages of Injection Moulding:
There are several advantages to using injection moulding for product manufacturing, including:
- High efficiency: Injection moulding allows for fast and efficient production of large quantities of products, making it a cost-effective option for mass production.
- High precision: Injection moulding allows for precise control over the size and shape of the product, ensuring that each product is consistent and of high quality.
- Versatility: Injection moulding can be used with a wide range of materials, including plastics, metals, ceramics, and composites, making it a versatile option for product manufacturing.
- Automation: Injection moulding can be automated, allowing for even faster and more efficient production of products.
- Waste reduction: Injection moulding produces minimal waste, as any excess material can be recycled and reused in the production process.
Challenges of Injection Moulding:
While injection moulding offers many advantages, there are also some challenges to consider, including:
- Tooling costs: The cost of creating a mould for injection moulding can be expensive, particularly for complex designs or small quantities of products.
- Material selection: Choosing the right material for injection moulding can be challenging, as different materials have different properties and require different processing conditions.
- Design limitations: Injection moulding requires a certain amount of design flexibility to accommodate the requirements of the process, which can limit the design options for certain products.
- Environmental concerns: While injection moulding produces minimal waste, the use of plastics and other materials can still have environmental impacts, particularly if they are not properly disposed of or recycled.
Conclusion:
Injection moulding is a versatile and cost-effective method for manufacturing a wide range of products, from automotive parts to medical devices. By understanding the materials and processes involved in injection moulding, manufacturers can create high-quality products that meet the necessary specifications and standards. While there are some challenges to consider, the advantages of injection moulding make it a valuable tool for product manufacturing in a variety of industries.